From Germany to Georgia:
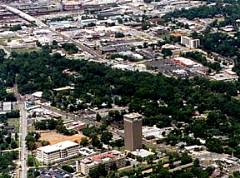 Heckler & Koch's first U.S. plant is headed for Columbus, Ga., home to the headquarters (pictured in foreground) of AFLAC, whose TV ads have created the most famous webfoot not named Donald. |
|
Heckler & Koch Gun Plant May Trigger 500-600 Jobs
by JACK LYNE, Site Selection Executive Editor of Interactive Publishing
COLUMBUS, GA. Barreling into America in high-caliber fashion, German gun-maker Heckler & Koch is building a 200-worker plant in Columbus, Ga., that may eventually employ 500 to 600.
The project marks a major milestone for Heckler & Koch, representing its first production facility in the United States.
The company already has a long-standing American presence; heretofore, though, it had no U.S. manufacturing. The company first set up an operation in the Washington, D.C., metro in 1975 to strengthen access to the U.S. military, police and civilian markets. Sterling, Va., until now has been home to all of Heckler & Koch's U.S. operations.
The gun-maker's maiden U.S. production voyage will take shape on a 25-acre (10-hectare) site in Muscogee Technology Park. The 1,391-acre (556-hectare) park sits some 89 miles (142 kilometers) south of Atlanta.
"Recent significant contract awards, as well as our assessment that the company is well positioned in competing for additional business, have convinced us to accelerate our plans to establish a manufacturing facility in America," said Vice President of U.S. Operations Peter Simon, a retired U.S. Army lieutenant colonel.
Heckler & Koch recently won the contract to supply the U.S. Transportation Security Administration's federal flight deck officers with its USP 40 compact pistol. The Columbus plant's output will include the USP 40 and the MP5 submachine gun, used by police SWAT teams and U.S. special military forces. (The company's customers also include the German and Spanish armed forces.)
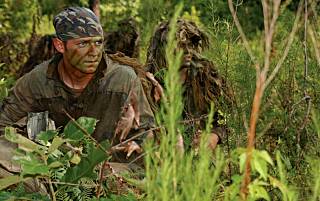 The proximity of Fort Benning (pictured), the nation's largest infantry training center and home of the Army Infantry School, was likely a major factor in Heckler & Koch's decision. |
|
Heckler & Koch is initially building a 50,000-sq.-ft. (4,500-sq.-m.) plant that can accommodate 200 workers. But employment could triple in a greatly expanded facility if anticipated demand pans out, Simon said.
"We will initially create about 200 American jobs in Columbus," he explained, "and we forecast additional growth as some of our U.S.-based design and development projects mature into production."
Project Signals Shift from Company's
Historic 'Euro-Centric Center of Gravity'
Additional U.S. growth is a central tenet in the Columbus project's strategic rationale for Heckler & Koch, founded in 1948 in its headquarters city of Oberndorf, Germany.
"This decision reflects our strategic commitment to the U.S. market and also our acceptance and support for 'Buy American' provisions," Simon explained.
"Buy American" requirements have been a contentious point in the current congressional debate over the U.S. Defense Dept.'s fiscal 2004 appropriations bill. The House has passed a version of the Defense Authorization Act that would limit U.S. weapons acquisition to domestically made products. It remains to be seen whether that limit will survive House-Senate conference committee negotiations on the bill. (Opponents of the provision have pointed out that the U.S. defense industry sells six times more to Europe than it buys from the continent.)
For Heckler & Koch, though, the Columbus plant signals a transition running even deeper than its first U.S. production venture. The project, Simon explained, signals the company's shift away from what he called "our Euro-centric center of gravity." The new Georgia operation, in fact, is the gun-maker's first production facility to be located outside of Germany.
The U.S. will apparently make up a large portion of Heckler & Koch's broadened center of gravity. The Georgia plant, Simon said, represents the beginning of a U.S. buildup over the next five years that could create as many American jobs as the company's 700 current positions in Germany.
Heckler & Koch's U.S. commitment in Columbus may also extend beyond manufacturing. Simon said that the company is considering co-locating some of its higher-end U.S. functions at the Georgia site, including part of the Design and Engineering Office now based in Virginia.
Decision Drivers: Customer Proximity, Business
Climate and 'Economically Viable Agreement'
Georgia won Heckler & Koch's first U.S. plant from competitors that included Florida, South Carolina, Texas and Virginia, company officials said. The German company will be the Peach State's second gun manufacturer. Austria-based Glock has its U.S. and Canadian headquarters and a manufacturing plant in Smyrna, an Atlanta suburb.
Heckler & Koch picked Georgia, Simon explained, because of "the combination of proximity to our primary customer base in the military and law enforcement, the business climate and the economic viability of the agreement that we reached."
The exact value of the gun-maker's Georgia agreement hasn't yet been determined. State officials said that the company will receive $300,000 in incentives from the Georgia Dept. of Industry, Trade and Tourism.
The company, they added, will also be eligible for other state and local incentives and property tax breaks. One of them will be Georgia's Quick Start program, which will train Heckler & Koch's workers at Columbus Technical College, said Simon. In addition, local officials added that they anticipate a company request for a bond issue from the Columbus Development Authority to fund building the plant.
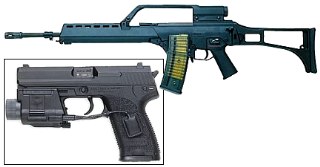 The present and the possible future: The Columbus plant's output will include the USP 40 Compact Pistol (bottom left) for the U.S. Transportation Security Administration's federal flight deck officers. And the Georgia plant hopes to make the XM8 lightweight assault rifle, which is based on the company's G36 assault rifle (top). |
|
Fort Benning Proximity Likely a Factor
But what was likely a major decision factor - the proximity of the Army's Fort Benning - got scant mention in Heckler & Koch's official rationale for its Peach State pick. Columbus sits only 10 miles (16 kilometers) north of Fort Benning.
The fort, though, was almost certainly a substantial site selection factor. Heckler & Koch last year began R&D work on the XM8 lightweight assault rifle. The Army is considering the XM8 as a replacement for its M4A1 carbine and M16A2 rifle.
Heckler & Koch is now manufacturing 220 XM8s in Germany. The XM8 is based on the company's G36 assault rifle, revered for its resistance to jamming in dusty and sandy conditions.
Army testing of the XM8s is scheduled for this fall, and Fort Benning is one of the test sites. Significantly, the fort is the nation's largest infantry training center and is the home of the Army Infantry School. Fort Benning also has a wide range of units that could serve as XM8 test groups, including the 3rd Infantry Division and the Rangers.
Heckler & Koch's initial XM8 output will be followed by a second production run of some 2,000 rifles. Defense industry analysts expect the contract for the full production run to be awarded in 2006.
The German company, however, isn't a lock for the full-run XM8 deal. Competitors including Colt and General Dynamics are also reportedly working on their own versions of a new lightweight assault rifle. Connecticut-based Colt has been making the M16 since 1964.
Heckler & Koch plans to break ground in Columbus by November, with production going online by the end of next year.
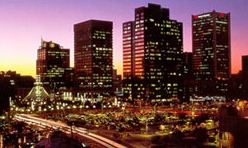 Coming to Phoenix (pictured) will enable Angelica to better serve its existing customer base in the area. The company had been serving those customers through one of its Southern California operations. |
|
Angelica Textile Services' Phoenix Plant Could Employ 300
by JACK LYNE, Site Selection Executive Editor of Interactive Publishing
PHOENIX By the time Angelica Textile Services gets to Phoenix, it'll be cleanin' - as much as 13 million pounds (5.85 million kilograms) of linen a year, in fact.
With apologies to songwriter extraordinaire Jimmy Webb, that's how much annual cleaning capacity Angelica Textile Services plans to install in its new facility in Arizona's capital city.
The Atlanta-metro-based subsidiary of Angelica Corporation has broken ground on a 74,000-sq.-ft. (6,660-sq.-m.) linen processing facility in Phoenix; and it's building the operation to be expandable by another 30,000 sq. ft. (2,700 sq. m.).
The extra space may well be needed. Angelica Textile Services plans to open its Phoenix facility with 100 employees in sales, customer service and linen management. But the operation may eventually employ as many as 300 workers, company officials say.
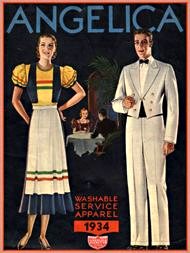 Founded in 1878, Angelica first made its name as a provider of service-industry uniforms, introducing the first uniforms made of synthetic fabrics (pictured above in a 1934 magazine ad). Today, though, three-fourths of the company's sales come from laundry plants like the one opening in Phoenix. |
|
And employment could hit the upper end of job-generation projections, given Angelica Textile Services' strong existing local customer base - the project's driving raison d'etre. The company specializes in laundry services for health-care facilities, including hospitals and surgical centers, nursing homes and long-term care operations. A number of Phoenix-area institutions are already major clients, including Scottsdale Healthcare and St. Joseph's Hospital and Medical Center.
Company's Area Customers Previously
Served by Southern California Operation
Angelica Textile Services has been supplying such Phoenix-area clients from one of its out-of-state operations.
"We've been serving our Arizona customers from a Southern California location," Division Manager Ron Sneddon, "so this new facility in Phoenix will allow us to continue providing linen management solutions for our customers in a more efficient manner. We're also looking forward to presenting our capabilities to other hospitals in the area."
Angelica, Sneddon added, was sufficiently intent on getting closer to its Arizona customer base that it considered acquiring local commercial launderers before deciding to build from scratch in Phoenix.
Angelica Textile Services further bulked up its West Coast presence a year ago by trading commercial laundry facilities with a rival firm. The company traded its operations in Philadelphia to Houston-based Tartan Textile Services in exchange for Tartan's operations in Vallejo, Calif.
Plant Will Emphasize Resource Efficiencies
In addition to its existing customer base, Angelica picked Phoenix for its ground transportation infrastructure and its available labor pool, Sneddon said. The company will transfer a few employees from California, but most hires will come from the Phoenix area, he explained.
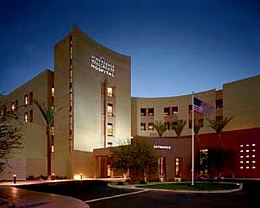 Angelica Textile Services existing Phoenix-area clients include Scottsdale Healthcare. (Pictured: the Shea Women's Center at Scottsdale Healthcare.) |
|
The Phoenix facility will be the first in the area for Angelica Textile Services. But another arm of Chesterfield, Mo.-based Angelica Corporation, Life Uniform, has four retail outlets in the metro area.
Angelica Textile Services, though, accounts for the lion's share of the parent firm's business. Some three-fourths of Angelica Corporation's 2002 annual sales of $363.4 million came from its 25 laundry plants.
The 26th plant will generate more than $315,000 annually in direct and indirect revenues for Phoenix, Maricopa County and the state, the Greater Phoenix Economic Council estimated.
Angelica Textile Services' plant is already generating direct revenues for some local real estate service providers. Joe Diemer Associates Architecture and Planning designed the facility, while LGE Design Build is serving as general contractor.
The facility will be a state-of-the-art structure, said Sneddon, using 50 percent less water and 20 percent less energy that most commercial laundry operations. And unlike most laundry facilities, the Phoenix plant, he added, will include air-conditioning throughout the premises.
Editor's note: For more on location activity in Arizona and the Southwest U.S., see the Southwest Regional Review in the upcoming November issue of Site Selection.
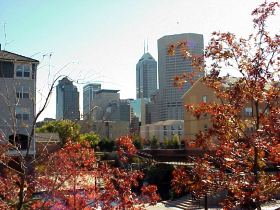 BioStorage Technologies chosen site in Indianapolis (pictured) puts it at the heart of Indiana's robust life sciences sector. |
|
BioStorage Technologies Picks Indy for 100-Employee HQ, Storage Site
by JACK LYNE, Site Selection Executive Editor of Interactive Publishing
INDIANAPOLIS BioStorage Technologies Inc., has chosen Indianapolis for a new 100-employee operation that could prove to be a pioneering facility of sorts for the life sciences sector. The new Indianapolis operations will the first focused solely on pharmaceutical specimen storage, according to Oscar Moralez, president and founder of the newly formed company.
That Indianapolis operation will include some very cold space to serve the hot life sciences sector. BioStorage Technologies' officials say that the facility will store "hundreds of thousands" of life sciences specimens, some of them in freezers that are cooled to minus 232 degrees Fahrenheit (minus 150 degrees Celsius). In addition to storing biological specimens, the facility will also serve as the company's headquarters and will house its sales and logistics staff.
"The market BioStorage Technologies will serve is large and growing rapidly," Moralez said in announcing the city's Indiana project.
Moralez illustrated that burgeoning market by citing a 1999 federal advisory panel report. The report estimated that more than 282 million biological specimens were then stored in U.S. laboratories, military facilities, forensic DNA banks, tissue repositories, health-care facilities and other sites. And the U.S. total of stored specimens, he added, is increasing by 20 million a year.
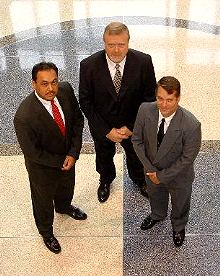 All three of BioStorage Technologies principals - (l to r) Oscar Moralez, John Mills and Scott Sheaffer - were previously high-ranking executives with New Jersey-based Covance, which bases its Central Laboratory Services Division based in Indianapolis. |
|
That's where BioStorage Technologies comes in as an outsourced solution, Moralez noted. "By managing the time-consuming and detail-dependent processes of specimen storage, BioStorage Technologies will free life sciences organizations to focus on their core functions and achieve their scientific goals," he said.
Factors: Central Location, FedEx
Hub, Strong Life Sciences Cluster
The company picked Indianapolis to serve that fast-growing sector because of the city's central U.S. location and the presence of a major Federal Express air hub for overnight delivery, explained CEO F. John Mills.
"We will be an integral part of the infrastructure that will serve the life sciences." said Mills, who called biological samples "worth their weight in gold." BioStorage Technologies' Indianapolis facility, he asserted, "will provide the world's best and safest management, logistics and storage services of biological specimens and data."
BioStorage Technologies will be providing those services from a ripe area for life sciences. A 2002 Battelle Memorial Institute report ranked Indiana's life sciences sector as the state's largest employer, providing 318,000 jobs, more than 13.3 percent of private-sector employment.
Much of that sector is epicentered in Indiana's central region, particularly in the area stretching from Bloomington to Indianapolis to West Lafayette. Central Indiana's life sciences cluster includes some 900 companies with 82,000 employees, including Anthem, Clarian Health Partners, Dow AgroSciences, Eli Lilly, Guidant and Roche Diagnostics.
"BioStorage Technologies is another piece of the life sciences infrastructure that is so critical to attracting and encouraging the kind of life sciences businesses that we want to see in Indianapolis," said Jeb Conrad, executive director of Marion County Economic Development, part of The Indy Partnership.
One life sciences company that residents already see, in fact, accounts for much of BioStorage Technologies' key initial knowledge about Indianapolis' strengths. A contract company that develops and tests drugs, Princeton, N.J.-based Covance Inc. has its Central Laboratory Services Division based in Indianapolis. And all three of BioStorage Technologies' principals - Mills, Moralez and Vice President of Technical Operations Scott Sheaffer - were high-ranking executives with Covance before deciding to venture out to launch the new startup.
Sites Sits Adjacent to Indianapolis International
The company picked an Indianapolis site that will fully take advantage of the city's heartland position to facilitate fast specimen transit. BioStorage Technologies will open its operation in Park Fletcher Business Park, located in the southwest suburbs just across from Indianapolis International Airport. The park also provides rapid access to I-465, I-70 and I-65.
The company is leasing its facility from Duke Realty, which developed and operates the 700-acre (280-hectare) Park Fletcher. Terms of the lease weren't disclosed. BioStorage Technologies, said Mills, will invest $3.5 million in the building over the next two years.
The company expects to hire approximately 100 employees during its first 24 months of operations. Personnel working in the Indianapolis operation will include management, laboratory and computer technicians, salespeople, and others, Mills explained.
City, State Providing $300,000-Plus in Incentives
Company jobs will pay an average salary of $37,600, 20 percent above Indiana's mean average.
"The life sciences continue to be a driver of our regional economy, attracting good-paying jobs and investment to our community," Mayor Bart Peterson (D) said in welcoming BioStorage Technologies.
State and local economic development arms are providing the promising startup with more than $300,000 in incentives. The largest chunk of that total is coming from the city's six-year property tax abatement, which has an estimated value of $230,000. The Indiana Department of Commerce is also providing $78,500 in worker training grants.
"Life science is one of the core industries that Indiana is focusing on through the 'Energize Indiana' economic development package of programs," Lt. Gov. Joe Kernan (D) said in announcing the BioStorage Technologies project. (Kernan was soon after named Indiana's governor after the death of Gov. Frank O'Bannon.)
BioStorage has raised $1 million thus far from investors. At least one firm has signed a letter of intent for specimen storage in Indianapolis, Mills said.
pw0915bpw0915b
PLEASE VISIT OUR SPONSOR CLICK ABOVE
©2003 Conway Data, Inc. All rights reserved. Data is from many sources and is not warranted to be accurate or current.
|