After Huge Losses, Bridgestone/Firestone
Looks to Unload Huge Factory
by ADAM BRUNS
After languishing in the spotlight of scandal since the August 2000 recall of 6.5 million tires, the giant manufacturing facility belonging to Bridgestone/Firestone in Decatur, Ill., has officially hit the road.
On June 18, the company named Philadelphia-based Binswanger/CBB as the exclusive agent for the 2.2-million-sq.-ft. (204,173-sq.m.) facility, sprawled across 153 acres (62 hectares). The initial asking price is $16 million.
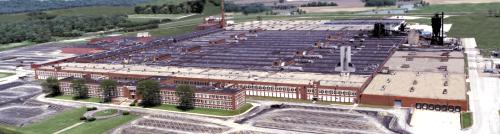 The massive former Bridgestone/Firestone facility, on 153 acres in Decatur, Ill., had the capacity for making seven million tires per year.
|
|
The plant, which had the capacity to produce around seven million tires annually and had accounted for 10 percent of the company's tire production, had been leaking employees ever since the scandal hit the headlines two years ago. Tires made by the company were linked to over 270 deaths and more than 700 injuries, although the company very publicly deflected some of the blame in the direction of Ford Motor Co.'s Explorer. Most of those tires were 15-inch Wilderness AT tires, made in Decatur, an industry town of some 80,000 otherwise known as the home of Archer Daniels Midland.
So how do you market a facility marked by age, mega-scale and recent history? That's just the beginning of the challenges, says Robert Wall, Jr., Binswanger senior vice president for the midwest region.
The size is fairly daunting, he says. And the fact it has a central power plant, with high pressure boilers and air compressors is a challenge. How do you break it up? That's what we're asking the people looking at it to figure out. It was built in 1942, with a million square feet of wood truss roof, so that's a challenge too.
And while those prospects are considering what to tear down, they might also consider the labor union strength that has built up in the region.
Decatur is perceived as a hotbed of union activity, says Wall, so area perception comes into play. There is a very strong economic development group in Decatur that is fighting to overcome this preconceived negative about the area. The reality is that union and non-union labor work very well together in the area, as evidenced by ADM, with union and non-union working side by side. It's the same with Caterpillar: they have a non-union shop that does all their transporting of finished goods.
Binswanger is mailing to about 5,000 groups internationally, targeting such sectors as primary metals, heavy fabrication and plastics. Besides its mere size, which encompasses 92,700 sq. ft. of office space, the facility boasts rail service and proximity to both Decatur Airport and Interstate 72, which spins off traffic toward Chicago in one direction and St. Louis in the other.
One additional strike against the mammoth offering is the recent shutdown of automotive compressor manufacturer Zexel Valeo's 400,000-sq-ft. plant nearby, adding to a market that is already saturated. But the good news, says Wall, is the attitude of his sellers.
Bridgestone/Firestone America has a very realistic idea of what the value is, and will work diligently with any buyer to ensure that a deal gets structured and closed on. They are very realistic in their expectations.
Unilever Unveils Expanded Southeast Distribution Center
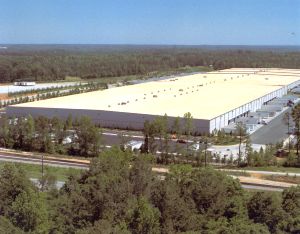 The newly expanded Unilever site in Palmetto, Ga. is one of five that will serve the company on a regional basis as a result of consolidation from 28 different distribution centers.
|
|
by JOHN McCURRY and RON STARNER
Unilever's newly expanded Southeast distribution center in Palmetto, Ga., is the first of five the company will build around the U.S. The facility represents an investment of about $50 million. The 443,000-sq.-ft. (41,203-sq.-m.) expansion joins an original 600,000-sq.-ft. (55,740-sq.-m.) building. The enlarged facility, resting on 38.3 acres (15.5 hectares), now has 85 dock doors (an increase of 25) and employs 185 in three shifts.
Partnering with Uniliver Home Products NA are site developer ProLogis and facility operator GENCO. ProLogis, which acquired the original Unilever Palmetto site in 1999, provided design and engineering, allowing the expanding center to support multiple operations including consolidated fulfillment and customized pallets. The facility will serve Alabama, Florida, Georgia, Mississippi and the Carolinas.
We're streamlining our distribution network for flexibility, said Fred Berkheimer, Unilever's vice president, logistics. On the ground, that means combining its 28 distribution centers into five over the next few years.
A major factor in Unilever's location decision was the presence of a CSX freight hub in Palmetto. According to Randy Evans, vice president of real estate and industrial development for Jacksonville-based CSX, Highway congestion is making rail access a necessity for distribution centers, and in the future we foresee the development of large industrial parks with integrated logistical centers.
Companies like Unilever can experience significant cost savings using rail transport, noted Evans. Rail is the most cost-effective and most efficient means of transportation for the middle 1,000 miles of the logistical supply chain, he said.
Companies like Unilever also can take advantage of CSX's new TransFlow technology, which allows real-time tracking of all inventory including goods in transit.
With TransFlow, we have the ability to track all shipments in motion, tell you exactly where they are and their expected day of delivery, and even re-route cars, if needed, in the middle of a delivery, said Evans.
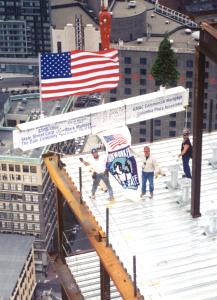 Workers above and dignitaries below celebrate the topping out of the 36-story One Lincoln Place building, a $350-million, 1,000,000-sq.-ft. project that is fully leased.
|
|
'New Gateway' Goes Up
in Boston Financial District
by ADAM BRUNS
While the Big Dig continues to go down, One Lincoln St. is going straight up, and right on schedule.
Dignitaries including Boston Mayor Thomas M. Menino, Mark Maloney of the Boston Redevelopment Authority; John B. Hynes III, partner, The Gale Co.; Gino J. Baroni of construction manager Beacon Skanska Inc.; and Thomas Cataldo and George Russell, executive vice presidents of State Street Corporation, were on hand June 5th to celebrate the topping out ceremony for the fully leased, 36-story, 1,000,000-sq.-ft. (92,900-sq.m.) office tower.
One Lincoln will be a tremendous addition to the City and will become a signature gateway to the Financial District, said Mayor Menino of the $350-million project, designed by Jung/Brannen Associates. Plus, the housing and jobs linkage generated by this project will have a positive impact on the neighboring communities.
We would like to extend our sincere gratitude to our world-class partners, Local 7 Ironworkers Union and numerous other contractors who have ensured that this historic project maintains its stringent development schedule, said Hynes.
Everyone involved was anxious to see the building progress after nearly 14 years of project planning, Baroni added. We were able to speed up the building process and come together today to celebrate this historic milestone by applying the novel Up/Up construction method. Up/Up construction essentially involves starting the building's structure at two locations - at the bottom of the garage and at the ground floor level, once the excavation and foundation system are finished - and then progressing simultaneously upward. This methodology eliminates several months of excavation work.
The first spec building that the Boston CBD has seen in over a decade, One Lincoln was to be the first downtown office building to be developed through the City's Parcel-to-Parcel Linkage Program which included the investment and participation of a group of City-designated local minority partners, Columbia Plaza Associates. Due to the downturn in the real estate market in the early 1990s, the project was put on hold. In the fall of 1999, The Gale Company, backed by Morgan Stanley Real Estate Funds and The State Teachers Retirement System of Ohio, entered into a development joint venture with Columbia Plaza Associates, and then completed the design, approval and permitting work for the project and began construction in April 2000. Prompted by the participation of Columbia Plaza Associates, a group of local Asian American, African American and Hispanic investors, the project is contributing over $15 million in linkage payments to benefit numerous community groups and initiatives addressing affordable housing, jobs and job training, minority business enterprises and childcare programs.
Minoura Helps Break New Ground for Toyota in Mexico
by ADAM BRUNS
With a new footprint in Mexico, Toyota has now walked the NAFTA circle.
Mexican President Vicente Fox, Governor Eugenio Elorduy, and Jesus Gonzalez, Presidente Municipal de Tijuana, joined hundreds of community leaders, government officials, and Toyota executives in a ceremony June 12 to mark the construction of the automaker's truck deck plant to be built in Baja, California.
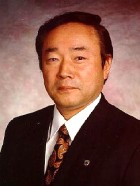 Teruyuki Minoura, president of Toyota Motor Manufacturing North America, bid his new Mexican team members a fond hola in breaking ground for the company's first Mexican facility in Tijuana.
|
|
Positioned to make and ship truck beds for the Tacoma pickup trucks made just up the road at New United Motor Manufacturing in Fremont, Calif. (a Toyota/General Motors joint venture), the plant is part of Toyota Motor Manufacturing North America's 2003 goals: capacity to build 1.45 million cars and trucks and 1.6 million engines a year, and employment of some 33,000 people.
This Mexico facility is an extremely important milestone for us, said TMMNA President Teruyuki Minoura. This plant finally closes the Toyota North American manufacturing circle - the U.S. - Canada - and now Mexico.
As if to drive home that point, the new president of Toyota Motor Manufacturing de Baja California will be Seiji Ikezaki, who currently holds that same post at Toyota's oldest North American plant, TABC in Long Beach, Calif. Through a linkage program similar to the Boston office building arrangement, Toyota is marking the occasion by donating one million pesos to some 30 libraries and technical schools in the Tijuana and Tecate regions.
A further sign of promising horizons in Mexico: Toyota Motor Sales began selling Camrys there in April, with Corollas scheduled to bloom along the autovias this month.
It is our basic policy that 'We make them where we sell them, said Minoura.
Mexico is not the only Latin American location to see investment from the parent company. Two days later, Toyota announced the completion of a $30-million investment in the expansion of the Indaiatuba Plant of Toyota do Brasil Ltda. (TDB), its manufacturing subsidiary in Sao Paulo, Brazil. The plant, which has been building Corollas since 1998, now has an annual production capacity of 57,000 units, up from 15,000.
The expansion enlarged the plant's floor space from 29,000 square meters (312,000 sq. ft.) to 69,000 square meters (743,000 sq. ft.), and includes a new stamping shop. The plan also aims for a two-shift system, anticipated to add as many as 1,000 new jobs to the payroll. According to the company, the Indaiatuba-made new Corolla will be sold in Brazil and exported to more than 20 countries, including Argentina and Uruguay, helping to establish TDB as a Toyota export base for Latin America.