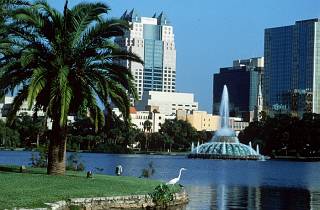 The some 180 firms in Orlando (pictured) that are involved in flight training and simulation were a major attraction for JetBlue's training center. |
|
Fast-Rising JetBlue Picks Orlando for 150-Worker Training Center, Hangar
by JACK LYNE, Site Selection Executive Editor of Interactive Publishing
ORLANDO, Fla. Forest Hills, N.Y.-based JetBlue Airways, making its first major expansion sally outside the Empire State, has picked Orlando, Fla., for a new flight training center and aircraft maintenance hangar. The two facilities collectively will involve an investment of as much as US$160 million and will create 150 JetBlue jobs at Orlando International Airport.
The new training center will be the first ever for the fast-rising upstart. Founded in 2000, the fledgling low-fare firm currently bases all of its training at a Miami center owned by Airbus. Training for all JetBlue pilots, in-flight crews, and technical operations and customer service personnel will shift to the Orlando center in late 2005, when construction is scheduled for completion.
But the 150 Orlando jobs that the low-fare airline is creating won't be low-wage affairs. Annual earnings will average $60,000, company officials said.
The Florida move marks a southward shift in JetBlue's expansion flight plan. The company thus far has clustered most operations in the New York area, where it's registered its most pronounced success.
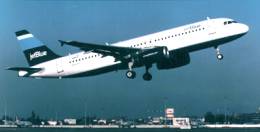 Fast-rising JetBlue's business model is also soaring, recording operating margins of almost 16 percent. |
|
Orlando a Flight Training, Simulation Hub
Orlando, though, had a lot to offer, particularly for the training center, JetBlue President and COO Dave Barger said at the project announcement at Orlando International.
The metro is home to some 180 firms involved in flight training and simulation. Orlando is also the headquarters city of the National Center for Simulation, a non-profit organization made up of governmental agencies, defense contractors and educational institutions.
Another Orlando draw was the University of Central Florida (UCF). UCF is home to two highly regarded flight-training centers: the Institute for Simulation and Training and the Central Florida Research Park, which includes a Defense Department national training and simulation center. UCF also offers graduate programs in flight simulation and modeling.
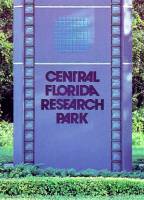 One Orlando draw for JetBlue was the University of Central Florida's Central Florida Research Park (pictured), home to the Institute for Simulation and Training and the Central Florida Research Park, which includes a Defense Department training and simulation center. |
|
JetBlue already knew a lot about Orlando and its airport, Barger explained. The city is one of the airline's current 22 U.S. destinations.
"Building on our long-standing partnership with the Greater Orlando Aviation Authority, Gov. Jeb Bush, Mayor Buddy Dyer and County Chairman Rich Crotty have all stepped up to the plate to help take JetBlue's commitment to Central Florida to a new level," Barger said.
"This is a great day for metro Orlando and is another indication of our region's dominance in the modeling, simulation and training sector," said Ray Gilley, president and CEO of the Metro Orlando Economic Development Commission.
Orlando is also the headquarters city for AirTran Airways.
JetBlue Coming Off Finest Month Ever
The 80,000-sq.-ft. (7,200-sq.-m.) training center will accommodate a wide range of activities. The new facility will have the capacity for eight flight simulators and two cabin simulators, plus classrooms, cabin crew training equipment, a training pool, a fire-fighting training station and administration areas.
JetBlue's 70,000-sq.-ft. (6,300-sq.-m.) hangar will be big enough to accommodate three Airbus A320s. The Orlando hangar, explained Barger, will be used for aircraft maintenance, as well as for installation and maintenance of the airline's LiveTV system. LiveTV is a wholly owned JetBlue subsidiary that provides free in-flight satellite television on all the company's aircraft. The hangar is scheduled for completion in early 2005, Barger said.
Full details of JetBlue's incentive package haven't yet been released. At present, though, that package totals at least about $3.5 million in tax credits and job-creation grants already approved by Orlando and Orange County. The state is expected to add its own job-creation grant of about $500,000.
JetBlue is coming off its best month ever. The airline in 2003 had just over 5 million passengers through the end of July, a 68.5 percent increase from its performance through July of 2002.
Emboldened by its success, JetBlue is bulking up the 53 planes it will have flying by year's end. It has ordered 100 Embraer 190s, with options for an additional 100. The first Embraer 190s are scheduled for delivery in mid-2005.
Company Also Planning $1-Billion NYC Terminal
JetBlue's expansion designs also include its home turf in New York.
The airline, along with the New York and New Jersey Port Authority (which operates the region's major airports), is proposing a $1-billion terminal at John F. Kennedy International Airport. JetBlue's Kennedy terminal would have from 48 to 51 gates, company officials reported.
JetBlue's current operating margin is an eye-opening 15.9 percent, according to The Motley Fool. The airline's business model is patterned after highly successful Southwest Airlines.
The airline's success has been particularly pronounced in the New York area.
JetBlue now has a 10-percent share of domestic flights from LaGuardia, Kennedy and Newark airports; that figure represents a nine-percent increase over the last two years. JetBlue ranks No. 4 in revenues in the hotly contested New York area.
And analysts expect the airline to move up to No. 3 in New York revenues by the end of next year, supplanting United, which has an 11-percent market share.
JetBlue is faring better still in the key New-York-to-Florida market. The airline has 20 percent of that sector, trailing only Delta and Continental, both with a market share of about 22 percent.
JetBlue has some 4,000 employees.
Editor's note: For more coverage of major projects in the Sunshine State, see the Florida Spotlight Section in the upcoming September Site Selection.
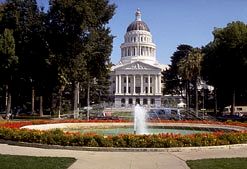 Home to California's capital (pictured), Sacramento will also be home to James Hardie's $47.5-million fiber-cement plant. |
|
Hardie's Hearty U.S. Expansion: New Sacramento Plant Part of $100M Plan
by JACK LYNE, Site Selection Executive Editor of Interactive Publishing
SACRAMENTO, Calif. Accelerating its aggressive U.S. expansion strategy, Netherlands-based James Hardie Building Products has decided to build a new 100-worker, $47.5-million fiber-cement plant in, Elk Grove, Calif., part of the Sacramento metro.
The company has picked a 53.7-acre (21.5-hectare) site in California's capital city for the 225,000-sq.-ft. (20,250-sq.-m.) production operation.
The Elk Grove project squarely fits the menu for James Hardie's hearty U.S. expansion appetite. The company announced late last month that it would spend more than $100 million in expanding its U.S. fiber cement operations.
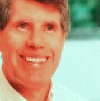 Hardie needed a new plant, explained CEO Peter Macdonald (pictured), because "we do not have sufficient capacity on the West Coast to meet projected demand next year. U.S. West Coast markets account for about a quarter of our worldwide sales today." |
|
The Sacramento plant, however, marks a departure from some commonly held perceptions about California business costs. Owing to Hardie's technological advances, the new Golden State operation will actually be less expensive than the company norm, explained CEO Peter Macdonald.
"The new plant will represent another breakthrough in James Hardie's manufacturing technology, resulting in significantly lower capital and operating costs from those achieved at our existing plants," he said.
"The new plant will have a single production line with a design capacity of 300 million sq. ft. (27 million sq. m.) a year," he continued, "50 percent more than the capacity of the company's biggest production lines today. Additionally, the new plant will generate further operating cost savings of about 10 percent compared to other Hardie plants."
The new Sacramento plant, Macdonald said, "will make plank, panel and backer products."
Hardie Needed More West Coast Capacity
Hardie already had a significant fiber cement manufacturing presence on the West Coast, with existing plants in Fontana, Calif. and Tacoma, Wash. But it needed more output to meet regional demand, Macdonald explained.
"We do not have sufficient capacity on the West Coast to meet projected demand next year," he said. "U.S. West Coast markets account for about a quarter of our worldwide sales today, and we believe demand from these markets will grow strongly over the next five years."
Hardie looked at a number of other West Coast locations, said Macdonald, who didn't name any competing sites.
But Brian Strom, chairman of the Sacramento Area Commerce and Trade Organization (SACTO) and president and CEO of SureWest Communications, called Hardie's process "a wide and lengthy search both in and out of state" in his remarks hailing the area's win. "They will be a great addition to the region's manufacturing community," Strom said.
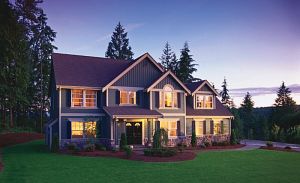 What's in a house? Profit, if you're James Hardie. Riding largely on the strength of strong U.S. housing demand, the company's increased sales by 35 percent and earnings by 58 percent in its 2002-03 fiscal year. |
|
And Hardie's new Sacramento addition will add more than production capacity to the company's operational efficiencies, Macdonald pointed out.
"The Sacramento plant will mean that we can deliver to all of our customers on the West Coast faster and at lower cost," Macdonald said.
Hardie's U.S. Sales Goals:
20 Percent-Plus Annual Increases
The Sacramento announcement comes as Hardie continues to track ahead of its ambitious U.S. expansion goals. The Amsterdam-headquartered company's business plan calls for increasing U.S. sales by 20 percent a year, with earnings increasing before interest and taxes by 20 percent or better.
Hardie did considerably better than that in its 2002-03 fiscal year.
The company's U.S. fiber cement operations registered a 35 percent annual sales increase and a 58 percent earnings increase, finishing at $155.1 million. (Fiber cement products now account for almost all of Hardie's sales since the company exited the gypsum business last year, selling that business for $345 million.)
Hardie's $100-million American expansion strategy is clearly designed to keep such figures coming. U.S. sales now account for 75 percent of the company's total earnings.
$49.9-Million Illinois Expansion Completed
One part of Hardie's U.S. expansion plan is already completed - a $49.9-million new production line added this year at its plant in Peru, Ill. The plan also calls for some $3 million to be spent in doubling the size of Hardie's R&D center at its Fontana plant.
The company's 2003 U.S. expansion flurry comes on the heels of the two fiber cement expansions Hardie announced in the fall of 2002: a $27-million new production line added at its Waxahachie, Texas, plant and a $15.3-million capacity upgrade of its Blandon, Pa., plant.
When the Sacramento plant is complete, James Hardie's nine U.S. fiber cement plants will have a collective capacity to produce some 2.8 billion sq. ft. (252 million sq. m.) a year.
The Sacramento plant should come online in mid-2004, Macdonald said.
Sacramento is also enjoying expansive manufacturing times. 2003 inquiries from production prospects are almost twice as high as last year, SACTO officials report.
A number of other players helped SACTO turn Hardie from prospect into project, Strom explained. Those players, he said, included Colliers International, Elk Grove Economic Development Manager Reid Montgomery and Pacific Gas & Electric Company.
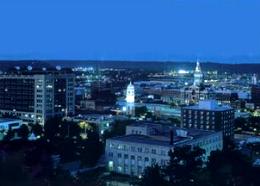 Quebecor World's 100-worker expansion will increase by one-third the company's current presence in Dubuque (pictured). |
|
Roll the Presses: Quebecor's 100-Worker Iowa Expansion Still a Go
by JACK LYNE, Site Selection Executive Editor of Interactive Publishing
MONTREAL and DUBUQUE, Iowa Bucking its industry's sharp downturn and widespread layoffs, Montreal-based Quebecor World has announced that its $13-million, 100-worker expansion of its Dubuque, Iowa, plant is a go.
The Canadian power's project comes during tough times for the printing trade. Quebecor World, though, has been anything but immune. Despite being the primary printer for such boffo bestsellers as Harry Potter and the Order of the Phoenix and Living History, the world's largest commercial printer earlier this month reported a second-quarter 2003 loss of $61.7 million.
The rest of the industry is likewise reeling, with printers buffeted about by sluggish demand and severe pricing pressures. Quebecor World recently announced that it's laying off 1,000 of its 38,000 worldwide employees. Half of those cuts are U.S. jobs.
"We won't take work at any price," Quebecor World North America COO David Boles vowed in the face of the company's woes.
Things are different, though in Dubuque. That's because the Iowa plant is in the process of being shifted over to textbook printing to fulfill Quebecor World's contract with McGraw-Hill.
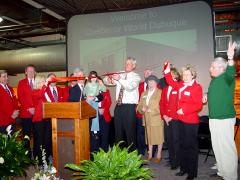 Quebecor employees at the Dubuque plant celebrate with city and county officials after learning that the phase II expansion has gotten the green light. Photo: Dubuque Ambassadors |
|
"We recognize that a facility dedicated to the education market will allow us to best meet the needs of our customers," John Bertuccini, Quebecor World North America president of Book and Directory Publishing Services, said in Montreal in announcing the Dubuque expansion. "We will continue to invest and realign our platform to offer specialized solutions to help educational publishers compete in the marketplace."
Project Marks Phase II Dubuque Expansion
The $13-million expansion continues Quebecor World's growth in Dubuque. The company in February of 2002 announced that it was going to spend $19 million in a two-phase project that would convert the Iowa plant to textbook printing.
With phase II getting the green light, the company will now complete the full plan, which includes installing new presses, sewing and in-line binding equipment, and capacity for casing-in (the process of adhering a finished book to hardbound covers).
Quebecor World expects the phase II expansion to be finished by the middle of 2004's second quarter. With the completed expansion, the Dubuque facility will appreciably increase its capacity to produce elementary, secondary and higher education textbooks. The added capacity will enlarge the company's current 300-worker Dubuque work force by a third.
"This is a market that Quebecor World has identified as having strong potential for future growth," Boles said in announcing the Dubuque expansion's second phase. "We believe the demographics and product dynamics will continue to generate increased opportunities over the years. Our customers have indicated that an investment in a specialized facility is the correct approach to capturing this market."
Rich Dunn, vice president and general manager of Quebecor World Dubuque, credited the expansion to "the combination of skilled craftsmanship demonstrated by our employees and the company's investment in state-of the-art technology."
Quebecor World officials also praised Greater Dubuque Development Corporation and city officials for their project assistance, which included securing state training funds.
Editor's note: Look for further coverage of the Quebecor project and the Dubuque and Iowa business climate in the November 2003 issue of Site Selection.
pw0818bpw0818b
PLEASE VISIT OUR SPONSOR CLICK ABOVE
©2003 Conway Data, Inc. All rights reserved. Data is from many sources and is not warranted to be accurate or current.
|