Facility Could Employ 400
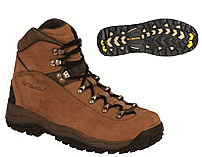 The Kentucky distribution center will make for faster deliveries at lower costs for footwear products like the Columbia boot pictured above.
|
|
Boots Made for Walkin': Columbia Sportswear Picks Kentucky for New Distribution Center
by JACK LYNE, Site Selection Executive Editor of Interactive Publishing
DIXON, Ky. Re-jiggering its supply line to better tap a key customer segment, Columbia Sportswear is building a US$40-million, 428,000-sq.-ft. (38,520-sq.-m.) footwear distribution center in Dixon, Ky., that may employ as many as 400 workers.
Portland, Ore.-based Columbia's active outdoor apparel has rung up bullish business during the economic downturn, with last year's $816 million in sales marking a 273-percent increase from 1996. Until now, though, those popular products have only been distributed in the U.S. from Columbia's 850,000-sq.-ft. (76,500-sq.-m.) operation in Portland.
That left a large U.S. delivery-system gap. Seventy percent of Columbia's footwear sales comes from the U.S. East Coast and Midwest. And the company's line of hiking boots, shoes and sandals registered 24-percent average annual sales increases from 1998 to 2002, said Columbia President and CEO Tim Boyle.
That missing supply-chain link, he explained, prompted the search for the new center, which will be built on a 68-acre (27-hectare) Henderson County site.
"We have identified the Midwest and East Coast as key regions, where cold weather outdoor activities requiring inclement weather footwear are consistently popular, and where the company can continue to grow," Boyle said. "The construction of this new facility underscores Columbia's commitment to our growing footwear business."
The new operation will boost cost-efficiencies as well, he added. The western Kentucky center will enable Columbia to make two-day East Coast and Midwest deliveries of its often-heavy footwear. Those deliveries will be headed to retailers like JC Penney, Famous Footwear, Kohl's and REI, which handle final sales.
Several other unnamed Midwestern locations were also considered for the distribution center, Boyle said.
Construction will begin this fall. The operation, added Boyle, will be designed to be expanded to 836,000 sq. ft. (75,240 sq. m.), which could increase the work force to 400. The company currently has some 1,800 employees.
Park Picked Is a Four-County Cooperative Effort
Columbia's site in the 4 Star Industrial Park also represents a win for regional economic development. Opened in 2000, the 900-acre (360-hectare) park is a cooperative venture of four Kentucky counties: Henderson, McLean, Union and Webster.
That sort of teamwork is the wave of the future, Gov. Paul Patton (D) asserted in commenting on the Columbia project.
"The future success of economic development efforts will rely on approaches that rise above political boundaries and help regions, not just individual communities," said Patton. "I want to commend Henderson, McLean, Union and Webster counties for the cooperative effort in developing the 4 Star Regional Industrial Park and their work on this project."
The regional industrial park concept has been one of the Patton administration's major initiatives. Kentucky's regional park program was cited as a best practice by the National Association of Regional Councils, a nonprofit advocating federal and state policies that promote regional cooperation and growth.
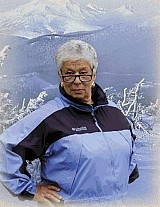 Tough mother: Seventy-nine-year-old Columbia Chairman Gertrude Boyle is credited with turning a marginal company into a very profitable enterprise. Boyle even stars in the company's highly successful commercials, pushing her son, CEO Tim Boyle, through demanding product testing in blizzards, driving rainstorms and car washes. |
|
Columbia's center will mark 4 Star's first tenant. But some creativity was required in landing the project after 16 months of recruitment.
None of 4 Star's existing parcels were large enough to accommodate Columbia's needs. So the park purchased an unused 51-acre (20-hectare) tract from KB Alloys, which operates an adjacent grain refining and hardener alloy plant.
Bond Payoff Will Fund Project
Columbia's occupancy agreement is also inventive.
Initially, 4 Star's board will hold the site's title. The Henderson Regional Industrial Development Authority is financing the project by issuing up to $49 million in industrial revenue bonds (IRBs). Columbia, however, will be responsible for all bond payments. Once the bonds are retired, Columbia will own the site.
That arrangement will enable the company to avoid paying property taxes for the bonds' 25-year payoff period. Columbia will also circumvent sales taxes on construction materials.
The company, however, will pay the Henderson County school property tax annual equivalent, which is in line with the county's IRB policy. In addition, Columbia unilaterally insisted on paying the equivalent of the Henderson County Public Library tax, county officials said.
Federal Aid Helps with Funding
The project is also getting additional assistance.
The Kentucky Cabinet for Economic Development has pledged up to $2 million in tax incentives. And local government has pledged $3.2 million to buy KB Alloys' land, build temporary construction and permanent roads to the site, and install water and sewer lines.
The recruitment side of the location equation is also getting some help.
Park officials expect a $150,000 grant for the Columbia facility's sewer lines from the Delta Regional Authority. The authority, a federal-state partnership, last year approved a $500,000 grant for 4 Star's phase-one sewer construction.
In addition, the park board earlier this year received more infrastructure improvements funding through a $450,000 zero-interest loan from the U.S. Agriculture Department and $360,000 from the Kentucky Transportation Cabinet.
There's also more potential state aid on tap. The Cabinet for Economic Development has pledged up to $200,000 to cover any project funding shortfall.
The Kentucky center, however, isn't actually Columbia's second distribution center. That distinction goes to Cambrai, France, where the company opened a center in December of 2002 to support its growing European sales.
Editor's note: For more on the Columbia Sportswear project, watch for the Ohio River Corridor coverage in the upcoming November issue of Site Selection.
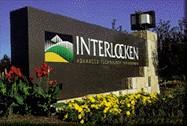 Sirenza Microdevices has taken its 220 jobs to Interlocken Technology Park (pictured), whose other tenants include Sun Microsystems, Ernst & Young, Level 3 Communications and McKesson. |
|
Sirenza Relocates Silicon Valley HQ, 220 Jobs to Metro Denver
by JACK LYNE, Site Selection Executive Editor of Interactive Publishing
BROOMFIELD, Colo. Go east, young technology company.
That seems to be the reworked headquarters location logic powering Sirenza Microdevices. A manufacturer of high-performance radio-frequency (RF) chips for communications equipment, Sirenza has traded its tony Silicon Valley address for new digs in Colorado's Rocky Mountains.
In a move reflecting the Golden State's well-documented business climate problems, the company has relocated its headquarters from Sunnyvale, Calif., to Broomfield, Colo. And it's not only headquarters jobs that have come to Colorado. The company has also centralized all of its manufacturing in Broomfield. All told, the move involves 220 jobs.
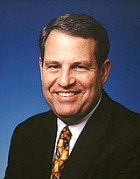 Sirenza's metro-Denver relocation and consolidation is saving the company $10 million a year in operating costs, said President CEO Robert Van Buskirk (pictured). |
|
The decision driver: costs, along with Sirenza's May acquisition of Denver-based Vari-L, a manufacturer of wireless communications RF and microwave components and devices.
"This move will improve our efficiencies, lower our operating costs and accelerate the process of integrating Vari-L's operations into Sirenza," said President CEO Robert Van Buskirk.
Relocation Savings: $10 Million a Year
There's a lot of money lurking in Van Buskirk's rationale. All told, the company says that it is saving $10 million a year in operating costs with its metro-Denver relocation and consolidation.
Slashed occupancy costs are accounting for much of the capital saved in Colorado. Founded in California in 1989, Sirenza is leasing two facilities totaling 74,000 sq. ft. (6,660 sq. m.) in the 936-acre (374-hectare) Interlocken Technology Park. The company at Interlocken is paying less than $5 per square foot a year, said Van Buskirk, who called the new space "radically up-scaled." In Silicon Valley, Sirenza was annually paying $25 to $30 per square foot, he said.
The company has also upped it cost-efficiencies, added Van Buskirk, by co-locating its six manufacturing plants in one of the Interlocken facilities. Four of those plants were already in the Denver-metro area, while one was in Sunnyvale and the other in Tempe, Ariz.
Sirenza, which officially dedicated its new headquarters last month, has found further savings by successfully consolidating its IT systems into a single platform. And, finally, there are the savings coming from the 25-percent reduction of the combined work force of Sirenza and Vari-L.
Poll: 20 Percent of Companies
Planning Out-of-State Projects
Sirenza isn't exactly the Lone Ranger in its eastward move from California.
A broad range of state-based companies have bemoaned California's business costs, particularly its high workers' comp and energy rates. And the state's complex regulatory framework, $38-billion budget deficit and a fractious gubernatorial recall add further to business discontent.
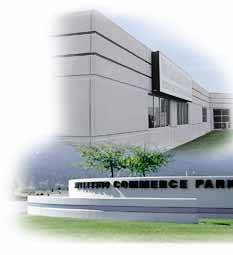 Buck Knives, a 101-year-old company, is also leaving California, heading for Riverbend Commerce Park (pictured) in Post Falls, Idaho. |
|
No reliable records exist for business migration from the state. But an April survey conducted by California Business Roundtable and California Chamber of Commerce couldn't have been reassuring for business recruiters. Twenty percent of polled corporate leaders said that their companies planned to expand or relocate outside the state because of California's costs and regulations.
In response, a group of state business leaders is fighting back through the Coalition for California Jobs (CCJ), which formed in May. The CCJ has mounted a "Jobs 1st" campaign to communicate with constituents about how state legislators are voting on bills that affect California employment.
"Policymakers 'talk the talk' about protecting jobs in California, but far too often their votes don't 'walk the walk,' " said California Chamber of Commerce President Allan Zaremberg. "The Jobs 1st campaign is designed to ensure that people know the voting record of their legislators on bills that affect jobs. You can't say you're pro-jobs and then vote for bills that kill jobs, including expanded workers' comp benefits, without cost-saving reforms, more burdensome regulations, higher taxes and fees, health-care mandates, and more litigation."
Buck Knives Also Headed Elsewhere
Meanwhile, some other in-state companies are still headed out.
One of them is Buck Knives. A California corporate citizen since just after World War II, the company is leaving its current headquarters in El Cajon in San Diego County to relocate in Post Falls, Idaho. By 2005, Buck Knives plans to have its operations base inside a 110,000-sq.-ft. (9,900-sq.-m.) facility that it's building in Post Falls' Riverbend Commerce Park.
Occupancy costs again loomed large in the decision. The 101-year-old knife manufacturer has put its 10-acre (four-hectare) site in El Cajon on the market, with an asking price of $9 million. By comparison, Buck is buying its new 12-acre (five-hectare) site in northern Idaho for about $800,000, company officials say.
The Gem State relocation promises other cost cuts as well. Buck Knives' executives estimate that the company's energy costs could fall by as much as 60 percent, and workers' comp costs could decrease by as much as 40 percent. In addition, the company expects a 20-percent cut in its current wage and benefit outlay.
Adding to Buck's savings is the $3,000 per employee that it's receiving from the state for worker training.
Such cost reductions are a high-priority consideration for the company during the economic downturn. Buck's annual sales have dropped by a fourth since 1995.
Idaho is only one of the east-of-California states that's benefiting from some Gold State firms' cost-cutting relocation notions. Colorado is another. And Gov. Bill Owens seemed to be differentiating his state from California in welcoming Sirenza Microdevices.
"In addition to offering a superior quality of life, Colorado is a business-friendly state," said Owens, "that provides technology companies with a highly educated labor pool and a strong technology infrastructure."
Editor's note: In the Rocky Mountain States Regional Review in the brand-new September issue of Site Selection, you'll find further tales of companies relocating to Idaho and Colorado, including yet another from California.
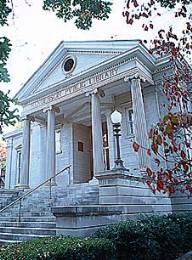 C.R. Bard already had two division headquarters and a Southeast distribution center located in Covington (pictured: the Henderson County courthouse in Covington). |
|
Bard Centralizing Distribution, Adding 130 Workers in Metro Atlanta
by JACK LYNE, Site Selection Executive Editor of Interactive Publishing
COVINGTON, Ga. Further consolidating its considerable presence in north Georgia, medical device manufacturer C.R. Bard is adding 130 employees in Covington, Ga. The new jobs stem from the company's decision to create a national distribution center in Covington. The operation will handle some 90 percent of C.R. Bard's entire output, company officials estimate.
And that adds up to a lot of output. Developer of the first balloon catheter, Bard now provides over 7,000 products and services to customers in the Americas, Asia and Europe. With the company recording 2002 sales of $1.27 billion, that means the Georgia center will likely handle more than $1 billion a year in products.
Covington, which sits some 35 miles (56 kilometers) east of downtown Atlanta, already contained major Bard operations. The Murray Hill, N.J.-based company has two of its divisional headquarters, Bard Medical and Bard Urological, in the city. In addition, Bard has an existing distribution operation in the city focused on the U.S. Southeast.
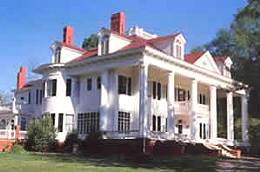 Covington is also home to vintage architecture, including Whitehall (pictured), a Greek Revival-style residence built in the 1930s that Gone With the Wind author Margaret Mitchell chose as the model for the Hollywood set for Twelve Oaks, the home of Ashley Wilkes. |
|
All told, Bard has some 500 employees in Covington, ranking as Newton County's second-largest private-sector employer.
Labor, Transportation Big Distribution Drivers
One of Covington's corporate citizens since 1967, Bard picked the Georgia location in part because of the quality of the local work force, company officials said.
"The high quality of Newton County's work force - people with both skills and a tremendous work ethic - was one of the key factors in our decision to build and expand here," said James Natale, president of corporate health-care services.
The Atlanta area's status as a major transportation hub was also an obvious major factor, Bard officials said. Covington, for example, is only 42 miles (67 kilometers) from Hartsfield International Airport.
The Peachtree State also has a strong existing cluster in Bard's industry niche.
"Georgia has long been known for its strength in the medical device industry," said Carol Henderson, a senior project manager with the Georgia Department of Industry, Trade & Tourism, pointed out in commenting on the Covington project. Ernst & Young recently ranked Georgia as the nation's ninth-largest life sciences center. (North Carolina, ranked as the fourth-largest center, landed this week's Blockbuster Deal, a KBI BioPharma biomanufacturing plant that could employ as many as 550 workers in Durham.)
Temp Space Deal Helps Seal Decision
Bard has chosen a 38-acre (15-hectare) site in Lochridge Industrial Park for its 411,184-sq.-ft. (37,006-sq.-m.) distribution center.
Atlanta-based park developer Pattillo Cos.' agreeing to provide temporary space was a key factor in selecting the site, company officials said. Pattillo Construction Co., a Pattillo Cos. arm, will develop the build-to-suit facility while Bard's national distribution function is housed in other temporary quarters in Lochridge Industrial.
The 130 jobs are well-timed news for the Covington area. Newton County's population has been expanding rapidly, straining the local job market. Newton, in fact, ranked as the seventh fastest-growing U.S. county in 2002, according to Census Bureau data.
"We are very excited to be chosen for the new distribution center," said Adam Jones, director of economic development for the Newton Chamber of Commerce. "This comes at a very good time. C.R. Bard has demonstrated a commitment to the Covington area with the addition of its new distribution center, and we have been very impressed with its corporate citizenship."
That corporate citizenship includes the company's being one of the major corporate sponsors for the area's Healing Hands Clinic. The clinic helps uninsured residents of Newton and Rockdale counties receive a range of free health-care services, including dental care, immunizations, pap smears and physicals. Healing Hands now sees more than 3,000 patients a year.
pw0818bpw0818b
PLEASE VISIT OUR SPONSOR CLICK ABOVE
©2003 Conway Data, Inc. All rights reserved. Data is from many sources and is not warranted to be accurate or current.
|