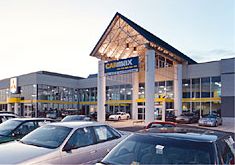 CarMax plans to build between 34 and 44 new stores (like the one pictured above) between 2004 and 2007, which could double the company's current number of operations. |
|
CarMax Cruises, But Opts to Keep HQ Parked in Virginia
by JACK LYNE, Site Selection Executive Editor of Interactive Publishing
GLEN FALLS, VA. After cruising a few other Southeast U.S. cities as well, CarMax has decided to keep its 600-employee headquarters parked in the Richmond, Va., metro.
But the automotive retailer is moving nonetheless. CarMax will relocate its current Richmond-area headquarters in Glen Falls to the 3,500-acre (1,400-hectare) West Creek Business Park in Goochland County.
Buoyed by strong business, the company was outgrowing its existing operations base, President and CEO Austin Ligon said in explaining the move. The new facility, he added, will provide a larger footprint that can accommodate a gradual increase of headquarters staffing for CarMax, which was founded in Richmond in 1993.
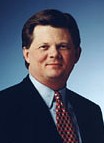 "It is only fitting that as we celebrate CarMax's 10-year anniversary, we announce we are staying in Virginia," said President and CEO Austin Ligon (pictured). |
|
"It is only fitting that as we celebrate CarMax's 10-year anniversary, we announce we are staying in Virginia," said Ligon. "CarMax was created here, and thanks to the cooperation of state and Goochland County officials and the owners of West Creek, our decision to stay was an easy one."
Considering a Higher-Profile Site,
Or Simply Covering All Its Bases?
Maybe it was an easy decision; maybe not.
CarMax also considered two other Southeast cities, with Atlanta apparently getting a long look, company officials confirmed.
The Southeast was a logical location palette for CarMax's headquarters search. The region is the retailer's strongest sales territory, especially for used cars, which continue to be the company's business bread and butter.
CarMax, however, already had a strong presence in the Richmond area, where it humbly began with a single store. The company has about 13 percent of its 8,800 employees in the metro, with the headquarters staff and more than 550 employees at area stores in Richmond and Sterling, Va.
Nonetheless, CarMax decided to consider locations outside its corporate birthplace. That decision may have reflected a desire to establish its base in a Southeast city with a more central location and a higher profile. Such a site would have matched CarMax's current high-profile growth mode. The company recently announced that it plans to build between 34 and 44 new stores between 2004 and 2007. That plan could conceivably double the company's current total of 44 stores in 15 states, most in the Southeast and Midwest.
The growth reflects the strong demand - particularly in new stores - generated by CarMax's model, with no-haggling, below-Blue-Book pricing. "Our new stores delivered results significantly above our expectations," Ligon noted to the Securities and Exchange Commission in a March 31 8-K form, which is generally used to notify the SEC of an unusual matter that could have an impact on the company's stock prices. "The severe winter weather impact in the fourth quarter was partially offset by the strong performance at our new stores," Ligon said.
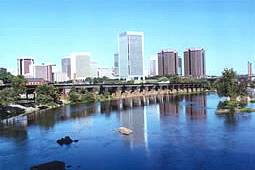 CarMax has some 13 percent of its total work force based in and around Richmond (pictured). |
|
That strong performance included CarMax's 12 percent gain in net sales and operating revenue - going from $3.52 billion to $3.97 billion - in its latest fiscal year, which ended on Feb. 28.
Considering stes outside Richmond may, on the other hand, have not had all that much to do with wanting a higher-profile home. CarMax's aim instead may have been securing hard-number comparisons to show its board of directors.
Then again, perhaps both factors played a role in the broadened search. CarMax officials, for their part, offered no specifics that ruled either factor out - or in.
State Also Lands Cardinal Glass
For certain, CarMax will certainly have more room to expand its headquarters staff in the new Goochland County location.
The new facility at build-out may exceed 500,000 sq. ft. (45,000 sq. m.), according to Richmond-based Millennium Retail Advisors, a CarMax location and facility consultant. The first phase of the campus would cover about 200,000 sq. ft. (18,000 sq. m.), according to Hardin Construction, an Atlanta-based company that the auto dealer hired in February in securing an architect to design the new headquarters.
CarMax will join several other headquarters in West Creek Business Park, including Performance Foods and the Farm Bureau of Virginia. Capital One also has a major corporate campus in the park.
CarMax didn't announce a time frame for the relocation, which Ligon said would be completed "within two to three years." The Virginia Department of Business Assistance is providing workforce-training services for the project.
CarMax's decision was followed a week later by more good news for Old Dominion business recruiters: Cardinal Glass Industries selected the Roanoke County city of Vinton for its first Virginia facility, a 220,000-sq.-ft. (19,800-sq.-m.) insulating-glass plant that will employ 200 workers during its first 30 months of operations.
Georgia Enduring Tough Going
Georgia, on the other hand, has hit some disappointments in recent months.
In addition to losing CarMax to Virginia, DaimlerChrysler in late September pulled out of a long-delayed plan to construct a $750-million, 4,000-worker Mercedes Sprinter van plant in Pooler, Ga. (see Sept. 29 Blockbuster Deal of the Week). And that news came only some two weeks after Atlanta-based Newell Rubbermaid announced that it was ditching its previously unveiled plans for a new 225,000-sq.-ft. (20,250-sq.-m.) corporate campus. The plastic products manufacturer will instead lease between 35,000 and 45,000 sq. ft. (3,150 and 4,050 sq. m.) of north Atlanta space, company officials said.
Nonetheless, real estate consultants working in the Atlanta area report that at least four other major location projects - one a ready-to-relocate headquarters - are currently eyeing the Peach State's capital city.
Ford Motor Co. is one company that's looking. The automaker is reportedly searching for a 1,500-acre (600-hectare) site in the area for a new manufacturing plant. That search initially shrouded the future of Ford's 2,322-worker Atlanta-metro plant in Hapeville. The Hapeville plant makes the Ford Taurus and the Mercury Sable; both have slowed in sales and are expected to be phased out by the end of the decade.
The Georgia facility's future solidified, however, several days after the reports of Ford's Atlanta-area search first surfaced. The automaker announced that the Hapeville plant will begin building its Ford- and Lincoln-branded sport wagons in 2006. Ford had earlier announced that those vehicles would be made in Canada.
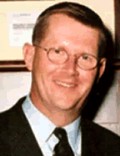 GFS was 'particularly pleased with the quality of people we see in the Shepherdsville-area employee pool," said Executive Vice President Jim Gordon (pictured). |
|
Gordon Food Taps Louisville, Ky., Metro for $79-Million, 280-Worker Distribution Center
by JACK LYNE, Site Selection Executive Editor of Interactive Publishing
SHEPHERDSVILLE, Ky. International Distributors (ID) is - quite literally - bringing some large-scale economic news to little Shepherdsville, Ky., a city of some 6,000 residents.
A subsidiary of Grand Rapids, Mich.-based Gordon Food Service (GFS), ID has unveiled plans to build a new $79-million, 300,000-sq.-ft. (27,000-sq.-m.) distribution center employing 280 workers at the Bullitt County site in the Louisville metro. And the facility will stand tall in the community in ways extending beyond its obvious job-generating stature: At 10 stories, it will be more than twice as tall as any other building in Bullitt County.
The Shepherdsville facility will use floor-to-ceiling automated cranes to shift food pallets between its 10 stories of stacks. The building's advanced design will make the operation the "flagship" of the company's distribution network, said Jim Gordon, executive vice president of GFS, North America's largest family-owned and -managed food-service distributor.
The Bullitt County facility will be the company's seventh U.S. distribution center. It will join GFS's existing distribution operations in East Bernstadt, Ky.; Grand Rapids and Brighton, Mich.; Martin, Tenn.; Miami, Fla.; and Springfield, Ohio. That network reflects the company's regional geographic focus, with operations primarily targeted in 10 states that stretch from Florida to Michigan, as well as in southern Canada. The 5,000-employee company's regional approach rang up $2.75 billon in 2002 revenues.
GFS Muscling Up Kentucky Presence
GFS was already familiar with Kentucky, one of the 10 primary states in which it delivers food products to more than 30,000 customers, including hospitals, nursing homes, restaurants and schools.
Moreover, on Jan. 1, 2001, GFS acquired Bluegrass State-based ID, one of the six corporate monikers under which the company operates. ID distributed food in parts of eight Southeast and Midwest states. GFS's acquisition included ID's distribution center and headquarters in East Bernstadt, a central Kentucky city some 150 miles (240 kilometers) southeast of Louisville.
GFS, however, previously hadn't fully tapped potential business in and around Louisville, the state's largest city. That, though, is changing. The company has chosen Jeffersontown, Ky. (part of the Louisville metro), for its first GFS Marketplace retail store. GFS has 95 Marketplace stores in Michigan, Ohio, Indiana and Illinois, which sell in bulk (a la Sam's Club) to both the general public and existing commercial customers. GFS plans to rapidly build more Louisville-area stores, said Scott, a great-grandson of Isaac Van Westenbrugge, the recent Dutch immigrant who founded the company in Grand Rapids in 1897.
State's $7.5 Million in Tax Breaks
Helped Spike Site-Selection Appetite
GFS looked at about 20 sites in the Louisville metro during an eight-month distribution center search, said Scott. Shepherdsville, he explained, best fit the bill in terms of labor, location and culture.
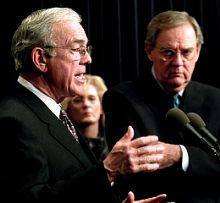 "Nothing energizes an industry or an economy like a qualified work force," Gov. Paul Patton (above left at microphone) said in announcing GFS's new distribution center. |
|
"We are particularly pleased with the quality of people we see in the Shepherdsville-area employee pool," Scott said in announcing the project. "We are excited about this location. Not only does it position us geographically to better serve our customers in the region, it gives us a home in a community that shares our corporate culture and values."
GFS's Bullitt County site positions its new distribution center 20 miles (32 kilometers) south of Louisville and just east of Interstate 65. The company is purchasing an 85-acre (34-hectare) site near Cedar Grove Business Park from a local developer. Construction, said Gordon, could begin next year, with the operation's projected start-up in 2006.
The distribution center will initially go online with 150 employees. GFS plans to increase the operation's work force to 280 over a five-year period, Gordon said.
The Kentucky Economic Development Finance Authority whetted the food distributor's site-selection appetite with $7.5 million in state tax breaks. The incentives will be used to offset part of the project's start-up costs, GFS officials said.
Editor's Note: For insights into the food processing industry, look for the Industry Focus feature in the upcoming November 2003 issue of Site Selection.
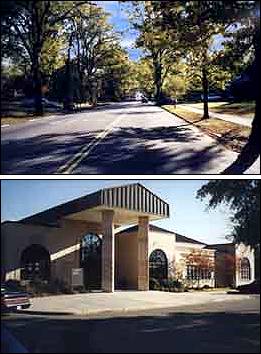 GOJO Industries will bring its 250-employee plant to Laurinburg (whose main street and courthouse are pictured above), a city of 17,000 in southeast North Carolina. |
|
GOJO Gets North Carolina Mojo Working with New 250-Worker Plant
by JACK LYNE, Site Selection Executive Editor of Interactive Publishing
LAURINBURG, N.C. GOJO Industries is bringing a new 250-employee manufacturing plant to Laurinburg, N.C., a job-hungry area in the southeast corner of the Tar Heel State.
And the Akron, Ohio-based hand-hygiene and skin-care products manufacturer is getting a big hand up from Abbott Laboratories - a company that's actually no longer part of the area's corporate community. Abbott's aid in getting GOJO's Carolina mojo working comes in the form of a 300,000-sq.-ft. (27,000-sq.-m.) manufacturing operation that the health-care company shut down on June 27th in 2002.
The Abbott plant had been part of Laurinburg's business landscape since 1970. With 900 full-time employees and 100 contract workers, the operation had ranked as Scotland County's second-largest employer. Abbott, however, decided to transfer the Laurinburg plant's production of components for medical devices (e.g., anesthesia kits and trays and IV sets) to its facility in Rocky Mount, N.C., and to company operations in Utah and Costa Rica.
Abbott, however, decided to leave a bricks-and-mortar valentine behind to a community it had called home for more than three decades: It dedicated the closed plant to the non-profit Scotland Development Corporation, made up of city, county and chamber of commerce officials. "We hope that donating the plant will help the county to attract a quality employer," Laurinburg plant manager Brent Bowers said in announcing the dedication.
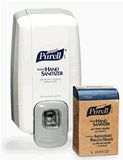 The Laurinburg plant will make Purell (pictured), GOJO's flagship product and a strong seller in both the institutional and retail markets. |
|
Local recruiters aggressively began marketing the facility, eager to bring in new jobs to an area that sorely needed them. Scotland County's current unemployment rate stands at 12 percent, almost twice the national average.
GOJO answered opportunity's knock. The company will retrofit the old Abbott operation to manufacture Purell, the hand sanitizer that's its flagship product.
Building, Land Valued at $15.5 Million, but
'Expansion and Growth and Speed' Drove Project
GOJO will spend some $10 million on the retrofit, said company COO Mark Lerner.
But Abbott's donation also provides GOJO with what county officials at the plant's donation called "a multimillion dollar incentive package to bring a potential employer into the area." The former medical-device plant and its 50-acre (20-hectare) site are valued at $15.5 million. The complex includes a 190,000-sq.-ft. (17,100-sq.-m.) manufacturing facility, as well as a 110,000 sq.-ft. (9,900-sq.-m.) warehouse.
The financial windfall from the free land and facility, however, wasn't a deal-maker in GOJO's decision, Lerner said. Rather than savings, he insisted that the Laurinburg project was "about expansion and growth and speed."
Facility Online by January 2005
The old Abbott facility will provide many speed-promoting particulars.
One of them is the clean rooms that are part of the closed plant. The manufacturing process for Purell, a waterless, alcohol-based "instant hand sanitizer," requires clean-room space, Lerner said.
In addition, the site and facility remain in excellent condition, despite the 16 months that have passed since the closing. Abbott Labs since the shutdown has, of its own volition, been spending $25,000 a month in maintaining the plant.
The ship-shape facility's fit with GOJO's manufacturing needs will enable the new plant to be up and running as soon as January of 2005 - excellent speed for a facility with pharmaceutical-level requirements. Coming online that rapidly will help capitalize on demand for Purell, Lerner explained. Already a strong seller with institutional users like health-care and food-service operations, Purell enlarged its market when GOJO launched it in the retail sector in 1996.
State officials further aided the project by providing GOJO with $250,000 from the One North Carolina program. The funds will be used for the building retrofit and new equipment purchases.
Laurinburg/Scotland County Area Chamber of Commerce President Andy Foshay lauded the project as "a joint effort with Abbott Laboratories, the state of North Carolina, the city of Laurinburg, and Scotland County that made this possible."
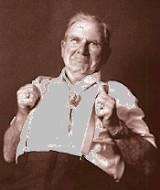 An Akron rubber plant worker during World War II, GOJO Founder Jerome Lippman (pictured) came up with the idea of a stain-cutting soap that would work with or without water. Photo: GOJO Industries |
|
Abbott Laboratories, still keeping tabs on its former home, was also pleased.
"We are delighted there is a new owner for the facility," said Dale R. Johnson, Abbott's divisional vice president of state government affairs. ''We hope the Laurinburg community will benefit as a result, and that the area will continue to grow and develop."
Resourceful Project Reflects GOJO's Founding
The Scotland County community's resourcefulness in landing GOJO parallels the company's beginnings.
GOJO Founder Jerome Lippman worked, along with wife Goldie, in an Akron rubber plant during World War II. Dirty hands were part of the rubber plant workers' lot, with hard-to-remove stains coming from graphite, tar and carbon black. Chemicals like benzene cut those stains, but they irritated the skin and presented health hazards as well.
Still laboring at the rubber plant, Jerome began working with Kent State University professor Clarence Cook to develop a stain-cutting soap that would work with or without water. Eventually, the two men came up with a product they called GOJO.
Emboldened, Jerome quit his factory job and began to spend his nights making GOJO in an old washing machine tub. During the days, he visited auto-maintenance garages, persistently peddling his new product.
Jerome's doggedness paid off. GOJO Industries was founded in 1946. Still privately held, the company's products are now used worldwide in schools, manufacturing plants, hospitals, health-care facilities, restaurants, automotive service and repair shops, arenas, recreational facilities, and public and commercial buildings.
pw1013bpw1013b
PLEASE VISIT OUR SPONSOR CLICK ABOVE
©2003 Conway Data, Inc. All rights reserved. Data is from many sources and is not warranted to be accurate or current.
|