AAA Takes Sharp Turn - and 750 Jobs - into Delaware
by JACK LYNE, Site Selection Executive Editor of Interactive Publishing
WILMINGTON, Del. The American Automobile Association (AAA), that steady beacon of reliability for 44 million U.S. and Canadian motorists, has mapped out its own sudden, unexpected trip, shocking two states in the process, while delighting another: AAA's Mid-Atlantic regional arm is relocating some 750 jobs - including its headquarters - to Delaware from Maryland and Pennsylvania.
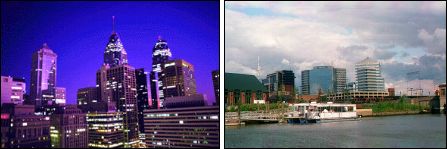 Headquarters, present and future tense: AAA Mid-Atlantic's current headquarters in Philadelphia's Center City (pictured at left) will relocate to Wilmington on the city's frontage on the Christina River (pictured). |
|
News of the moves hit Maryland and Pennsylvania like some sharp, unexpected hairpin curve on a winding two-lane road at midnight. Both states' economic development leaders said that they were stunned by AAA Mid-Atlantic's relocations.
Scheduled for mid-2005, the moves are strictly business, AAA officials explained. The relocations to Newark and Wilmington will bolster the Mid-Atlantic branch's finances and operational efficiencies for its 3.5 million members, they said.
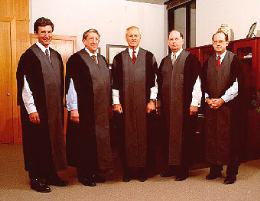 One of Delaware's attractions is its Chancery Court (pictured), recognized as a fast-working, no-nonsense forum for business issues. |
|
"These changes are required to strengthen and refocus our business so that AAA Mid-Atlantic can more effectively serve its expanding membership base," President and CEO Allen J. DeWalle said in announcing the decisions at Wilmington's Riverwalk.
AAA: Key Factors Included Costs,
Centrality, Favorable Tax Structure
The relocations will shift all of AAA Mid-Atlantic's well-paying jobs from two operations. Currently in Philadelphia's Center City, the 350-employee headquarters will move to Wilmington. And a 400-employee call and operations center in Elkton, Md., will move to Newark (where DaimlerChrysler late last year completed a $180-million retooling of its plant to make a larger Durango SUV). AAA plans to lease space at both locations, officials said.
"The headquarters relocation has both economic and practical benefits for this organization." DeWalle said at the Riverwalk, not far from the future headquarters site. "The Delaware sites were picked for their central location, lower total business costs, a competitive tax structure and favorable incentives."
Most of those factors have strong economic implications. That, said DeWalle, "will clearly help reduce overhead costs to our members' benefit. As a membership organization, we have an obligation to operate in as cost-effective a manner as possible."
Another headquarters relocation driver, he added, was to better align central operations with the organization's current geographic focus. The Mid-Atlantic's territory has broadened since it first opened its headquarters in Philadelphia more than 100 years ago, DeWalle explained.
"[We] once served only the Philadelphia region," he noted, "but our service area now spans from Northern New Jersey to Southern Virginia. We have a regional footprint, [and] we need to be able to easily reach locations throughout."
More Central Sites Actually Close by
How much more central the new sites are, though, will surely be questioned.
Philadelphia, for example, sits only some 29 miles (46 kilometers) southwest of Wilmington. And Elkton is an even shorter drive, only some eight miles (13 kilometers), from Newark.
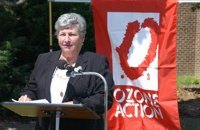 Gov. Ruth Ann Minner (pictured at a press conference last year) and state economic officials began wooing AAA Mid-Atlantic a year ago.
|
|
In fact, the new locations are so close that DeWalle said that AAA expects about half of its 750 affected employees to transfer to Delaware.
Many observers will also surely question the decision-swaying clout of Delaware's incentives. While substantial, those subsidies look rather modest, considering the coveted 750-job prize.
AAA Mid-Atlantic is receiving a $6-million state performance grant (tied to job creation), plus Wilmington's $1 million in incentives.
But what Delaware's economy gets in return is a $100-million-a-year boost, Gov. Ruth Ann Minner's (D) office estimated.
Business Costs, Tax Structure
Likely Key Relocation Considerations
Instead, the real deal-makers for AAA were likely Delaware's lower business costs and business-friendly taxes.
The state's tax structure, in fact, has made it a headquarters haven. Delaware corporate laws' predictability and flexibility are widely revered. And the state's tax structure conforms to the federal definition of "corporate net income," adding an edge in securing maximum benefits from federal corporate tax law changes.
In addition, Delaware has a Chancery Court that specifically handles business issues. The state also levies no personal property taxes, intangible property taxes or sales taxes on state-based corporations.
Such features have boosted the state's standing in many studies of business-friendliness.
Delaware, for example, was named the 10th-most "pro-business state" in a study last year by Chicago-based real estate consultancy Pollina Corporate Real Estate. And a 2003 Hudson Institute study on business costs and productivity ranked Delaware in a tie for No. 5.
"Tax competition among states is an unpleasant reality for state revenue raisers," said Scott Hodge, executive director of the Tax Foundation, a nonprofit that promotes better public knowledge of taxes.
"But competition is a godsend to taxpayers," added Hodge. "The most effective restraint on state taxes is the knowledge that business will take jobs and prosperity out of state if taxes become unmanageable."
Recruiters' Information Varied Widely
AAA Mid-Atlantic officials, however, certainly didn't say anything critical of Maryland and Pennsylvania's taxes. Neither did they specify how decisive a role Delaware's costs and taxes played.
Things left unsaid also generated some post-announcement head-scratching among competing business recruiters. Apparently, some were working with widely divergent data about what was happening.
Maryland's Cecil County, for example, competed for AAA's headquarters. But county officials conceded that they had no inkling that the Elkton center might also relocate.
Philadelphia officials, on the other hand, apparently weren't fully aware of how seriously AAA Mid-Atlantic was considering an out-of-state move. The city only several months ago first talked to AAA to make an offer to retain the headquarters, Philadelphia officials recounted.
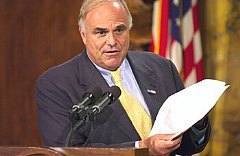 Philadelphia, said Pennsylvania Gov. Ed Rendell (pictured at a 2003 press conference) must have "an earlier warning system to find out when leases expire." |
|
"There's got to be an earlier warning system to find out when leases expire," Gov. Ed Rendell (D) told the Greater Philadelphia Chamber of Commerce's CEO Council for Growth soon after the relocation announcements. "We can't just leave it to happenstance," added the governor, who urged the CEO Council to form a task force tracking soon-to-expire leases.
Then there were Delaware's officials, who apparently knew, at some point, that both operations were in relocation-ready mode.
"We worked very hard to convince AAA Mid-Atlantic of the benefits of locating in Delaware, and we were persistent in our pursuit of the total package," said Gov. Minner.
But just when AAA Mid-Atlantic added the Elkton center to the moving mix is murky. Mid-Atlantic spokeswoman Colleen Healey said that the Maryland center's relocation was tacked on only after the headquarters move was approved. Moving both operations to Delaware "was the most logical choice," she said.
And the moves will reduce the distance between the two facilities to some 13 miles (21 kilometers), 28 miles (45 kilometers) less than the current trek.
State's Private Sector Helped Courtship
Delaware's recruiting efforts, on the other hand, got major mileage from the state's private sector.
The First State first got wind of a possible headquarters move about a year ago, tipped by AAA Mid-Atlantic board members who lived in Delaware, state officials recounted. Gov. Minner and state economic development officials quickly approached AAA to make their pitch.
Soon after, the state's recruiting team added a powerful ally: top executives of MBNA, which is headquartered in Wilmington. The world's largest independent credit-card issuer, MBNA has a whopping 10,000 Delaware employees in Wilmington, Newark, Greenville, and Dover. In addition, MBNA manages AAA's banking services.
Other Delaware business executives also joined in wooing AAA. Many were members of the state's Committee of 100, a group of private-sector leaders that monitors Delaware's economic health and promotes economic development.
That private-sector push for AAA drew lavish praise from Delaware Economic Development Director Judy McKinney-Cherry.
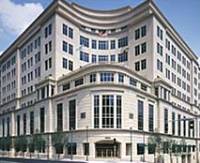 Top executives from MBNA, which has its headquarters (pictured) in Wilmington, touted Delaware's business-location advantages to AAA.
|
|
"This announcement is the result of a tremendous effort put forth by a public and private partnership," McKinney-Cherry said. "It demonstrates Delaware's power . . . to partner and to link so closely with our business community. . . . Business leaders from major Delaware companies were instrumental in making this happen."
What happened will add a cluster of quality jobs in Delaware. Headquarters employees' salaries will average between $55,000 and $60,000, AAA officials said. The Newark center, which will include call-center workers, will pay less.
Still, the 750 jobs' average salary will be between $40,000 and $45,000, said AAA officials.
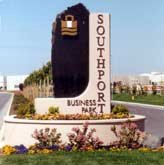 CertainTeed is going online rapidly by moving into an existing 229,000-sq.-ft. (20,610-sq.-m.) facility in the Southport Business Park (pictured), a 670-acre (268-hectare) mixed-use development owned by Summit Commercial. |
|
CertainTeed's New West Sacramento Window Plant Will Employ Up to 500
by JACK LYNE, Site Selection Executive Editor of Interactive Publishing
WEST SACRAMENTO, Calif. CertainTeed Corporation, adding what company officials called "a strategic link" in its manufacturing network, is opening a new vinyl-window assembly plant in West Sacramento, Calif., that will create up to 500 new jobs.
"This West Sacramento facility will provide us with the potential to tap into a number of high-growth markets in the western United States," Harald Jacobsen, president of CertainTeed's Window Group, said of the project. "It fills in a key piece of our strategic direction for the future."
The company's future direction is aimed toward establishing itself as a nationwide, fully integrated manufacturer and supplier of vinyl windows. The new West Sacramento plant plugs what has heretofore been a large gap in building a national network.
Up till now, using CertainTeed vinyl windows in northern California necessitated ordering them from one of the company's two nearest plants in the western U.S.; and neither was all that near. One plant is in Corona, Calif., some 430 miles (688 kilometers) to the southeast, while the other is in Auburn, Wash., some 742 miles (1,187 kilometers) to the north.
CertainTeed picked West Sacramento, Jacobsen explained, for its location between the Auburn and Corona plants, as well as for the area's ready access to some of the region's most rapidly growing construction markets and its strong local work force.
The Sacramento area already includes sizable several window-assembly operations. One of them is Tacoma, Wash.-based Milgard, the largest window manufacturing company in the western U.S., which employs about 500 workers at its 300,000-sq.-ft. (27,000-sq.-m.) plant in Sacramento.
Selecting Existing Facility Will Speed
Operation's Time in Getting Fully Online
Valley Forge, Pa.-based CertainTeed eventually plans to employ as many as 500 workers in three eight-hour shifts, Jacobsen said. Most of the West Sacramento jobs will be assembly-work positions.
The company is setting up its plant in a leased 215,000-sq.-ft. (19,350-sq.-m.) facility inside the 670-acre (268-hectare) Southport Business Park. Owned by Summit Commercial, the mixed-use park's corporate clientele already includes Cal Sierra Express, Crum & Crum Logistics, Evergreen Floral Imports, Mesa Beverage and Nor Cal Beverage.
The plant will open with a staff of about 125 employees. And it will open soon, getting up and running as rapidly as this summer, Jacobsen projected. Selecting an existing facility is helping compress the time frame for getting the company's new West Coast operation online.
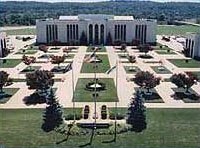 With its headquarters (pictured) in Valley Forge, Pa., Saint-Gobain subsidiary CertainTeed employs some 8,300 U.S. workers. |
|
So, too, will a team of experienced manufacturing employees from CertainTeed's operations in Auburn and Corona. That team will be temporarily assigned to West Sacramento to assist in facilitating the plant's initial operations.
"The support that these knowledgeable and seasoned employees offer will help assure an efficient and effective start-up," Jacobsen explained. "We can expect this facility to deliver a high level of service for our customers throughout the region."
Sacramento Area's Heavy New-Home
Construction Action Will Aid Plant Ramp-Up
Initially, though, CertainTeed will limit shipments of the new West Coast plant's output to within a 25-mile (40-kilometer) radius of Sacramento.
As output and staff both increase, shipments will reach further afield, extending westward - particularly to the key San Francisco market - as well as northward up to the Oregon border, said Jacobsen. The plant's location gives its strong access to I-80 and I-5, as well as U.S. 50, he added.
The Sacramento area's current heavy construction activity will help in absorbing the plant's initial output. Home builders in the region's El Dorado, Placer, Sacramento and Yolo counties sold 15,300 new houses in 2003, according to market research from the Gregory Group. Last year's total came close to reaching the area's annual record, the 15,850 new homes sold in 2002.
The West Sacramento plant will add to CertainTeed's current work force of some 8,300 employees. The 100-year-old company registered sales of some $2.6 billion in 2002 (the most recent year for which complete data are currently available), and anticipates an increase in 2003's final tally.
CertainTeed's unusual name comes from one of its early slogans: "Quality Made Certain, Satisfaction Guaranteed." That catchphrase was later condensed to form the company's current moniker. CertainTeed is now a subsidiary of France's Saint-Gobain, which acquired the company in 1988.
The Sacramento facility is the latest installment in the company's flurry of expansion activity. CertainTeed last year announced that it would open other new plants in Sherman, Texas, and South Buffalo, N.Y.
The company further filled out its nationwide network late last year with two other projects: the completion of an expansion of its manufacturing operation in Shakopee, Minn., and the launch of a new plant in Lebanon, Ind.
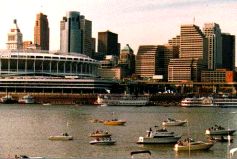 Part of the metro around Cincinnati (pictured), Hamilton Township lies about 20 miles (32 kilometers) north of downtown. |
|
SUMCO Adding 260 Jobs in $51-Million Cincinnati Expansion
by JACK LYNE, Site Selection Executive Editor of Interactive Publishing
HAMILTON TOWNSHIP, Ohio Japan's Sumitomo Mitsubishi Silicon Corporation (SUMCO) is adding 260 jobs in a $51-million expansion of its plant in Hamilton Township, Ohio.
The Cincinnati-metro project will relocate part of the silicon-wafer production now performed at a West Coast plant that SUMCO has scheduled for eventual shutdown. The shift is part of the company's effort to boost cost-efficiencies and slash expenses by consolidating production.
"Our parent company has decided that we can best meet our global customers' needs by expanding our Ohio plant," Yasuo Tsujigo, SUMCO USA's president and CEO, said at the project announcement at the state capitol in Columbus. The Ohio plant's high levels of operational efficiency, Tsujigo noted, led to its selection.
In particular, company officials explained, the Hamilton Township facility is significantly more efficient than the 620-employee plant in Salem, Ore., that's heretofore done the work that's moving to Ohio. SUMCO in late 2003 announced that it will fully close the Oregon plant sometime in late 2004 or early 2005.
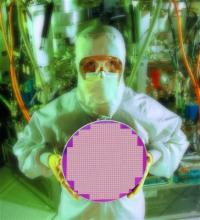 Chip-makers' shift to using larger, more cost-effective 300-millimeter wafers (pictured) has created another major economic pressure on the beleaguered silicon manufacturing sector. |
|
$21 Million in Incentives, but Only
$1 Million Allocated for Building New Space
The Ohio expansion will certainly be efficient in terms of additional space needs. The company will double wafer output at its 190,000-sq.-ft. (17,100-sq.-m.) Hamilton Township operation while investing only $1 million for a 6,000-sq.-ft. (540-sq.-m.) addition.
Of the remainder of the $51-million expansion allocation, $25 million will go to purchase new equipment. Another $25 million is budgeted to relocate some of the Salem plant's existing equipment.
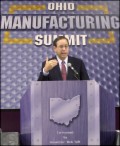 SUMCO's expansion decision is a win for Gov. Bob Taft (pictured), who has been pushing high-tech job creation through his Third Frontier initiative. |
|
The 24-year-old Hamilton Township facility makes electronic-grade silicon wafers that are used in transistors, motor controllers and transformers.
"SUMCO's plan to expand its Warren County operation is a win for SUMCO and a win for Ohio," said Gov. Bob Taft (R), who has been pushing high-tech job creation through his $1.6-billion Third Frontier initiative.
An Ohio incentive package of almost $21 million helped put the project in the win column for both SUMCO and the state. The Buckeye State's subsidies include:
an $8-million bond from the Ohio Enterprise Bond Fund, which provides subsidies for commercial and industrial expansions, funding equipment purchases, as well as the acquisition, construction, expansion or renovation of land and buildings;
a loan of up to $5 million for water and sewer improvements;
a $4-million direct loan;
a variable job-creation tax credit for up to 10 years, with an estimated value of $2.1 million;
a $900,000 grant to Warren County for highway improvements;
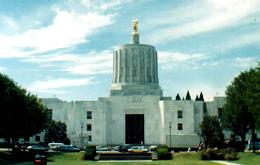 At its peak four years ago, SUMCO's Oregon operation employed almost 1,400 people in Salem, home of the state capitol (pictured). |
|
a $400,000 worker-training grant, and.
a $500,000 business-development grant.
Incentives' Influence Likely Not as
Great as SUMCO's Business Rationale
The Buckeye State's ample enticements, in fact, may make the SUMCO deal seem purely incentives-driven. But internal economic considerations look like they actually played a far more dominant role in the relocation decision.
SUMCO's niche, silicon manufacturing, has been the weakest-performing segment of a computer-chip industry that's struggled mightily since the onset of a downturn in 1997. Excess production capacity has triggered cutthroat price wars.
Simultaneously, silicon manufacturers are scrambling - very expensively - to adapt to chip-makers' pronounced swing toward using larger, more cost-effective 300-millimeter wafers. That shift has necessitated numerous costly retrofits of silicon manufacturing plants.
The depth of the 300-millimeter sea change is evident in the 2004 forecast for silicon-wafer shipments by SEMI Silicon Manufacturers Group, a San Jose, Calif.-based global association of 2,500-plus industry firms. SEMI is predicting an industry-wide increase of 15 percent in this year's shipments. But 300-millimeter shipments clearly dominate that projected 2004 growth, with SEMI predicting an 84-percent increase.
Those pressures are what drove SUMCO's November 2003 decision to shut down all of its once-massive Oregon operation.
"By consolidating our Salem production into other SUMCO facilities worldwide, we can achieve economies of scale and reduce our overall costs," Senior Vice President of Sales and Marketing Nick Stroud explained in announcing the shutdown.
Those cost considerations, in fact, were so strong that SUMCO officials told Oregon's Economic and Community Development Department that an incentives counteroffer wouldn't matter. "They told us that they didn't think that any sort of offer would really make any difference," said spokesman Scott Ballo.
SUMCO Must Now Sell $242.7 Million
Worth of Land, Buildings and Equipment
The dominance of the relocation's economics is further underscored by the massive disposal that SUMCO faces in the decision's wake. Its two Salem campuses, which housed some 2,000 employees at the operation's peak in 2000, cover 90 acres (36 hectares). The total tax-assessed value of the land, buildings and equipment is $242.7 million.
That huge swath of real estate, however, isn't yet on the market. The Salem operation is in the process of a gradual shutdown, as equipment is relocated to other SUMCO plants. Only a skeleton crew will remain onboard when the full shutdown comes in about a year.
Company officials say they'll first try to market the operation to other high-tech concerns.
They - as well as state and local officials - can only hope for as sanguine an outcome as the one that unfolded in Gresham, Ore., in late 2002. Microchip Technology took over a Gresham flash-memory plant that Fujitsu shut down in late 2001, laying off 670 employees. (For more details, the December 2002's Incentives Deal of the Month in the SiteNet/IAMC Dispatch online archives.) And Microchip Technology plans to hire as many as 688 employees at that facility.
"It's a miracle we were able to enter into a definitive agreement to sell the plant in such a short period of time during a slow economic climate," said Gresham Mayor Charles Becker.
In a somewhat ironic twist, incentives did play a major role in that deal, with Oregon providing a $17.3-million package.
As for the work that's being relocated from Salem, the Cincinnati plant isn't getting all of it. The Oregon production will be spread around to selected SUMCO plants in Indonesia, Japan and the United States, officials say.
Other locations for the relocated work, however, haven't yet been named. SUMCO also has U.S. plants in Albuquerque, N.M., and Phoenix.
pw0202bpw0202b
PLEASE VISIT OUR SPONSOR CLICK ABOVE
©2004 Conway Data, Inc. All rights reserved. Data is from many sources and is not warranted to be accurate or current.
|