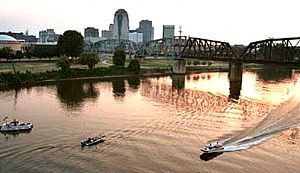 Greater Shreveport (pictured) has only 1,600 call center workers. Using the industry's general rule of thumb, it could support as many as 6,000 workers in the industry before becoming oversaturated. |
|
Answer Group's Louisiana Center Could Create 1,300 Jobs
by JACK LYNE, Site Selection Executive Editor of Interactive Publishing
BATON ROUGE, La. The Answer Group (TAG), a Florida-based outsourced customer support operation, has decided to open a large new call center in Shreveport, La., that's projected to employ as many as 1,300 workers.
A subsidiary of Reston, Va.-based Wirthlin Worldwide, the company made its announcement only some two months after first anonymously contacting the Greater Shreveport Chamber of Commerce. The project was unveiled in the state's capital city of Baton Rouge shortly after a $1.3-million grant request from the Louisiana Department of Economic Development was approved.
The project is the first for TAG outside of Florida. All of the company's 3,500 current employees - including a 3,000-worker call center - are clustered in Fort Lauderdale, Fla., the 10-year-old firm's headquarters city.
"With the conditions of our business today, it's necessary to have a lower-cost business model," TAG Executive Vice President Dennis Quinn explained.
Offshore outsourcing is one of the heaviest cost pressures on the call center industry. U.S. jobs in that sector "have been hammered by offshore competition," Quinn said.
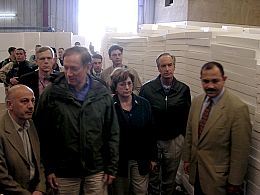 "We're defeating the outsourcing effect," Gov. Blanco said of the Answer Group project. (Pictured: Blanco, center, while touring a Styrofoam factory in Baghdad during a visit to Iraq by five U.S. governors.) |
|
TAG's focus on costs is part of the company's effort "to keep jobs in the U.S.," he added. "This is a business model that can exist here. Satisfaction levels with offshore services are low."
Site's Uses Have Ranged from
Retail to Religion to Call Center
The price of TAG's Shreveport facility was one of the cost factors that jibed with the company's business model, Quinn said.
TAG executive Frank Bellitto, however, was at first unsuccessful in finding suitable space. The options he reviewed during his initial site visit in January were either too pricey or not big enough to accommodate the operation that TAG had in mind, said Bellitto, who will head the new Shreveport operation.
Then Shreveport Chamber officials suggested another option during TAG's second visit. That possibility was a property in the southwest part of the city that was owned by Summer Grove Baptist Church. The site was once part of the South Park Mall, which closed last year.
The church then bought the property. It found, though, that it was rarely using part of the property, which included two side-by-side education buildings totaling 50,000 sq. ft. (4,500 sq. m.), plus some nearby offices.
TAG visited the church's site, and liked what it saw. It then met with Summer Grove officials and struck a deal. The church was willing to sell the property for $1.95 million.
Incentives Push Property Price Lower
TAG, however, wanted to push property costs even lower with its new model. It successfully asked for a $1.3-million grant from the Louisiana Economic Development Corp. (LEDC), a financing arm of the state's economic development department. The LEDC board at its monthly meeting approved the funds, drawn from the state's Economic Development Award Program.
"The help that Louisiana gave us today was also paramount in our decision," Quinn said. TAG, he explained, will create a subsidiary in Shreveport, U.S. Support Co. That moniker will be the name under which the Louisiana center will operate.
The state's grant will be used to offset part of TAG's expenses in purchasing the property. The company also plans to spend $900,000 in retrofitting the facilities, plus another $1 million for the operation's equipment. Quinn called to place TAG's Shreveport equipment order only 10 minutes after the LEDC approved the project grant.
"We are committed to working together," Gov. Kathleen Blanco (D) said in Baton Rouge. "We are looking forward to another success story for Louisiana.
"We're defeating the outsourcing effect," added Blanco, who personally called Quinn to make the state's case. "If they succeed, we succeed. If they don't succeed, we don't succeed."
Shreveport Market Still
Unsaturated with Call Centers
Shreveport's labor force was also a major factor auguring well for TAG's success, Quinn said.
"We need a talented labor force," he explained. "That's the key ingredient here. And we're convinced that just such a work force exists in Shreveport."
The Shreveport market appears to be nowhere near over-saturation for call center operations. The city currently has 10 call-center facilities that collectively employ 1,600 workers, according to the Shreveport Chamber.
The industry's general rule of thumb is that call centers can support up to 3 percent of a city's work force. Using that yardstick, Shreveport could support a call center industry with 6,000 workers.
TAG plans to hire 675 workers in the call center's first year of operations. Customer service representatives will make about $18,700 a year, said Quinn. The center's floor manager will make some $35,000 a year, while supervisors will make about $24,000. All new employees will receive full benefits after 90 days on the job.
The Shreveport center will handle inbound calls for about a dozen large firms, noted Quinn, including companies in the computer, retail and broadband-Internet sectors.
Quinn added that TAG "has no intentions" of cutting its call center work force in Florida.
 ConAgra is adding 440 jobs in Omaha (pictured), its headquarters city. |
|
ConAgra Adding 440 Omaha Jobs as Part of Reorganization
by JACK LYNE, Site Selection Executive Editor of Interactive Publishing
OMAHA, Neb. Nebraska-based ConAgra is doing a giant real estate shuffle as it remakes its organizational modus operandi. Now in the midst of a reorganization, the nation's second-largest food producer is expanding some plants, closing others and centralizing company-wide functions.
That effort remains very much a work in progress. But one of the clear reorganization winners thus far is Omaha, ConAgra's headquarters city. Some of the company's jobs began shifting to Omaha last summer, when the firm first announced its reorganization.
Now, ConAgra has quantified just how many positions it's moving to the city. As part of the release of its third-quarter 2003-04 results, the company said that a total of 440 jobs will be relocated to Omaha by the end of this year.
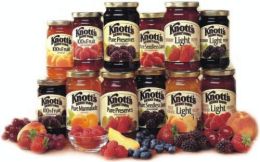 Knott's Berry Farm products (pictured) represent one of the 35 brands for ConAgra, where a wave of acquisitions rendered decentralization too unwieldy for cost-effective management. |
|
All of the jobs are in white-collar functions that do corporate-wide work. The relocated positions will be in customer service, food service, information technology, payroll, R&D and retail finance.
More ConAgra jobs could be Omaha-bound. The company describes the reorganization only as "ongoing."
Unwieldy Number of Subsidiaries
Triggered Shift Away from Decentralized Style
Focusing the formerly diffuse corporate functions in Omaha reflects ConAgra's reorganization - which the company calls its "operations initiatives."
By any name, the changes represent a major operational shift. ConAgra traditionally functioned as a decentralized holding company. Individual operating companies went about their business with significant independence. Some of ConAgra's individual brands even had their own dedicated production operations, public relations programs and marketing efforts.
A wave of acquisitions brought that decentralized management style into sharp question. The company has grown to 35 product brands. Only a few of them include Armour, Banquet, Blue Bonnet, Chef Boyardee, Cook's, Crunch 'n Munch, Egg Beaters, Fleischmann's, Golden Cuisine, Gulden's, Healthy Choice, Hebrew National, Hunt's, Knott's Berry Farm, La Choy, Libby's, Manwich, Marie Callender's, Orville Redenbacher's, Parkay, Peter Pan, Reddi-wip, Slim Jim, Swiss Miss, Van Camp's and Wesson.
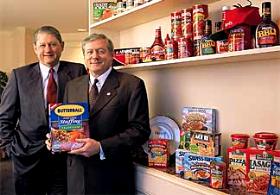 ConAgra's reorganization produced "a very solid quarter," said Chief Executive Bruce Rohde (right in photo above, standing beside Union Pacific Chairman and CEO Dick Davidson at ConAgra's Omaha headquarters). |
|
The list of subsidiaries simply became far too long to cost-effectively continue the decentralized setup, ConAgra Chief Executive Bruce Rohde explained in announcing the reorganization.
Four Plants Expanding, Three Closing
The resulting reorganization is also reverberating through ConAgra's manufacturing and distribution networks.
The company last year began assessing the efficiency of its production facilities. That evaluation has already resulted in one closing. A 400-employee cooked roast beef plant in Wells, Minn., shut down last month. And in January, ConAgra announced that a 100-worker hot-dog plant in Queenstown, Md., would close later this year. March saw another pending shutdown announced: a 170-employee meat-processing plant in Nevada, Ohio.
At the same time, the reorganization is expanding other ConAgra operations. The company announced that the closed plants' production will be moved to existing manufacturing operations in Lufkin, Texas; Mason City, Iowa; Peru, Ind.; and Quincy, Mich.
ConAgra says that it will add 225 workers at its Indiana food processing plant in Peru, some 70 miles (112 kilometers) north of Indianapolis. The company hasn't yet estimated how many jobs will be added at the three other plants that it's ticketed thus far for expansion.
More manufacturing facilities may later be tapped for closure or expansion, said Rohde. Operations that are older, lack market proximity or don't have sufficient space for expansion could be candidates for closure, he explained. Facilities with outdated equipment could also be targets, since ConAgra is retooling many of its food plants to produce more than one product, Rohde added.
From 1,800 Warehouses to 15
In addition, ConAgra is in the process of dramatically consolidating its distribution network. The company is replacing 1,800 small warehouses scattered around the U.S. with 15 large warehouse operations in 15 hub cities.
The reorganization clearly comes with substantial costs, not only in capital, but also in the human toll of lost jobs, relocations and unsettled employees.
The effort, though, may be paying off. The reorganization resulted in third-quarter spending of $24 million in closing facilities, preparing others for expansion and relocating employees. The company over the last year has also cut non-core business lines that were bringing in $15 million a quarter. But even with the reorganization costs and divestitures, ConAgra's third-quarter earnings of $203 million marked a 26-percent increase over last year. And those higher earnings came with third-quarter sales of $3.6 billion, which only equaled the previous year's third quarter.
"This was a very solid quarter," said Rohde. "We are particularly encouraged by sales and category share trends for several key brands and products. . . . We are continuing our focus on top-line growth, mix improvement and operations initiatives as part of our plan to improve profit margins and returns on capital."
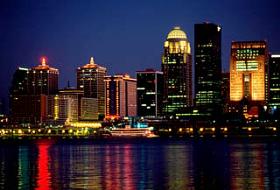 Ford's two plants in Louisville (pictured) already employ more than 9,000 workers. Photo: Louisville Leadership Foundation |
|
Ford's $73M Expansion of Louisville Plant Will Add 100-150 Jobs
by JACK LYNE, Site Selection Executive Editor of Interactive Publishing
LOUISVILLE, Ky. A $73-million vote of confidence, you could call it.
That's how much Ford Motor Company is going to spend in expanding its truck plant in Louisville, Ky. The 95,000-sq.-ft. (8,550-sq.-m.) expansion to the facility's stamping plant will add 100 to 150 jobs at the truck assembly operation.
Even more importantly for the Louisville plant, the investment represents a big shot of job security. Ford's announcement of the expansion comes as the automaker has been sharply scaling back operations in an effort to boost is sagging bottom line.
"This is another milestone in the longstanding partnership between the city and Ford Motor Company," metro Louisville Mayor Jerry Abramson (D) said at the expansion announcement. "It's a tremendous vote of confidence in our Louisville work force."
The big confidence booster is coming to a very large Ford presence. Known within Ford as the Kentucky Truck Plant (KTP), the 5,900-worker, 4.6-million-sq.-ft. (414,000-sq.-m.) Louisville operation is already considered North America's largest truck facility.
New Press Will Likely
Weigh Eight Million Pounds
Similarly jumbo-sized is the expansion's centerpiece: a second press.
The new press may weigh as much as 8 million pounds (3.6 million kilograms), said Ford officials. That's even larger than the 7.4-million-pound (3.33-million-kilogram) press that went online in 1998 when the $28-million Louisville stamping operation first opened in 214,000 sq. ft. (19,260 sq. m.) of space.
The additional press will increase the stamping operation's output to 100,000 parts per week, more than doubling current production. The enlarged output means that the Louisville plant will be able to stamp steel sheets to make almost all of the body sections that are used in the F-Series Super Duty trucks and Excursion SUVs that are assembled there.
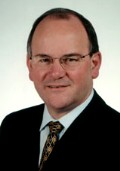 "There has been sustainable, continuous improvement here in quality and throughput," said plant manager John Crew (pictured), "which gives us the quality to make further significant investment." |
|
"We will now be stamping every major panel that we assemble, so we will have control of our own destiny," explained John Crew, general manager of the plant (who had just been tapped to become vice president of Ford's Australian operations).
UAW Cooperation Critical
Ease of expansion was an element that Ford built into its original stamping facility in Kentucky. The fact that the operation is now expanding is a testament to the Louisville plant's strong performance, Crew said.
"We're able to make this investment with confidence in a very difficult business climate," he noted. "There has been sustainable, continuous improvement here in quality and throughput, which gives us the quality to make further significant investment."
Ford has two other plants - located in Hermosillo, Mexico, and Wayne, Mich. - at which assembly and stamping operations are housed on the same site.
Labor cooperation was also a major factor in Ford's decision to expand its Louisville stamping operation. When the completed expansion goes online in 2006, Ford will run both presses 24 hours a day, seven days a week.
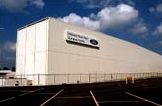 The expansion will add 95,000 sq. ft. (8,550 sq. m.) of space to Ford plant's existing 214,000-sq.-ft. (19,260-sq.-m.) stamping facility (pictured), doubling the operation's output. Photo: Whittenberg Construction Company |
|
To accommodate that schedule, United Auto Workers Local 862 agreed that stamping plant employees will work 12-hour days for three to four days a week. In return, workers get time-and-a-half wages for all work exceeding eight hours a day.
Hourly workers at the Ford plant average $25.40 an hour, according to company officials. "This agreement is a win-win situation," said Mike Stewart, UAW 862 building chairman of the Ford truck plant.
"This arrangement," said Crew, "speaks to the kind of innovative flexibility that exists at KTP between the union and management, which has allowed us to secure this investment."
Ford Will Fill New
Jobs from Within
The addition of the new press will enable the Louisville stamping operation to begin making fenders, floor pans, hoods, roof panels, tailgates and truck beds. The plant's current press stamps out truck doors and roofs. The operation's increased output will allow the Kentucky plant to supply parts to other Ford plants.
For the Louisville plant, the stamping expansion also means a huge reduction in waste, explained Crew.
"We take out the waste of freight costs," he said. "We take out the waste of excess inventory, the waste of excess railcars, the waste of investing in more racks, the waste of planning to have our presses idle. . . . I could go on and on and on."
The new jobs created by the expansion, however, won't be filled through applications, Ford officials said. Instead, the automaker will fill the positions from within, primarily hiring workers who have been laid off at other Ford plants.
Ford also has another major plant in Louisville: a 4,000-employee assembly operation that makes the Ford Explorer and Sport Trac, as well as the Mercury Mountaineer. That plant opened in 1956. KTP was built in the next decade, going online in 1969. The Louisville stamping operation already makes some of the body sections for the Explorers that are assembled at Ford's other plant in Kentucky's largest city.
"We appreciate Ford as an example of a company that's committed to its hometown with a tradition of creative collaboration, working with management and labor, to bring about the best product," said Abramson.
Editor's Note: For more on the recent Ford and CitiGroup projects in Louisville, as well as other automotive projects in Kentucky, read the Kentucky Spotlight in the May 2004 issue of Site Selection. The article will include our exclusive interviews with Louisville Mayor Jerry Abramson and Kentucky Gov. Ernie Fletcher.
pw0322bpw0322b
PLEASE VISIT OUR SPONSOR CLICK ABOVE
©2004 Conway Data, Inc. All rights reserved. Data is from many sources and is not warranted to be accurate or current.
|