Competition offers challenges.
by John W. McCurry
n the European biotech world, things are often greener across the pond in the U.S.
That's the case of U.K. firm
BioVex, a developer of vaccines for the treatment and prevention of cancer and chronic infectious disease, which has moved its headquarters from Oxford, U.K., to Cambridge, Mass.
"There were three reasons to move to the U.S.," says Philip Astley-Sparke, BioVex's president and CFO. "The U.S. is the largest healthcare market in the world and every biotech company seeks to locate here. Most of our potential corporate partners are U.S. companies and having your partners on your doorstep is beneficial. And the whole capital market structure here is more sophisticated."
Astley-Sparke says the company wanted an East Coast location to stay within five hours of the U.K. While Maryland was given a look-see, he says Massachusetts quickly became the front-runner location.
"Cambridge has the densest cluster of biotech companies in the world," Astley-Sparke says. "It's all here. We didn't spend an awful lot of time looking."
BioVex will be looking for a manufacturing site in the coming months and Astley-Sparke says he's looking at a site in Cambridge and at another in the Boston area. BioVex was recently named as one of the top emerging biotech companies for 2005 by respected industry newsletter FierceBiotech.
Life science companies are increasingly moving R&D to the Cambridge area to be close to related academia and the area's immense talent pool. This trend recently helped pull in
CSSC Inc., a regulatory compliance and consulting firm that opened an office in Cambridge to be close to clients.
Another European firm is establishing a Cambridge beachhead. Organon International, the human pharmaceutical business unit of Netherlands-based
Akzo Nobel, recently opened its first U.S. research facility in the Boston suburb. Organon makes products for the mental health, contraception, fertility, pain, anesthesia and urology markets. Organon says Cambridge was chosen for its concentration of medical research institutes, universities and hospitals.
Bio Market Robust,
But Faces Challenges
Brendan Carroll, director of research for commercial real estate firm Richard Barry Joyce & Partners, says the greater Boston bio market continues to grow, but faces various challenges. These include increased efforts by other states to attract biotech companies.
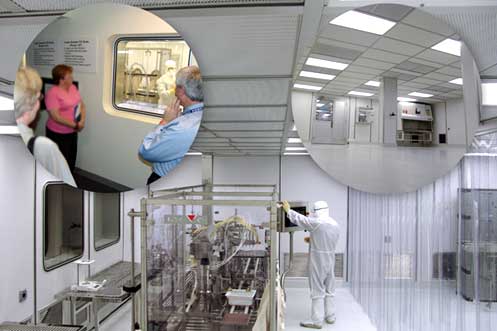 |
Hyaluron opened a facility in Burlington in 2004 and is now seeking a site for a larger commercial manufacturing operation. |
"The greater Boston area is the epicenter of biotech," Carroll says. "Cambridge, a city of just over 100,000, has 38 percent of its residents with post-graduate degrees. It has an extremely highly skilled labor force and now a biotech industry that is equal to that of Cambridge has spilled out to different types of environments."
Carroll says there is about 700,000 sq. ft. (65,000 sq. m.) of lab-oriented construction under way in greater Boston, but about 85 percent is pre-leased. He says a lot of the Harvard and MIT graduates of the late 1980s started companies in the late 1990s. As they have moved their businesses to the suburbs, that has helped develop a suburban cluster of about 3.2 million sq. ft. (297,280 sq. m.) of life sciences real estate.
"A lot of those people are now 35 to 40 and, [instead of] living in the city with night life, they have moved to a suburban setting. So, we're seeing the emergence of an extremely attractive life science cluster in the suburbs."
Bio Spreading Beyond Boston
But not all of the Massachusetts life sciences development is in the greater Boston area. The Worcester Business Development Corp. and Worcester Polytechnic Institute (WPI) broke ground in June on a project that will turn a former industrial brownfield into an 11-acre (4.5-hectare) mixed-use life sciences park. The WPI Life Sciences & Bioengineering Center at Gateway Park.
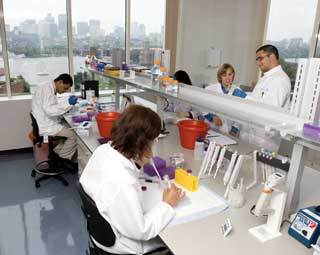 |
Organon, which opened its U.S. research center in June, is one of a growing number of biotech firms siting R&D facilities in Cambridge. |
The four-story facility, a $35-million investment, will be 124,600 sq. ft. (11,600 sq. m.) of lab and office space. The facility is slated for completion in early 2007.
WPI will be the anchor tenant and the center will serve as the focal point for the university's graduate research in the life sciences and related engineering fields.
Straumann, a Swiss specialist in implant dentistry and dental tissue regeneration, opened its 161,000-sq.-ft. (15,000-sq.-m.) North American headquarters in Andover in June. The facility includes a 35,000-sq.-ft. (3,250-sq.-m.) training center. Andover houses Straumann's first manufacturing unit outside Switzerland. The company plans to double its North American work force within five years to 500, with 300 based in Andover.
Can the Bay State
Keep Its Homegrown Bio Firms?
Hyaluron, a new biopharma contract manufacturer, opened its first manufacturing facility in Burlington early in 2004. But the company, which has its sights on a larger commercial manufacturing plant, is casting a wide net in its search for the right site for its next facility. Early in its site selection process, Hyaluron is considering its home state, but it's also scrutinizing a growing list of contenders that include Connecticut, New York, Rhode Island and Québec, where Hyaluron will be meeting with industry recruiters in September.
"Looking at it from an economic perspective, it will depend on what types of incentives are offered and the availability of trained personnel," says Rebecca Butler, Hyaluron's manager of corporate and legal affairs. "There's no essential need to stay in the Northeast. Of course, we would love to stay in Massachusetts, but with real estate prices the way they are, we will have to weigh the costs vis-a-vis incentives the state may offer."
Hyaluron began in 1999 as a manufacturer of hyaluronic acid, a product extracted from rooster combs and used in eye surgery and treatments for joint pain and infertility. The company evolved as it developed a better way to put viscous products into syringes. Today, the company continues hyaluronic acid manufacturing, but its growth has come as a filler of syringes and vials.
The proposed facility will be in the 60,000-100,000-sq.-ft. (5,600-9,300-sq.-m.) range, employing 100 initially and 200 eventually. Butler says in addition to incentives, an educated work force is critical to Hyaluron's site decision.
"We need to be in an area where can get the kind of educated population to work in our factory," Butler says. "They should have at least some college and a science background. Even in Boston, one of our most difficult things has been to hire personnel that can handle the work. We want to be in a place where real estate values are good and employees have access to homes they can afford."
Butler says Hyaluron hopes to have the site chosen by the end of 2006 and have the facility built by the end of 2007.
"We're very eager to choose the right site, but it's difficult to sort it all out," she says. "There are a lot of incentive programs out there and I have an obligation to look into as many as I can and find the best for Hyaluron. The state definitely wants to keep us and we would love to stay as well. The question is whether they can offer incentives the same as other locations. That's a question that's yet to be answered."