Facility reuse, flexible production, consolidation and creative financing solutions characterized the Top Deals of 2010, chosen by Site Selection editors based on scale of capital investment and job creation, creativity in negotiations and incentives, regional economic impact, competition for the project and speed to market.
In addition to widely recognized trends toward renewable energy and sustainability-minded products, the deals feature a strong showing from straightforward manufacturing, often using older space to serve the needs of new waves of industry.
TOP DEALS IN NORTH AMERICA
________________________
Abound Solar
Tipton, Ind.
$500 million, 850 jobs
orn on the Fourth of July, this project was announced by the President of the United States, who also announced a $400-million loan guarantee from the U.S. Dept. of Energy. The funds allow Colorado-based Abound, which is also expanding its operations in Longmont, Colo., to purchase the never-used manufacturing complex belonging to Getrag Transmission, which sat vacant after the company declared bankruptcy in 2008 following a lawsuit by partner Chrysler over financing for the plant. Now Abound will make solar modules at the plant, just north of the Indianapolis metro area.
Abound officials started talking to Indiana Economic Development Corp. and Secretary of State officials some 18 months before the announcement, later bringing Tipton County commissioners into the conversation. Indiana Secretary of Commerce Mitch Roob told the Kokomo Tribune that much of the money involved in the purchase would go to contractors left holding the bag when Getrag went bankrupt. IEDC incentives include up to $11.85 million in performance-based tax credits and $250,000 in training grants. Tipton County offered tax abatement as well as tax increment financing funds totaling $13 million to the land trust of contractors that the bankruptcy court had put in charge of selling the building by September. Other parties helping the deal come to fruition included Cassidy Turley, Franklin Advisors LLC, Benesh Freidlander Coplan & Aronoff LLP, Barnes & Thornburg, Ice Miller LLP, and WW Reynolds Companies.
________________________
Cerner Corp./OnGoal
Kansas City, Kan.
$414 million, 4,000 jobs
he “other” Kansas City, which found out just last month that it had beat out 1,100 others to become the first recipient of Google’s ultra-fast broadband program, continues to make a bid to become “the” Kansas City when it comes to economic development. This deal with healthcare information management systems company Cerner, Major League Soccer’s Kansas City Wizards ownership group OnGoal and developer Lane4 will create thousands of jobs (at an average salary of $54,000) by 2016, a new stadium for the Wizards and an athletics complex with up to two dozen new fields. In January 2010 the Unified Government Wyandotte County/Kansas City, Kan., approved the deal, 10 months after the idea was first broached. Revenues attached to successful retail growth in KCK helped make the deal, in the process pulling it from its original destination at a former mall site in Missouri, even as Kansas Secretary of Commerce David Kerr jumped ship to Missouri while negotiations were still unfolding in late 2009.
“We were trying to get the deal done but at appropriate costs,” Kansas Deputy Secretary of Commerce Steve Kelly told us. “It’s like walking a gauntlet, with people clubbing you from both sides … It’s a tribute to the parties involved that people were able to stick to it and keep moving the ball.”
________________________
Electrolux
Memphis, Tenn.
$190 million, 1,200 jobs
hen Electrolux announced the location of its new North American Cooking Products manufacturing center in December, Kevin Scott, president of Electrolux Major Appliances North America, cited the area’s lower cost structure; skilled labor pool; central location and logistics capabilities; and connectivity to other Electrolux operations, including a cooking operation in Springfield, Tenn., that employs 2,900. “Over the years, the state of Tennessee has been very supportive of our growth and investment in the Springfield facility, and has worked with Electrolux to create jobs for the community,” said Scott. “In many ways, today’s event is a Tennessee homecoming as much as an announcement of a new plant in this great state.” The site in Frank C. Pidgeon Industrial Park was chosen over other sites in the U.S. and Mexico, and will be replacing a site in L’Assomption, Que., Canada, that is scheduled to close. Incentives included a payment-in-lieu-of-tax agreement. Electrolux plans to begin transitioning production to the new 700,000-sq.-ft. (65,030-sq.-m.) facility in mid-2012, and the process is expected to be completed by the fourth quarter of 2013.
________________________
First Quality Tissue
Anderson, S.C.
$1 billion, 1,000 jobs
he Pennsylvania company will build a new tissue and towel plant at a former Shaw Industries property in Anderson that once was also home to operations from BASF and Honeywell. The new jobs will pay between $15 and $17 per hour, equating to annual gross income of $33,280 in an area that saw unemployment rise as high as 14 percent as 5,000 textile jobs vanished since 2007. “Among the factors that attracted First Quality to Anderson are the pool of skilled labor, positive work ethic and the availability of the infrastructure necessary to sustain our facility,” said the company. Other factors cited by the state included proximity to markets in the Southeast, and low energy cost. As legacy contamination and cleanup issues were being confronted with various companies, Burriss Nelson, interim director of Anderson County Economic Development, gave great credit as well to the South Carolina Dept. of Health and Environmental Control. He also said rail, sewer and a large water demand were among the check marks on First Quality’s site selection matrix. “This is a company that talks about a 100-year business plan,” he told us. “It’s kind of refreshing.”
________________________
Ford Motor Co.
Louisville, Ky.
$600 million, 1,800 jobs
ord’s roll of success in 2010 included this December announcement, as it moves Explorer SUV assembly from Louisville to Chicago and revamps its Louisville Assembly Plant (one of two plants in the city) to make the next model of its Escape small SUV. Crucial to the decision was the passage by the Kentucky General Assembly of the Kentucky Jobs Retention Act, which allows the use of payroll taxes on existing employees as well as new employees. The act could allow Ford to recover up to $240 million through income tax credits and wage assessments. The plant had about 1,100 employees at the time of the announcement, but will have 2,900 when the new production ramps up later this year.
________________________
Intel
Hillsboro, Ore.
$4 billion, hundreds of jobs
ven as the company’s leaders talk tough about conditions for investing in the U.S., they put some skin in the game, including CEO Paul Otellini’s recent naming to the President’s Council on Jobs and Competitiveness. As Intel spokesman Howard High put it in describing how much investment may eventually go overseas, “We go where the smart people are.” So they must be awfully smart in Oregon, where Intel will construct its new D1X R&D facility as well as upgrade two other fabs in nearby Portland. “These are very high paying jobs, on average over $100,000 in salary and benefits,” Bob Whelan, director of consultancy ECONorthwest, told us. “For every job Intel creates, another 4.8 jobs are created in the region.” Intel has invested about $18 billion in its Portland operations since 1974. With 15,000 staffers, it is Oregon’s largest private employer.
________________________
Navistar
Joliet, Lisle and Melrose Park, Ill.
$205 million, 2,100 jobs retained or created
sequence of maneuvers, legislation and negotiations ended happily for Illinois and Navistar by year’s end, as the longtime Metro Chicago-based truck manufacturer committed to a new corporate headquarters in Lisle, an engine research and testing center in Melrose Park and a parts distribution center in Joliet. As we reported in our March 2011 issue, the HQ project originally was on the books as early at 2009, but the company had postponed the move in May 2010 and threatened to leave the state altogether after neighbors had opposed the presence of the engine testing facility in the HQ complex. Navistar considered relocating to South Carolina, Alabama or Texas. But a compromise was brokered by state and local leaders. Navistar plans to invest $110 million in the HQ, located at a former Alcatel-Lucent campus.
Illinois offered $65 million in incentives for that project. Recovery zone facility revenue bonds worth $90 million were approved for issuance by the Cook County Board of Commissioners to support the Melrose Park investment, and $135 million of recovery zone facility revenue bonds issued by the Illinois Finance Authority will help finance the Lisle and Joliet projects. Daniel C. Ustian, Navistar chairman, president and CEO, credited Illinois Gov. Pat Quinn and Attorney General Lisa Madigan with clearing a path for the company to retain or create nearly 3,000 permanent jobs between the Lisle and Melrose Park campuses over the next several years. Quinn was behind a law signed in June 2010 that expanded the Economic Development for a Growing Economy (EDGE) tax credit, specifically aimed at Navistar.
________________________
Nucor
St. James Parish, La.
$3.4 billion, 1,250 jobs
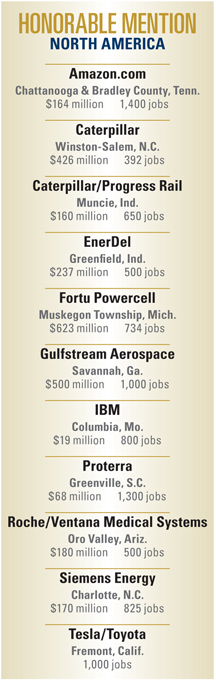
ucor will bring to the Bayou one of the largest industrial projects in Louisiana’s history, a five-phase iron and steel making complex with a payroll of up to roughly $100 million. Among the attractants, said the state, were the elimination of state sales taxes on natural gas and business utilities, and on manufacturing machinery and equipment. Other parties involved in the negotiations included St. James Parish, Entergy and the Port of South Louisiana. Louisiana beat out sites in Brazil, Canada and other Southern states for the project.
Prior to Nucor finalizing its location decision, Louisiana dedicated $65.2 million of the capital outlay budget (in non-cash line of credit) to the “Mega Project Site Preparation, Planning, and Construction” project, created specifically for Nucor, should it select Louisiana as the site of its future operations. Upon Nucor announcing its decision to locate in Louisiana, Louisiana Economic Development requested the Bond Commission prioritize the Nucor project and make $30 million of the total capital outlay allocation available to the company immediately. Funding for future phases of the project will likely utilize the Louisiana Mega-Project Development Fund, created in 2007.
Incentives include performance-based grants and loans for land, infrastructure and equipment that total approximately $160 million over six years. An extended local property tax exemption of approximately 20 years will be made available to the company through local government; however, Nucor will make an annual payment in lieu of taxes to support the local school system, parish government, and sheriff. These payments will begin at $850,000 per year and eventually will increase to $4.5 million per year. Under the Louisiana Quality Jobs incentive, Nucor will receive cash rebates for each new hire, resulting in $35 million to $40 million over 10 years. They will also be able to take advantage of rebates on sales tax relating to construction costs, resulting in $40 million to $55 million in the five-year period beginning in 2013. Additionally, the company secured a $600-million tax-exempt Gulf Opportunity Zone Bond allocation from the State Bond Commission with the support of LED. After receiving a key air quality permit, Nucor broke ground early this year.
________________________
Samsung
Austin, Texas
$3.6 billion, 500 jobs
his investment, announced last June, will bring the company’s overall investment in Samsung Austin Semiconductor to more than $9 billion since its establishment in 1996. The decision to bring the additional capacity to Austin was based on the company’s long-term business requirements. The expanded fabrication plant, one of the largest in the United States, will produce advanced logic devices for Samsung’s System LSI business. The investment in the Austin campus will build out the second phase of the company’s 2.3-million-sq.-ft. (213,670-sq.-m.) semiconductor complex. The first half of the building was started in 2006 and began production a year later. The 12-inch facility was built in 2007.
The new facility is expected to be completed by the end of 2011. “This investment, along with the creation of Samsung Austin Semiconductor’s first research and development entity this spring, makes the Austin campus a true semiconductor complex and ensures Austin’s premier status as a center for semiconductor research and manufacturing,” said Dr. W. S. Han, president of Samsung Austin Semiconductor. The annual payroll in Austin will grow from its current $70 million to about $105 million. The utility bill will grow too: Already Austin Energy’s largest customer, with an annual electrical utility bill of about $32.9 million, Samsung’s electricity bill will increase by more than $45 million per year. Water and waste water purchases from the city will grow to almost $13 million per year.
________________________
Samsung/KEPCO
Ontario, Canada
$7 billion
ntario passed the Green Energy Act and its associated feed-in tariff in May 2009, and plans to shut down all of its coal-fired power plants by 2014. Those conditions laid the groundwork for the provincial government’s January 2010 signing of a green energy investment agreement with a consortium created by Samsung C&T Corporation – Trading and Investment Group and the Korea Electric Power Corporation (KEPCO).
Samsung C&T and KEPCO will establish and operate a series of wind and solar power clusters over the next 20 years. The clusters will include wind turbines that will generate up to 2,000 MW as well as solar power facilities that will generate up to 500 MW. The entire project will have a combined power-generating capacity of 2.5 GW by 2016, producing energy equivalent to four per cent of Ontario’s total electricity consumption. The first stage of the project is scheduled to be completed by the first quarter of 2013 and will include a 500-MW cluster (400 MW wind and 100 MW solar) that will be built in the Chatham-Kent and Haldimand County regions of Southern Ontario.
Samsung C&T and KEPCO will support the development of local infrastructure for the renewable energy industry by constructing production facilities to provide key components, such as blades, wind towers, solar modules and inverters. Samsung C&T will also encourage component suppliers to build manufacturing facilities in the area. In total, the project is expected to generate more than 16,000 green energy jobs within the province.
Among the early follow-on projects is a wind turbine blade plant in Tillsonburg from Siemens, and a solar module plant in Guelph from Canadian Solar, the company’s first plant not in China.
INTERNATIONAL TOP DEALS
________________________
Bayer MaterialScience
Shanghai and other cities, China
$1.3 billion
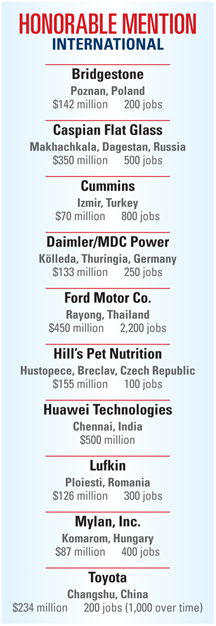
ayer announced in December a family of investment projects in China as it anticipates Bayer Group sales increasing from €2.1 billion in 2009 to around €5 billion by 2015, with Bayer MaterialScience expected to account for at least half of that total. Investments of around €1 billion are planned at the Shanghai site, via five separate projects. Capacities for the polyurethane raw material MDI are to be more than doubled to one million metric tons a year and for high-performance polycarbonate to 500,000 t/y. R&D operations will increase, and the headquarters of the Polycarbonates Business Unit will be relocated from the main Leverkusen site in Germany to Shanghai.
“The expansion of our capacities in China is an important step in strengthening our presence in the emerging economies,” explained Bayer AG’s Management Board Chairman, Dr. Marijn Dekkers. Bayer MaterialScience already was investing €2.1 billion in Shanghai as part of a long-term project lasting until 2012. Another part of the plan involves a €110-million investment in five customer support facilities in Shanghai and three other Chinese cities.
________________________
Case New Holland/Fiat Group
Sorocaba, Brazil
$563 million, 800 jobs
pened in March 2010, the company’s new complex is expected to generate 3,000 direct jobs, and up to 6,000 including indirect jobs in the region in two years, when the factory reaches full production capacity. The project — the biggest, single machine industry investment in the history of the country —required an investment of $1 billion and is part of the Fiat Group investment plan for the years 2007-2011 announced in November 2006. The Sorocaba factory will produce equipment to supply the domestic market, as well as exporting to other Latin American countries and more than 50 countries around the world. The site also includes the largest CNH Parts Distribution Center in Latin America. The structure was designed to achieve the greatest operational speed through the whole logistics chain, from the supplier to the end customer, at over 500 points in Latin America.
________________________
Guangqi Honda Automobile Co., Ltd.
ZangCheng, China
$869 million, 1,200 jobs
he car industry explosion in China continues apace, as the passenger vehicle segment alone saw a 53-percent increase in production capacity in 2010. Guangqi Honda Automobile Co., Ltd., in May announced its plans to expand its annual capacity from the current 360,000 units to 480,000 units in order to meet continuously growing demand in the Chinese market. The company said it would double the annual capacity of its plant in ZengCheng to 240,000 units by the latter-half of 2011, thereby matching the output it already had achieved at its plant in HuangPu. Guangqi Honda began production in March 1999 with Accord, and by this year will have added six more brands to its mix, including the new LI NIAN brand vehicle.
________________________
Hyundai Heavy Industries
Chungcheongbuk-do, South Korea
1,000 jobs
hrough an agreement with French firm Saint-Gobain and the province of Chungcheongbuk-do, Hyundai Heavy Industries is constructing Korea’s biggest CIGS (copper, indium, gallium, selenide) thin-film solar cell plant, with 100 MW of capacity, in the Ochang Foreign Investment Zone. Depending on business conditions, there is potential to quadruple that capacity by 2015. “The new plant makes Hyundai Heavy the sole Korean company producing both thin-film and crystalline solar cells,” said Kim Jung-rae, a senior executive vice president of Hyundai Heavy. “Upon completion of the plant, we can achieve our target of being a Global Top Five CIGS solar cell manufacturer by 2015.”
With more than three dozen solar cell and module companies doing business in the province, Chungcheongbuk-do continues to grow, pushing in September for the designation of its Jeungpyeong area as a solar energy special zone.
________________________
Intel
Kiryat Gat, Israel
$2.7 billion, 1,000 jobs
xpected to be carried out over eight years, this expansion at one of Intel’s landmark sites should bring Intel’s overall employment there to about 3,100 by 2018. Intel is also adding 50 jobs at an R&D center in Jerusalem, and just achieved LEED certification at its design center in Haifa. After starting with five workers in the nation in 1974, Intel now employs 6,600 people in seven Israeli communities. A $187-million grant is expected from the Israeli government for the Kiryat Gat project. Located near Ben-Gurion University, Kiryat Gat, the capital of the Lakhish region, now has a population of approximately 48,000. Its industries also include textiles, cotton and sugar processing.
________________________
Novartis
St. Petersburg, Russia
$140 million, 350 jobs
n December Novartis announced the signing of an MOU with the City of St. Petersburg, confirming its intent to build a new full-scale pharmaceutical manufacturing plant in St. Petersburg; Russia. This investment is part of an overall $500-million commitment in local infrastructure and collaborative healthcare initiatives planned over a five-year period. This comprehensive partnership addresses three core areas that include local manufacturing, research and development (R&D) partnerships and public health development.
“Novartis is making a strategic investment in Russia for long term growth. This collaboration shows our commitment to contributing to the ambitious healthcare goals of the Russian government,” said Joseph Jimenez, CEO, Novartis AG.
Construction is scheduled to start in 2011 and the plant is expected to produce approximately 1.5 billion units per year. The scope of the company’s public health collaborations may include out-licensing of Novartis compounds to Russian companies with proven scientific capabilities, in-licensing and scouting for promising drug candidates from Russian scientists and universities and modeling and simulation activities for clinical trials.
________________________
Portucel Soporcel
Zambezia, Mozambique
$3.1 billion
7,500 direct and indirect jobs
ortugal’s Portucel/Soporcel group plans to invest €2.3 billion in Mozambique by 2025 in a pulp and paper factory and tree growing complex. In December 2009 the nation’s government granted Portucel/Soporcel the right to use 427,477 acres (173,000 hectares) of land in Zambezia, with 543,613 acres (220,000 hectares) still potentially available pending government approval. The company plans to produce 30 million eucalyptus trees per year.
Mozambique, a southeast African nation of 22 million people, was formerly a Portuguese colony. Part of the investment in the huge undertaking will come from Portugal’s largest construction company, Mota-Engil SGPS SA. According to Bloomberg, Mota will build a bridge that can support cargo demands over the Zambezi River, linking the country’s port city of Beira to landlocked nations like Democratic Republic of Congo, Malawi, Tanzania and Zambia.
A separate new joint investment bank established by the two nations is backing various rail, road and power projects to support continuing industrial investment, including by coal and iron ore mining companies.
________________________
POSCO/PT Krakatau Steel
Cilegon, Indonesia
$6 billion
n late October 2010, after the signing of a JV agreement in August following months of negotiations, PT Krakatau Posco, a joint venture between Korean steel giant Pohang Iron and Steel Corporation (POSCO) and Indonesia’s PT Krakatau Steel, broke ground on a new integrated steel plant in Cilegon, Banten province, 62 miles (100 km.) west of Jakarta. POSCO will invest $2.7 billion in infrastructure, including leases of harbors and land, as it saves money over the greenfield approach by working with its partner’s infrastructure network. The project, located near Krakatau Steel’s existing plant, is backed by tax breaks and special economic zone status conferred by the Indonesian government, and is located on a 98-acre (40-hectare) site. The project is driven in large part by demand from the shipbuilding and automotive sectors in the Asia Pacific. As reported in The Jakarta Post, POSCO’s investment in the Cilegon plant is part of the company’s planned $30 billion in overseas investment in India, Vietnam and Indonesia. It’s also one of several megaprojects in Indonesia under consideration by a handful of Korean conglomerates, including a possible electronics complex from LG Corp.
________________________
SunPower Corp./AU Optronics Corp.
Malacca, Malaysia
$1.2 billion, 7,000 jobs
ilicon Valley-based SunPower Corp. announced in late May its agreement to form a JV with Taiwan-based AU Optronics Corp. that will own and operate SunPower’s 1.4-gigawatt third solar cell fabrication facility. The company’s existing two fabs are located in the Philippines. “We expect this JV will reduce our effective Fab 3 capital expense per watt by more than 35 percent while capitalizing on AUO’s world-class manufacturing expertise to reduce solar cell manufacturing costs,” said Tom Werner, SunPower’s CEO. SunPower hopes to reduce cost per watt to US$0.55 by 2014. Helping the project happen is a $288-million loan from the Malaysian government. Expected to be complete in early 2011, this huge solar PV plant in Rembia, Alor Gajah, will produce more than 1,000 MW a year of solar panel components. With the help of primary contractor Hexagon and IEN Consultants, it is targeted to achieve the first LEED Platinum certification in Malaysia.
________________________
Taiwan Semiconductor Manufacturing Co.
Taichung, Taiwan
$9.3 billion, 8,000 jobs
SMC broke ground in July 2010 in Taichung’s Central Taiwan Science Park for Fab 15, TSMC’s third 12-inch (300mm) “Gigafab.” “Science Parks have played a critical role in the development of Taiwan’s high-tech industry,” said TSMC Chairman and CEO Dr. Morris Chang, noting the company’s flourishing presence in Taiwan’s Hsinchu and Tainan science parks over the past 20 years. “They have also provided important support to TSMC as we grew to become a leading global semiconductor company with its roots in Taiwan.” The company plans to hire 4,000 engineers. Chang said 8,000 high-quality jobs would be created as the new fab’s capacity grows. The Gigafabs have capacity of more than 100,000 12-inch wafers per month. The new facility, covering 46 acres (18.4 hectares), will include 14 soccer fields worth of clean room space. TSMC is scheduled to begin equipment move-in for the Phase 1 facility in June 2011.
In a separate development, TSMC is investing $258 million and hiring 2,000 at a new solar module manufacturing complex in Taichung.