At the same time migrants are reported to be crossing the U.S.-Mexico border en masse in order to avoid apprehension by U.S. Border Patrol personnel, companies continue to vote with their feet with new projects along both sides of the border corridor.
In the region that includes Brownsville, Texas, and Matamoros, Tamaulipas, Mexico, for example, Michigan-based Fisher Dynamics, a maker of seating systems for OEMs, operates a location in Brownsville while also operating a facility in Matamoros over the past 25 years that employs around 1,450 people. In spring 2023 the company announced it would construct a second plant with an investment of approximately $77 million in Matamoros that could create as many as 1,400 more jobs at the Las Ventanas industrial park.
In the Borderplex region encompassing El Paso, Texas; Las Cruces, New Mexico; and Ciudad Juarez, Chihuahua, Mexico, Ohio-based power management company Eaton in September announced an investment of $80 million to expand its manufacturing footprint in El Paso. The company aims to create more than 600 new skilled manufacturing jobs, it said in a release.
The project is part of an overall investment of $150 million to increase the supply of electrical power distribution solutions across North America, including at existing facilities in Beaver, Pennsylvania; Arecibo, Puerto Rico; Haina, Dominican Republic; and Juarez, Mexico — El Paso’s sister city across the border.
“Eaton solutions are at the heart of electrical systems everywhere and are vital to accelerate complex infrastructure projects for buildings, healthcare facilities, data centers, industrial facilities and utilities,” said Mike Yelton, president, Americas Region, Electrical Sector at Eaton. The news came only one month after Eaton had announced it would invest $500 million in multiple North American manufacturing and operations locations.
Taiwan-based Tesla supplier Hota Industrial Manufacturing in September announced a new $99 million, 350-employee plant in Santa Teresa, New Mexico, part of the Borderplex region. The announcement was made in Taipei City, Taiwan, where New Mexico Gov. Lujan Grisham was participating in U.S. Business Day as she led a trade mission. “Hota has picked Santa Teresa as its next manufacturing site based on various comparison analyses among the states on the U.S.-Mexico border,” said Hota Chairman David Shen. “Its location makes it a one-day trucking distance to many of our main customers. Transportation infrastructure is in place to support the logistics of our goods and services. Utility supply is stable and relatively inexpensive. Labor costs are currently the lowest among its neighboring states. Another important thing is that New Mexico has no major natural disasters. Most importantly, the fast responsiveness and support from the state officials have enhanced our decision and confidence to go to New Mexico.”
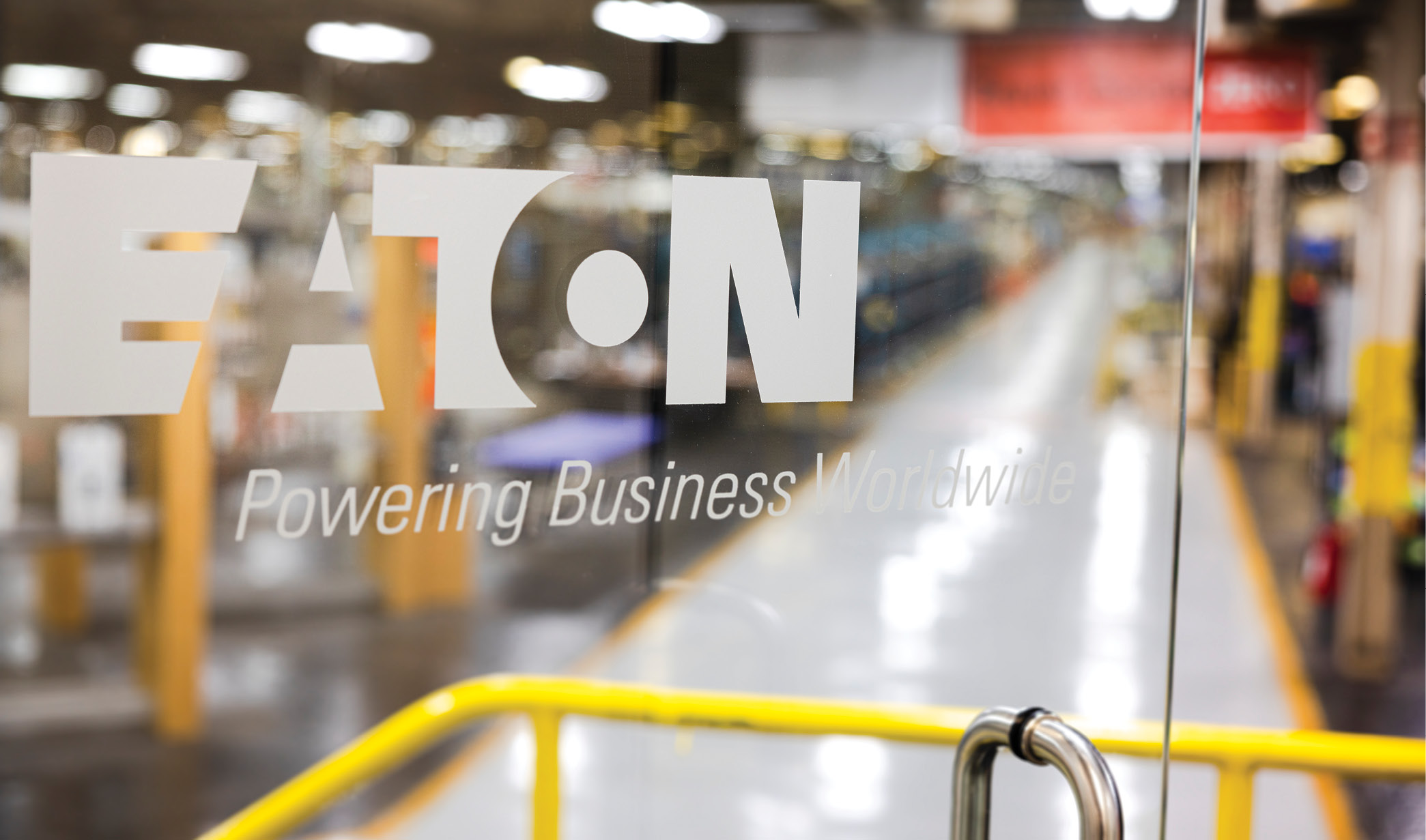
Photo courtesy of Eaton
The state has awarded Hota $3 million to assist with land, building and infrastructure costs from the Local Economic Development Act (LEDA) Job-Creation Fund. Other incentives are likely too, in addition to assistance from the City of Anthony with issuing Industrial Revenue Bonds.
The state said in the last two years, the Santa Teresa point of entry on the border has doubled the number of commercial vehicles processed per hour and hit a new record in 2022 by processing more than 160,000 trucks.
Increasing Borderzone Competitiveness
In a July episode of the Wilson Center’s “Need to Know” podcast, Mexico Institute Director Andrew Rudman, fresh off the Institute’s “Building a Competitive U.S.-Mexico Border” conference, told host John Milewski the border is “such a vibrant, essential part of our two economies. The 10 border states — six Mexican and four U.S. — combined would be the fourth largest economy in the world.” We envision the border as a customs inspection booth, he said, “but the border region is obviously much more than that.”
In terms of day-to-day business, Rudman said there have been changes since the pandemic.
“Things have shifted from just in time — where literally a widget you needed for production crossed the border and you knew it was going to cross the border at 2 p.m. and be in your warehouse at 3 p.m., so that’s when you were ready to assemble,” Rudman said. “Companies have moved now to just in case, where they’re storing more widgets on the U.S. side of the border because they aren’t as certain that they’ll be able to get them across the border.”
There are additional costs to that, Rudman asserted. All the more reason to make sure that the infrastructure works, “that we have a modern border, that we find ways to screen cargo and people efficiently,” Rudman said. Technology use, he said, could reduce the perennial tension between taking care of business and taking care of security, whether it’s a trusted traveler program for regularly scheduled trucks or scanners at railroad crossings.The use of AI to classify products helps too. “The more you can automate that, the more quickly you can move goods across the border,”Rudman said.
Some goods certainly are moving more, if not faster. The Mexico Institute reports that since the transition from NAFTA to USMCA in July 2020, the value of two-way agricultural trade shot up by 44% from $50.86 billion in 2019 to $73.14 billion in 2022 —think beer, tequila and avocados.
Rudman says workforce is another touchpoint for making the borderzone more competitive as reshoring and near-shoring continue to grow.
“Part of that is making sure a company that wants to invest in a new factory can find the engineers it might need,” he said, including those it may need to simply cross the border to do work.
One California company benefiting from its Tijuana presence is light sport aircraft manufacturer ICON Aircraft, based in Vacaville in the Bay Area. In September the company celebrated the manufacture of its 200th A5 aircraft, all built at a 300,000-sq.-ft. facility in Tijuana. ICON’s facility employs around 250 technicians and engineers.
“We are proud of the team and the infrastructure we’ve built at our production facilities in Tijuana and Vacaville,” said ICON Aircraft CEO Jerry Meyer in a press release. “We made the tough decision back in 2016 to insource our carbon fiber manufacturing and it was absolutely the right one. Now, we have control over everything we produce, and our parts meet our exacting quality standards. ICON is firmly on the map as an example of manufacturing excellence. In fact, we are having serious conversations with other companies in the industry and beyond about assisting with their manufacturing.”