A new white paper written by journalist Ann Moline and co-published by the Industrial Asset Management Council (IAMC) and the Society of Industrial and Office Realtors (SIOR) sheds light on emerging trends that will impact the way food processing firms design, site, build, and use their industrial facilities in the future.
“Recipe for Change: The Flexible Food Processing Plant of the Future,” highlights these disruptive trends and offers next-generation design and best practices recommendations for future food processing facilities.
Among the changes highlighted in the paper: Growing demand for fast, fresh, local and customized food at affordable prices means that food processors will locate production facilities closer to major population centers so they can make customers happy without upending their logistics budgets.
That trend will pick up momentum as evolving transportation and logistics technologies, along with mobile applications and real-time connectivity, give consumers ever more grocery-shopping options.
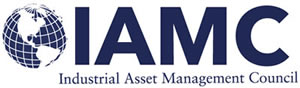
These changes will also drive a shift in how such facilities are used, including a growing convergence of activities not directly related to core production functions. Meat-packing plants, for example, will have increasingly mechanized, robotic operations, with shelf-ready packaging operations centralized on site, rather than in individual grocery stores.
Third-party providers of temperature-controlled warehousing and distribution facilities also will have an on-site presence to support food manufacturing plants in the future, a trend that has already begun, according to Tony Lucarelli of Henningsen Cold Storage. “We focus on co-locating our facilities adjacent to our customers’ plants, thus establishing long-term partnerships with them so they can maximize their cold supply chain efficiencies,” he said.
R&D, too, will have a more prominent place on site, so that emerging research can be tested and commercialized more quickly and efficiently. Several benefits arise from such changes, including safer workplaces, lower transportation costs, faster time to market, improved quality control and oversight, increased opportunity for cross-collaboration, and the potential to reduce food safety risks through less handling.
Closer Proximity Means Increased Design Focus
Veterans of public hearings before local officials on land use proposals know that community acceptance is key to ensuring a swift approval process. And incentives experts say that shrinking pools of funds along with increased scrutiny make it that much more difficult for companies to make their incentives case.
For companies in industries like meatpacking, the challenges are even greater, given the negative public relations surrounding some meat processing operations. The desire for proximity to population centers could make it difficult to obtain approval for industrial facilities that have not attended to exterior aesthetics.
“If companies want incentives, they have to demonstrate the value proposition that they offer to the community,” says Mark Beattie, a principal with location advisors Hickey & Associates. “Communities don’t want unattractive assets that could quickly become vacant eyesores.”
So, a company that proffers a more attractive, energy-efficient, water-efficient and flexible facility could stand a better chance of accessing incentives and approvals.
An open floor plan also adds to the facility’s re-use potential and value at resale. The researchers recommend production equipment situated in pre-fabricated modules that slide in and out with ease as uses change.
In addition to identifying trends that will impact the food processing industry going forward, the paper unveils a conceptual rendering highlighting six areas of innovation (see diagram), and suggests directions for future research and exploration.