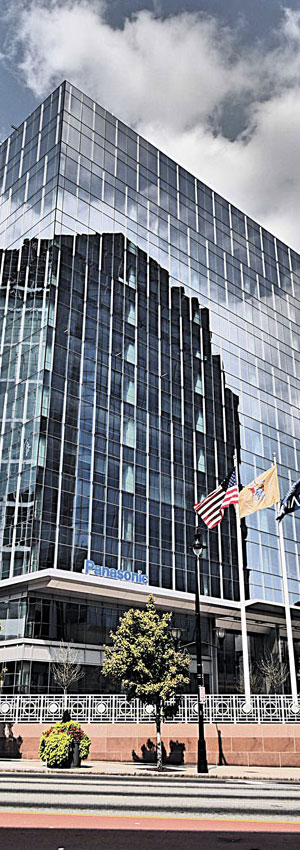
Panasonic’s new headquarters in Newark, N.J., is an 18-minute train ride from Penn Central Station in Manhattan. Panasonic CFO Mike Riccio says choosing Newark from among 40 US candidate sites came down to making “en eco-friendly statement.”
Image courtesy of Panasonic
Cory Guimond’s grandfather, Philias Guimond, began building wooden boats in the small fishing village of Escuminac in New Brunswick, Canada, in 1942. Since then, over 600 boats have been built over three generations.
“There have been two real jumps in the company history,” says Cory Guimond, president of Millennium Marine. “One was in 1980 when my father took it from wooden boat building to fiberglass boat building. And then when I made the new molds for the larger boats and took it on an international scale.”
The company is about to make another big jump, this one across an international border and into the United States — Eastport, Maine, to be precise. That’s where Millennium will expand production of its commercial fishing vessels, which are sold throughout the North Atlantic and into Europe. Making the big jump, whether it is a company expanding into a new market or increasing its presence in an existing location, has a long history in a place that speaks of history — America’s Eastern Seaboard.
From Maine to Florida, this is America’s first coast, where English, Dutch and Spanish made their first attempts at colonizing a new world. And it is here, even today, where much of commerce resides. Companies big and small are still attracted to and taking risk on the Eastern Seaboard.
Here’s a brief north-to-south survey of the risks and rewards they’re finding.
Down East
In Eastport, which just happens to be the easternmost city in the United States, Guimond says he at first was skeptical that he could find the required labor. And work force was the primary reason he had expanded his search outside his native New Brunswick.
“There is not a whole lot of work force here, as we compete here in Canada for a work force that is going out west for high-paying jobs in the oil industry. It makes it very difficult to build a boat economically here and to be competitive in the world market,” he says.
Eastport, a five-hour drive from company headquarters in Escuminac, at first seemed too small to fill the bill.
“I did have a lot of concerns about the work force initially, but after speaking to more and more people in the area, I found that many of these people had experience with electrical, plumbing, welding and carpentry. Many were doing odd jobs, because you have to do multiple things in Eastport in order to survive,” Guimond says.
The expansion of what will be called Eastport Maine Composite is being bankrolled with the help of a $1.4-million federal economic development grant. Guimond’s company will lease two-thirds ft. of a 60,000-sq.-ft. (5,574-sq.-m.) building to be renovated by a city-chosen contractor. The project is expected to create as many as 50 jobs, paying $12 to $20 an hour. Some employees are expected to be hired before the end of the year to begin limited production.
Going Up
Down in New York City, employees were not so much a factor as space, which always comes at a premium. Here it is more often than not better to go up than to go out. And that holds true for data centers, too.
John Sabey, president of Seattle-based Sabey Data Center Properties, said the opportunity presented itself back in 2011 to pounce on a high-rise office tower in Manhattan and transform it into a data center, and his company jumped at the chance.
Sabey’s company bought the upper 29 floors of the 32-floor building from Verizon, and dubbed the newly transformed tech hub as Integrate.Manhattan, which began operations earlier this year.
“The New York City Manhattan data center market is one of the top three largest data center markets in the United States and definitely top five in the world,” Sabey says. “This was a once-in-a-generation opportunity, as it would be a challenge to find another building such as we were able to acquire and do what we were able to do in that market.”
Sabey says the fact that New York/Manhattan is the most densely populated area in the U.S. is precisely what gives it an advantageous position.
“It is the primary interconnection point for global networks in the world. So there is a confluence of business reasons why New York, and Manhattan specifically, is one of the best data center markets that exists in the United States,” he says.
The Eco-Friendly Choice
Across the Hudson River from New York City, Panasonic Corp. has moved into a new corporate headquarters in Newark, N.J., the culmination of a project that was announced in April 2011 (see the July 2011 issue of Site Selection for “The Shot Heard Around the World”).
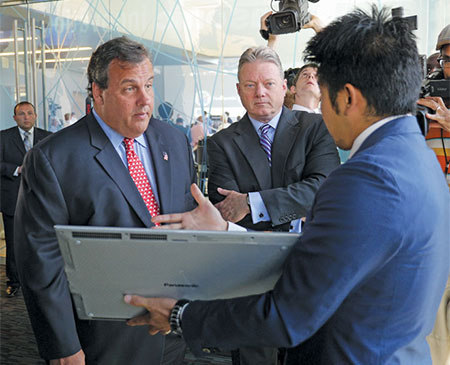
New Jersey Governor Chris Christi visits the new Panasonic corporate headquarters.
Panasonic CFO Mike Riccio says the company considered 40 sites, including those at existing facilities in Secaucus, N.J. (where the company was based for 40 years), New York City, Chicago, Atlanta and San Diego, but chose Newark because of the eco-friendly direction that the company is taking.
“We were looking to make an eco-friendly statement. That was our corporate direction — that we wanted to be the number one eco-friendly electronics company. This is one step in that direction,” Riccio says.
The company chose to sign a 15-year lease for the 12-story building, 10 floors of which it will occupy. Developed jointly by SJP Properties and Matrix Development Group, it is the first new office building in Newark in more than 20 years.
Panasonic was able to design the interior space to foster a more open and collaborative work environment, Riccio says. The new headquarters, occupied in August, also gives employees more flexibility in terms of commuting to work because of its close proximity to commuter trains, thereby coinciding with the desire to reduce the company’s carbon footprint.
“We wanted people to be able to get here,” Riccio says. “We are essentially an 18-minute train ride to Penn Central Station in Manhattan.”
Wake-up Call
Thirty-five miles south of Newark in Holmdel, people made the difference at the colossal Bell Labs complex. As far back as the 1930s, the site was a research center where scientists amassed seven Nobel Prizes in their pioneering efforts to develop the transistor, cellphones, touch-tone dialing and fiber-optic communications.
The property, which today features a complex of four five-story buildings essentially sitting inside a glass box and totaling 1.9 million sq. ft. (176,510 sq. m.), was closed in 2007 by Alcatel-Lucent, which had acquired it in a spinoff from AT&T. For years, there was no consensus as to the fate of the vacant structure, set on 473 acres (191 hectares) in a wealthy rural community.
But the white elephant has budged. On Aug. 29 Somerset Development closed on the property after years of legal and preparatory wrangling to get all the entitlements in place and the property rezoned.
“We spent literally six and a half years getting the property rezoned to mixed use, as we are looking at this more as a neighborhood and not a building,” says Somerset President Ralph Zucker.
Because of the historic nature of the property, there were many stakeholders, he says.
“We walked into an environment where there was no community consensus. So it took awhile to get the community to come together and focus on the right use and the right plans and build consensus,” Zucker says.
The neighborhood concept as envisioned by Zucker and the Somerset team includes a quarter-mile-long, 100-foot-wide pedestrian street with a square or central atrium, flanked by the five-story buildings.
“So off that street, we have restaurants, shops, health clubs, and above we have offices and even some residential users,” says Zucker. “The focus will be health, wellness and fitness.”
“We basically went down the Eastern Seaboard, and the Savannah model came up as the most cost-effective for us.”
— John Grasso, vice president of operations, Dukal Corp.
Community Healthcare Associates, a health care developer, intends to lease up to 400,000 sq. ft. of the building from Somerset. It plans to build an ambulatory surgical center, an assisted-living facility, physician offices and other medical services.
In the meantime, Somerset is working to get the property back into shape.
“We’re working now on the landscaping and making repairs to the roof, and have started to walk potential tenants through the building. We would like to see our first tenants within the next three to six months,” says Zucker, adding that it will probably take five to seven years for the project to fully mature.
Change of Scenery
While human resources was certainly one big concern, Josh Fiorini had a lot more on his mind in determining where to uproot and move his company.
Fiorini is the president and CEO of PTR Industries, now based in Connecticut and soon to be based near Myrtle Beach, S.C. PTR Industries makes guns — not just any kind of guns, but their own version of the AR-15, a semi-automatic rifle.
In the aftermath of the December 14, 2012, massacre of children at Sandy Hook Elementary School in Newtown, Conn., the political and regulatory climate was simply too difficult for PTR to remain in that state and successfully operate.
Fiorini said 43 states and several hundred economic development organizations made overtures to his company as a possible new home.
“States that have reputations for being heavy on the anti-gun side we eliminated right off the bat,” Fiorini says.
The choice came down to Texas and South Carolina. Fiorini says South Carolina was favored by most of the Connecticut employees who were willing to pick up and move, and who preferred an Eastern Seaboard location that was closer to home and family in New England.
But there were other factors involved as well, including a pool of talented retirees in Myrtle Beach who started to come out of the woodwork.
“We started to hear from people who lived in Myrtle Beach, many of whom had been forced into early retirement — 50- to 60-year-old gentlemen who used to work in the tool room at Pratt or Sikorsky or wherever. They were wanting to come back to work,” Fiorini says.
A tour of the Southern Institute of Manufacturing and Technology in nearby Florence also made a huge favorable impression.
“They have an absolutely amazing training program there for machinists, programmers, as well as tool-and-die makers. We spent an entire day there and saw the equipment that they have, the curricula and met with the instructors,” Fiorini says. “We have never seen anything like it.”
PTR will move to what was a 58,000-sq.-ft. (5,388-sq.-mm.) spec building owned by Horry County in January 2014. About half of the company’s 42 employees in Connecticut are expected to make the move down south. An $8-million investment is expected to eventually create 145 new jobs.
Where the Goods Move
The scope of John Grasso’s search ranged from the Port of New York and New Jersey to Jacksonville, Fla. His company, Dukal Corp., a leading supplier of disposable medical products, needed a distribution center near a major port of entry along the Eastern Seaboard. The location he chose was Savannah, Ga.
For Grasso, the choice boiled down to logistical costs.
“One of the major driving forces for us is that we import 90 percent of our product from Asia,” says Grasso, Dukal’s vice president of operations. “So the cost to bring containers, our inbound freight, is probably one of the biggest cost components. When I looked at inbound freight costs, Savannah and Charleston gave us the lowest rates.”
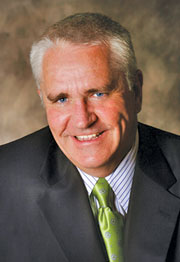
Lawrence Rydzewski, COO, Berlin Packaging
Six months of outbound freight data was also analyzed, and again it came down to Charleston or Savannah, but with Savannah having the edge.
“From our perspective Savannah is a bigger port and has more traffic, which gives us better shipping lanes and a better time perspective,” Grasso said. “We basically went down the Eastern Seaboard, and the Savannah model came up as the most cost-effective for us.”
Dukal has contracted for 140,000 sq. ft. (13,006 sq. m.) within a 400,000-sq.-ft. (37,160-sq.-m.) building that is close to Interstate 95 (north-south) and I-16 (east-west) and less than six miles (10 km.) to the port. The space features 32-ft. clearance and 32 dock doors and is within Savannah’s Foreign Trade Zone.
Down in South Florida, another warehouse project is already making waves. Lawrence Rydzewski, chief operating officer of Chicago-based Berlin Packaging, says his company, with 90 locations in North America, recognized a huge opportunity in the Miami area and made its move.
“We wanted to expand our presence in south Florida and frankly take on a major competitor that has dominated the market there. We felt this was a good market to go after because the customer base there for rigid container packaging was starving for other sources,” he says.
Berlin Packaging found a 40,000-sq.-ft. (3,716-sq.-m.) warehouse in Miramar, where it will house customers’ packaging components for just-in-time delivery and enable same-day shipping to virtually the entire state of Florida.
The new warehouse in the Miramar Park of Commerce, developed by Sunbeam Properties & Development, is adjacent to the Florida Turnpike and features high ceilings and large bays to optimize space utilization.
“This facility will allow us growth in that market for the next five years,” Rydzewski says.