ConAgra Foods Lamb Weston‘s new sweet potato processing plant in Delhi, La., has hit a sweet spot in terms of sustainability. The plant, which began operations last September in the small town 30 miles (48 km.) east of Monroe, is the first frozen food plant in the world to earn LEED Platinum certification, the highest distinction available to green buildings. The design, construction and operations at the Delhi processing facility were all developed with environmental impact and sustainability in mind.
The plant landed in Delhi (“dell-high”) because of its proximity to Southern sweet potato growing states, says Rick Martin, vice president, manufacturing, Lamb Weston. Delhi was the winner in a search that covered about a dozen Southeastern locations.
Heretofore, the company has processed sweet potatoes at facilities that also process russet or Irish potatoes, but health conscious Americans have been consuming lots of sweet potatoes in recent years. That’s the key driver in ConAgra’s decision to build its first dedicated sweet potato plant.
Martin says Delhi, located near Interstate 20 and just west of the Mississippi, offered a good mix of what industrial site seekers routinely seek: good rail and highway transportation systems and a good, qualified work force. Strong local support for the plant was clearly evident. And Delhi has good proximity to sweet potato growers.
“We bring in potatoes from a wide area, the majority from the Louisiana-Mississippi-Arkansas area, but we go as far as North Carolina to source raw potatoes,” Martin says. “We have been working closely with our growers to provide high-quality sweet potatoes.”
The US$156-million plant, built with future expansion in mind, currently employs 275. The company processes about 20 different kinds of frozen sweet potato products, but does not publicly disclose which ones are made in Delhi.
Achieving the top LEED distinction gives ConAgra Foods Lamb Weston added cachet, Martin says.
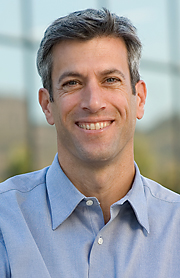
“LEED certainly gained the interest of a lot of our customers,” he says. “What is important to us is how it supports the environment. It makes sure the plant is a sustainable operation. Our customers are very interested in understanding and learning more about the LEED process, and we expected that.”
A scan of all LEED-Platinum designations worldwide as of mid-2010 revealed mostly commercial office projects, a couple warehouse/office projects and only two other manufacturing projects: apparel plants located in Sri Lanka from Brandix and MAS Intimates.
A Case of Rising Expectations
Greg Lambier, director of engineering for Lamb Weston, says the company combined its in-house approaches to energy-footprint reduction with those provided by the Burlington, Wash.-based architectural firm Fisher & Sons, which served as project manager. Lamb Weston also hired the Seattle-based sustainability consultancy Paladino to guide the administrative process of LEED certification.
“They were key members of our team and were engaged very early on,” Lambier says. “We looked at what we were doing for our plant already and what LEED involved and married the two. They helped us with things we didn’t have experience with in terms of sustainability practices to come up with a good project.”
As a result, Lamb Weston reduced energy consumption at the 165,000-sq.-ft. (15,328-sq.-m.) building by 40 percent compared to similar-sized facilities. Construction relied heavily on recycled materials, accounting for 29 percent of the building’s content. This includes recycled steel and recycled materials used in concrete and carpet. In addition, 90 percent of the building’s construction debris, including metal, wood and plastic, was recycled.
Lambier says achieving Platinum LEED status was not an initial goal, but, expectations rose. “We didn’t know what level we could achieve since it was our first time through the process,” he says. “Our expectations went up as we went through the design process, so we raised the bar.”
A long list of features gives the plant a green feel. More than 100 acres (41 hectares) of the property will be maintained as open space, including protected wetland areas, ponds and restored native vegetation. Water is conserved outside the building by landscaping with native plant species that require no irrigation once established.
The plant is climate controlled to increase worker productivity, safety and comfort. Climate control in such a hot, humid environment reduces condensation build-up and water on the floors, thus reducing slip and fall hazards. Materials such as low VOC carpeting, cleaning products and paints are used in the interior of the plant to reduce occupant exposure to airborne pollutants.
“We do a lot of energy recovery and recycling in the plant,” Lambier says. “Some are proprietary processes.”
Biogas, produced by treating process waste water, is piped back to the plant boilers to produce steam. This process is expected to offset approximately 20 percent of the annual natural gas demand of the plant, and prevents methane from entering the atmosphere.
“The LEED program does a very good job of education, and we will continue to learn from it,” Lambier says. “We’ve installed bicycle racks so some employees can ride bikes to work, and we give parking spots close to the entrance for car pooling. We educate people about recycling. The internal publicity engages our employees.”
Austin’s Cali Connection
Since 2004, 47 companies have either relocated from or expanded out of California to Austin, Texas. Of the city’s 28 relocations in 2010, nine were from California. The city is counting on that trend to continue with the hiring of a California-based site consultant to keep the pipeline flowing.
“We typically take 10 to 12 marketing trips to California, and this year we decided to open an office in California for business development purposes,” says Dave Porter, senior vice president, economic development, for the Austin Chamber of Commerce. “It will generate leads and respond quicker to leads. California is our greatest source of success, and we will continue this effort at least through this year.”
Irvine-based RSH Group is Austin’s representative in California. Porter believes Austin is the only city to have an economic development office in California. He says RSH is focusing on software-related companies, creative media, life sciences, automotives, green industries and advanced manufacturing.
“It’s a way to separate us from what others are doing,” Porter says. “We target tech-related companies in high-cost areas like California and show them our advantage in labor costs and the lack of an income tax. We show them that they can get an equally talented work force here, plus the quality of life will be better. We are hearing that companies just don’t want to grow there anymore. They may stay there, but they just can’t grow.”
California firms choosing Austin in recent years include Facebook, Sun Power and online legal document service LegalZoom.
For Los Angeles-based LegalZoom, it was a need to expand beyond its Southern California roots with an augmentation of its existing operation, says Mike Wilson, vice president of operations in Austin. LegalZoom also wanted a lower cost profile as it recruited up to 600 people over the next five to 10 years for its expansion. Another consideration was staying within a two- to three-hour flight from Los Angeles. The search encompassed cities including Albuquerque, N.M.; Provo, Utah; Boise, Idaho; and San Antonio.
“We geographically constrained ourselves to the western half of the U.S.,” Wilson says. “Obviously we wanted to make sure it’s a place that reflected the diversity and culture of our company. We wanted a place where we would be able to attract and retain the type of work force to complement the type we had in California over the first 10 years of the company. It became pretty clear that Austin was the front-runner.”
Wilson says the eclectic nature of Austin’s culture and the community’s progressive thinking were other key factors. He also cites the Austin Chamber’s efforts.
“The idea of expanding was a first for our company. The ability to have a business partner like the Chamber helping us to navigate the process as well as put together a set of attractive incentives was a tremendous value to the experience.”
LegalZoom used Jones Lang LaSalle to guide the company through the real estate selection process as well as manage incentive negotiations with the city and the state.
Consolidation Dilemma
The prolonged economic downturn created long-term ripples through many industrial sectors, including roofing products for commercial buildings. That posed a dilemma for Firestone Building Products, which operates plants in Prescott, Ark., and Kingstree, S.C. The company needed to close one of the plants and consolidate operations into the other, but the choice wasn’t immediately evident even though the Prescott facility is larger. Both plants produce (ethylene propylene diene monomer) roofing membrane, and have been running reduced shifts.
Last fall Firestone executives approached officials with both states to see what kind of incentive packages might be available. After a few months of deliberating, the Prescott site was pegged for the expansion. The Kingstree plant will be closed by the end of June, and 100 employees will be hired in Arkansas as the Prescott plant ramps up to increase production.
Arkansas offered the following incentives, according to the Arkansas Economic Development Commission: $1.25 million from the Governor’s Quick Action Closing Fund for on-site infrastructure; Create Rebate — a 5-percent payroll rebate for five years only for new jobs; InvestArk — provides sales tax credits on qualified equipment for construction or modernization; $225,000 for training.
“Both states had a very comprehensive set of initiatives,” says Ken Weaver, president, FSBP, and chairman, CEO and president of Firestone Diversified Products. “While the package from Arkansas was comprehensive, it was a combination of factors that led us to our decision. By the time we are done expanding in Arkansas, we will have the capacity to make both plants’ production. Both states were very well organized, and we looked at a number of different alternatives with economic development agencies that frankly we were surprised at.”
Weaver says the Prescott plant has more diverse capabilities, and to expand it to have the equivalent capabilities of both plants is much easier than it would have been in Kingstree. He says there are some positive indicators for improvement in the roofing market, but it’s not yet translating into building starts.
“The challenge is credit. There is a lot of liquidity in real estate investment trusts, but there is a lot of uncertainty. There are enough projects out there to do. We just have to get people out there. My best advice is to stay lean. We have gone through a really tough last 24 months. In our case, our expectation is for moderate growth over the next couple of years.”
OK Wind Projects Propel Regions
Even as oil companies such as Baker Hughes continue to fortify their footprints in Oklahoma, alternative energy also is taking giant steps into the state.
Eagle Claw Fabrication, LLC, is building a 150,000-sq.-ft. (13,935-sq.-m.) facility specifically designed for the construction of wind turbine towers at the Port of Muskogee. Eagle Claw expects to create approximately 175 jobs in Phase 1 of the $28-million project.
The manufacturing facility is scheduled to come online this spring and move to full capacity late in 2011 to meet growing demand for new wind towers. The 47-acre (19-hectare) site on which the facility will be built is adjacent to the Port’s railcar marshaling yard, connecting with the Union Pacific Railroad in Muskogee.
“Access to the McClellan-Kerr Waterway, via the Port of Muskogee, provides Eagle Claw with unique and substantive competitive advantages over other turbine tower manufacturers, including substantial transportation cost savings that can be passed along to its clients,” said Tom Word, company founder.
Eagle Claw will be able to acquire steel and distribute towers by truck, rail or barge. At the Port of Muskogee, Eagle Claw will have access to markets not otherwise accessible from an inland location. In addition to onshore wind towers, Eagle Claw says it will also have capabilities to fabricate offshore wind towers and other heavy tubular structures for the geothermal, tidal, solar, hydrokinetics, biomass and carbon capture sectors.
ACCIONA Energy has begun construction on the Dempsey Ridge Wind Farm located in Roger Mills County, on the western border of the state below the panhandle. The 132-megawatt wind farm will take approximately one year to build. It will be the company’s sixth wind farm in the U.S. and third in Oklahoma. The project will create enough energy to power around 46,000 homes in Oklahoma and surrounding states.