A rower on the Canadian national team in 1987, Joe Camillo knows a thing or two about the cadence of success, and converting efficient operation into forward momentum. He and the city of Hamilton are therefore a good match.
After earning his MBA at McMaster University in Hamilton, Ontario, in the mid-1980s, he went on to found RegattaSport apparel company in St. Catharines, Ontario, in the province’s Niagara region, in 1988. The operation partnered with a family-owned cut-and-sew operation in Hamilton. The opportunity came in 1994 to take over the Hamilton shop, which he named Niko Apparel Systems after Nikole, the first of four children.
Today the company’s technical sports apparel from both shops is sold all over the world to runners, cyclists, football teams and even the U.S. national dragon boat team. And it’s all made in Hamilton.
“I think sport is a big part of our lives,” he says. “Part of our success is myself and my partner in St. Catharines are heavily involved in sport. There’s an affinity in understanding the need for discipline, determination and teamwork.”
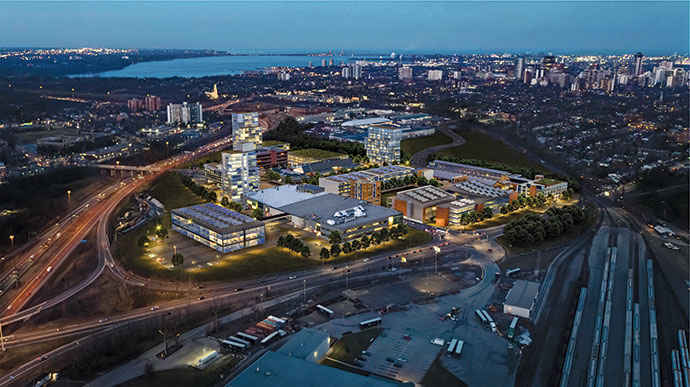
Camillo says their success also comes from “creating products and having relationships with partners who recognize the importance of locally made, custom made, competitively priced and attractive products, and they have to be delivered on time,” he says. “We’re still little. Being nimble and flexible is key.”
That was especially so in 2020, when Niko answered the call from McMaster University Engineering and Hamilton Health Sciences (HHS) to provide locally manufactured masks for hospitals in the area. Niko has also developed reusable, washable masks for hospitals, industries and public use, all made by around 32 employees.
When a pandemic-induced shutdown was announced in March 2020, Camillo was prepared to lay off all staff until the situation improved. Then he received an email from one of Canada’s centers of excellence asking if he’d be interested in working on a surgical mask.
“I had never made a mask in my life. But when your back is up against the wall … I said, ‘Sure, I will do it.’ The team at McMaster started to coordinate with our design team. We had a skeleton crew, and sourced material from all over the world. Over a period of months, we converted our boardroom into a system, selecting and testing the proper materials to provide the right metrics for a disposable surgical mask.”
“During that time, because we were fortunate enough to have McMaster work with us, we became a conduit for people to ask for other things, and got into reusable masks,” Camillo says. “That pushed our staffing levels. There was a great need. We manufactured hundreds of thousands of masks for companies all over Canada,” including 140,000 for Canadian communications giant Rogers. “That was massive,” he says. “They tried to order foreign at the beginning, and the masks were terrible. Those orders saved our business.”
Along the way, Niko worked with Fox 40 International, known for its Fox 40 whistle used by officials in the NBA, NFL, NCAA and other sports organizations, to develop a whistle cover to reduce spittle from use of the whistle. Thousands of the whistle masks have now been produced for the NBA, NCAA, CFL and other leagues.
McMaster: Anchor Institution on the Prow of Discovery
Camillo has nothing but praise for McMaster and the team led by Prof. John Preston, associate dean for the faculty of engineering, and Ravi Selvaganapathy, professor of mechanical engineering and biomedical engineering who heads the newly formed Centre of Excellence in Protective Equipment and Materials (CEPEM) at McMaster. “Without McMaster, we wouldn’t have had the energy and tailwinds to push us forward,” Camillo says. CEPEM has also worked with local packaging manufacturer Whitebird to make more than 1 million face shields since March 2020, helped by $3.9 million in federal funding; and with Ontario auto parts manufacturer Woodbridge Foam Corp. to test materials for a certified high-performance L3 surgical mask.
The university also is partnering with McMaster Innovation Park (MIP) to launch The Global Nexus for Pandemics and Biological Threats, an international network of scientists, clinical health and medical specialists, engineers, social scientists, history and policy researchers, economics and business experts.
Ty Shattuck, CEO of McMaster Innovation Park, tells me the Global Nexus is the latest example of how “research continues to be at the core of our value.” Company partnerships abound alongside that research focus, such as the University of Toronto spin-off CCRM, a regenerative medicine-based technologies and cell and gene therapies company that signed an agreement with MIP in November 2020 to establish a Contract Development and Manufacturing Organization (CDMO) and ultimately a Biomanufacturing Campus (BMC) some 300,000 sq. ft. in size.
“There is a lack of space in Toronto to build manufacturing facilities,” explains Shattuck, “and what space is available is not economically feasible. MIP’s proximity to Toronto along with access to talent, logistics, space and manufacturing expertise led to the selection of MIP as their location.”
“Our partnership with MIP is about more than building a facility,” said CCRM President and CEO Dr. Michael May in November. “This is about building domestic manufacturing capacity within the region for the next generation of medical advances. Our expectation is that the biomanufacturing campus within MIP, and the CDMO, will result in jobs, economic stimulus for the region and, most importantly, life-saving products for patients. For Canada, our opportunity to be amongst the global leaders in cell and gene therapy is of strategic significance.” CCRM will retain its current Toronto offices, research facilities and manufacturing facilities in the universally praised MaRS Centre business accelerator in Toronto.
“At MIP, our sector focus is aligned with the research strengths of McMaster University and the economic pillars of the area,” Shattuck says. “We are leveraging Hamilton’s historic strength in manufacturing to life sciences. In other words, we are seeing the intersection of advanced manufacturing and life sciences.”
Fusion Pharma is another company in scale-up mode that is expanding into a new facility at MIP. “This scale-up theme is part of our core strategy,” Shattuck says.
Banner Year
It might be considered a core strategy in general for Hamilton, which has seen a record year for projects as it also continues to welcome startups and cultural movers and shakers.
“In the midst of a pandemic, it’s been the most successful year ever from an industrial building perspective,” says Norm Schleehahn, director of Invest in Hamilton, now in his 30th year with the city. His January presentation to city council featured a slide listing 15 projects under construction. He also showed city leaders that his team had even surpassed their stretch target — “we call it an overreaching target” — of 7 million sq. ft. of new commercial real estate between 2016 and 2020, which was more than double the 3 million sq. ft. achieved between 2011 and 2015.
Investors include L3 Harris, DHL, Bridgestone and Amazon, which has invested in two facilities in the area. “It’s a tale of two economies right now,” he says. Tourism, personal services and small businesses are hurting, but manufacturing, distribution, food and beverage and life sciences are flourishing.
The Amazon projects, says Schleehahn, came in the wake of Hamilton being part of the HQ2 sweepstakes in 2017. The company saw that Hamilton was home to the No. 1 cargo carrier airport in the country, and noted at the time it would be an ideal location for a fulfillment center.
Meanwhile, the Hamilton team continued to cultivate relationships with developers such as Panattoni, which has worked with Amazon in the past and which recently acquired 82 acres by the airport.
Today, he says, “a lot of developers have taken an interest in the city. This morning I was in a discussion with three different developers about a total of over 1 million square feet of potential property in the city. It used to be we’d be thrilled with a 250,000-square-foot development, and we still are, but now they’re talking in the range of 500,000 to 1 million square feet. We only have so much land, and our next objective is to get more services around the airport.”
A new trunk sewer line is expected to open up a lot more land in that vicinity. But projects underway in the meantime are expected to bring up to $21 million in new taxes to the city.
It’s all part of a rebirth for this former steel town that’s been aided by other infrastructure such as perimeter roads and highways, says Joe Camillo, who credits economic developers like Schleehahn with supporting small businesses and entrepreneurs, and likes the increasingly diverse richness of the city and its cultural scene.
“It’s not just infrastructure, but what attracts people,” he says. “People want to live in Hamilton. They’re developing down by the piers. There are things to do with your family, and a lot of leaders and visionaries have come here. Look at real estate right now, it’s going through the roof. It’s because people see it as a diamond — not a diamond in the rough.”