What happens when an area’s supply of engineering talent dries up and it can’t supply its local aerospace cluster with the labor it needs? Wichita does not intend to find out.
Kansas’ largest metro is arguably one of the leading aerospace centers in the US with major operations from Spirit AeroSystems, Textron Aviation (Beechcraft, Cessna and Hawker), Airbus Engineering, Dassault Systemes and other aviation manufacturers. It’s also home to the National Institute for Aviation Research (NAIR) at Wichita State University (WSU), an R&D facility specializing in testing and certification of airframe technologies.
In other words, there’s no shortage of aerospace engineering talent in Wichita today, but employers can’t count on that being the case forever. And Wichita can’t assume it will always be able to supply the talent required to be competitive in the future with other aerospace hubs. That’s why Wichita State University’s former golf course is now a construction zone. Before long, those 150 acres will be WSU’s Innovation Campus, where aerospace and other companies can locate non-manufacturing facilities and hire student engineers into work programs that could well result in permanent employment.
Facilities for Airbus and Dassault are already under construction. Other campus features will include an Experiential Engineering building “for greatly expanding technology-based economic growth and diversification for the metropolitan area and the region,” according to Tracee Friess, director of communication, research and technology transfer at WSU. A membership-based Maker Space facility, says Friess, is “a cross between a business incubator, a manufacturing plant and a design studio — a place where creative people of all ages and skill levels will have access to sophisticated equipment and training, shared work spaces, expert advice and a supportive community of like-minded people.” NAIR and an Applied Technology Acceleration Institute are two additional features. The latter, says Friess, “is focused on building strong partnerships and providing applied and experiential learning opportunities for students while transforming the very way the educational experience is developed, packaged, delivered and supported.”
Demand — Meet Supply
Championing WSU’s Innovation Campus — and the future of Wichita’s aerospace industry more broadly — is Dr. John Tomblin, WSU Vice President for Research and Technology Transfer, and director of NAIR. Few are as plugged into the city’s aerospace cluster as Tomblin, who estimates the sector’s current local demand for aerospace engineers at about 300.
“WSU and other schools in Kansas are not producing enough engineers to meet that demand,” he relates. “Let’s assume WSU did produce 300 engineers, and we send them all to one of the aerospace companies. Not one of them will get hired. Part of the problem is they don’t have the experience. Industry is looking for a low-cost workforce, and they don’t want to invest the typical two years it takes to hire a new graduate to train them to be effective in their industry.”
That’s where the Innovation Campus comes in.
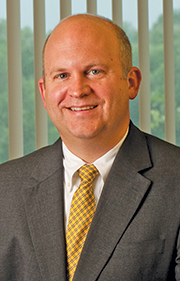
“I can offer both in an applied learning environment,” says Tomblin. “I started this in a major way three years ago. When Beechcraft went through bankruptcy, they were sourcing everything out to India, and I would tell them, ‘I have a low cost labor force, too, and I can beat $40 an hour — my students will work for $10 to $15 an hour.’ They said they couldn’t do the job, and I said ‘I beg to differ.’ So I competed for a job and basically won on cost, quality and time. At that point, they hired 80 students and did $250,000 worth of work. According to the data on that experience, we had a 96 percent job placement rate for those 80 people. The other 4 percent went to grad school, so that’s 100 percent job placement; 38 percent of those stayed with Beechcraft, and 83 percent of those stayed in Wichita.
“Why is Airbus moving its North American engineering headquarters on to the Innovation Campus? And why are other companies considering it? I have an applied learning environment,” says Tomblin. “These are undergraduate students going to school in an applied learning environment. The companies get a low-cost workforce, and at the same time they are training a future engineer.”
Why is Airbus building an engineering center on WSU’s Innovation Campus? Any why is Airbus doing engineering work in Wichita anyway?
“The main engineering centers are in Toulouse, France; Hamburg, Germany; and Filton in the UK,” explains John O’Leary, vice president and general manager, Airbus Americas Engineering. “The work we do here is an extension of the wing design office in Filton. No one else in Airbus engineering is doing the same work we’re doing — we’re an extension.”
Pylon testing on Airbus’ newest airliner — the A350 — is among the work done by O’Leary’s team in Wichita. “There are large attachments made of titanium that attach the A350 engine and pylon to the wing — it’s a very critical structure designed here in Wichita for the A350 program. When the company decided it needed to do some developmental testing on those components, we said since the design was done at Wichita, why don’t we do the testing at NAIR? They do a tremendous amount of structural testing, so it’s well within their sweet spot to be able to do this.”
O’Leary says Airbus’ ties to the university have gotten closer over the last several years.
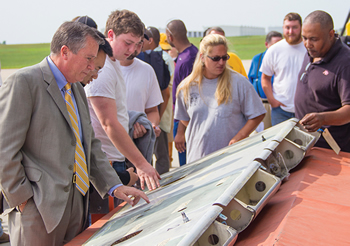
“We work with a few WSU students — the university is building what it calls an experiential learning model for undergraduates,” he relates. “We’ve used a handful of their students in the past, and one of the things we’re looking to do as we move onto the Innovation Campus is to expand that model, the applied learning model.
“There are two elements to it for us,” says O’Leary. “One is a strategic element. If this cluster is going to remain active and viable, then we need to have a pipeline of qualified engineering talent coming into the region in order to replace those who are retiring, for example. Within aerospace there is a term known as the gray tsunami, but it’s an aging workforce. Because of the tech bubble, there is kind of a trough where we don’t have a strong pipeline of engineers coming up behind us — and it’s aerospace workers as well. By using the applied learning model, we will get undergraduate engineers and potentially graduate engineers engaged in working in the aircraft engineering environment prior to graduation. That way they hit the industry ready to go with a better perspective on applying what they learn in the classroom to real life. And we get to pick out the best up and comers.”
Aerospace engineering companies on WSU’s campus also benefits WSU.
“The university does a very good job of recruiting today,” says O’Leary. “But I believe it’s also understood on the university side that if they have a company name up there like Airbus or Spirit AeroSystems or Textron Aviation, and as potential students come and walk around the campus, they realize they could work at a fast food company somewhere else, or go Wichita State and work at an aerospace company while they’re still going to school and get paid for that. It helps us in terms of having a pipeline of talent coming into the industry and it helps the university in terms of talent coming onto campus. It helps the whole sector.”