This is not just the land of Thoroughbred horses and bourbon whiskey. No, Kentucky is far more than that. This is a place where cars and trucks are built and in a very big way.
Kentucky’s automotive industry employs nearly 80,000 people at more than 450 motor vehicle-related facilities in 80 counties. Kentucky trails only Ohio and Michigan as a top vehicle producing state.
On a per capita basis, Kentucky led the nation in light vehicle production in 2013. The Commonwealth produced a state record 1.2 million vehicles, a 22-percent increase over 2012.
Proof that Kentucky’s automotive industry is firing on all cylinders is seen by the fact that since January 2010, about 230 motor vehicle-related projects have been announced in the state, representing 15,700 new jobs and $3.6 billion in capital investment. That’s more than one-third of all new investment announced in the state during that period.
Kentucky motor vehicle exports were up to 42 percent in 2013. That amounts to nearly $4 billion. The state’s exports grew third fastest among major motor vehicle producing states.
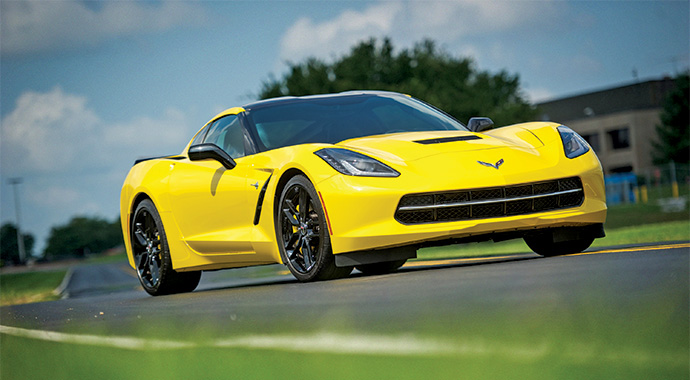
The 2014 Corvette Stingray, manufactured at the General Motors Bowling Green Corvette Assembly Plant in Bowling Green, is the most powerful standard model ever with an estimated 450 horsepower. It will accelerate from 0 to 60 mph in less than four seconds.
Photo by Joe Imel
OEMs – Original Equipment Manufacturers such as Toyota, Ford, and General Motors – continue to invest billions of dollars in the state, with Tier 1 and Tier 2 suppliers following suit.
Toyota’s decision to locate its first production site in the United States for the Lexus ES 350 at Toyota Motor Manufacturing Kentucky (TMMK) in Georgetown is one of the bigger stories in recent years. Construction on the future assembly line began in January 2014.
The move, announced in April 2013, is expected to create 750 new jobs. To support the new dedicated assembly line, Toyota will invest $360 million in the Georgetown plant, and another $171 million in other plant refurbishments, said TMMK spokesman Rick Hesterberg.
About 50,000 Lexus vehicles a year will be produced, bringing the plant’s total annual production capacity to more than 550,000 vehicles. It will be the first time the ES 350 will be assembled outside of Japan. Production in Georgetown is expected to begin in the fall of 2015.
The plant’s longstanding experienced workforce was a primary deciding factor in the Georgetown plant being chosen to build the first Lexus vehicles in the U.S. Toyota now builds the Lexus ES 350 at a plant on the island of Kyushu in southern Japan.
“When the company considered where to build one of its luxury models, there were many factors that went in on that decision,” said Hesterberg. “I think some of the cost factors included the experience of our workforce. The Kentucky plant has some of our most veteran and accomplished team members.”
Established in January 1986, the Georgetown plant is Toyota’s largest manufacturing facility outside of Japan, employing about 7,000 people. New hires as a result of the Lexus ES 350 production will bring the total to more than 7,700, Hesterberg said.
The plant, which comprises 7.5 million sq. ft. under one roof, currently assembles the Toyota Camry, Camry Hybrid, Avalon, Avalon Hybrid and Venza, and manufactures 4-cylinder and V6 engines.
The company’s North American Manufacturing & Engineering Headquarters is north of Georgetown in Erlanger, Ky., and its North American Parts Logistics Division is located in Hebron. The company currently employs about 12,000 people in Kentucky.
But Toyota is not the only OEM to see the value of expanding in the Bluegrass State.
Ford Motor Company, which celebrated its 100th anniversary in Louisville in 2013, is also making important production moves.
The company began operations in 1913 in a small shop on South Third Street in Louisville, where 11 employees built 12 Model T vehicles a day. In 1955, Ford began producing vehicles at its Louisville Assembly Plant off Fern Valley Road. Today, the 3-million-sq.-ft. plant on 180 acres employs 4,400 workers producing the Escape SUV on three shifts.
In 2011, the Louisville Assembly Plant underwent a $600-million retooling to prepare for Ford Escape production with more than 20 miles of conveyors and nearly 1,000 programmable machines and robots. At the time, Ford billed the facility as the “most flexible automotive assembly operation in the world.”
And beginning in the second quarter of this year, the Louisville Assembly Plant begins production of the 2015 MKC, which is Lincoln’s first entry into the “compact luxury crossover” market.
Ford is also upgrading and expanding the nearby Kentucky Truck Plant(KTP), where it employs more than 4,000 people. More employees are soon to come, too, as Ford prepares to boost production of its popular F-Series. The plant will invest $80 million, expand operations and add 350 jobs. The move will help Ford increase production capacity by an estimated 15 percent.
Ford manufactures the F-Series Super Duty line of trucks as well as the Expedition and Lincoln Navigator SUVs at KTP. The 4.6-million-sq.-ft. plant on 500 acres opened in 1969.
General Motors plans to move its Performance Build Center from Wixom, Mich., to its Bowling Green Corvette Assembly Plant.
The move of the Performance Build Center follows in the wake of the Bowling Green plant undergoing a $131-million upgrade, including $52 million for a new body shop to manufacture the new aluminum C7 frame.
The 2014 Chevrolet Corvette Stingray – the seventh gener-ation Corvette and the first to bear the Stingray name since the 1976 model – began production in Bowling Green in September 2013. Designed to rival the Porsche 911 and other world-class sports cars, the car has been well received by critics.
The new Corvette, which went on sale last year, sports a redone 460-horsepower, 6.2-liter V-8 that had 25 more horsepower than the base engine last generation, but with better fuel efficiency.
The Kentucky-built vehicle was named 2014 North American Car of the Year by a panel of automotive journalists at the North American International Auto Show in Detroit.
Automotive suppliers, many of them foreign based, have also been quite active with their own expansion projects in Kentucky.
German supplier Mubea opened a new $60-million plant near Florence in October 2013. The northern Kentucky plant manufactures tailored rolled blanks and will supply various automakers. The flexible rolling mill was built in 18 months.
Doug Cain, CEO of Mubea North America, said the plant is the only one of its kind in North America.
“The innovative technology we’ve brought to northern Kentucky is a key factor in our continuing successful growth,” Cain said.
Mubea, which is a privately held subsidiary of Muhr und Bender KG, makes stabilizer bars and coil springs used by Volkswagen Group, General Motors, Ford Motor, Fiat-Chrysler and others.
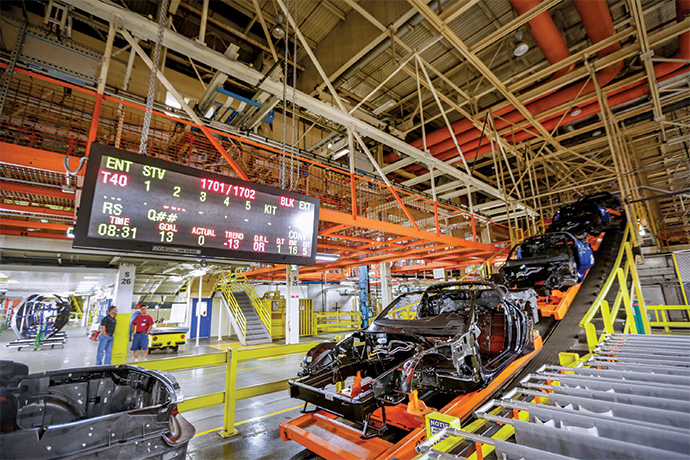
014 Chevrolet Corvette Stingray frames enter the assembly line at General Motors’ Bowling Green Corvette Assembly plant in Bowling Green.
Photo by AJ Mast
“The innovative technology we’ve brought to northern Kentucky is a key factor in our continuing successful growth.”
— Doug Cain, CEO of Mubea North America
There were more German projects in the works for Kentucky in 2013.
In August, German plastics specialist Dr. Schneider Automotive Systems said it would invest $29 million to open a plant in Russell Springs, to serve Mercedes-Benz, BMW and Ford. The new plant is within 112 miles of Ford’s car assembly factory in Louisville, about 310 miles from Mercedes-Benz’s Alabama site, and 370 miles away from BMW’s factory in South Carolina.
Dr. Schneider specializes in designing and molding plastic interior parts such as heating and air conditioning registers and movable cup holders. The 85-year-old family-owned company is a pioneer in the processing of plastics and produces high-end vent and trim systems for OEM manufacturers around the world. To meet increasing customer demand, the plant in Russell Springs will manufacture parts for companies such as Ford, GM, BMW, Mercedes, Volkswagen and more.
“At the end of an intensive selection process where we checked 69 locations, we decided to choose Russell Springs,” said Wilhelm Wirth, member of the Dr. Schneider board of directors. “The decisive factors included the quality and expandability of the facility and the competitive location costs.”
The Bilstein Group announced in October 2013 that it would establish a new production plant, Bilstein Cold Rolled Steel LP, in Bowling Green.
The family-owned German automotive supplier said it would spend $120 million in building the new plant, a 150,000-sq.-ft., cold-rolled steel manufacturing facility in the 72-acre Kentucky Transpark in Bowling Green. The plant will eventually employ about 90 people.
“We are absolutely certain that Bowling Green is the perfect spot for our new state-of-the-art cold-rolling mill, our most advanced annealing furnaces and slitting operations,” said Marc T. Oehler, CEO and partner of Bilstein Group. “Being both sufficiently close to our customers, suppliers and well within reach from Europe and any place in North America was critical to our decision.”
In conjunction with and a part of the Bilstein Group’s planned rolling mill, Horizon Steel, a U.S.-based producer of flat rolled steel products, said in November that it would also open a new facility in Bowling Green to supply the Bilstein plant. Horizon will eventually employ 30. (For more, see p. 58.)
A. Kayser Automotive Systems USA, a subsidiary of Germany-based A. Kayser Automotive Systems GmbH, announced in August 2013 that it would build its first U.S. plant in Fulton, Ky. The company’s decision to locate a plant in Kentucky follows Gov. Steve Beshear’s visit with Kayser officials during an economic development trip to Germany in January 2013.
Kayser will invest more than $17.5 million in the project, creating 121 jobs. The future plant will produce modules and ready-to-install systems for automotive OEMs and Tier 1 suppliers.
“The U.S. market is very important to us, and we believe that Fulton, with its skilled employees, will ensure that we continue to live up to our high quality standards,” said Kayser CEO Kurt-Heinz Borth.
“We have had great experiences working in Kentucky, and we have never regretted our decision.”
— Susumu Koike, President/CEO, Kobe Aluminum Automotive Products
German automotive supplier iwis Motorsystems ramps up production this year in Murray, to produce timing drive systems. The plant represents a $12.5 million investment and, when fully operational, will employ 75 people. The company began operating in the 119,000-sq.-ft. facility last year that used to house Webasto.
FDI Plays a Major Role
Kentucky has added nearly 100 new facilities over the past decade through foreign direct investment. In 2013, nearly 40 percent of all capital investment and almost 30 percent of new jobs announced in the manufacturing, service and technology sector were a result of foreign-owned companies.
The state maintains economic development offices in Hamburg, Germany and Tokyo, Japan.
Japanese automotive companies have joined their German counterparts in investing in new plants in Kentucky. There are more than 150 Japanese-owned manufacturing plants now operating here, employing more than 38,000 people.
Hayashi Telempu North America Corp., a subsidiary of Japan-based Hayashi Telempu Corp., announced in March 2013 that it would spend $10.7 million and add 103 jobs at a manufacturing operation in Frankfort. Operations will start in September 2014.
Hayashi Telempu, which has more than 3,000 employees worldwide, manufactures automotive interior parts. Its Frankfort operation will occupy a 60,000-sq.-ft. facility.
“This new location will enable us to improve our ability to serve our customers more effectively, as we produce our new lightweight products with state-of-the-art equipment and leading edge technology there,” said Norio Takami, president and CEO of Hayashi Telempu North America Corp.
Another Japanese company, Kobe Aluminum Automotive Products, broke ground in May 2013 on an 87,000-sq.-ft. addition to its manufacturing plant in Bowling Green, representing $66 million of new capital investment and the addition of 100 new full-time employees.
The expansion makes room for new furnaces and casting machines, forging presses and advanced processes used to meet increasing demand for components to aluminum automotive suspension systems.
“Kobe had many options when we decided to establish this business in Bowling Green. We have had great experiences working in Kentucky, and we have never regretted our decision,” said Susumu Koike, president/CEO.
Mitsui Kinzoku Catalysts America Inc., a subsidiary of Mitsui Mining & Smelting Co. Ltd., announced in August 2013 that it would establish manufacturing operations in an existing building in Frankfort.
The company, which makes catalytic converters for automobiles and motorcycles, anticipates creating 50 new, full-time jobs and investing $19.5 million in the Commonwealth. It hopes to begin operations by July 2015.