In January 2016, Matthew Early, vice president for campus services at Emory University in Atlanta, faced a challenge. Like many building owners, Emory had selected a great architect and engineer to design a new 110,000-sq.-ft. (10,220-sq.-m.) Campus Life Center (CLC). However, there was no way to understand if the design decisions being made also made sense from the perspectives of cost and energy.
With a fixed budget to work with, first costs were rising as the design team labored to meet the aggressive energy targets of the university. Matthew was checking his LinkedIn feed one morning and came across the cove.tool software for optimizing cost vs. energy consumption in buildings, and he called Pattern r+d CEO Sandeep Ahuja right away. “This is the most revolutionary idea I have seen in a while. How soon can you run an analysis on our building?” he asked Sandeep.
Within a couple of hours of getting pricing of various building components and assemblies from Holder Construction, the ownership team was able to interactively visualize hundreds of energy simulations, run in the cloud, to find the lowest cost and highest performance bundles of wall and roof assemblies, HVAC systems, glass types, daylight controls and more. The cove.tool process used on the Emory CLC is now standard practice on the campus.
Recognizing the urgency of reducing consumption and anticipating code updates, many owners like Matthew Early are aggressively seeking to deliver high-performance buildings for both new and existing improvement projects. However, consistent project delivery is a challenge for building owners. Teams vary from project to project and the unequal experience of these teams leads to missed opportunities for lower consumption along with higher construction and operating costs.
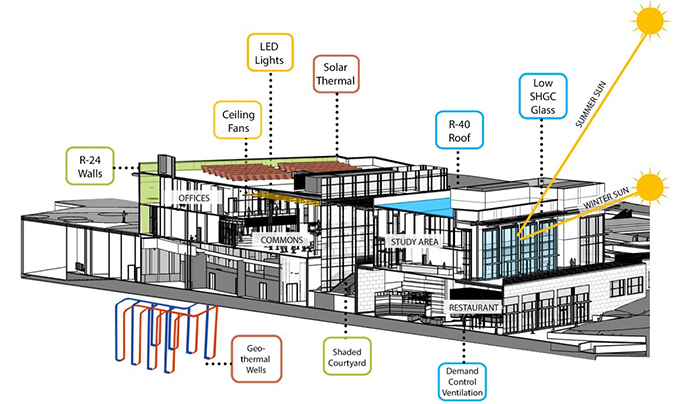
Adopting a tool such as cove.tool that allows owners to independently evaluate decisions with an automated energy modeling software is key to avoid massive cost increases.
Out of the five key metrics of energy, daylight, glare, thermal comfort, and cost, only energy was being evaluated for Emory. While energy consumption is a vital metric, focusing only on energy leaves out the enormous effects daylight has on productivity and comfort. On the other hand, too much daylight creates damaging glare. Thermally comfortable spaces increase productivity and comfort by allowing people to work faster and have fewer health problems. Underpinning all of these metrics is cost. Without evaluating the cost impacts, decision-making tends to favor “what we did last time,” driving costs up since millions of combinations are not being examined.
Strategies for Meeting Targets
To change the way buildings are designed, decision-makers should focus design teams on varying shading, glazing, orientation, and building schedules and measuring the outcomes in terms of energy, daylight, glare, thermal comfort and cost. Shading systems should focus on solutions that maximize views and reduce cost through the use of frit glass and horizontal projections and overhangs. Glazing decisions should be focused on varying glass types by orientation, using the most expensive glass only where it is needed.
However, the largest impact on building performance is the schedules used to control everything from lights to HVAC to plug-loads. This alone can potentially lead to a 25-percent reduction in energy consumption.
Lighting loads should also be minimized by the lighting consultant. Heating and cooling loads should be determined based on actual occupant loads and avoid standard engineering practice of using area weighted occupant loads. Emory used simulations to track where the major energy loads came from to make rational decisions based on performance.
Changing the Design Process
In a design process with these strategies and metrics, the traditional architect-to-engineer relationship does not work. Architects cannot take owner feedback, create a design, throw it “over the wall” to the engineers, and hope for a positive outcome.
Instead, during programming and feasibility studies, the owner must use conceptual energy modeling as a means of setting benchmarks for design process. Using tools such as cove.tool, ownership can take the required program area, input the rough size of such a building and determine an energy use intensity (EUI) to put into the request for proposals.
This EUI should be compared with other buildings of its type to determine a realistic benchmark upon which all other decisions are made. Combined with historically accurate cost numbers, the cost-vs.-energy optimization should be run to determine a realistic budget. These two numbers can guide the rest of the programming and feasibility studies so that capital improvement budgets have realistic expectations.
Once a project team is awarded the design contract, ownership should track progress along the way by requiring that each presentation also have a corresponding energy and cost performance comparison to the benchmark. Detailed energy models require weeks to be set up, and cannot provide feedback as fast as the architects need it to affect their decision-making process. Between detailed energy models, design teams should run their designs through a tool such as cove.tool to ensure that designs are reflective of ownership goals. In this way, there is never a disconnect between design and project goals. Energy and cost should be graphed, allowing everyone to quickly understand the impacts of decisions that push outside of targets.
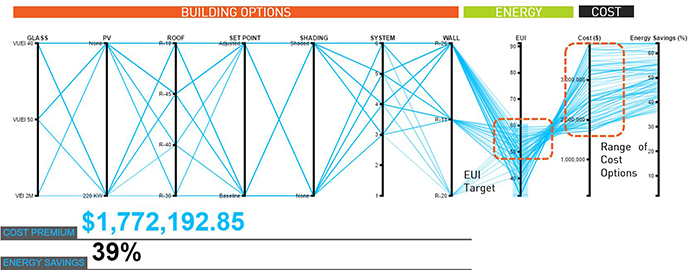
During the design development stage, a tool such as cove.tool should be used to refine material selections by working closely with cost estimators to provide the most up-to-date cost. Multiple glass types, insulation thicknesses, controls, schedules, and any other decisions that impact energy consumption should be run through the optimizer to ensure that cost and energy discipline is maintained.
Decisions made using a tool such as cove.tool can be fed into the detailed energy simulation of the engineering team. In the construction documentation phase, ownership should rely on the engineer’s detailed simulation and watch out for changes that can affect consumption, such as an overzealous lighting package or equipment substitutions. Before construction begins, everyone should ensure that the detailed energy simulation is up to date and graphed to make sure that the benchmarks have been maintained. During construction, ownership and the design team should watch out for substitutions or omissions that will adversely affect the project goals. Where possible, ownership should conduct post-occupancy studies to understand how construction quality differs from design specification, in order to learn lessons for future projects.
Patrick Chopson is COO at Pattern r+d, an Atlanta-based architecture and sustainability consultancy focused on using advanced analysis tools and methods to design for building energy, daylighting, and thermal comfort performance.