Policies, migration and infrastructure create the perfect storm for manufacturing growth.
Florida’s manufacturing resurgence coincides with policy changes, demographic trends and infrastructure investments that are turning the Sunshine State into a production power.
Data from the U.S. Census Bureau and the Florida Department of Commerce show the manufacturing sector across the state surging since 2019, with employment in production rising by 10% between 2019 and 2023. That equates to 36,000 new manufacturing jobs statewide, pushing Florida’s total production workforce to 420,942 in 2023 and propelling the state into the top 10 nationally in manufacturing jobs.
With a national manufacturing recovery being somewhat uneven around the country, Florida is one of just five states that together accounted for two-thirds of total manufacturing job growth nationwide.
Experts interviewed for this article say that notable tax policy changes, demographic migration patterns and the sheer growth of the state are the biggest factors driving Florida’s manufacturing renaissance.
As more people — particularly younger workers and families — move to Florida, two things happen: The swelling population generates more demand for products; and the size of the available workforce continues to grow.
Census counts show that from 2010 to 2025, Florida’s population is projected to grow from 18.8 million to 23.3 million. That equals 4.5 million new residents. While Florida’s growth in 2024 slowed to 1.5%, the state population increased by 8.5% from 2020 to 2024.
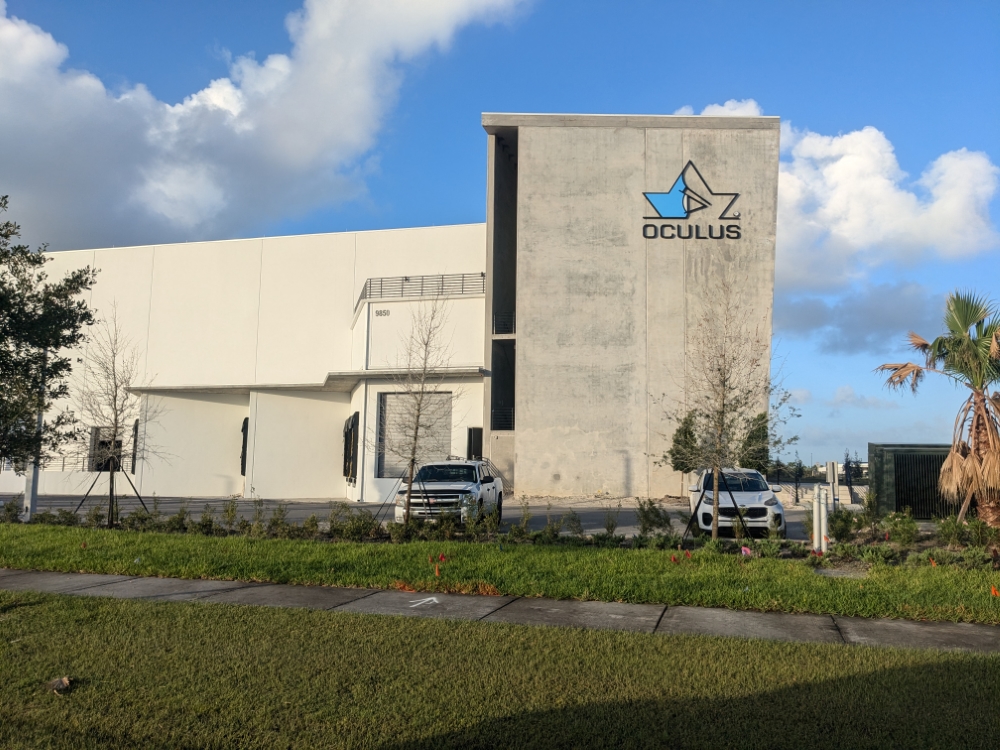
Medical device manufacturer Oculus Surgical Inc. recently moved into its new 75,000-sq.-ft. plant in Port St. Lucie.
Image courtesy of Oculus
The state’s new population is also getting younger, meaning it is more mobile and more likely to adapt to the kind of advanced manufacturing jobs now in high demand in multiple industry sectors. For example, in Leon County around Tallahassee, the median age is now just 31.4 years. In Alachua County (Gainesville), it is 31.7 years. While these are both university towns (home to Florida State University and the University of Florida), they are not the only cities getting younger. In Hendry County, the median age is now 35.1; in Hardee County it is 35.2; and in Orange County (Orlando), it is now 35.9.
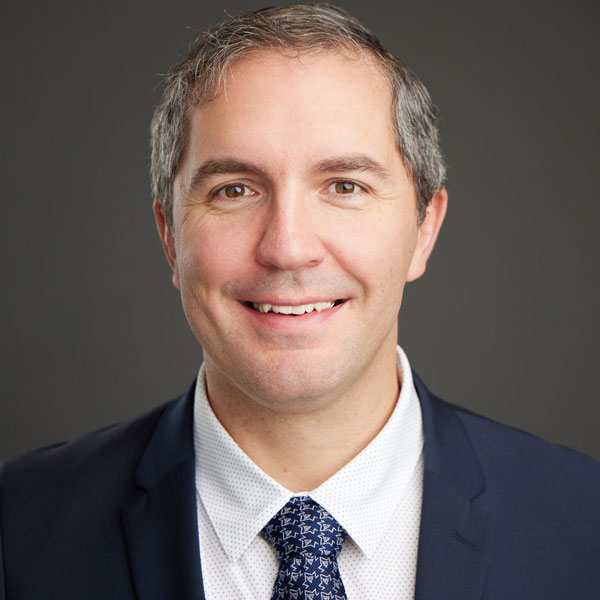
“The employees were the driving factor.”
— Michael Ansorge, CEO, Oculus Surgical Inc., on why his firm chose Port St. Lucie
Combined with policy changes aimed at benefiting employers who produce goods, Florida has created the perfect storm for manufacturing growth. From 2014 to 2022, Florida’s manufacturing output increased from $43.5 billion to $73 billion. That is a growth rate of 67.8%. During that same 8-year period, manufacturing employment in the state rose 23.3%. As a result, Florida today ranks as the 10th largest state for manufacturing jobs.
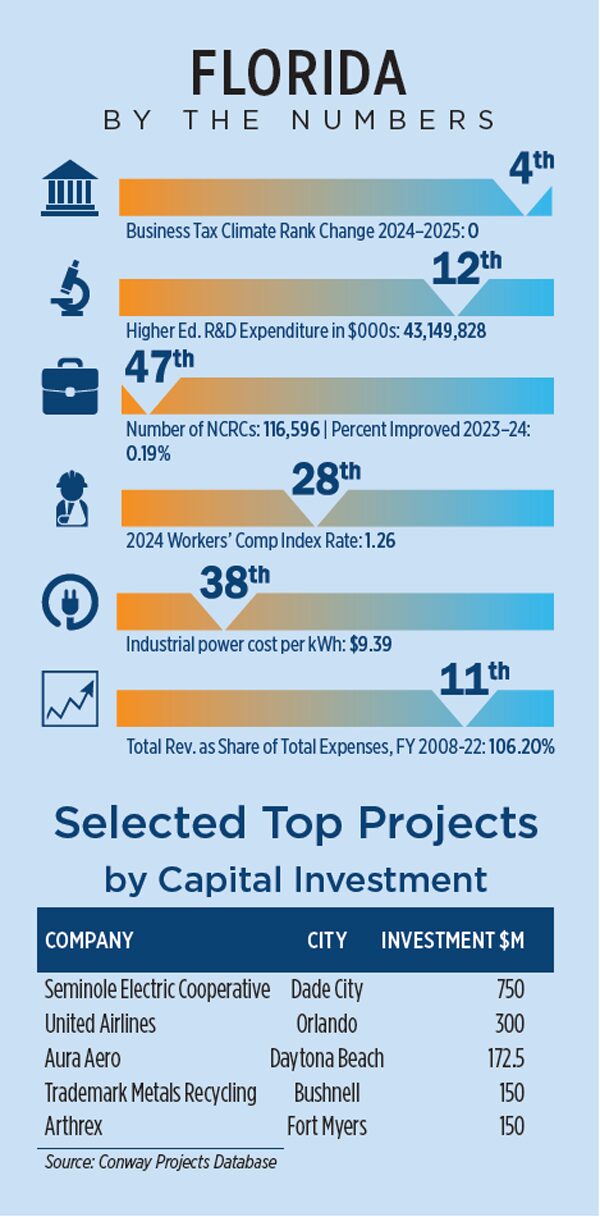
I-4 Corridor Leads the Boom
The biggest growth is occurring along the Interstate 4 Corridor in Central Florida, stretching from Tampa-St. Petersburg-Clearwater on the Gulf Coast to Palm Bay-Melbourne-Titusville on the Space Coast. Gross domestic product for manufacturing along this corridor mushroomed to $17 billion in 2023 — a 93% increase from 2014.
One industry growing rapidly is aerospace and defense. In Tampa, CAE Defense & Security recently celebrated the opening of a new U.S. headquarters. The 326,000-sq.-ft. project on Tampa International Airport property creates space for 750 employees. A Canadian manufacturer of simulation and modeling technologies and training services for aerospace and defense customers, CAE was founded in 1947 and today maintains operations and training centers in 35 countries.
Susan Gehrig, vice president of operations for CAE in Tampa, says her firm likes this location because “it is a big thing for us to be near our customers in the Tampa Bay Area. Our closest neighbor is MacDill Air Force Base. They have been a customer for a long time. We develop and produce high-tech solutions for complex missions across the world. This Tampa location permits us to do that. We want to make sure that America’s warfighters are mission-ready and safe.”
She adds that the Tampa Bay Area provides CAE access to a highly skilled workforce, nearby colleges and universities that partner with the company, a low cost of living compared to other well-known defense clusters in the country, and an enviable quality of life with year-round sunshine.
Building the new complex at TIA allows CAE to add about 100 new employees to its workforce. “It also gives us the capacity to grow,” Gehrig notes. “Our footprint here is wonderful. People want to move here.”
‘Employees Were Driving Factor’
CAE is not alone. Around Florida, manufacturers in a variety of sectors are expanding. On the Atlantic Coast in Port St. Lucie, Oculus Surgical Inc. just moved into a brand-new facility of 75,000 sq. ft. in the Tradition. A global leader in the medical device industry, Oculus invested $30 million into this new plant that will enable the firm to grow its headcount from 44 to 79 over a 3-year period.
“The employees were the driving factor” behind the site selection,” says Michael Ansorge, CEO of Oculus, whose parent company in Germany was founded 1895. “We were already based here, and we wanted to keep everyone we had on staff. We use this location as a hub for a lot of our Americas operations — from Alaska and Canada down to Panama and Brazil. We have access to the Port of Miami to our south. It is a good hub for container shipments.”
Since Oculus does business globally, Ansorge says it helps to have a location that is accessible and welcoming for visiting customers. “This location is phenomenal,” he says. “We get a lot of visitors domestically and globally. Most of our international visitors are able to get direct flights to either Orlando or Miami, and we are equidistant to those cities. That was a big factor.”
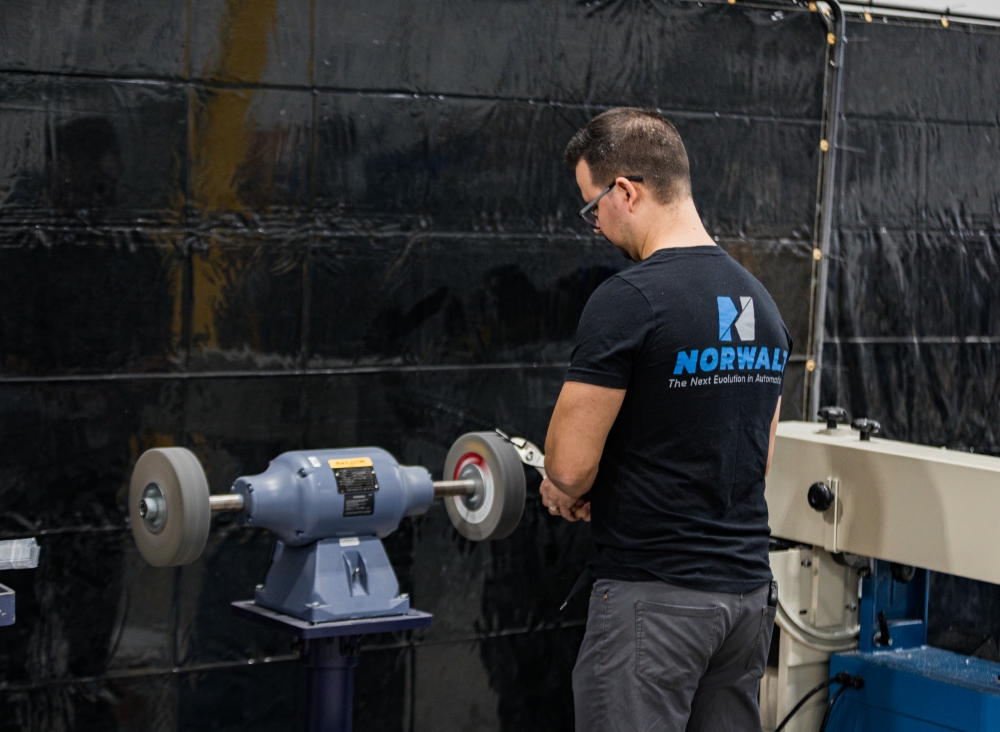
Less than two years after opening a new plant in Tampa, Norwalt — a specialist manufacturer of custom-built automation — added 28,000 sq. ft. of new space to the operation.
Image courtesy of Norwalt
He adds that “the cost of land was good, and we can access the labor we need very easily. People come to work here, and they don’t want to leave. Some of our workers have been with us for 25 years. We also participate in several manufacturing organizations like the Treasure Coast Manufacturing Association and Florida Makes. They support this region very well. They are great neighbors, and we work together very well.”
A Decade in the Making
Leslie Boyd, managing principal of industry for CLA Indianapolis, a consulting firm that advises companies on tax incentives and location issues, says, “What you are seeing in Florida has all been done in the past 10 years.”
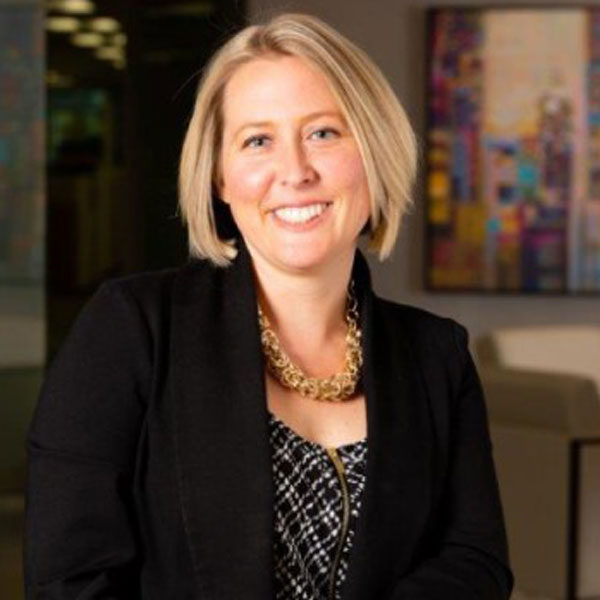
“They have created an environment
conducive to creating a manufacturing workforce.”— Leslie Boyd, Managing Principal of Industry,
CLA Indianapolis
When I asked Boyd what makes Florida a good state for manufacturing, she said, “They have made a lot of intentional moves to do that with their highway and transportation network. They are the top marine manufacturer in the country. They are very strong in high-tech manufacturing. They have invested a lot in higher education and secondary education in manufacturing. They have created an environment conducive to creating a manufacturing workforce. And they have a lot of land in rural areas where there is an opportunity to invest. A lot of people are moving to Florida due to the state’s favorable tax rates. In short, they have done a lot of things well.”
Case in point, says Boyd, is the fact that Florida created a new position called Chief Manufacturing Officer. “Other states have better incentives, but Florida has been smart about its efforts,” she says. “With it getting harder to secure housing and property insurance in coastal areas, we are seeing growth in people moving to inland and more rural Florida communities. You can have a great life if you move to these inland areas.”
A recent report by WalletHub bolsters Boyd’s assessment. According to WalletHub, Florida residents now have the sixth least total tax burden in the country; and the return on investment they receive from the taxes they do pay is second best in the U.S.
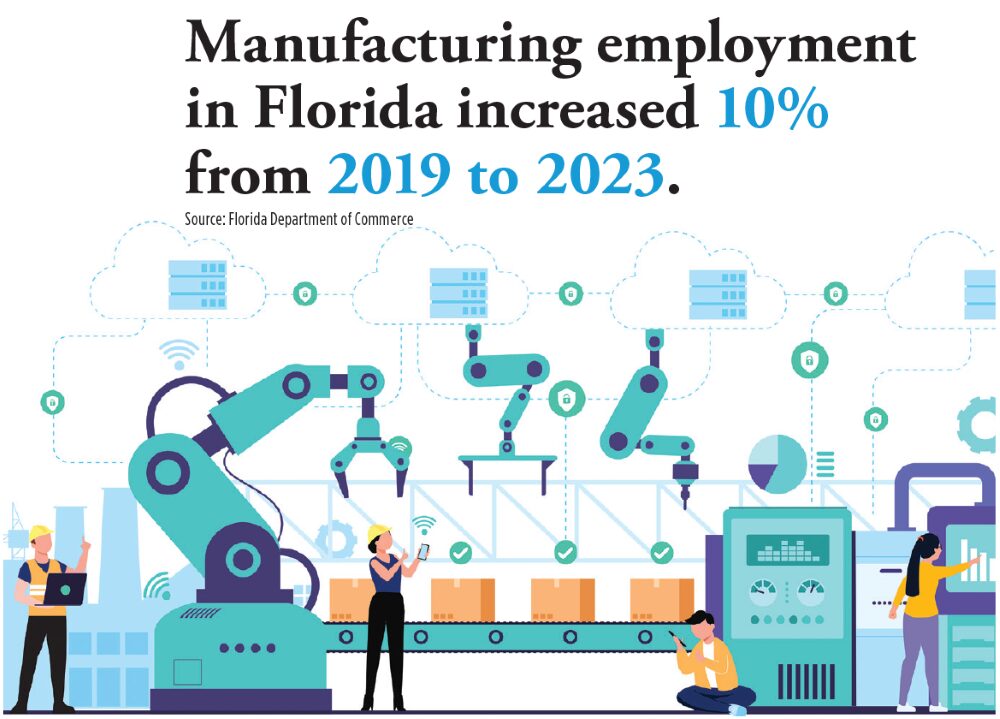
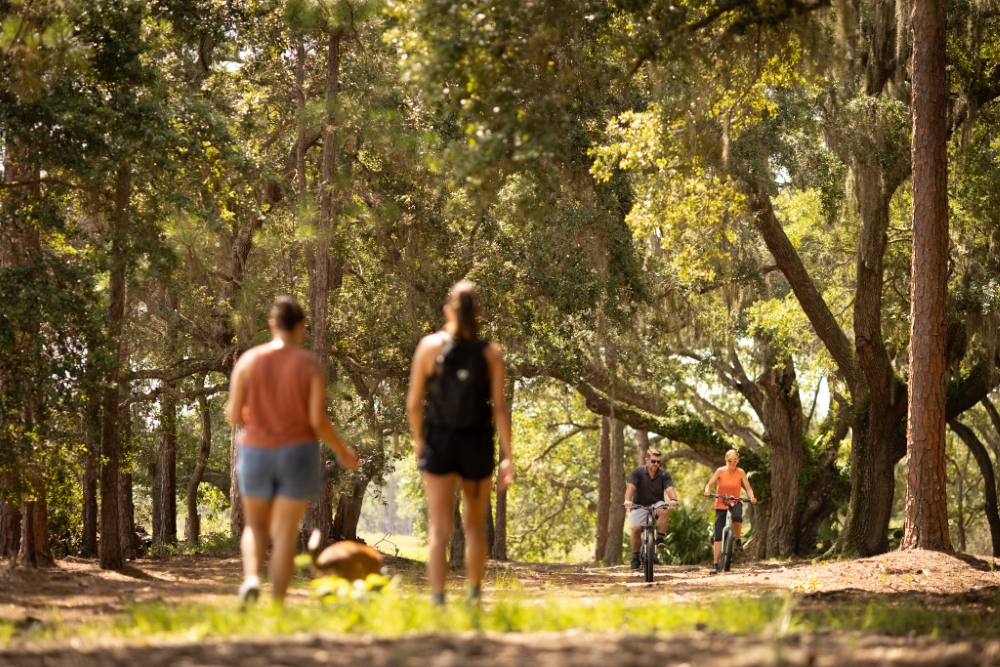
Sunbridge, a master-planned community of more than 27,000 acres southeast of Orlando, will soon be home to large industrial facilities for Blue Origin and TJ Maxx.
Image courtesy of Tavistock Development Co.
A New City Rises South of Orlando
Over the past 30 years, Florida has given birth to some of the largest and most impactful master-planned communities in the country: The Villages, Celebration, Lakewood Ranch, Trinity, Babcock Ranch, Viera, Wellen Park, FishHawk Ranch, Lake Nona, Seaside, Watercolor and Ave Maria — just to name a few.
Thanks to Tavistock Development Company, creator of Lake Nona, you can add another large-scale, mixed-use development to that mix: Sunbridge in southeast Orlando.
At 27,447 acres, Sunbridge will be comparable to Lakewood Ranch in Manatee and Sarasota counties on the Gulf Coast and will be the largest master-planned development of its kind in Central Florida. And while a massive Del Webb community of private homes will anchor the development, industrial end-users are already lining up to sign big deals.
Jeff Bezos’ space company Blue Origin and department store retailer TJ Maxx have both signed agreements to build and occupy giant industrial facilities in the Sunbridge Business Park just off State Road 528. TJ Maxx closed late last year on the purchase of 186.5 acres at the northwest corner of Innovation Way and the Beachline Expressway for $45.4 million. The company plans to build a 1.93-million-sq.-ft. warehouse on site. Blue Origin signed a 220,853-sq.-ft. lease in the Venture Park Beachline complex at S.R. 528 earlier in 2024.
Many other industrial investors are showing interest. Sunbridge is unprecedented in Central Florida. Upon buildout, Tavistock plans to deliver 5,720 single-family homes, 1,650 apartments, 5.47 million sq. ft. of office space, 2.9 million sq. ft. of industrial space, 880,000 sq. ft. of retail space and 490 hotel rooms on the 8,000 acres of land in Sunbridge within Orange County.
The Osceola County portion of Sunbridge is even bigger. At nearly 20,000 acres, it will have another 29,320 homes; 8.54 million sq. ft. of commercial, office and industrial space; around 2 million sq. ft. of institutional or civic space; and 5,000 hotel rooms.
Skipper Peek, senior vice president with Tavistock Development in Orlando, said the proximity to Orlando and the Space Coast make sites in Sunbridge Business Park attractive. “That was a major factor in the Blue Origin decision,” he says. “When you look at the proximity to Orlando with its major employment base and being just 15 minutes from Orlando International Airport, this location made a lot of sense for both companies.”
Peek says the success of Lake Nona on the south side of Orlando opened the door for Tavistock to develop Sunbridge in the southeast quadrant of America’s top tourist destination. “There were no roads here, but as infrastructure accesses more land, the growth follows,” he says. “Tavistock poured a lot of resources into it.”
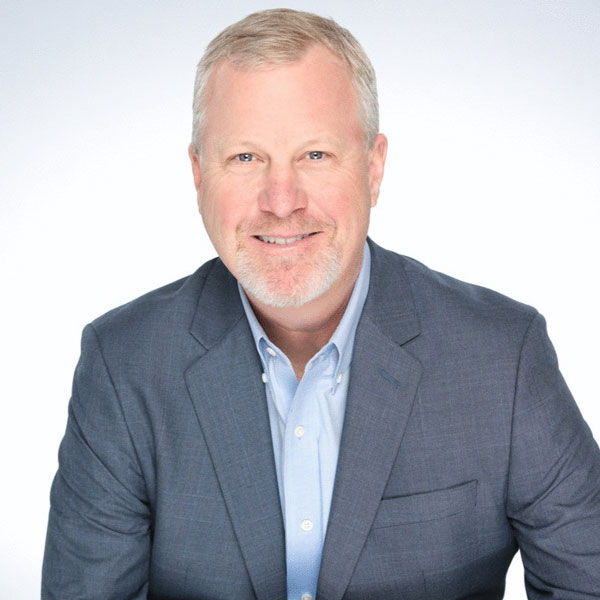
“Our goal with Sunbridge is simple: If you can get immersed in nature and still get to the airport in 15 minutes, we will have created something very special.”
— Clint Beaty, Senior Vice President of Operations, Tavistock Development Company
Clint Beaty, senior vice president of operations for Tavistock, says Sunbridge is part of the 300,000-acre Deseret Ranch owned by the Church of Jesus Christ of Latter-Day Saints. “They are long-term thinkers,” he says. “Tavistock’s role is that we are doing finished-lot development for large public builders. Some of the entitlements are denser than downtown Orlando. It will take decades to get to that full entitlement.”
Beaty says the entire community, including the business park, is designed to blend in with the surrounding natural environment and focus on wellness and sustainability. Much of the property in Sunbridge falls within the headwaters of the Kissimmee River Basin that ultimately flows into Lake Okeechobee and the Florida Everglades.
“Water is the new liquid gold in the state,” says Beaty. “The average citizen does not understand that. A very native Florida plant mix is here. In collaboration with strategic partners like the University of Florida and The Nature Conservancy, we developed a no-turn compost production material for use in Sunbridge. It holds about six times its weight in water. This product creates a healthy soil environment and reduces the need for irrigation while reducing runoff. Using this material, there will be a 40% to 60% reduction in normal irrigation use in the residential areas of Sunbridge.”
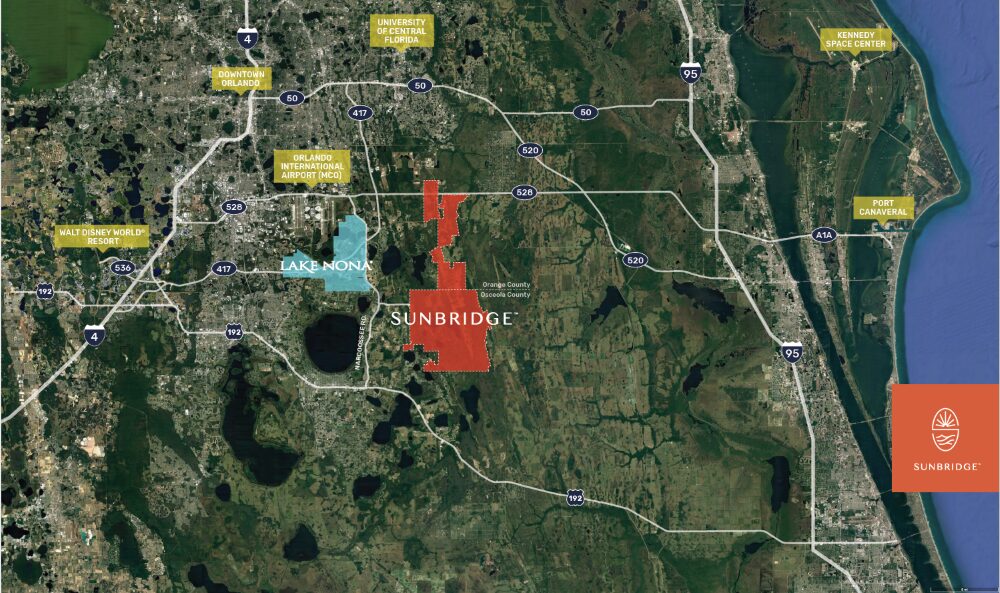
Sunbridge Business Park has already secured major leases from Blue Origin and TJ Maxx.
Photos courtesy of Tavistock Development Co.
Industrial occupants will adhere to these same standards, Beaty says. “We are coming at this from a scientific research basis,” he adds. “We are creating the ethos, culture and education to preserve this natural part of Florida over the coming decades. Our goal with Sunbridge is simple: If you can get immersed in nature and still get to the airport in 15 minutes, we will have created something very special.”
Sunbridge at a glance:
- Location: Southeast Orlando in Orange County and Osceola County
- Size: 27,4447 acres
- 30,000 residences
- 5,000 hotel rooms
- 5.5 MSF of office space
- 2.9 MSF of industrial space
- 15 minutes from Orlando International Airport
Source: Tavistock Development