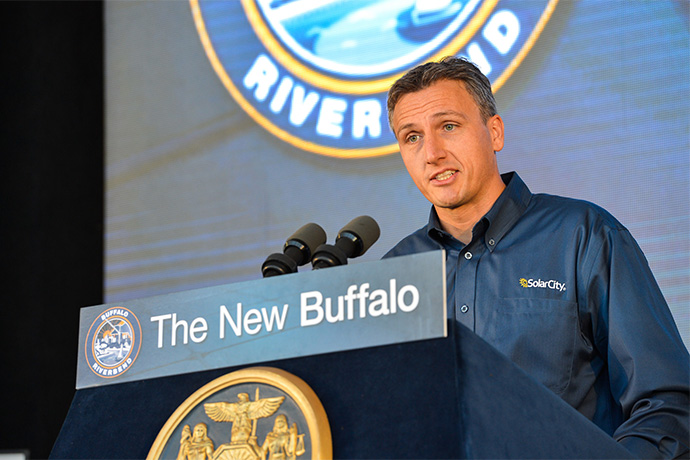
The Tesla Gigafactory plan for battery production in western Nevada got all the attention this summer. But there’s another billion-dollar gigafactory in the works in western New York from yet another Elon Musk-affiliated company.
California-based SolarCity, co-founded by CEO Lyndon Rive and his brother Peter and chaired by their cousin Musk, marked the beginning of fall in September with a groundbreaking at the former Republic Steel manufacturing site in South Buffalo for what will eventually be the largest solar panel manufacturing complex in the Western Hemisphere. The SolarCity GigaFactory will have annual capacity of 1 gigawatt at full production, and will create more than 3,000 jobs in the region and 5,000 jobs statewide.
“This is bigger than anything we could have imagined,” said New York Gov. Andrew Cuomo at the groundbreaking. “It is the perfect metaphor for Buffalo, where the fundamental strength was the available hydropower. That hydropower now, that renewable energy now, will fuel the renewable energy industry for the future. I am incredibly proud that the state is playing a role in this project, because Buffalo’s future is New York’s future, and today that future is brighter than ever.”
The project quintuples the output and economic impact of the originally planned project from silicon solar cell and module maker Silevo, announced in November 2013 along with a facility from LED manufacturer Soraa. SolarCity in June announced it would acquire Silevo.
“This acquisition will redefine SolarCity’s path, from installer and service-company to a vertically integrated total solution provider,” said Frost & Sullivan Visionary Innovation Consultant Pramod Dibble of the $200-million deal. “The market faces oversupply from fairly low-efficiency panels, but introducing a clearly superior technology option, from the market leader in residential solar, may just be the disruption needed to rock the landscape.”
Dibble was speaking metaphorically, but the Buffalo landscape will be rocked concretely. The SolarCity GigaFactory will be located at the Buffalo High-Tech Manufacturing Innovation Hub at RiverBend, a new START-UP NY site owned by the State University of New York’s College of Nanoscale Science and Engineering. SolarCity, the nation’s largest solar power provider, will spend $5 billion over the next decade in connection with the creation and operation of the facility in New York, and New York State will invest a total of $750 million through the Buffalo Billion and other state resources to establish infrastructure, construct the 1.2-million-sq.-ft. facility and purchase required equipment.
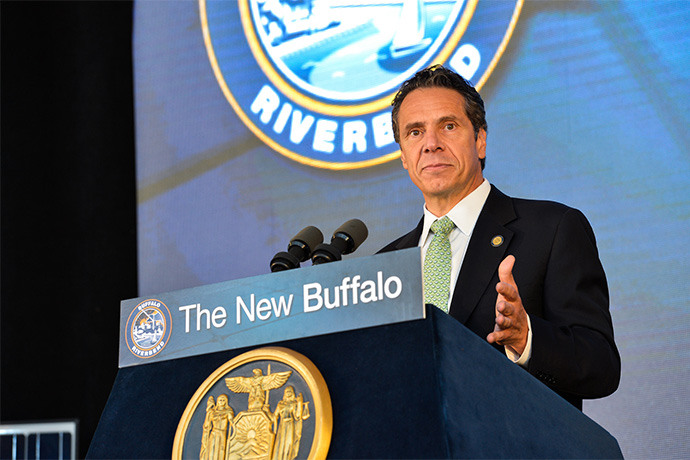
The project’s development is led by LP Ciminelli as Construction Management along with: EYP, Project Architect; CHA, Civil Engineer; and M+W Group, Mechanical Engineer. The factory is scheduled to be online and in high-volume manufacturing as early as the first quarter of 2016.
Chain of Events
SolarCity’s primary business has been the design and installation of solar power systems — some of them slated to eventually employ batteries from the Nevada Tesla Gigafactory. Founded in 2006, the company’s payroll has grown since then from its two co-founders to about 7,500 employees. The company serves customers in 15 states with over 45 operations centers, and says it signs a new customer every three minutes. In addition to thousands of homeowners, government agencies and schools, its list of customers also includes eBay, HP, Intel, Walgreens and Walmart.
The company’s operations centers continue to pop up like daisies in the sun, with locations established this year alone in Arizona, California, Delaware, Maryland, Massachusetts, Nevada and New York expected to create more than 600 new jobs. The Nevada operation in August surpassed 640 employees, with more than 1,500 local customers signed up. The firm most recent earnings release says it “passed the 140,000-customer mark in June 2014 — with more than 30,000 customers added in the second quarter alone — an increase of 218 percent over the year ago quarter.”
Christopher Beitel, executive vice president of global operations and planning at Silevo, previously served as GM and managing director for the Thin Film Solar Business Group at Applied Materials. In an interview from the firm’s HQ in Fremont, in Silicon Valley, he says Silevo’s first site selection occurred four years ago, when a pilot plant of about 32 MW in capacity was ultimately established in Huangzhou, China, a coastal town where the company’s founder Zheng Xu grew up and where attractive subsidies were offered.
“We ramped up our first factory there from 2011 to 2013, and in 2013 we successfully transferred our technology,” says Beitel. “Yields and outputs were good, and it was time to scale our operation to meet customer demand and lower our cost structure — with bigger factories you can see a 30- to 40-percent reduction in terms of economies of scale, labor and equipment costs.”
The goal was to multiply output by six times for the big plant, to 200 MW of annual capacity. The Silevo team considered building out in Huangzhou, Beitel and the company founders had learned from working with companies such as Intel the value of developing technologies at geographically dispersed nodes. And through some detailed analysis of inputs, he says, “You could quickly understand manufacturing in North America and the US could be cost-competitive” for the larger-scale plant, as costs are amortized and head count per megawatt is reduced.
Beitel, along with Silevo’s CFO, led the site selection process last summer by engaging with large architecture and engineering firms such as CH2M Hill, evaluating costs for skilled labor and utilities (including water), as well as available facilities, incentives and quality of life. The team initially examined Arizona, where the talent was available at a lower cost than Silicon Valley, and power was six cents per kilowatt-hour (kWh), compared to 10 or 11 cents per kWh in California. New Mexico, Oregon, Texas, Tennessee, Missouri and New York were also in the mix after the first round of analysis by CH2M Hill and M+W Group.
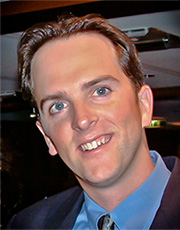
Silevo next engaged with boutique consultancy Clark Street Associates to engage with economic developers. As the team evaluated greenfield vs. brownfield and looked at potential retrofit opportunities, the field was narrowed eventually to three finalists: New Mexico, Arizona and New York.
“When we met with the individuals with the State of New York economic development team [Empire State Development], several things were very attractive to us,” says Beitel. “In western New York, skilled labor talent is good. There’s the SUNY network, and University at Buffalo is a top engineering school. Buffalo is also somewhat of a depressed region in terms of industry, and labor rates are lower, so we could get skilled talent, but not necessarily the highest- priced talent. And being within 35 miles of Niagara Falls, they have access to hydropower, which is very attractive in terms of cents per kilowatt-hour, at four to five cents. With additional negotiation and potential assistance from the state, you can’t find a location with lower cost electricity.”
Also helping New York’s case was the longtime effort headed by Dr. Alain Kaloyeros, CEO and Officer in Charge of SUNY Polytechnic Institute, who for years has led the buildup of semiconductor industry R&D and talent, mostly in the eastern half of the state, and a few years ago transferred that approach to the solar sector via CNSE, the SUNY Colleges of Nanoscale Science and Engineering. The state investment at RiverBend will replicate the model created in Albany at CNSE, in which rather than giving money directly to private companies, the state invests in core infrastructure and equipment and uses that equipment as the incentive to attract companies to establish themselves in these new high-tech facilities.
Peter Cammarata, president of the Buffalo Urban Development Corp., and David Stebbins, vice president, have been heading the city’s brownfield redevelopment efforts for many years, and worked with the Republic Steel site since the city acquired it. Cammarata says he first met Kaloyeros in spring 2013, after the state had called and said they wanted to send some people to look at the city’s redevelopment sites. Cammarata says Kaloyeros first stopped at BUDC’s first successful park redevelopment, Lakeside Commerce Park.
“He got out of the car, spent a minute or two, and all he said was that there was not enough acreage,” recounts Cammarata. “So I took them over to South Park Avenue [the Republic Steel site], he got out of the car, looked at this broad expanse of 90 acres of flat land where the main Republic Steel plant was, said ‘This is it,’ and got back in the car and left.”
That is what visionaries tend to do.
“This is a crowning achievement for Governor Cuomo’s Buffalo Billion initiative and his strategic vision to bolster New York’s burgeoning high-tech economy,” said Kaloyeros in September. “Under the governor’s leadership, the nanotechnology boom that began at CNSE in Albany has now spread clear across the state, creating tens of thousands of jobs and billions of dollars in investments.”
Governor Cuomo announced in July that a purchase agreement had been reached between New York State and the City of Buffalo for the purchase of the remaining developable 96 acres of City-owned property at the RiverBend location. The newly acquired property is in addition to the 88 acres that the State had purchased from the City at the site in May. The state paid a collective $4.8 million for the two parcels. The city paid $4.6 million when it acquired the property in 2008. The agreement was made from the City of Buffalo via the Buffalo Urban Development Corporation to the Fort Schuyler Management Corporation, a not-for-profit entity created by SUNY to manage property transactions on behalf of the College of Nanoscale Science and Engineering.
Scale and Reach
Stebbins says the RiverBend plan was slated to follow the successful example of the Buffalo Lakeside Commerce Park, which has attracted facility investments from several employers including Certainteed.
“We thought this site would follow the same path,” says Stebbins, perhaps for small-scale startup manufacturing related to downtown Buffalo’s expanding medical campus. “But we never expected such a big project to come in and essentially take the whole property. Fortunately we had the land available.”
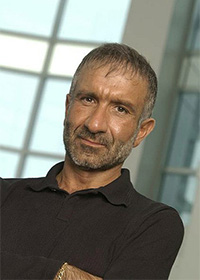
An abundance of water, and “a really good logistics network” furthered the case for Buffalo. In addition to rail and road shipping for North America, says Beitel, proximity to Lake Erie and the canal was a plus for eventual export to the EU and China. Among the other assets at the RiverBend site: a 115-kv line, a 170-million-gallons-per-day water intake, and a rail corridor that includes Norfolk Southern and CSX tracks, as well as trackage rights from Canadian National, Canadian Pacific and shortline operator Genesee & Wyoming.
Beitel says Silevo panels — which weigh about 45 pounds apiece and are currently shipped from China in high-cube containers — cost about four to five cents per watt to ship to the US. Salaries may be higher in the US, he says, “but the magnitude is negated when you factor in logistics costs. Factor in efficiencies, water and power costs, and even though China salaries are probably one-fifth of those in the US, you have quite a bit of efficiency in the US, and you don’t need to hire as many heads. Labor is probably 2x in the US. It’s one of the reasons we believe setting up scaled operations in the US is a good strategy, and will lead to innovation leadership.”
Last but not least, Beitel says, the New York team was “very aggressive in terms of their incentive package.”
Silevo was on track after that Nov. 2013 project announcement, when SolarCity and everyone’s favorite visionary Musk came into the picture. After the decision was made to sell, Beitel says, discussions to expand the scope of the project ensued. And the ambition was as aggressive as the incentive package.
“We decided to use the same location, but scale it to 5x,” says Beitel. Asked to clarify the math from the original 32-MW plant in China, he explains the multiple has now reached 30: “It was already 6x on paper, and now it’s 5x from that — so a huge amount of scale.”
Asked if there are any parallels or cross-discussions between Musk’s two gigafactories, Beitel says, “We shared learnings in terms of Tesla and SolarCity, but it was not a deliberate strategy. Elon has taken some heat in the press as ‘Mr. Subsidy,’ but I don’t think that’s a fair characterization. He is the chairman of the board, and does not get involved in day-to-day operations.”
Soraa Loser?
Shuji Nakamura, the scientist and UC Santa Barbara professor who discovered the LED lighting technology behind fellow new Buffalo high-tech arrival Soraa, this week earned the Nobel Prize in Physics. But even that highest of laurels won’t help Soraa solve its real estate conundrum, as SolarCity’s 30-fold expansion plan overtakes most of RiverBend’s first phase and apparently leaves Soraa temporarily out in the cold.
“At this point, Soraa is working with New York State to find a suitable solution,” says Soraa spokesman Andy Beck. Soraa’s only plant happens to be in the same place Silevo’s HQ has been located: Fremont, Calif.
Meanwhile, there’s a sense that SolarCity’s just getting started. Beitel confirms the hunch.
![soraa-nakamura23[3][1][1][1] soraa-nakamura23[3][1][1][1]](https://siteselection.com/media/onlineInsider/images/soraa-nakamura23-3-1-1-1.jpg)
“Absolutely,” he says, noting Elon Musk’s statements and vision when the Silevo acquisition was announced. “The gigawatt plant is our pilot plant. I have a team evaluating sites that would be even larger. Elon is interested in developing the full ecosystem.”
For instance, the Buffalo plant will need glass, potentially imported from offshore, but the company “would love to partner with US domestic glass companies,” says Beitel. Thinking even bigger, “When you start to look at five to 10 gigawatts at one facility, you can put other components right next to it.”
The 10-GW vision could include, for instance, a float glass line feeding directly into the panel manufacturing plant; aluminum extrusion; polysilicon manufacturing, wafering and ingoting. Beitel says his team is looking at other sites, and engaging with key players and partners to “build potential solar cities.”
The solutions for Soraa and for SolarCity could still easily unfold in Greater Buffalo, which is simultaneously gaining a well-deserved reputation for the trifecta of brownfield redevelopment, historic preservation and downtown rejuvenation.
Stebbins of the BUDC has been doing brownfield work since the early 1980s, “honestly before the term ‘brownfield’ was even invented,” he says. BUDC is in the process right now of acquiring another 50 acres on the city’s upper east side, where about 700,000 sq. ft. of buildings are still standing.
Steve Weathers, president and CEO of the Erie County Industrial Development Agency (ECIDA), took the post last December after working in locations as various as Toledo, Savannah, Tucson and San Diego over the past 20 years in economic development. He says he’s already been impressed by the diversity of blue-collar and white-collar jobs announcements in Buffalo. But when it comes to brownfield redevelopment, “I’ve never seen an area that is so progressive and able to actually get brownfield redevelopment completed, not just talked about. I was having a conversation today —there’s a building built in 1870 that an investor wants to build out for some housing. The federal government and also the state are a big help in providing resources, and good partners.”
Weathers says the pessimist in him might have chalked up the original Buffalo Billion plan from Gov. Cuomo as a campaign promise. But he’s seen evidence of the commitment: “The Buffalo Billion is a reality,” he says. “It’s not just political rhetoric.”
All In
Cammarata of the BUDC says it helps to have such committed developers as Krog Corp. and LPCiminelli, who haven’t shied away from brownfield properties, but used their knowledge of supportive programs and their sheer guts to step up the plate and deliver. Stebbins says the trend is accelerating, in part because of the national realization that cities need to backfill their urban cores, and in part because the State of New York has such a strong program of brownfield tax credits and planning support.
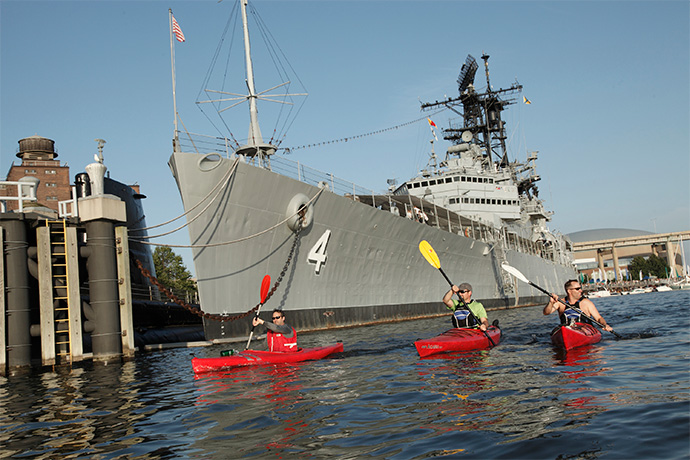
In some cases, the brownfield crowd and Buffalo’s historic preservation crowd align, as with the Larkin District, a 600,000-sq.-ft. Class A office space developed on the site of a seven-story Larkin Co. factory from the early 1900s.
Another historic property is occupied by law firm Hodgson Russ, a practice with 200 lawyers in all, 150 of whom work in Buffalo. Partner Terrence M. Gilbride serves as counsel to LPCiminelli on the development of RiverBend.
“Virtually every major development project in Western New York is using brownfield tax credits right now,” he says. “The state has done a really good job of educating people,” including regular meetings with applicants. “The knowledge level is pretty high. We have a governor and state government that knows it’s all about creation in the right emerging industries. They commit the resources to go at those industries.”
Gilbride is working with the owner of the Buffalo Sabres and — after today — the Buffalo Bills, Terry Pagula, on the $190-million Harbor Center mixed-use development near the waterfront and the terminus of the Erie Canal. The first building, at 650,000 sq. ft., opens in two weeks. The overall complex not only features major retail, but two NHL-quality hockey rinks on the sixth floor, an academy of hockey, and tunnels from a Marriott hotel to First Niagara Center, where the Sabres play. It’s slated to host NHL combines, hockey tournaments and other events. He calls it just another part of the renaissance of Buffalo.
Told that SolarCity CEO Lyndon Rive is, among other talents, a longtime member and supporter of the US National Underwater Hockey Team, Gilbride does a telephone double-take, laughs and says, “I can assure you the hockey being played in Harbor Center is not underwater.”
Nor, it seems, is the fiscal future of his city. Gilbride says he’s never seen the amount of development activity going on now in Buffalo during his 26 years in the profession.
“It’s unprecedented, and they’re all feeding off of each other,” he says, noting a population that’s not only growing for the first time in decades, but growing decidedly younger. “For years for my firm, I have had to convince lawyers this is where they want to come. I wouldn’t say I was being less than honest in other years, because I believed it, but I can say it right now with a conviction I’ve never had before. I’m living it every day, and I believe it.”
From the planet Elon, that’s where. The more important question may be “Where do they go, and what do they do when they get there?” Below is a snapshot comparison of one powerful pair of manufacturing investments this year from companies under Elon Musk’s control.
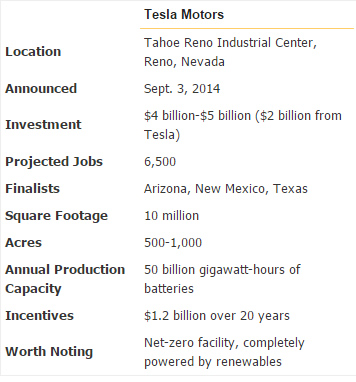
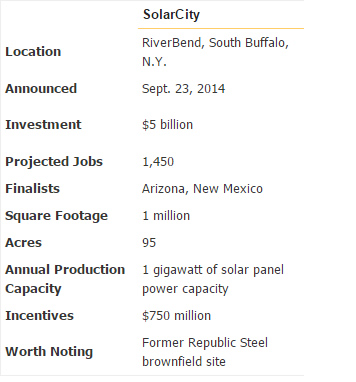