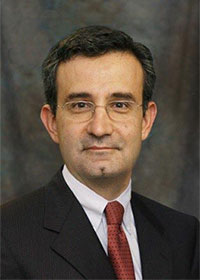
Chinese shirt and yarn company Luthai Textile announced this week it is opening a New York City office. The company, whose 30,000 employees make 20 million shirts a year among other products, realized it needed to be “in country” where more than a third of its business resides … much like many US companies once did in China.
Like many textile firms, Luthai, based in Shandong Province, has its primary manufacturing base in China. But could it one day spin, dye or finish product in a US facility?
Judging from project trends, the answer might be yes.
Site Selection’s New Plant database has tracked nearly 170 textile, clothing and footwear firm facility investment projects in the US since Jan. 2011, led by North Carolina (50 projects), Georgia (27), Tennessee (14), South Carolina (13), Ohio and Alabama (11 each).
Auggie Tantillo, president of the Washington, D.C.-based National Council of Textile Organizations (NCTO), says there has been a rash of “very significant” announcements as 2013 came to a close.
“We calculate it as over $700 million in new plant and equipment announced just since September,” he says. He’s quick to add that companies historically have reinvested in their assets even as employment has dwindled. From 2001 to 2010, he says, the US textile industry invested $16.5 billion in the United States.
The new thread, he says, is foreign direct investment (FDI). And where it’s coming from is what might inspire a double take.
“When a company in China or India, which has enormous advantages in the cost production model either through labor rates or subsidies their government might provide, does the analysis and says it might be better or more cost-effective for us to do this in the United States, that’s saying something,” he says, calling it a sign of “how efficient and capable the US model for production has become.”
It happened in Georgia in October, when India’s Shrivallabh Pittie Group, a leading textile manufacturer in India since 1898, said it will build its first US manufacturing facility at the Screven County Industrial Park near Sylvania, creating 250 jobs and investing $70 million in the area just north of Statesboro in the state’s southeastern quadrant. The plant will manufacture a range of different counts of carded cotton yarn and production will be flexible in order to meet market demand.
Founded in 1898, Shrivallabh Pittie Group is a leading textile manufacturer with substantial presence in the Indian textile sector, operating in 13 locations.
“We are very excited about this project, which is the biggest single investment in the US cotton yarn sector in decades,” said Vinod Pittie, chairman of Shrivallabh Pittie Group. “We believe there is a significant market opportunity for yarn manufacturing in Georgia due to a skilled local work force, proximity to high-quality cotton fiber, the economical supply and reliability of power and world-class infrastructure to international markets.”
“Georgia’s resources for textile manufacturing are best in class,” said Pat Wilson, chief operating officer at the Georgia Department of Economic Development. “Sylvania has been home to textile facilities in the past and offers the Shrivallabh Pittie facility a diverse work force that has experience in textile manufacturing.”
A Legacy Lives On
The announcement was followed a week later by the news that Parkdale Mills, a US company and the country’s largest manufacturer of spun yarn, will expand its production plants in Rabun Gap, Ga., creating 210 new jobs and investing $85 million.
“When a successful Georgia operation like Parkdale Mills decides to expand its facility and its employment roster, it’s a win for all concerned, especially for our work force,” said Gov. Nathan Deal. “The textile industry has deep roots in Georgia and remains a vital part of our manufacturing sector thanks to our strategic location, logistics advantages and the expertise our skilled workers bring to the table.”
Parkdale purchased the 750,000-sq.-ft. (69,675-sq.-m.) Hanesbrands facility in Rabun Gap in 2009 and produces fiber for use in high-end, quality active wear. The company will begin installing equipment in early 2014 and anticipates completion by the end of the year. Using advanced new technology, the Rabun Gap facility will be converted from a 100-percent cotton T-shirt product line to a polyester/cotton blended yarn for the performance wear business — a sector whose growth is on the uptick worldwide.
As if to illustrate the efficiency Tantillo spoke of, the Parkdale facility will stay in operation at all times during the expansion, with one plant running while the other is being renovated. According to the NCTO, the US textile industry has increased productivity by 45 percent over the last 10 years, making textiles one of the top three industries in productivity increases.
“The decision to reinvest in Rabun Gap was easy thanks to the community that has given us a warm welcome and the many state and local organizations that have aided our growth,” said Lee Thomas, vice president of services with Parkdale. “An investment of this magnitude could not take place without their support.”
Founded in 1916, Parkdale Mills has grown from a single mill in North Carolina to a cotton giant, with 25 plants in three different countries: the United States, Colombia and Mexico.
“The economic impact of Parkdale’s commitment to this community cannot be underestimated, both in economic and human terms,” said Greg James, chairman of the Rabun County Commission.
“Georgia has been a nice beneficiary of this reshoring,” says Tantillo. “It’s a very competitive environment now with states and economic development boards, but there is a natural infrastructure in place in the Southeast for the textile industry. It is there because the industry has been there for 170 years.”
That infrastructure was under-utilized for the past 30 years as companies downsized and offshored. Now that the move to return is afoot, says Tantillo, “People say, ‘If we’re going to make yarn, let’s go where they make yarn or weave fabric.’ “
It’s natural to gravitate toward a built-in network and infrastructure like that in the Carolinas and Georgia, he says, “where the chemical and transportation companies and other ancillary players are all familiar with the textile industry, and understand the needs of the industry. If this movement of reshoring textile production has a bigger level of traction than we’ve already seen, I fully expect Georgia, South Carolina and North Carolina to be big winners” and attract 70 to 80 percent of the investment.
Gaining Purchase
Is the domestic natural gas revolution in the US at least partially responsible for the industry’s reshoring? Tantillo says it is. But it’s about more than low cost. It’s about reliability and consistency.
There are other reasons too, beginning with the reason the industry came in the first place: a reliable source of high-quality raw material.
“If you’re a cotton yarn spinner — and a lot of this investment is in yarn spinning — you have the best cotton in the world right here,” he says. “You generally have ample suppliers of it, and of course you have reduced transportation costs if your factory is in the US.”
A third motivating factor is trade policy, he says, as the US has steadily negotiated a series of free trade agreements (FTAs) over the past 25 years, including NAFTA and CAFTA as well as agreements involving Singapore, Morocco, Colombia and Peru.
In the textile sector, he says, “They’ve wisely tied duty-free access to the US market back to where the components of the product come from. Make a shirt in Mexico, and the rule requires that the yarn and fabric must also be made in the NAFTA region.” The looming Trans Pacific Trade Agreement involves 12 countries, including many hot spots for textiles such as Vietnam.
“If your factory is producing yarn in India, that yarn doesn’t qualify for any of these US FTAs,” Tantillo explains. “If you’re making yarn in Georgia, it qualifies for every US FTA. That’s a huge driver.
“It’s not a hard sell for Georgia or North Carolina to convince those textile investors that this is where you ought to be,” he says. But again, it may be hard to believe where some of those investors are coming from. “I do think it’s really striking when you see Chinese and Indian investors, because they have so many government advantages back home. It’s quite an amazing development that they’re actually investing in the United States.”
Ready Assets
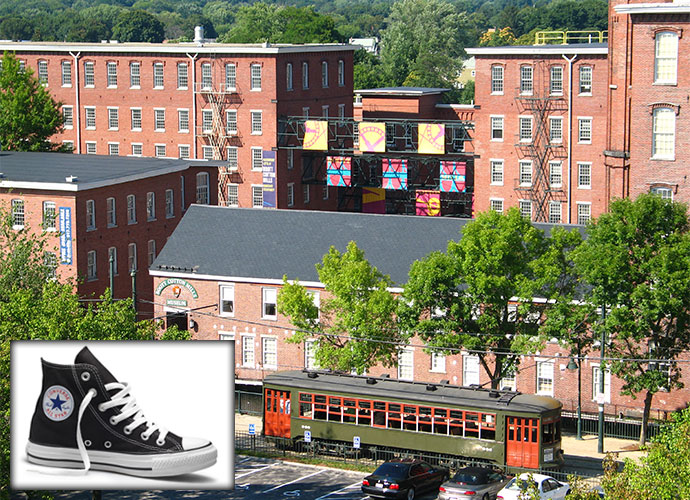
Among other projects announced in 2013 was a September decision by the Footwear Division of the Merchant House International Group to purchase a 40,000-sq.-ft. (3,716-sq.-m.) building in the Jefferson City Industrial Park just northeast of Knoxville, Tenn., where it will manufacture its line of men’s leather boots and shoes. The operation, to be known as Footwear Industries of Tennessee, Inc. (FIT), will begin shipping footwear in March 2014.
“We are excited about expanding our international presence and thrilled that’s happening in Tennessee,” said Loretta Lee, the founder of The Merchant House International Group, in September. “Jefferson City is an excellent location for our company because it is centrally positioned in the eastern United States, has excellent logistics infrastructure, and a work force with skills and experience in the apparel industry.”
The company plans to hire 109 employees, from sewing machinists and material cutters to operators for a state-of-the-art direct-injection molding machine. The company worked through the Tennessee Career Center to set up hiring and training programs.
The Footwear Division of The Merchant House International Group was established in 1980. Initially the company specialized in work boots, but in 2003 diversified into American-style western boots. The Division operates two shoe factories and in recent years has added production lines in Tianjin, China, to increase capacity to over 5 million pairs of shoes annually. The Group has shipped its footwear to the United States for 30 years, supplying major retail chains like Walmart, Kmart, and Sears.
Helping cement the deal were the Tennessee Department of Economic and Community Development, Jefferson County Chamber of Commerce and Baker Realty. Chamber spokesperson Garrett Wagley says the building was formerly part of BAE Systems’ complex in Jefferson City, where BAE had expanded several times to three buildings as it made bulletproof vests for the military. But the company saw contracts wind down and defense spending dwindle, so it had to lay off 132 workers and close the plant, as it moved other production to Ohio. The area unemployment rate before the announcement was 9.5 percent. As of the fall, there were still two BAE buildings on the market.
Stephanie Kaemmerer, operations manager for FIT USA, says the company has three employees as of this week, but plans to hire about 30 more in February, and 20 to 30 more in March.
“The response we’re getting from the area is very, very positive,” says Kaemmerer, who lives in Knoxville abnd used to work for a government footwear maker. “This was just a fabulous opportunity because it was brand new, and it was coming from China to the US — that was what I found so exciting about it.”
She says FIT USA’s supply chain extends into nearly every state in the country. “There is not an abundance of suppliers in the US, but I’m hoping in the next 10 years we’ll see that,” she says.
FIT’s is not the only good fit in Tennessee. Earlier in 2013, New York Times fashion reporter Cathy Horyn documented how the need for authenticity in fashion was translating into global attention and continuing investment in Bristol, Tenn., by L. C. King Manufacturing Co., which Horyn identified as “the oldest cut-and-sew factory in the United States still owned by its founding family.” The operation makes limited-run designer jeans, functioning in many cases as an “atelier” where the designer can come in and work with the craftspeople. Other recent textile investments in the state have come from Seaman Corp.’s industrial fabrics division, also in Bristol; hosiery maker Renfro in Cleveland; and Fiberweb in the Nashville-area community of Old Hickory.
In November, Fitesa Simpsonville, Inc., a designer and manufacturer of nonwoven fabric solutions for the global hygiene market, announced it will expand its existing facility in Greenville County, S.C., to significantly increase production capacity for its spunmelt nonwoven hygiene products. The $50-million investment is expected to generate at least 32 new jobs.
“Our mission is to be the preferred choice for the supply of nonwoven fabrics to the global hygiene industry, and to deliver high quality products with exceptional service and sustainable processes,” said Ray Dunleavy, director of marketing for Fitesa Simpsonville, Inc. “We are pleased to continue to grow our operations here in Greenville County, and appreciate the support of the Greenville Area Development Corporation and South Carolina Department of Commerce in making this announcement a reality.”
Fitesa Simpsonville, which is global headquarters and one of 10 Fitesa plants in eight countries on four continents, competed with other Fitesa locations in Washington and Wisconsin for the investment, said Dunleavy. The company in 2012 established a spunbound production facility in Lima, Peru.
“At the end of the day, we believe strongly that Greenville, South Carolina is the optimal location to help us attract and retain the quality workforce and the quality customers that we need to continue to grow and succeed,” said Dunleavy. “We believe this expansion is a win for all parties.”
Fitesa will invest an estimated $50 million to upfit and remodel its existing 190,000-sq.-ft. (17,651-sq.-m.), 100-employee facility in Simpsonville, making infrastructure improvements and adding equipment to increase production of spunmelt fabrics used in products for the hygiene, medical and industrial markets. Company leaders expect to begin hiring this spring, and to complete facility improvements by November 2014.
In October, Colliers International Charlotte’s Don Moss and Grant Miller represented Gildan Activewear in their recent site selection and expansion process for $250-million yarn-spinning facilities in North Carolina. Bringing 500 jobs to the area, Gildan will build two plants over 500,000 sq. ft. (46,450 sq. m.) in Salisbury and Mocksville. Moss and Miller worked with the North Carolina Department of Commerce, Bladen, Davie and Rowan Counties in North Carolina to procure the purchase of 26.2 acres of land for $1 and over $8 million in local cash incentives. The State of North Carolina Job Development Investment Grant could yield $3.49 million in state incentives over 12 years. The Golden Leaf Foundation is providing a $1-million grant to Davie County to buy machinery and equipment that Gildan will use at both plants.
According to the National Council of Textile Organizations, the US textile industry — from textile fibers to apparel — employed 499,000 workers in 2012 and indirectly supported 1 million additional domestic jobs. Some other facts:
- Over the last three years, US textile mills have built 23 new plants and invested more than $3 billion in new plants and equipment. Producers have opened new fiber, yarn and recycling facilities to convert textile waste to new textile uses.
- US textile shipments totaled more than $53 billion in 2012.
- The US textile industry is the third largest exporter of textile products in the world. Exports of all textile products exceeded $17 billion 2012 and have grown by 36 percent since 2009, an increase of over $4 billion. Total textile and apparel exports were a record $23 billion in 2012.
- Two-thirds of US textile exports during 2012 went to our Western Hemisphere free trade partners. The US textile industry exported to more than 170 countries, with 24 countries buying more than $100 million a year.
- The US textile industry supplies more than 8,000 different textile products per year to the U.S. military.
- The US is the world leader in textile research and development, with private textile companies and universities developing new textile materials such as conductive fabric with antistatic properties, electronic textiles that monitor heart rate and vital signs, antimicrobial fibers, antiballistic armor for people and the machines that carry them and new garments that adapt to the climate to make the wearer warmer or cooler.
- In 2012, textile workers on average earned 135 percent more than apparel store workers ($576 per week vs. $245) and received health care and pension benefits.
Moss and Miller were engaged by the company to begin the site selection process to include a number of initial candidates in multiple southeastern states. After narrowing down their recommended list, a site in Mocksville and a site behind the existing Salisbury facility were chosen as the finalists.
“The state of North Carolina provides us with a qualified textile work force, competitive energy rates and a good transportation network, which are all central to our expansion projects,” said Gildan Yarns, LLC President Chuck Ward.
Colliers’ Moss and Miller have been involved in several recent projects in 2013 including Gildan’s initial location in Salisbury and Gildan’s expansions in Clarkton, N.C., and Cedartown, Ga. They also were involved in Custom Nonwoven Inc.’s site selection and incentive negotiation process, which resulted in their selection of Thomasville, N.C., on October 4, 2013.
All the Way from Up North
As reported in this space in the fall, as part of Walmart’s initiative to help suppliers return production to US shores, Elan-Polo, Inc., a global footwear and 35-year Walmart supplier, will start production of injection-molded footwear in March 2014 at a factory in Hazelhurst, Ga., as part of a joint venture with McPherson Manufacturing. Once at full capacity, the new facility will create 250 jobs and produce 20,000 pairs of shoes per day. Previously, the company manufactured the shoes overseas in China, where the company currently ships 200,000 shoes per day.
Louis Hornick & Company, a leading manufacturer and importer of window coverings and home textiles, will invest $2.5 million to establish a new manufacturing facility in Allendale County, S.C. The investment is expected to create 125 new jobs over the next three years. The company has been supplying Walmart for 40 years.
“We aren’t just building a facility — we are moving to South Carolina,” said Louis “Tripp” Hornick III, COO of Louis Hornick & Company, in October when the announcement was made at the SelectUSA conference in the nation’s capital. Sounding as if a move from Manhattan to the Lowcountry might indeed be counted as “foreign” direct investment, Hornick said, “The fact that three Manhattan residents are doing so is testament to our dedication, but, equally, reflects on the wonderful people in the great state of South Carolina.”
Hornick’s company was founded in 1918 by his grandfather. Like many firms in the Southeast, it’s had military business in the past, making camouflage during World War II. Its biggest site selection up to now was in the late 1940s when the founder’s son, M. J. Hornick, decided to prove out his Wharton Business School thesis title — “The Inefficiencies of Manufacturing in New York City in a Multi-Storied Building” — and moved manufacturing to Haverstraw, N.Y., in Rockland County.
Hornick III said in October the South Carolina site is “not only cost-competitive with China and India,” but reduces lead time by up to 50 percent. Louis Hornick II, his father and CEO of the company, wrote in a year-end letter, “As my family and I move from Manhattan to South Carolina in order to be right next to our facility, let us remember that every job we create helps a family, our nation and our economy. We proudly look forward to our centennial.”
Or as the L. C. King slogan puts it, “Made in America was how America was made.”