Is it better to play favorites with project-specific packages, or to improve conditions more generally for everybody, thereby eliminating the need for all that incentives deal-making?
The same conundrum is evident when it comes to physically demarcated free trade zones. Should a port or city or nation devote its time to developing and administering such bounded areas, or do what it can to make its entire territory, in effect, one big zone of industrial bliss?
Look to Singapore or Hong Kong as shining examples. Or look to eastern China, where boundaried zones have proliferated to the extent that, from the outside looking in, it might as well be one big zone. The Republic of Korea’s internal competition among zones has led to several excellent models such as the Incheon Free Economic Zone and the Gwangyang Free Economic Zone. Vietnam’s burgeoning roster of zones is also engaged in healthy competition — a recent internal ranking of them sparked a fusillade of objections that only served to point out to corporations how many good choices there really are.
Maybe zones are, paradoxically, the best path toward no longer needing them.
“The argument for special economic zones (or SEZs) is hard to refute,” stated a Sept. 2011 report from KPMG, noting the SEZ leadership of Singapore, China and India, and the growing popularity and use of zones across Asia, the Middle East and Africa. But, it pointed out, “matching up industries to infrastructure is relatively straightforward stuff. The real challenges come in delivering that infrastructure in a well-planned, carefully integrated and financially sustainable way.”
Hartley Powell, principal in the Global Location and Expansion Services practice at KPMG, LLP, says whether zones are advantageous or not depends on the type of operation. He also says U.S. zones cannot be compared with zones in the rest of the world, which he equates to “what I would call a certified site. This is the way these countries attract investment — land and buildings are abundant, permitting risks are eliminated, all infrastructure is in place, there is a consistent and advantageous taxing environment, there is clustering of industries, labor risks are eliminated and time to market is reduced. So it’s a lot more than import/export. You can come up with some real savings by locating in a zone in another country. “
Powell ticks off prominent zone programs in Ireland, Panama and Brazil. He characterizes Latin American zones as “really strong.” But “China is off the charts.”
One site consultant says he has no favorite free trade zones. That’s because, in his 13 years in site selection across NAFTA, “almost none of our clients have expressed meaningful interest in or need for” free trade zones (called foreign trade zones or FTZs in the U.S.). He says regular incentives “frankly often have a greater financial impact than the tax/duty savings that FTZs specialize in. Each of the few companies that I have worked with that evaluated FTZs for their facilities concluded that the gains would not be worth the effort or tradeoffs of being in a FTZ. Savings are suggested but never quantified and put in the context of the entire operating cost structure and the impacts of location on costs.”
That’s not just a NAFTA problem. In May 2012, published reports recounted Siemens’ request to free its subsidiary from the free trade zone system in Colombia, where administering compliance was proving to be not worth the tax and customs exemptions. Another site consultant cites difficulties in India, and yet another says too much red tape caused his client to bail on a project. Indeed, asked what they’d most like to see improved across the board, respondents cite simplified reporting and more flexible terms.
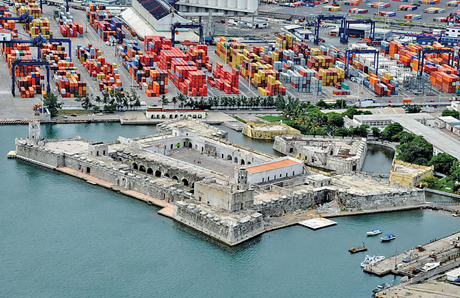
Such experiences aside, there are standouts. Among U.S. FTZ leaders named by other survey respondents are FTZs in Charleston, S.C.; Denver, Colo.; Tucson, Ariz.; Indianapolis, Ind.; and Granite City, Ill., along the Mississippi River near St. Louis. Also prominent in their superior results are the FTZs associated with the Alliance projects in North Texas, California and, now, Jacksonville. Where are zones improving the most? Respondents named such territories as Germany, Canada, the Middle East, Malaysia and Indonesia, where Batam — like Hong Kong and Singapore — is an island city that functions as one large free trade zone.
Greece is looking at zones as a possible path to fiscal salvation. Laos is pursuing a zone program. Zones in the Middle East continue to attract corporate interest, especially in the UAE, where the newest entrant, the Khalifa Industrial Zone Abu Dhabi, is expected to be complete by the end of this year.
Even as it looks to invest billions in zones surrounding its own ports, Brazil, led by a leading bank and a glass manufacturer, is working with a Singapore-based port operator in Cuba to make a zone at the famous Port of Mariel, whence some 125,000 Cubans fled to the U.S. in the early 1980s. Honduras has continued to nurse high hopes for a new special development region. South Africa is trying to launch a new zone program (not without some blowback). And Panama’s Colon Free Trade Zone is doing its best to capitalize on the canal expansion that so many other ports have been preparing for over the past few years.
But free trade zones aren’t only for the up-and-coming. The KPMG report also took note of how the more developed world might be looking to zones in a less patronizing manner in the wake of the global financial crisis. As the Al Franken character Stuart Smalley might have put it, “I’m an emerging market too, and that’s … okay.”
“Western governments may want to look to Poland for inspiration,” noted KPMG. “The only EU country to successfully deliver a SEZ, the country now has 14 that span a number of industrial sectors. Interestingly, Poland was the only EU country to avoid a decline in GDP during the recent recession (in fact, it had the highest GDP growth in the EU in 2009) and is considered to be one of the healthiest economies to come out of the post-Communist bloc.”
The Next 600 Million
There is little doubt that Asian zones set the bar in terms of both superior service and scale, beginning with such Chinese stars as Tianjin Economic-Technological Development Area and the Shanghai Waigaoqiao Free Trade Zone, where DHL in July opened its $175-million, 88,000-sq.-m. (947,255-sq.-ft.) North Asia Hub. The logistics giant also plans to invest another $132 million to add eight aircraft to service high-demand routes between Shanghai and North Asia, Europe and the U.S. by 2014.
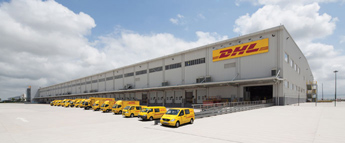
DHL’s Asia Pacific fleet already numbers 40, and the company has said it will continue to invest in facilities and infrastructure as the Association of Southeast Asian Nations (ASEAN) community looks to integration by 2015. The ASEAN region has a population of 600 million.
“DHL Express North Asia Hub is a logistics milestone in DHL’s Asia Pacific network and the culmination of a multi-hub and aviation strategy that cements our leadership position in terms of connections, convenience and cost-effectiveness,” said Frank Appel, CEO of Deutsche Post DHL. “With Asia’s leading economies fast integrating and free trade agreements reducing barriers to international commerce, logistics companies need capabilities that are ahead of the curve and offer simplicity, speed and service.”
Some see the next link in the free zone chain coming in Russia, where a 15-zone program already in operation is complimented by new port investments in such locations as Vladivostock in order to cement ties with the Asia Pacific.
DHL’s other Asia Pacific hubs are in Hong Kong, Singapore and Bangkok, where the company in May opened its fifth distribution center with a $2.7-million investment. Its primary hub in Thailand is located in the customs free zone at Suvarnabhumi International Airport. New aircraft connections to other Chinese cities such as Dalian, Qingdao, Beijing and Xiamen are coming this year and next year. The company was the first international express company to enter China 32 years ago — right about the time the PRC’s first free zones were making their debut.
As recently as 2009, the Waigaoqiao zone hosted companies employing 215,900 people.
In a report published this year, “Rebalancing and Sustaining Growth in China,” authors Huw McKay and Ligang Song of The Australian National University report that China had developed 55 export processing zones by 2010, with Jiangsu province home to 12 of them. The Kunshan EPZ in Jiangsu is the largest in the People’s Republic.
Since 1980, the nation also has developed at least eight SEZs, 33 Economic-Technological Development Zones, 49 High-tech Industrial Development Zones and five bonded zones or export-oriented units (EOUs). “Total processing imports in these free-trade zones accounted for more than 22 per cent of China’s processing imports,” in 2010, said the report.
When Zones Outrun Demand
Developing a zones plan is one thing. Filling those zones with dynamic activity is another. India, for one, has reconnoitered a bit after adding 323 zones in 2005 to the 19 that existed before an official government SEZ policy came into effect. As for which are actually operational, the total comes to 158, according to the government of India’s own website at sezindia.gov.in. The number of SEZs approved either formally or in principle in India comes to 637, with the most found in Andhra Pradesh, Maharashtra and Tamil Nadu, in that order.
The phenomenon is not unique to India. A total of 24 Export Processing Zones have sprouted in Nigeria since the first one — the Calabar Free Trade Zone — appeared in late 2001. But only 11 are operational.
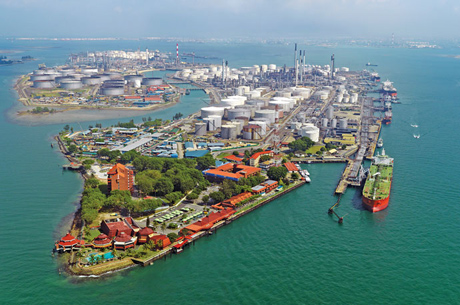
The minutes of India’s SEZ Board of Approval meeting held in September 2012 begin with statistics touting the fact that 588 formal approvals have been granted for setting up of SEZs out of which presently 386 stand notified.” Exports from SEZs were up in value by nearly 15.4 percent for FY 2011-12, said the chairman. But the dozens of agenda items that followed were littered with news of approval extensions and reductions in zone acreage, as well as outright withdrawals of zones. Some blame the re-imposition of a minimum alternative tax on zone occupants, and the pending consideration by the central government of doing away with SEZs’ income tax exemption.
Yet even as Indian SEZs undergo criticism for everything from real estate price escalation schemes to the recurring issue of inappropriate land acquisition from poor communities, the country’s central government looks to overlay yet another plan involving National Investment and Manufacturing Zones (NIMZs) measuring at least 5,000 hectares (12,355 acres) each. The government is asking states to start assembling land banks to help the process along.
And there’s yet another big plan out there: The $90-billion Delhi-Mumbai Industrial Corridor — also from the central government, but trying to access funds from abroad — will stretch across seven states; link Delhi with Mumbai; and feature high-speed freight rail, a six-lane highway and a 4,000-MW power plant. It’s also due to include nine industrial zones and 24 new cities.
In other words, one big zone.
The Business Times of India reported in August that India’s SEZs had created 680,000 jobs since 2006, and account for approximately a quarter of all exports. A review of export totals from India’s SEZs in 2010-2011 shows that of the seven zones set up by the central government before the new policy came into effect in 2005, the Cochin SEZ in Cochin, Kerala, is the far-and-away leader, with total exports worth more than US$3.3 billion. The SEEPZ SEZ in Mumbai comes next at $2.17 billion, followed by the Noida SEZ in Uttar Pradesh and the MEPZ SEZ in Chennai, Tamil Nadu.
Among the 21 state-run SEZs established before 2005, the Nokia SEZ in Tamil Nadu (named for the eponymous Finnish phone maker) led by far with exports valued at more than $2.5 billion, followed by Manikanchan SEZ in Kolkata, West Bengal, which specializes in gems and jewelry.
Other high totals come from zones established for such companies as Wipro, Infosys and Tata. Company-specific zones are indeed doing their part for corporate facility growth. Indian biotech giant Biocon got its 90-acre (36-hectare) Biocon Park in the Bommasandra area of Bangalore approved as an SEZ in 2005, and has populated it since with facilities operated by its various companies, with accompanying investment equivalent to $121 million.
This year the company inaugurated a new 300-scientist R&D center in April, then welcomed a five-year research contract and new 13,000-sq.-ft. (1,208-sq.-m.) R&D center from Abbott, working with Biocon subsidiary Syngene.
“India is a priority market for investment, growth and innovation,” said Robert H. Miller, Ph.D., divisional vice president, global research and development and scientific affairs for Abbott Nutrition. There were 114 reporting zones among those created since the 2005 decree. Beating all of the above in export value is the Reliance Industries Limited (RIL) zone in Jamnagar, Gujarat, with a figure of more than $19.3 billion, thanks to the presence there of a Reliance oil refinery and petrochemical complex. Company materials relate that the complex is “the largest industrial project ever implemented by anyone from the Indian corporate sector,” representing $6 billion in investment and a total area of more than 7,500 acres (3,035 hectares).
It was all built in less than three years thanks to a construction work force of 75,000 working round the clock for months on end. The complex includes a “self-contained” 415-acre (168-hectare) township, Reliance Greens, for over 2,500 Reliance employees and their families. In 2010, Boston Consulting Group ranked RIL as the second highest ‘Sustainable Value Creator’ for creating the most shareholder value over the decade in the world.
In July, RIL announced the selection of Technip to implement an ethylene cracker project at the site. Its products will be utilized for a sequence of new downstream petrochemical plants being built at Jamnagar.