Electrification Accelerates Stateside
The U.S. automotive industry continues to tread through murky waters as President Donald J. Trump seesaws on the implementation of a 25% tariff on automotive imports.
The tariff would lock in on passenger vehicles, light trucks and key automotive parts, such as engines and electrical components, with the potential to expand and encompass additional parts. New policy changes are said to be made in an effort to protect the U.S. auto industry and boost domestic supply chains, as President Trump and his administration focus on threats to national security and practically eliminating dependence on products manufactured outside of the nation.
Since President Trump’s proclamation signing, which invoked Section 232 of the Trade Expansion Act of 1962 in March 2025, the potential impact of the 25% (or more) tariff has thrown a hefty wrench into the workings of the global trade network. In the first week of April, tariffs on completed vehicles imported to the states went into effect. As of this writing, fees associated with automotive parts coming in have been temporarily postponed. Regardless, the global industry ecosystem now resides in a gray area shrouded in uncertainty as to how the full lifecycle of operations will continue and the potential impact of price hikes across the board.
It’s led to unique solutions in the meantime.
Automotive giants Honda and Toyota unveiled a new partnership following tariff news in March, announcing that Honda would begin tapping into Toyota’s U.S. battery supply. From Liberty, North Carolina, Toyota’s $13.9 billion battery manufacturing complex will supply Honda with enough batteries to power 400,000 hybrid vehicles. On the other hand, Ford Motor Company targeted consumer fears by offering employee discount pricing on its vehicles through its “From America, For America” campaign offering up to $10,000 off retail prices. Manufacturers such as Stellantis followed suit.
Reluctance to impose fees on auto parts comes as the President attempts to offer manufacturers time to relocate production operations to the U.S., a process that takes years to configure. While the overarching goal is to drive American-made automobiles, it seems the industry has been ahead of the game for some time.
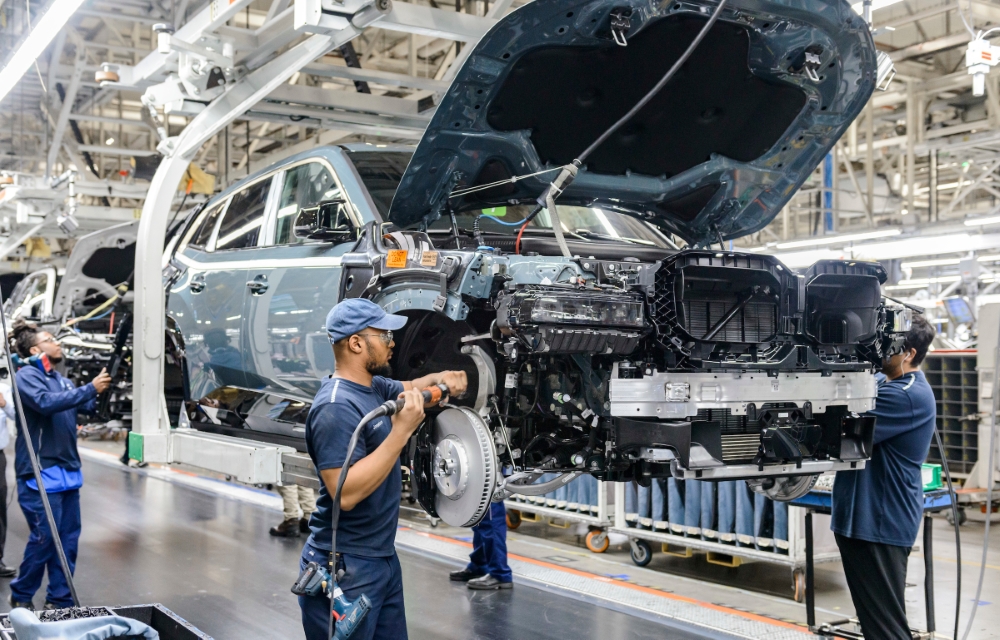
BMW Group has invested over $14.8 billion into Plant Spartanburg since 1992.
Image courtesy of BMW Group
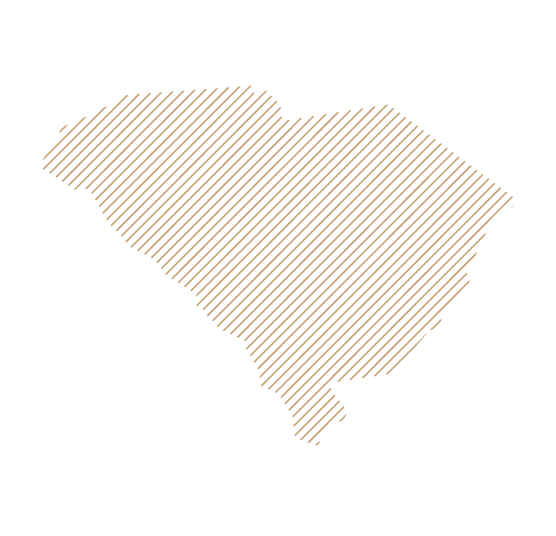
South Carolina
News of BMW’s arrival to Upstate South Carolina in 1992 turned the page on a lengthy chapter steeped in the remnants of a once-thriving textile industry. The fizzling out of textile manufacturing in Spartanburg left thousands without jobs and the community with no clear direction.
It took years for former Governor Carroll Campbell and his team to convince BMW that South Carolina was the ideal choice for its first U.S. manufacturing plant, recalls David Britt, who serves as vice president for Tindall Corporation’s South Carolina Division and vice chairman on the Spartanburg County Council. He recalls the overwhelming opposition the team faced at the time while cultivating incentives to secure the project centered around the region’s ability to manufacture vehicles.
“They gave us hope and opportunity for our residents with these jobs, and we have responded by proving to those naysayers that not only can we build an automobile, but we build the best automobile in the world right here at BMW’s largest plant in the world,” says Britt.
In March, BMW’s Plant Spartanburg rolled out its 7th millionth vehicle, a result of over 30 years of growth. A year ago, BMW was confirmed as the leading automotive exporter by value in the nation, bringing in $10.4 billion alone in 2024. Over the past decade, the campus has exported more than 2.7 million vehicles, equivalent to 63% of Plant Spartanburg’s total production and an export value of over $104 billion. The facility currently produces 1,500 vehicles per day, up to 450,000 per year, manufacturing 11 models including a suite of BMW X models, four BMW M models and two plug-in hybrid electric models. In 2024, nearly 50% of BMWs sold in the U.S. were produced in South Carolina.
“The prime reason BMW came here was because of the pro-business attitude of the state, from the governor all the way down to city council,” says BMW Manufacturing Media Communications Specialist Steve Wilson. “That alone was extremely important along with all the infrastructure that is here, the port, the airport and local universities and technical colleges. All of that creates a very sustainable quality of life.”
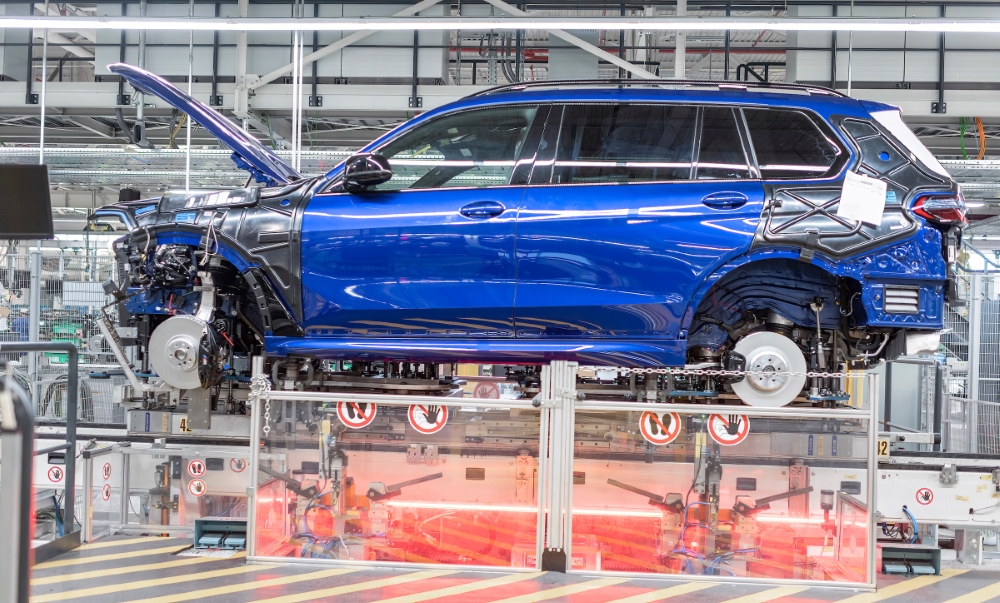
In March 2025, Plant Spartanburg produced its 7 millionth vehicle.
Image courtesy of BMW Group
A walk through Plant Spartanburg today takes one through a highly calculated and pristinely efficient workspace. Autonomous tuggers and Smart Transport Robots deliver various parts, sometimes weighing up to 2,000 pounds, with ease to employees throughout the freshly expanded lines of the assembly facility, while thousands of KUKA robots spanning the body shop maneuver massive tons of steel (70% of which is made in the U.S.) with unimaginable speed. A good portion of the vehicles manufactured at the site are custom built-to-order. Wilson says it has been key for suppliers to be at most a couple of hours away so when parts, such as specific seats, are unavailable at the facility they can be delivered and installed before a vehicle finishes moving through assembly that day.
Plant Spartanburg now spans over 8 million sq. ft. and will soon begin production of at least six fully electric BMWs thanks to a previous $1 billion investment to prepare the site. There has been a lot of activity in motion as the facility opened its first North American press shop, increased its X3/X4 assembly hall to over 2.4 million sq. ft., completed a 300,000-sq.-ft. main body shop expansion and introduced a new eight-story body shop stacker for vehicle storage in 2024. At the same time, BMW is in the midst of construction on a $700 million lithium-ion battery cell plant with partner AESC in Woodruff.
Recently, White House Senior Trade Advisor Peter Navarro alluded to BMW’s Spartanburg operations as a “scam,” stating that manufacturing international automobiles and parts is bad for the nation’s economy and national security. Britt shares a vastly different story, stressing the transformative economic impact BMW drove into Spartanburg, which has resulted in over $90 billion in various manufacturing investments from domestic and international companies whose industries will also be hit by new tariffs.
“When Peter Navarro takes on BMW, I am their staunchest advocate and fighter because I have worked closely with them for 33 years. I know what they’ve done,” says Britt. “BMW always under-promises and over-delivers — they’ve done this for years. Last year, their economic impact in South Carolina was $27 billion, they have over 60 direct Tier 1 suppliers throughout the state which employ about 55,000 in the supplier network. Their impact is not just in South Carolina, it’s in the Southeast. Without BMW there would be no Honda, no Kia, no Hyundai and no Volvo.”
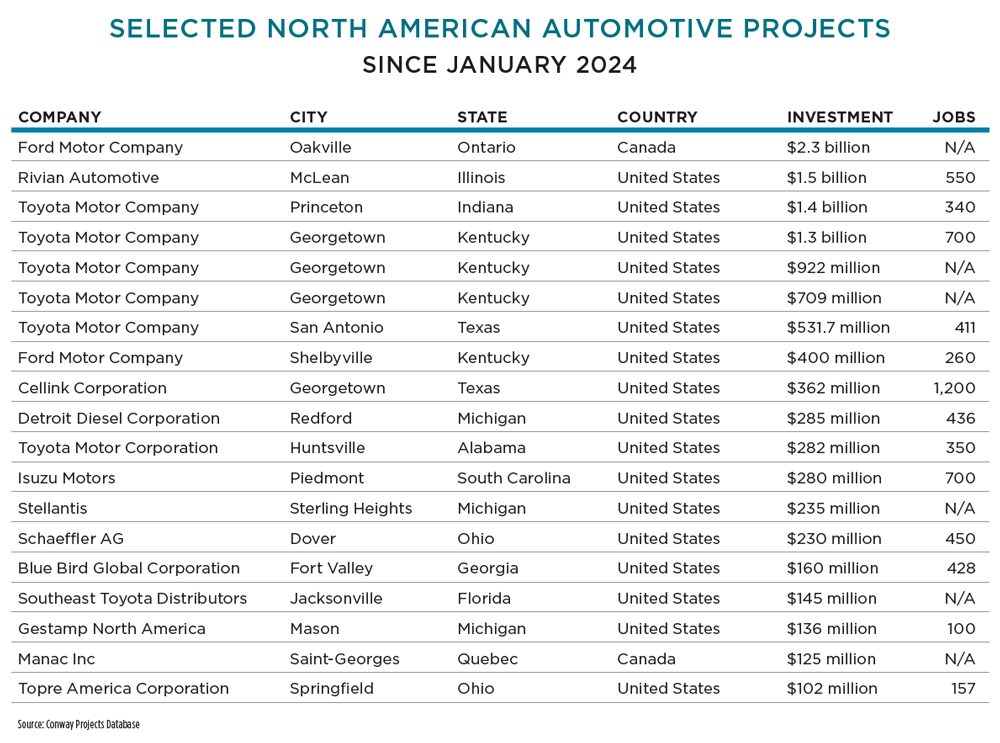
More than 11,000 employees are behind the production of those 1,500 vehicles per day, and BMW ensures its employees harness skills that continue to foster innovation. Aside from establishing its own $20 million, 68,000-sq.-ft. technical training center onsite, the company has been intent on building educational partnerships through programs like BMW Scholars, BMW Rising Scholars and BMW Fast Track. This includes tapping into local resources such as the Clemson University International Center for Automotive Research (CU-ICAR).
Pursuing research collaborations with CU-ICAR allows students and facility to interact with companies like BMW while exploring applications of new digital technologies, artificial intelligence, robotics, sustainable composite materials and more. This allows an innovative hands-on experience while students navigate their degree while unlocking industry-wide research potential. Wilson says BMW has hired several CU-ICAR graduates who earned their master’s in automotive engineering.
“We are their sandbox. Students interested in manufacturing can find a lot of opportunities here,” says CU-ICAR Executive Director David Clayton. “We’re trying to educate students that can help the industry that is here grow, but then also innovate and create leaders for tomorrow.”
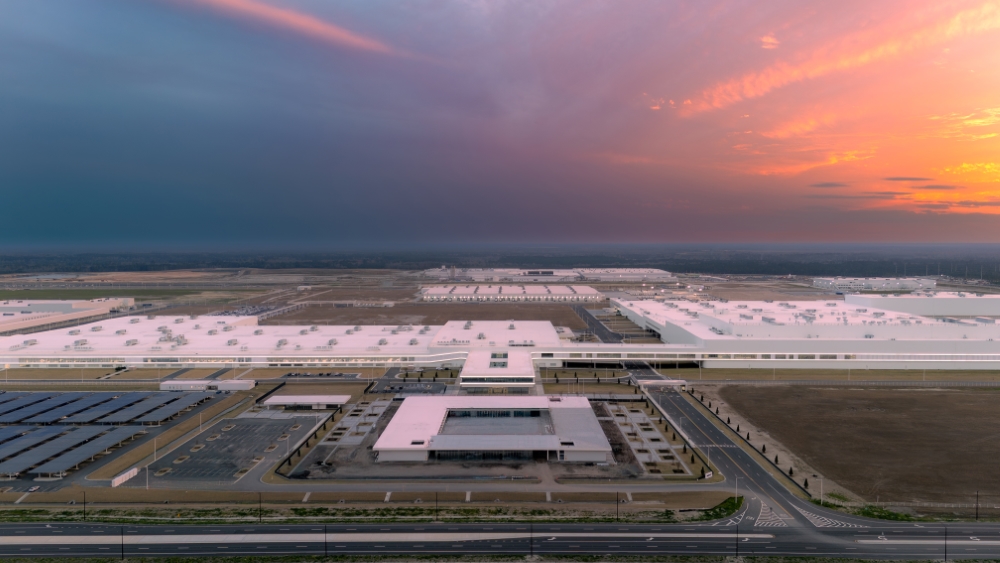
The HMGMA metaplant in Georgia features 850 robots and nearly 300 Automated Guided Vehicles to assist workers throughout assembly processes.
Images courtesy of Hyundai Motor Group
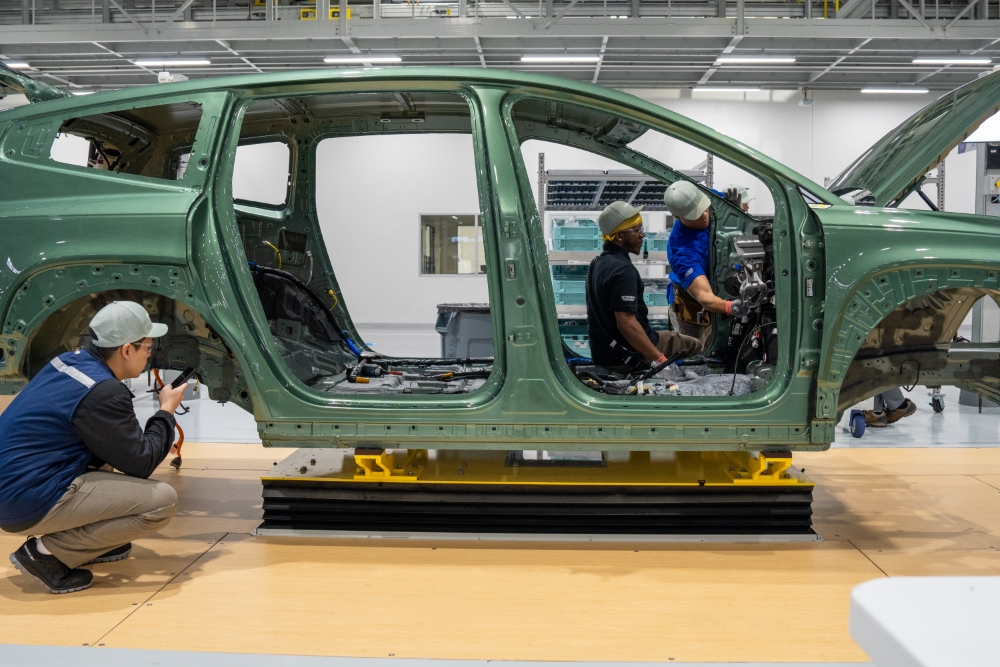
The first vehicle produced at HMGMA was a Hyundai IONIQ 5. HMGMA has now begun production of Hyundai’s IONIQ 9 SUV model, awaiting a new model projected to join the lineup by 2026.
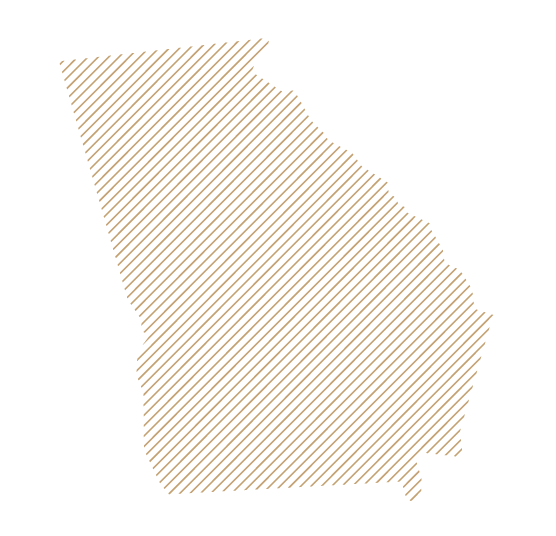
Georgia
In March 2025, Hyundai Motor Group officially launched the opening of the new Hyundai Motor Group Metaplant America (HMGMA) just outside of Savannah in Bryan County, Georgia. The $7.6 billion facility is the company’s first dedicated EV mass-production operation, featuring its own $4.3 billion battery cell manufacturing plant through a joint venture established with LG Energy Solutions.
About four hours northwest of HMGMA, Hyundai and Korea-based SK On will additionally house a JV battery cell production facility in Bartow County, Georgia. The $5 billion pursuit is set to begin production at the site in the latter half of 2025, carrying an annual production capacity of 35 gigawatt-hours or enough to power 300,000 EVs. The location of the facility is within proximity to HMGMA, Hyundai Motor Manufacturing Alabama in Montgomery and Kia Georgia in West Point near the Alabama state line. Hyundai Mobis will handle battery pack assembly using cells produced here and will distribute them among the company’s U.S. operations.
The sheer power of HMGMA’s formation has translated into over $2.5 billion in capital investment from suppliers making preparations across the state, creating 6,900 new jobs alone as of 2024. This moment arrives just two and a half years since HMGMA was announced in June 2022, marking the state’s largest economic development project to date. The facility will produce EV models for Hyundai, Genesis and Kia brands, and is geared up to manufacture hybrid models as well.
“In collaboration with our trusted partner Hyundai Motor Group, this investment underscores our dedication to driving America’s EV transition while bolstering the local economy through the creation of quality jobs,” said LG Energy Solution President and Head of the Advanced Automotive Battery Division Dong-Myung Kim at the time of the JV’s announcement in 2023.
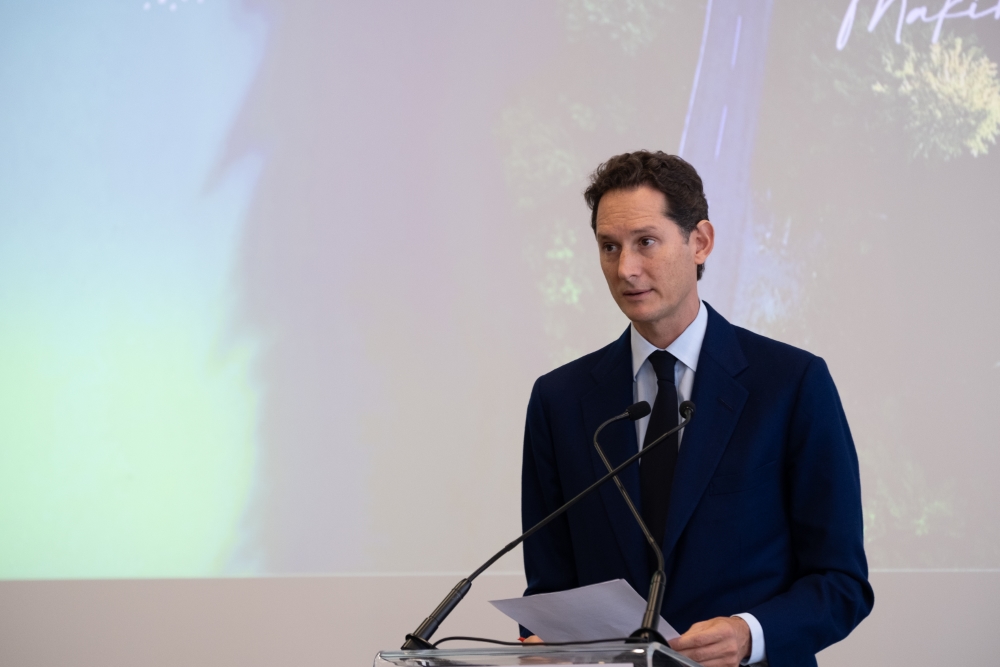
“With the current path of painful tariffs and overly rigid regulations, the American and European car industries are being put at risk. That would be a tragedy as car manufacturing is a source of jobs, innovation and strong communities.”
— John Elkann, Chairman, Stellantis, April 15, 2025
On-site production of battery cells will aid production of an initial 300,000 EVs per year. Proof-of-concept manufacturing technology has been integrated throughout the Metaplant and is boosted by AI and real-time data utilization, featuring 850 robots and 300 Automated Guided Vehicles designed to assist workers throughout vehicle assembly. In all, the site will have double the automation capabilities of any Hyundai production plant globally. HMGMA’s site also includes a 5.2-megawatt solar parking lot, in which solar panels have been installed over 1,878 parking spaces, collecting 5% of the site’s energy needs while providing shade below. Construction is still ongoing for the company’s 41-acre ecological park that will supply trails, running tracks, sports fields and green space at the site.
“Hyundai Motor Group Metaplant America not only represents the Group’s advanced manufacturing capabilities and commitment to innovation, but also our investment in relationships with our partners and communities right here in Georgia,” said Hyundai Motor Group Executive Chair Euisun Chung. “With the rich history of craftsmanship and manufacturing in this community, together with the talented workforce at HMGMA we are building the future of mobility with America, in America.”
In a move that deepens the company’s commitment to the U.S., Hyundai has announced a massive $21 billion toward U.S. manufacturing growth by 2028. A closer look at the funding’s breakdown shows that $9 billion is dedicated to increasing nationwide production capacity to reach 1.2 million vehicles; $6 billion to enhance Hyundai’s parts and logistics business, which includes a 2.7 million ton capacity electric arc furnace-based integrated steel mill in Louisiana; and $6 billion to drive innovation and expand partnerships with U.S. companies within autonomous driving, robotics, AI and advanced air mobility.
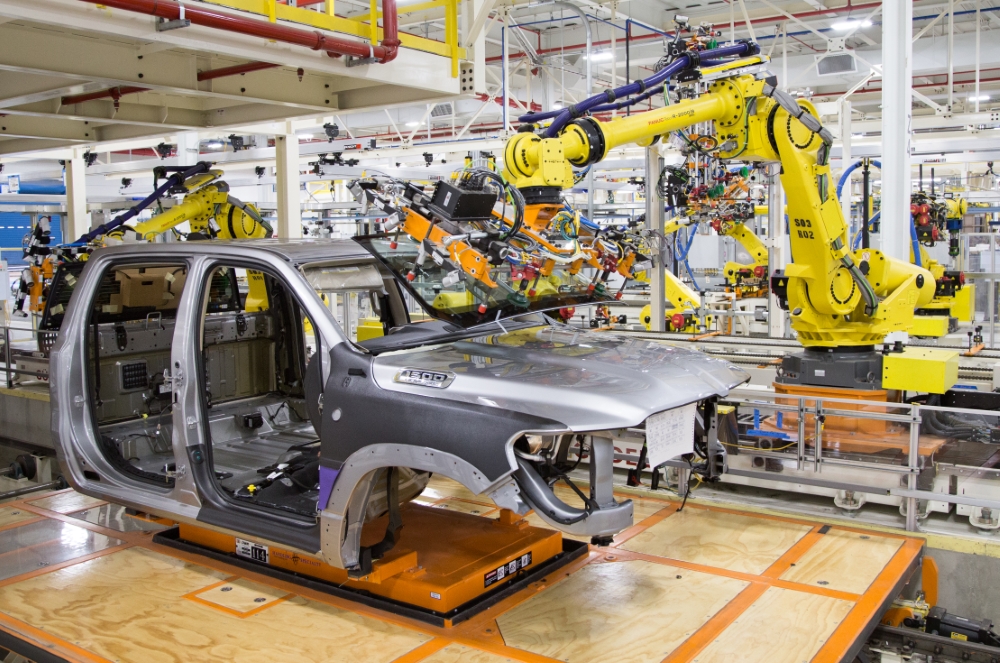
Stellantis is investing in upgrades to three Michigan facilities as the company focuses on its multi-energy strategy.
Image courtesy of Stellantis North America
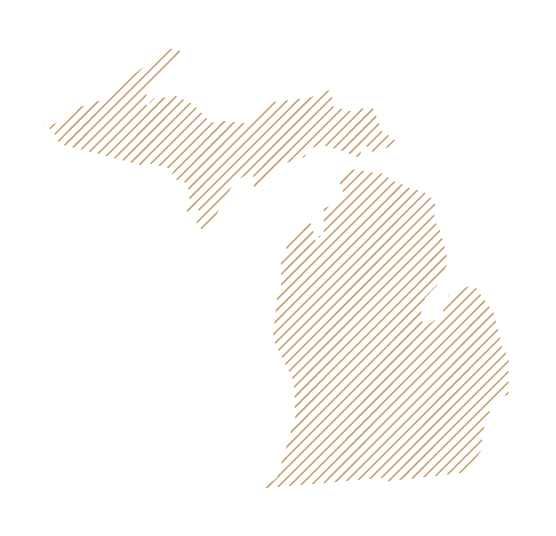
Michigan
While Stellantis North America has put a hold on operations in Canada and Mexico as of April 2025, leading to 900 U.S. employees being temporary laid off due to pending tariffs imposed by the Trump administration, the company will continue to improve U.S. production capabilities.
Announced in September 2024, Stellantis is ensuring its Michigan operations are set to roll out the company’s multi-energy strategy. Electrification efforts will allow three operations to fall directly in line with the company’s Dare Forward 2030 strategic plan, which aims to support a 100% passenger car battery electric vehicle (BEV) sales mix in Europe and a 50% passenger car and light-duty truck BEV sales mix in the U.S. within the next five years.
To do so, Stellantis has distributed over $406 million amongst the company’s Sterling Heights Assembly Plant, Warren Truck Assembly Plant and the Dundee Engine Plant.
The Sterling Heights Assembly Plant has received the majority of the planned investment, gaining $235.5 million as the facility prepares to manufacture the company’s first battery electric 2025 Ram 1500 REV light-duty truck. Project details include a new conveyor system, new automation for BEV-specific processes, retooling and rearrangement the general assembly line to cater to internal combustion engine, BEV and range-extended models on the same line.
“Gearing up to build our first-ever Ram electric truck and the range-extended version in Michigan is a meaningful moment of pride for our teams,” said former Stellantis CEO Carlos Tavares at the time of the investment announcement. “With these investments supporting both Jeep and Ram, we’re adding innovations to our Michigan manufacturing footprint to support a multi-energy approach that is laser-focused on customer demand.”
At the Warren Truck Assembly Plant, $97.6 million will support manufacturing processes for a future Jeep Wagoneer EV, representing one of the four models Stellantis will introduce in 2025. The Dundee Engine Plant will use $73 million in funding to prepare to produce battery trays that will be housed in STLA Frames, which have been specifically designed to integrate the battery pack in the new Ram 1500 REV. The investment allows the facility to be upgraded to assemble, weld and test battery trays for STLA Frames and to machine the front and rear beams for STLA Large architecture by 2026.
A few days following the announcement of paused manufacturing in Canada and Mexico, Stellantis announced it would be launching a new supplier support program, which is set to deliver financial assistance to qualifying suppliers to cover monthly tariff payments to the U.S. government. The short-term solution enables suppliers and the company to navigate the initial impact of the new tariff policy.
At the company’s annual general meeting in mid-April in Amsterdam, Stellantis Chairman John Elkann brought a global perspective to the situation: “In Europe and the United States, policy and regulatory choices have put our industry under extreme pressure, while China is on another trajectory,” he told shareholders. “This year, the Chinese automobile market is set for the first time ever to be larger than the American and European markets combined. In the United States, the car industry is severely affected by tariffs. On top of the 25% tariff imposed on vehicles, we are impacted by layer upon layer of additional compounding tariffs including those on aluminum, steel, and parts.”
Noting that CO2 regulations in Europe “have imposed an unrealistic path to electrification, disconnected from market realities,” he said, “With the current path of painful tariffs and overly rigid regulations, the American and European car industries are being put at risk. That would be a tragedy as car manufacturing is a source of jobs, innovation and strong communities. But it’s not too late if the U.S. and Europe take the necessary urgent actions to promote an orderly transition.”