
Monsanto Grows More Than Corn in Iowa
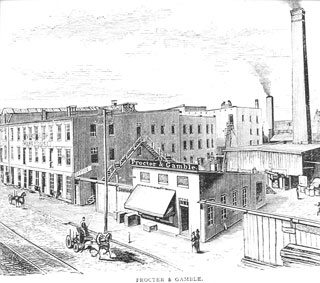
or its first domestic greenfield manufacturing investment in 34 years, Procter & Gamble Family Care in October chose a site in Box Elder County, Utah, for a 300-employee plant to make paper tissue and towel products for the western U.S. marketplace.
The project’s first phase is expected to attract an investment of US$315 million, with that figure edging toward $540 million eventually. Employment likewise is projected to creep toward 500 by 2010, according to state documents. Helping land the project was $85 million in incentives approved by the Governor’s Office of Economic Development Board. The county is working on its own set of property-tax refunds. But first, the company has to close on the 750 acres (304 hectares) of land, located a few miles west of Brigham City. That should occur in the first months of 2008.
P&G spokesperson Celeste Kuta offers some insights into why the company selected Colliers International to lead its process.
“Thirty years is a long time in Procter, and there are not that many people around that have done this type of thing in the U.S.,” says the 23-year P&G veteran. “For us, having an experienced organization like Colliers was just a tremendous asset, because we had lost a lot of that expertise in house from not having developed a greenfield site for so long.”
A search of the Conway Data New Plant database going back 10 years reveals 84 P&G projects worldwide. P&G Family Care currently maintains other U.S. manufacturing sites in Albany, Ga.; Green Bay, Wis.; Cape Giraardeau, Mo.; Mehoopany, Pa.; and Oxnard, Calif., where the division’s most recent greenfield investment took place in 1973.
Those existing locations were examined long and hard before making the leap to Utah with “Project Gold Rush,” says Gregg Wassmansdorf, the Toronto-based vice president and manager of Colliers International’s Location Advisory & Incentives Practice. Srinivas Reddy, associate director of engineering for P&G Family Care, helped lead the P&G team, which included its global corporate real estate group, a senior environmental engineer,
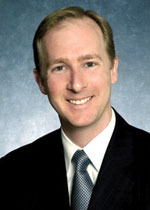
legal, HR, tax and finance personnel, as well as the future plant manager.
“In addition to evaluating the best deployment of capital,” says Wassmansdorf, “part of that best deployment decision by P&G was ‘Can we build a best-in-class capability with a greenfield plant more so than with an existing plant?’ “
In arriving at its Utah answer, the team considered sites in “a pretty broad sweep of the western region,” says Wassmansdorf, including sites in Washington, Oregon, Idaho and Nevada. Three finalists in three different states made presentations. “There wasn’t a singular turning point,” he says, “because we were looking at capital expenditure outlays, ongoing operational costs and risks all in parallel. How the three ranked just slowly became stratified over time.”
“The heavy infrastructure requirement is really the starting and the ending for this,” Wassmansdorf says. “There’s no shortage of land, obviously, in the western U.S., but to find the intersection of rail, ample supply of water, wastewater treatment capacity, electrical supply and natural gas supply in volumes that are required and at rates that make sense, that was a really big challenge.”
Helping meet that challenge will be Questar Gas, Pacificorp company Rocky Mountain Power and Union Pacific. Wassmansdorf says Box Elder County commissioners and Brigham City officials also deserve praise. The P&G plant’s jobs will pay an annual average wage of $42,000 – almost twice Box Elder County’s current median wage of $21,694.
Logistics and the products themselves drove the decision too. After all, customers like Charmin and Bounty because they’re soft and fluffy. Hence the plants that churn out those products tend to locate near the end customer.
Gov. John Huntsman was progressively more involved in negotiations as they wound down in the final months of a 14-month process, leveraging the work done by his office of economic development as well as the complementary efforts of the Economic Development Corp. of Utah.
Wassmansdorf says both state organizations send a strong and clear message, aided somewhat by “a bit of an anti-California response.
“Four projects have either landed or short-listed Utah in the past two years,” he says of his team’s site selection advisory work. “As companies look at their supply chain, Salt Lake City is positioned very well.
“If you’re going to handle the Western region and not be in California, Utah presents a pretty compelling option.”
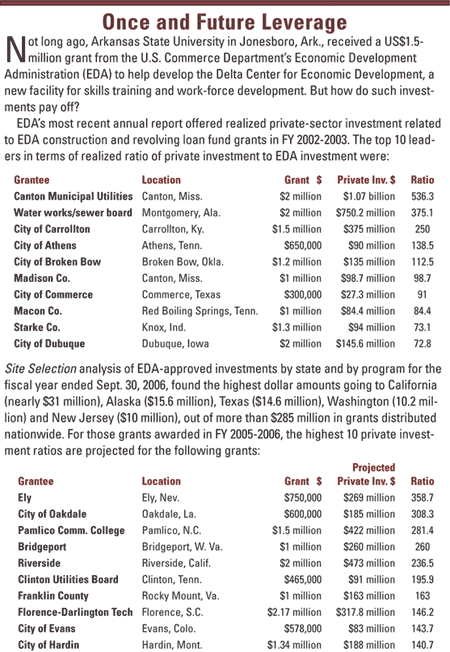
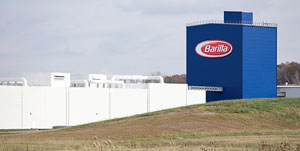
Italian-American
asta maker Barilla America opened its new manufacturing and distribution complex in Avon, N.Y., south of Rochester, on Oct. 19. The site will largely serve the U.S. northeast – which the company says composes half its U.S. market – with up to 50,000 tons a year of farfalle, ziti and other noodle shapes in its first phase, and up to 100,000 tons once two more planned production lines are added.
Originally forecast to cost $87.7 million when it was announced in March 2006, the project (pictured above) came in with a price tag of $75 million, and will employ 121 people. The 11-year-old U.S. division also operates a manufacturing and distribution facility in Ames, Iowa. The Avon complex, situated on 49 acres (19.8 hectares), will include a 205,000-sq.-ft. (19,045-sq.-m.) warehouse – managed, as in Ames, by Jacobson Warehouse Co. – and a 110,000-sq.-ft. (10,219-sq.-m.) manufacturing plant.
“Avon provides the hometown feel that this company strived to find in a new U.S. home,” said Kirk Trofholz, president of Barilla America. Guido Maria Barilla, chairman of 130-year-old Barilla Group, based in Parma, Italy, also attended the October festivities.
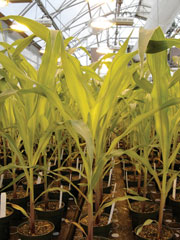
n a Nov. 8 presentation to investors, Monsanto Executive Vice President Carl Casale displayed the pre-eminence of the company’s DEKALB corn seed, which in 2007 achieved a 23-percent market share, three years ahead of schedule, and aims to corner up to a third of the US$3.2-billion U.S. corn seed market by 2012. By that same year, Monsanto aims to double its gross profit.
So it comes as no surprise that the company plans to double Iowa corn seed production with $230 million of operations investments that include expansions of DEKALB seed conditioning plants in Boone and Grinnell and a new seed conditioning plant at a yet-to-be-announced site in northeast Iowa where the company is finalizing a land purchase. The firm just completed a $4-million, 22,000-sq.-ft. (2,044-sq.-m.) research expansion in Ankeny, just outside Des Moines, one of 13 facilities it operates in the state, employing 1,000. The coming expansions could result in the employment of as many as 80 new full-timers and 1,200 seasonal and part-timers.
According to Monsanto Director of Manufacturing Kevin Lawrence, Iowa will produce about one fourth of the company’s U.S. seed corn when all facilities are operational, which is expected by 2010. The expansions include 150,000 sq. ft. (13,935 sq. m.) of new warehouse space in Boone; added space in Grinnell, where the company has operated for 70 years, after successive expansions in 2006 and 2007; and a 150-acre (61-hectare) operation at the northeast Iowa location, including 260,000 sq. ft. (24,154 sq. m.) of warehouse space and a seven-story conditioning tower.
Terminals Multiply
n Nov. 12, Singapore-based shipper APL loaded onto its APL Philippines vessel (below) its first “Ocean53” 53-ft. (16.2-m.) shipping containers, in order to help retailers and others take advantage of what it called “big box” economics. The ship sailed from the Port of Chiwan for the Port of Los Angeles shortly thereafter.
“We took the first order of 53-foot containers from our manufacturer in China and immediately put them to work,” said Bob Sappio, senior vice president of the Transpacific Trade at APL. “There’s a long list of shippers waiting for these boxes because they understand the potential for cost reduction and improved transit times.”
Though similar-sized containers have been used domestically in the U.S., the APL containers are the first of their size to be built durably enough to withstand ocean transport.
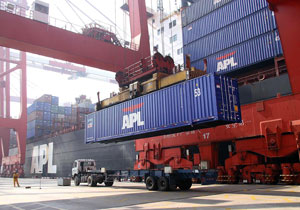
The company posits that fewer containers will mean reduced container expense, reduced handling and therefore less port, highway and rail congestion; and improved transit times because of the elimination of cargo transfer from smaller ocean containers to 53-ft. boxes at U.S. distribution centers.
APL introduced the domestic 53-foot box in 1989. Pilot tests of the oceangoing variety have received favorable reviews: “It can help international shippers control costs and simplify complex supply chains,” said Michael Jacobs, senior vice president of logistics for Toys “R” Us.
Big containers soon will be arriving on the U.S. east coast in larger volume. The Jacksonville Port Authority and Hanjin Shipping in October announced an MOU to develop a new $360-million container terminal. Expected to open in 2011, the 170-acre (69-hectare) facility is expected to move 1 million TEUs annually. It will be Hanjin’s first container terminal on the east coast, joining terminals in Long Beach, Calif.; Oakland, Calif.; and Seattle, Wash., and is expected to benefit from the expanding Panama Canal. It will be the growing port’s fifth marine terminal. At press time, a specific site had not been determined.
In August 2007, Hanjin announced first-half 2007 sales of 3.19 trillion Korean won, or US$3.5 billion, led by a 15-percent rise in container volume over the same period in 2006. However, the company said rising costs of stevedorage, inland transportation and chartering had contributed to an 80-percent drop in net income, to US$20.1 million.
Earlier in 2007, Hanjin ordered from Hyundai Heavy Manufacturing five new mega-ships with a capacity of 8,600 TEU each, on top of five 10,000-TEU vessels ordered in 2006 and scheduled to be deployed beginning in 2010.
Key to Record Investment
by UPS in Toronto
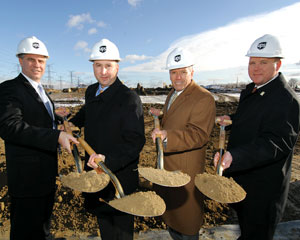
Pictured left to right are: Jim Wilson, Engineering Project Manager; Jim Lambis, UPS Americas Region VP Plant Engineering; Mike Tierney, President, UPS Canada; and Keith Porter, VP Operations, UPS Canada.
PS Canada announced on Oct. 30 its largest single capital investment to date, a US$73.4-million expansion of its Toronto Hub in Vaughan that is expected to be complete by 2009’s busy winter holiday season. And like the company’s successful partnership with Metro College for its WorldPort in Louisville, it expects to fill some 900 new positions in Vaughan with students from York University, whose main campus is right across the street.
With the expansion, the facility will increase to more than twice its current size, covering 40 acres (16 hectares) and expanding the building to 465,000 sq. ft. (43,199 sq. m.), doubling the hub’s processing and delivery capabilities.
“This new facility will be the largest UPS small package hub in Canada and will incorporate a number of new technologies,” said Jim Lambis, vice president of plant engineering for Mississauga-based UPS Canada. “We knew 20 years ago we would eventually exceed the limitations of our facility because of our successful operation and growth plans in Canada.”
The Toronto project came the same week that UPS revealed that it would be adding more than 17,000 sq. ft. (1,579 sq. m.) and investing several million dollars in its Fort Wayne, Ind., package handling hub, creating 25 new jobs and more sorting capacity at a site that already employs 333 full-time employees.
Site Selection Online – The magazine of Corporate Real Estate Strategy and Area Economic Development.
©2008 Conway Data, Inc. All rights reserved. SiteNet data is from many sources and not warranted to be accurate or current.