adam.bruns bounce@conway.com
he manufacturing infrastructure for a rejuvenated nuclear energy industry continues to sprout plum projects across the U.S.
In late October, French multinational AREVA announced it would join in a unique partnership with Northrop Grumman Shipbuilding to invest more than US$360 million and create 540 jobs at a new engineering and manufacturing operation in Newport News, Va., which will manufacture heavy components for the Evolutionary Power Reactor (EPR), AREVA’s Generation III+ nuclear reactor.
“AREVA intends to build one-third of all new reactors around the world and at least seven in the United States,” said AREVA CEO Anne Lauvergeon. “AREVA Newport News is a key step in our dual strategy to increase domestic content in the new nuclear power plants we build and to produce in the local currency.”
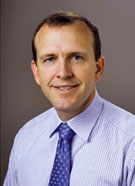
“Our shipbuilders embrace the opportunity to apply their considerable skills and training to a growing U.S. energy sector, backed by the pro-growth environment of the Commonwealth of Virginia, employing the same dedication and commitment to domestic energy security that has been applied to national security,” said Mike Petters, corporate vice president and president of Northrop Grumman Shipbuilding.
“Project Larkspur” will alight on Northrop Grumman property, affording the joint venture, named AREVA Newport News, prime access to the James River for transporting the reactor vessels, steam generators and pressurizers the 300,000-sq.-ft. (27,870-sq.-m.) plant will produce.
Chris Levesque, president and general manager of AREVA Newport News, LLC, led both the facility site selection process and the joint venture negotiations with Northrop Grumman, parallel processes that commenced in early 2007. Previously vice president of manufacturing, equipment sector, for AREVA, where he has worked since 2005, he also has served as manager of engineering and manufacturing at Westinghouse’s component manufacturing facility in Newington, N.H.
“AREVA decided we wanted to create this manufacturing capacity in the U.S., a capacity we already have in Marcel-St. Chalon, France,” he says. “I was tasked to find a location and potentially find a partner to create this capability.” The project proceeded in early 2007, with the assistance of Bob Price at Atlanta-based Herron Consulting.
“One of the key decision drivers was logistics – we receive very large forgings, weighing several hundred thousand pounds, and then ship components weighing in excess of 500 tons. So we need water access. That sent us to locations along the East Coast, and big river cities as well.”
Good transportation for customers and French colleagues was important too, says Levesque, as both will be very involved in the three-year transfer and ramp-up of the manufacturing process. “There are a lot of controls,” says Levesque, “and it’s very, very visible to our customers,” who will have senior managers on site for those three years. Thus talented labor is an absolute requirement.
“This is a highly engineered product, and the craftsmanship you need to weld and machine on these components is very demanding and specialized,” says Levesque. “For every shop hour of machining or welding, there is a matching hour of engineering – this operation will have 170 managers and engineers and 180 craftspeople.” It takes a lot of training, he says, but at the same time, “a heavy industrial welding and machining background is not something you can create overnight in a community.”
An overnight sensation Northrop Grumman is not. The company has been a stalwart sensation for the Virginia economy during its 100-plus years in the Commonwealth. As AREVA prospected for a partner as well as a site and work force, it could hardly have picked a more ideal companion.
“They had to pick us too,” says Levesque. “In parallel with the site selection process looking at going to communities and working on our own, we also had a negotiation in progress with Northrop Grumman, where we would build the facility together. Locating adjacent to their shipyard, where there are 10,000 craft personnel, was a great opportunity for us. In addition, the shipyard has a lot of recent experience of their own in building heavy industrial facilities on site. It’s not just the labor, but their experience with facility construction.”
That will come in handy as the companies endeavor to meet the unique requirements for the new facility. Among other attributes, the indoor crane capability must exceed 1,000 tons. There will be a 48-inch thick concrete floor, thick enough to support setting down a reactor and filling it with water for hydrostatic tests.
Levesque says Northrop Grumman’s strong apprentice program provides a lot of stability. But so does the AREVA factory in France, which employs more than 1,000.
“It would be almost impossible to have a pure greenfield facility where we didn’t have the process technology already,” he says. “We have a very well developed process that’s been created over 30 years, and we will be implementing those processes in Newport News.”
Much has been made of the dearth of heavy-duty forgings for the nuclear industry, which has been dependent in large part on one plant, Japan Steel Works, for some specialized components. AREVA, however, finds itself in a good position, having just signed a long-term agreement with JSW in early November that extends through 2016. In addition, the vertically integrated AREVA is working on smaller forgings with Lehigh Heavy Forge in Pennsylvania. Levesque says the company is well positioned.
“There is definitely a high visibility on these super-heavy-duty forgings being a critical piece of the supply chain,” he says. “The newer designs like the EPR have these large forgings designed into them. Japan Steel Works is the largest in the world, and the second largest is Creusot Forge in France, which in 2006 was acquired by AREVA [in partnership with ArcelorMittal]. It’s only about a half hour from the shop I was telling you about.” The companies announced a $110-million investment plan for Creusot in mid-2008, with French President Nicolas Sarkozy in attendance.
Among the first power plants in line for the components from Newport News may be a proposed reactor for UniStar Nuclear Energy at Constellation Energy’s Calvert Cliffs Nuclear Power Plant in Lusby, Md. An AREVA-Bechtel consortium was awarded a contract from UniStar in October that calls for detailed design engineering for the EPR plant. AREVA is constructing four EPRs elsewhere in the world – two in China, one in Finland and one in France – and has plans to work with U.S. utilities AmerenUE and PPL to construct other EPRs in Maryland, New York, Missouri and Pennsylvania.
To get ready, AREVA, which employs 5,300 people at some 45 locations in the U.S., continues to hire talent at its engineering operations in Charlotte, N.C., and Lynchburg, Va., bringing on 200 engineers in 2007 alone.
Other nuclear power industry-related corporate facility projects over the past 18 months include Alstom‘s $280-million, 360-job turbine and generator manufacturing plant in Chattanooga, Tenn.; GE-Hitachi‘s combined $954 million of manufacturing, R&D and headquarters projects in Castle Hayne and Wilmington, N.C., creating 1,150 jobs; Westinghouse‘s three-phase, $400-million headquarters expansion in Cranberry Township, Pa.; and, just announced in August 2008, a $100-million, 1,400-job nuclear reactor module fab and assembly facility in Lake Charles, La., from Westinghouse and Shaw Group.
“The nuclear power industry is bringing back ‘Made in America,'” said Tom Christopher, CEO of AREVA Inc., the group’s North American division, at the Newport News announcement.
Site Selection Online – The magazine of Corporate Real Estate Strategy and Area Economic Development.
©2009 Conway Data, Inc. All rights reserved. SiteNet data is from many sources and not warranted to be accurate or current.