
arly this summer, Chrysler Group announced three new investments in North America to support production of its Phoenix V-6 engine. While the new plants in Trenton, Mich., and Kenosha, Wis., will mean new investment but fewer overall jobs at their respective complexes, the US$570-million new plant in Saltillo, Coahuila, Mexico will create 485 new jobs.
“We are very proud of the union and support of our workers, many of whom were born and raised in this area,” Chrysler Group Mexico Manufacturing Vice President Roberto Guti?rrez said at ceremonies held in Mexico’s official presidential residence.
The 800,000-sq.-ft. (72,000-sq.-m.) Saltillo facility will be built near an existing 212,850-sq.-ft. (191,565-sq.-m.) Dodge Ram truck assembly plant that employs about 2,150 workers.
But a bigger job creator also is moving in right next door. In December 2006, Freightliner LLC, NAFTA’s largest commercial vehicle manufacturer and part of DaimlerChrysler AG (“Daimler AG” as of Oct. 4), announced its own $300-million, 1-million-sq.-ft. (92,900-sq.-m.) new plant, which could eventually employ up to 1,600 on its 740-acre (300-hectare) spread. It will be the 14th U.S.-owned car or truck OEM plant in Mexico.
In an interview from the truck maker’s headquarters in Portland, Ore., Freightliner COO Roger Nielsen explains how the site came into view, echoes Gutierrez in his praise of the work force, and dispels some misconceptions about Mexican infrastructure and economic development.
“In our experience, there is a big gap between the skills of the American and the Mexican government and economic development officials we’ve dealt with in being able to attract business,” says Nielsen. “The Mexicans are more focused and professional, from the President of Mexico on down. We have met with the President [Felipe Calderon] a couple of times. His goal is to create jobs for his citizens. You don’t see that as the primary goal of the [U.S.] states.”
In contrast to what he sees as a lack of in-depth knowledge among some U.S. economic developers of what businesses are doing and needing in their states, Nielsen cites the positive and multifaceted support he saw from the four Mexican states he visited in selecting this site: Tamaulipas, Nuevo Leon, Chihuahua and Coahuila.
“They were very articulate in what their states had to offer us,” he says, “not just in work environment, but ancillary support, university curricula, which ones have labs. It was amazing what they were prepared to do to support not only the startup of our business, but its continued growth into the future.”
And while one U.S. state expressed grave concern over the possibility a Freightliner operation might bring unions, says Nielsen, “In Mexico, they knew about every union, where they’d had strikes. The state of Coahuila hasn’t had a strike within its borders in 14 years. They have very strong unions – but the unions are pro-jobs and pro-business.”
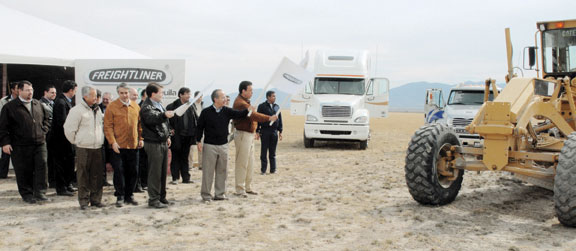
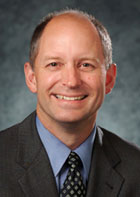
“Five major U.S.-based OEMs now have Mexican manufacturing capability, including Freightliner LLC,” said COO Roger Nielsen (inset) in December 2006. Above, the new plant’s groundbreaking delegation included Mexican President Felipe Calderon, Coahuila Gov. Humberto Moreira, DaimlerChrysler de Mexico Director of Legal and Government Affairs Luis Gomez and Alan Mayne, Freightliner’s general manager of manufacturing operations.
Freightliner’s site selection team comprises about eight people, including financial, HR, environmental, construction, architecture and logistics experts, as well as professionals from the DaimlerChrysler team who “have done this multiple times,” says Nielsen, emphasizing the team’s tight organization, planning and fact-finding model.
“We’re very productive on these trips,” he says. “The organization of site selection is just as important as going to visit a site.” While viable land parcels may not vary much in appearance, he says, “in every area, when you dig the next layer deeper, there’s always something you find that’s unique.”
Among Freightliner’s unique attributes is its breadth of products, including not only its Sterling, Freightliner and Western Star trucks, but also its motor-home chassis, Thomas Built school bus and step-in commercial van businesses.The company’s analysis of customer and supplier location was paramount, given that 85 percent of the value of a truck is supplied by outside suppliers. Figuring out how to haul the average seven tons of material per truck becomes an important calculation.
Based purely on miles driven, he says, the centroid for heavy truck manufacturing in North America would be Louisville, Ky. In terms of minimizing costs,
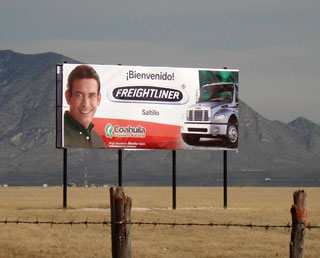
locations in the southeastern U.S. and in northern Mexico come into the picture because of a combination of existing supplier locations and low-cost labor, despite northern Mexico’s slightly higher freight costs.
Both Chrysler and Freightliner could point to excellent quality and business results at their respective plants in Toluca and Santiago Tianguistenco, outside Mexico City. Further supplier analysis cemented the Mexican option.
“We have about 1,800 different suppliers,” says Nielsen. “Of those, about 400 are primary, and the other 1,400 supply options and features and accessories. Of those 400, 90 percent already had an operation in Mexico or plans to put an operation in Mexico. We looked at our cost solution and said it’s only going to improve [in Mexico] because the largest cost was freight. That was a compelling reason to move there.”
According to press reports, Simon Boag, Chrysler Group USA procurement vice president, recently stated that DaimlerChrysler de Mexico expected to increase purchases from Mexican supplier plants from its current $6.4 billion to $8.5 billion by 2010.
For the remaining 10 percent of Freightliner suppliers who aren’t already there, “we’re in deep discussions about them moving to Mexico,” says Nielsen.
The talent waiting for them there is considerable, he says, fed by both a solid educational institutional base and sheer work force experience in the industry. U.S. states offer incentives for locating in disadvantaged areas, “but what you find out is the skills are not there.” That is what Freightliner now faces at its Cleveland, N.C., plant, as the state’s economic development success with some projects has in some ways depleted the work force for others.
“We are capped out because of immediately available work force in that immediate area,” Nielsen says. “We operate three shifts, drawing people from up to 80 miles (129 km.) away to our factory. Many employees get fatigued with that, and as soon as they can find a job closer on a day shift, they take it, and at a wage cut. Even where we’re at in North Carolina, we’d love to expand – great quality, great energetic work force. But at the peak of our market in 2006, we were losing 25 people a week. That’s about how many it takes to build one truck per day.”
In Saltillo, he says, “the state of Coahuila committed, before we got there, to build a town near our factories, with a planned population of 1,200 families. They will actually build the church, stores, homes, schools. And they will provide low-cost mortgages for people to move there. They see that as part of their responsibility and take a long-term view.”
Nielsen says there is one other way to measure the evolution of the Mexican work force, which he’s been watching since beginning to work there in 1989.
“Our workers are well-educated and highly motivated,” he says. “We really noticed the standard of living change at our factory outside Mexico City by how many times we’ve had to expand our employee parking lot. When we first expanded in 1992, there were lots of buses. Now everybody owns a car. They are very successful in terms of their community. We’re proud of that.
“Since I’ve been here, we’ve expanded parking at least six times, and we’re now in discussions to buy an additional 10 acres [4 hectares]. The state has been behind us, and has also come in with the road infrastructure.”
That isn’t the first time the state government has helped out with roads for Freightliner, says Nielsen, citing the replacement of a two-lane road with a commitment to a (76-km.) bypass freeway for the purpose of supporting the automotive industry.
Road widening and rail terminus work is also part of the Coahuila support for the new plant, in addition to gas pipelines, training curriculum development and delivery and site development assistance. On the federal level, Nielsen says he cannot divulge the amount, but the company will be able to use the funding to help entice suppliers to enlarge their industrial footprint in the Monterrey area.
Nielsen points out that “incentives are not at all in the financial equation of what we’re doing.” Instead, it’s simply a matter of optimizing operational costs. “At the end of the day, it came down to availability of work force and proximity to suppliers and customers,” he says.
Asked about the traditionally nagging issues of Mexican transportation and power infrastructure quality, Nielsen has no complaints on either count. Nor does he see flow of goods at border crossings to be a concern.
“I drove the road from Saltillo to the border at Piedras Negras to San Antonio, and the worst road was in the U.S.,” he says of a three-day trip to visit suppliers. “Mexican roads were autobahn quality. It was absolutely amazing. The old stereotype Mexican road, with speed bumps and red lights in cities, you don’t see that anymore.”
As for power, Nielsen says he’s seen more rolling brownouts in one of the southeastern U.S. states where the company operates than he’s seen at the plant outside Mexico City. A new line is being brought in over 9 miles (15 km.) for the Saltillo project, as there was not enough spare capacity for the facility to be served by the lines serving the Dodge Ram factory.
“One other stereotype you can dispel is environmental regulation, which is frankly stricter than we find in the U.S.,” says Nielsen. Among the requirements is 100-percent recycling of water, and he says air quality standards are on a par with U.S. standards.
The pace of the new project is too.
“It’s amazing what can be done in seven months,” says Nielsen, lauding the work of primary general contractor CH2M Hill Lockwood Greene. Approximately one third of the site’s acreage is being developed initially. Nielsen says it’s all leveled and graded, with foundations already poured for all major buildings and some minor ones. Excavation and concrete work has also been completed for settling ponds and drainage.
“We hope to erect the first walls in the fall, and have things under roof in January or February. Twelve months in, we plan on having a management meeting there with our top 200 people.”
Nielsen says his company is satisfied with the excellent support it has received in other NAFTA territories where it operates, including North Carolina, South Carolina and Oregon, as well as the province of Ontario. Each of those facilities has a place in the company’s network.
But “the only one running at full speed is the one in Mexico.”
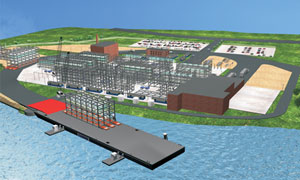
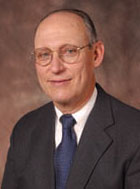
Home to a paper mill since 1889, this site in Brewer, Maine, will soon be producing industrial modules fabricated and assembled by homegrown industrial contractor Cianbro, based in nearby Pittsfield and led by Maine native Peter Vigue, president (inset).
he recycling of property is nearly as prevalent in Maine as woodstoves and town meetings. The projects reusing those properties could go a long way toward supporting a sometimes struggling state’s reputation for rugged independence and industrial fortitude.
There’s the proposed US$1.5-billion power and diesel fuel plant that Point East wants to build on the site of the former Maine Yankee power plant in Wiscasset, in the Midcoast region that begins at Muscongus Bay. At the state’s opposite extreme, in the far northern reaches of Aroostook County, two former MBNA facilities left over from that company’s incursion into the state in the early 1990s were closed in early March 2006 by MBNA purchaser Bank of America, but the Caribou-based Aroostook Partnership for Progress bought them in June 2006 for $924,000. The gamble has paid off, with contact centers from Connect North America (150 employees, growing to 300) and Synergy Solutions (100) now occupying the Presque Isle and Fort Kent facilities, respectively.
That purchase by the local economic development agency came over the initial protests of BOA itself as well as a local hospital and a health club that wanted dibs on the properties.
“We had the commissioner of the Maine Department of Economic and Community Development [Jack Cashman, now economic advisor to Gov. John Baldacci] intervene on our behalf, and through his efforts, Bank of America ultimately sold the buildings to us,” says Walt Elish, President and CEO of Aroostook Partnership for Progress. “Our concern was if Bank of America sold those to an existing local company, there was a good chance that new jobs would not be created.”
Instead, helped by CDBG and USDA Rural Business Opportunity grants, Maine Rural Development funds and Maine’s Pine Tree Zone program, the communities were able to offer significantly reduced lease rates that snared two corporate operations. The combined MBNA employment level of the two facilities has already been reached and may soon be exceeded.
In Brewer, just across the Penobscot River from Bangor, another rebirth is under way, thanks in part to the efforts of 59-year-old Caribou native Peter Vigue, president of industrial construction contractor Cianbro (pronounced “Chin-bro”). In early June, city officials announced that Cianbro and South Brewer Redevelopment, LLC signed a memorandum of understanding to work together towards a purchase and sale agreement for the 41-acre (16.6-hectare) former Eastern Fine Paper mill site, which had sat dormant since the mill closed in January 2004. A mill had operated there since 1889.
Cianbro will redevelop the site for the fabrication and assembly of large modules weighing in excess of 1,000 tons for industrial process plants located in North America and abroad. “Once manufacturing begins, the Brewer facility will employ approximately 500 highly skilled people performing work as welders, pipefitters, millwrights and electricians, along with other craft professionals and engineers,” said a company press release. “The shared vision for the Brewer mill site marries the revitalization of the site’s manufacturing roots to the growing demand outside of Maine for highly skilled craft professionals.”
Central to the vision is the Penobscot River, which will carry in steel and other components and carry out finished modules on barges to their end users.
The first phase of environmental remediation will begin in July 2007 with surficial soil remediation, the removal of abandoned above ground fuel storage tanks, and an updated lead and asbestos study. Additional work will take place this summer on the traffic study, road improvements, and design of a pier. It is anticipated that the site will be fully operational by April 1, 2008.
Employee-owned Cianbro is headquartered in Pittsfield, Maine, about a half-hour west of Brewer along I-95, and serves the eastern seaboard from offices in Pittsfield and Portland, Maine, Bloomfield, Conn.; and Baltimore, Md. Founded by the Cianchette Brothers in 1949, the firm operates in 15 states and employs 2,000 people on projects ranging from oil rigs to ship conversions, which it’s currently conducting in the Maine cities of Portland, Bath and Brunswick.
In an interview, Vigue says Cianbro operates two steel fabrication facilities, one in Pittsfield and one in Baltimore. Both the Baltimore site and the company’s marine site in Portland are redeveloped industrial sites. He says the company’s clientele ranges across industries as diverse as transportation, pulp and paper, power generation and transmission, petrochemicals, semiconductors, pharmaceuticals and food processing. Vigue says any heavy industrial user is a potential customer, including the coal-fired power and nuclear power sectors, LNG terminals and related energy projects in Atlantic Canada and the booming supply of projects in the oilsands of Alberta. He says negotiations on the company’s first module agreement for Brewer are nearing completion, though some module work done in Baltimore has already been shipped to a customer in China.
“Most of the work we do is sophisticated, with challenging schedules and a lot of complexity to it,” he says, citing a movable bridge project for Amtrak in Connecticut. “We have the ability to do all of the work ourselves with our own employees. We do all of the civil, structural, mechanical and electrical work – unique in this day and age.”
Also unique in Vigue’s experience is the “outstanding” quick turnaround and processing of environmental permits by state and federal agencies thus far. The project faces “huge challenges,” he says, including a significant amount of demolition, the reconstruction of every utility, cellular bulkheads on the river and the movement of large volumes of material in order to balance the site in terms of elevations.
The advantage of modularization, he says, is to remove some of the linearity of the construction process, allowing multiple activities to take place in parallel.
“When the site work is done, stack these modules and tie them together,” he says. “It’s safer, quicker and less expensive. Once manufacturers make decisions, they want to be producing.”
Vigue thinks Cianbro’s latest opportunity is a microcosm of what could lay ahead for U.S. manufacturing in general.
“I think the U.S. has some huge challenges when it comes to manufacturing, but I think certain jobs will stay here in the U.S.,” he says. “Manufacturers are certainly considering this. High-value, high-quality projects that have some uniqueness, or processes that require certain security, are going to stay here. Companies that are objective about that are going to be more efficient, will redesign their processes and are going to be able to advance.”
While the Brewer project has not yet received any incentives, Cianbro is looking for Pine Tree Zone status, working with the Maine Dept. of Transportation on the main access road and working with both city and federal governments to secure funding to assist in cleaning up the site. Asked about the company’s inclination to redevelop brownfield sites when so many such sites seem to go toward non-industrial reuse, Vigue says, “We look at them as transitions ? essentially we used existing industrial sites [for] different applications.
“People think it’s far more glamorous to have office, hotel and condos. However, brownfield sites and neighborhoods are far easier to develop,” he says. “These communities have undergone a major transition, are depressed and looking for opportunities. They’re accommodating and good to work with, and supportive of job creation.”
Site Selection Online – The magazine of Corporate Real Estate Strategy and Area Economic Development.
©2007 Conway Data, Inc. All rights reserved. SiteNet data is from many sources and not warranted to be accurate or current.