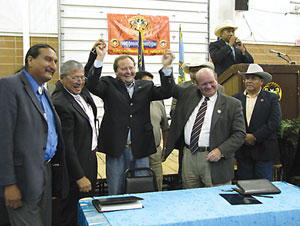
ing Coal has not abdicated the throne just yet.
There are many coal-to-liquid-fuel projects on the drawing boards, but until now the only active plants have come in South Africa. Now another is moving forward on a Native American reservation in Big Horn County, Mont. In early August, Australian-American Energy Co. LLC (AAEC) and the Crow Tribe (Apsáalooke Nation) inked a 50-year development deal that calls for the opening of a coal mine and a coal-to-liquids plant that would cost $7 billion to develop.
Called the Many Stars Project, it will employ as many as 4,000 during construction, and 900 when operational in 2016, when it will begin converting 38,000 tons of coal per day into 50,000 barrels of ultra-clean diesel, jet fuel and naphtha. The deal was brokered by Montana Gov. Brian Schweitzer, after meeting Australian-American executives at a conference.
“We are pleased to be bringing our Australian experience in clean coal projects to Montana,” said Allan Blood, AAEC Chairman. AAEC’s parent company has pursued two such projects in the Australian state of Victoria, the most recent with a price tag of $2 billion. “The Many Stars project is important on so many levels. It provides good jobs in a part of Montana that needs them, it helps address U.S. dependence on foreign fuels and it will demonstrate this is a technology that can be used in a way that addresses environmental concerns.”
Plans call for CO2 emissions from the plant to be sequestered underground and used to aid the petroleum industry in freeing up further reserves in nearby tracts.
“The Crow Nation has over 10 billion tons of coal resources,” said Crow Nation Chairman Carl Venne. Montana holds approximately 100 billion tons. Venne said the project would help his tribe of 12,000 become self-sufficient. Capacity of the plant could climb to 125,000 barrels a day, according to the company’s plan. According to the Associated Press, revenue from the plant, once fully operational and after investors recoup costs, could approach $1 billion a year.
AAEC now will spend 12 to 18 months to further evaluate the coal resources and select a final site for the mine and plant. The environmental permitting process will begin later this year. Construction is expected to begin in 2012.
n mid-June, HP found support for its technical support efforts in Rio Rancho, N.M., and Conway, Ark., where it will open new customer service and technical support centers.
The Conway Development Corp. will construct a $28-million, 150,000-sq.-ft. (13,900-sq.-m.) building and lease it back to HP, which will employ up to 1,200 at the center, located at The Meadows, a 181-acre (73.3-hectare) office and technology park in Conway, part of the the Little Rock metro.
“HP conducted a nationwide search and chose Conway as one of the locations based on multiple factors, including the quality of the work force, business environment, standard of living and government cooperation,” said Gary Fazzino, HP vice president, government affairs.
In Rio Rancho, just outside Albuquerque, up to 1,300 could be employed at the center, which will open in mid-2009 with several hundred employees. The project is in line for as much as $30 million in training and tax credit incentives from the state, in addition to financing assistance. Joe Flaxman, HP executive vice president and chief administrative officer, cited a substantial and educated labor force, education opportunities, amenities and an “eager” state government as reasons behind the choice.
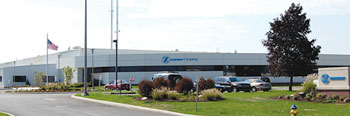
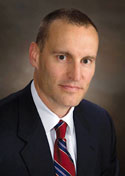
he Warsaw Wonder is at it again.
How many times can one company expand in one town? Orthopaedic device manufacturer and distributor Zimmer Holdings seems destined to find out, as it announced in late July a 100-job, $19-million expansion that will add 50,000 sq. ft. (4,645 sq. m.) to its complex in Warsaw, Ind., where it employs a payroll equal to more than 21 percent of the city’s population of 13,000.
It may sound like a broken record, but it’s really a case of record-breaking incremental investment. According to the Conway Data New Plant Database, this is the company’s fifth expansion in six years, including a two-phase project announced in May 2007. Earlier this year, Zimmer also announced a $70-million knee replacement implant factory in Shannon, Ireland.
Despite the apparent home-field advantage, Zimmer spokesperson Brad Bishop says, “We did look at other facilities. It’s an ongoing process evaluating where functions would best be located. We have major manufacturing in Puerto Rico, Switzerland and, soon, in Shannon as well. There are all of those sites to consider, as well as others we might also evaluate.”
“The demand for joint replacements continues to grow worldwide, and we are pleased to be adding this state-of-the-art foundry to our Warsaw facilities to address growth in a very cost-effective manner,” said Zimmer Holdings President and CEO David Dvorak.
The company’s most recent project was a new R&D center opened in summer 2007. The new castings foundry will go into a building the company purchased and expanded around that same time. With all that activity, it may be hard to look ahead. But, Bishop says, “We still have additional land where we could expand in Warsaw.”
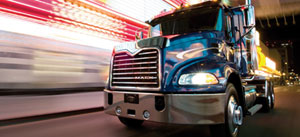
n mid-August, Mack Trucks, Inc., part of the Volvo Group, shook up its North American operations with the following restructuring moves:
• Moving the company’s administrative headquarters and most support functions from Allentown, Pa., to Greensboro, N.C., where many support functions are already headquartered.
• Transferring assembly of all Mack highway vehicles from the plant in Virginia’s New River Valley (NRV) to the plant in Macungie, Pa., (where Mack’s construction and refuse vehicles are currently assembled) to take advantage of efficiencies arising from consolidated assembly of the entire product line. The move will create 200 new positions at the plant. NRV will continue to produce all the vehicles in Volvo Trucks North America’s range. Macungie also will see a $20-million upgrade to its paint operation.
• Consolidating product development and purchasing functions currently located in the Allentown Engineering Development & Test Center to the Technical Center in Greensboro, N.C., to take advantage of synergies. The Allentown facility will be converted into a Customer Demonstration/Reception Center that will also house approximately 200 personnel supporting Macungie production.
• Restructuring parts distribution by creating a new Volvo Group North America central warehouse in a location to be determined; closing the Columbus and Dallas warehouses; and downsizing facilities in Baltimore, Chicago, Jacksonville and Memphis.
• Investing $50 million in a new engine block machining line in the Hagerstown, Md., powertrain facility, in order to complement the Volvo Group’s global capacity, and reduce both logistics costs and exposure to currency fluctuation.
Just over 1,500 people work in the three Lehigh Valley facilities affected by the restructuring: about 680 at the Allentown headquarters, about 540 at the Macungie plant, and about 300 at the Test Center, said the company. The NRV plant currently employs about 1,600 people.
The movement of Allentown-based administrative and support functions to Greensboro is planned for 2009, while those functions currently performed at the Allentown Test Center are scheduled to move in 2010.
The restructuring of the parts network will begin in 2009 and be completed in 2010.
n the same day in June that a new survey from Deloitte found that the majority of 321 top-tier manufacturing executives favored the United States over China or Mexico for investment over the next three years, a U.S.-Mexican joint venture announced a $75-million investment in two greenfield textile mills in Lacassine, Jefferson Davis Parish, La.
Zagis USA, a newly formed corporation between North Carolina textile executives and Mexico’s Grupo Zaga, will eventually employ 160 at the cotton spinning complex, with annual wages of $31,000 plus benefits. The mills will use as much as 20 percent of the state’s cotton crop, which historically has been exported.
“Zagis chose Louisiana because of its location relative to raw material, its infrastructure – Interstate, rail, ports – and the strong entrepreneurial support from the Louisiana departments of Economic Development and Agriculture,” said Zagis USA COO Dan Feibus.
A month later, DESA Heating Products, influenced by rising Chinese wages, rising transoceanic shipping costs and a falling dollar, announced it was bringing manufacturing work back from China to its 250,000-sq.-ft. (23,225-sq.-m.) facility in Bowling Green, Ky., where it will invest $6.4 million and add an unspecified number of jobs, projected by the state to be in the hundreds. DESA currently employs 450 at its Bowling Green plant.
“Bowling Green, Kentucky is an ideal location for DESA Heating Products’ expansion because we are located within a day’s drive of 70 percent of the U.S. population, we have a large labor base with whom we have a very solid relationship, and we enjoy a low overall cost of doing business here,” said Claude Hayes, president of retail heating for DESA, who called the work force factor integral to the decision.
“The partnership we have with Sheet Metal Workers Local 433 has enabled us to focus on our total quality initiative and given us the advantage of having the most productive labor force for our type of products in the nation.”
Site Selection Online – The magazine of Corporate Real Estate Strategy and Area Economic Development.
©2008 Conway Data, Inc. All rights reserved. SiteNet data is from many sources and not warranted to be accurate or current.