adam.bruns bounce@conway.com
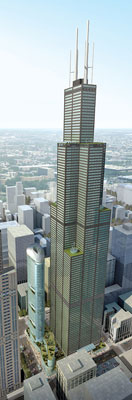
ome companies will follow an operational move with a headquarters move — witness NCR’s recent gradual shift to Georgia, or Oreck’s move of manufacturing and then headquarters from Louisiana to Tennessee during 2007-08. Not so for United Airlines, which announced in early August that it would follow the 2006 move of its corporate headquarters from suburban Elk Grove Township to downtown Chicago by moving its operational center and 2,800 jobs downtown as well, to the newly renamed Willis (formerly Sears) Tower.
“United and Chicago are inextricably linked, and this move further signifies our commitment to the city and region,” said Glenn F. Tilton, United chairman and CEO. “Willis Tower is a world-class, landmark building that offers a much-improved working environment for our people and the flexibility to adapt to the many changes that are inherent in our industry.”
Tilton serves on the board of directors of the city’s chief economic development agency, World Business Chicago, which played an instrumental role in linking the company, the city and real estate stakeholders.
The new operational center address on South Wacker Dr. will be positioned exactly 0.84 miles from United’s corporate headquarters on W. Wacker Dr., where 630 employees already work, just down the curving street’s path along the Chicago River.
The tower is doing its own job creation even as its denizens grow used to the new name bestowed in mid-July. Its sustainable modernization project, announced in June, aims to reduce the base building electricity use by up to 80 percent.
Modernization strategies designed by Chicago-based Adrian Smith + Gordon Gill Architecture (AS+GG) include window efficiency and glazing improvements similar to those being pursued simultaneously by the Empire State Building in New York; upgrades of mechanical systems, elevators, escalators and lighting systems; water savings; and installation of customized wind and solar systems. Other plans that are part of the US$350-million family of projects include a new park, a new LEED-Gold certified hotel and a sustainable technology learning center. Officials say the project is still exploring financing, but will reap energy savings within five years of implementation, as well as create 3,600 jobs in the process.
To Slip Away
hile much is made of new federal dollars pumping life into various agencies, not all count themselves so lucky. Owing to a discontinuation of federal funding, the National Ocean Economics Program (NOEP), operated out of the Monterey Bay Aquarium Research Institute since 1999, was due to close up shop in summer 2009. Among the premier services it offered was analysis of the U.S. coastal economy, including the shorelines of the Great Lakes.
Migration inland notwithstanding, coastal states account for 83 percent of the U.S. economy, says NOEP. Based on 2007 BEA data on the coastal industries of construction, living resources, minerals, ship and boat building, tourism and recreation, and transportation, the list below represents the leading 10 states ranked by coastal economy GDP.
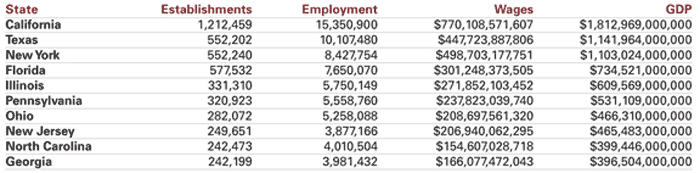
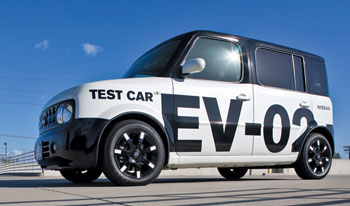
ummer began brightly for three automotive companies that were the recipients of $8 billion in conditional loan commitments awarded June 23 by the Obama Administration to support development of advanced vehicle technologies.
The breakdown:
- $5.9 billion for Ford Motor Co. to transform factories to produce 13 more fuel efficient models. The affected facilities include Chicago Assembly in Illinois, Louisville Assembly in Kentucky; Dearborn Assembly, Dearborn Engine, Livonia Transmission, Michigan Assembly and Van Dyke Transmission in Michigan; Kansas City Assembly in Missouri; and Cleveland Engine, Lima Engine, and Sharonville Transmission in Ohio.
- $1.6 billion to Nissan North America, Inc. to retool its Smyrna, Tenn., factory to build advanced electric automobiles and to build an advanced battery manufacturing facility. Nissan anticipates the project may result in an increase of up to 1,300 jobs in Smyrna when full production is reached. Construction at Smyrna is scheduled to begin by the end of this year, after an environmental assessment is completed. Production is planned to start in late 2012.
- $465 million to Tesla Motors to manufacture electric drive trains and electric vehicles, including a sedan model that would be roughly $50,000 less expensive than Tesla’s initial vehicle, the Roadster. Tesla now expects to create 1,000 jobs at an integrated facility in Southern California, after already moving the prospective complex location from Albuquerque to San Jose. The loan also supports a separate battery pack and electric drive train facility that would employ 650 in northern California.
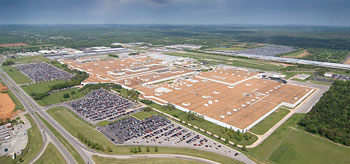
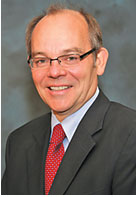
The loans were the first of a number to be awarded as part of the Department of Energy’s Advanced Technology Vehicles Manufacturing program. The department’s auto loan program has received more than 100 applications for loans to help firms achieve greater fuel efficiency, in keeping with the Obama Administration’s goal of raising passenger car fuel standards from 27.5 miles per gallon to a target of 35 mpg by 2016. First appropriated in the fall of 2008, the program will provide about $25 billion in loans to companies making cars and components in U.S. factories that increase fuel economy at least 25 percent above 2005 fuel economy levels.
as Vegas-based gaming system company Bally Technologies, Inc., is growing its campuses in both Las Vegas and Reno by leasing neighboring space.
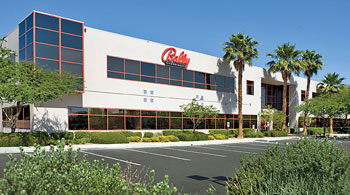
In Vegas, Bally is moving 175 game development, advanced development, and project management employees to 36,000 sq. ft. (3,344 sq. m.) in a former Carter Burgess building (pictured).
“The property is leased over a long-term basis which, including options, spans more than 20 years,” said Bally COO Gavin Isaacs in July. “Along with a smaller building across Bermuda Road housing about 100 employees, we truly have created a Las Vegas campus environment in a great location in the Hughes Airport Industry Center five minutes from the airport.”
The company is creating a similar campus-style environment in Reno, where it’s leasing a new 41,000 sq.-ft. (3,809-sq.-m.) facility adjacent to its existing facility, providing 340 employees more workspace, and enabling the efficient collaboration of the converging focus areas of games and systems. The staff in Reno consists primarily of R&D, customer service, product management, and various technical support and administrative personnel.
“We have had a presence in Reno for more than 20 years, and have had very positive experiences with the community and the Reno employee base,” said Gary Kapral, Bally’s senior vice president of human resources, when the agreement with Panattoni was first reached in April.
Construction on the Reno facility, being developed by Panattoni Development Co., is expected to be complete in September 2009.
Site Selection Online – The magazine of Corporate Real Estate Strategy and Area Economic Development.
©2009 Conway Data, Inc. All rights reserved. SiteNet data is from many sources and not warranted to be accurate or current.