California’s automotive design cluster has 22 design centers in Southern California alone, including facilities from GM, Toyota, Ford, Volkswagen (Santa Monica), BMW (Newbury Park), Volvo and Mercedes (Carlsbad). And California-born Tesla makes its home in Palo Alto, even as it’s reported to be searching northern Nevada and other states for a battery factory site.
Why are so many automotive design operations thriving in a state so prone to dysfunction and high costs? The answer may lie in looking more closely at an underlying asset, which the National Endowment for the Arts did in its August 2013 report “Valuing the Art of Industrial Design: A Profile of the Sector and Its Importance to Manufacturing, Technology, and Innovation.”
Numbering 3,370, more industrial designers reside in California than in any other state, according to 2012 statistics from the US Dept. of Labor’s Bureau of Labor Statistics. They’re also among the best paid in the nation: California metros occupy three of the top four spots in median annual salary for industrial designers (see chart on p. 138), topped by $100,610 in the Oxnard-Thousand Oaks-Ventura metro area, home to the Volvo Monitoring and Concept Center and BMW Design Works, where the bobsleds for the Winter Olympics in Sochi were designed (much to the German team’s chagrin).
The Santa Ana-Anaheim-Irvine area is home to Ford Advanced Product Creation, Hyundai’s American Technical Center and both Toyota’s Calty Design Research and Toyota Racing Development (TRD), less than two miles apart.
David Wilson was named president and general manager of TRD, USA in January. His responsibilities include overseeing two TRD facilities: the engine manufacturing location in Costa Mesa and the chassis engineering center in Salisbury, N.C. The TRD operation includes complete engine design, development and assembly, as well as production and development of engine component manufacturing. Wilson has been with the racing division (a subsidiary of Torrance-based Toyota Motor Sales) since it was “a step above a traditional California speed shop” in the 1980s. But that creation story is central to its ethos and success.
“When I came to the company, I was the first school-trained engineer,” he says. “We had a couple of lift bays, and we were basically hot-rodding Celicas and Supras.” From those aftermarket roots sprang TRD, which today encompasses about 235 associates, beginning with the 75,000-sq.-ft. (6,968-sq.-m.) headquarters in Costa Mesa.
“We’re principally an engineering company,” says Wilson, “and here in Southern California our focus is on engine and powertrain. We have the capability under roof to design and manufacture a purpose-built racing engine from a clean sheet of paper.”
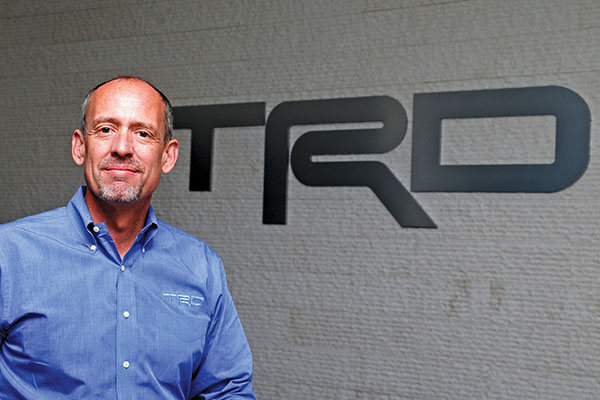
David Wilson, president and general manager, Toyota Racing Development, USA
The TRD complex includes six engine test cells, and an adjacent manufacturing operation with a dozen five-axis CNC machines, helping make everything from V-blocks to cylinder heads to casings. “It’s a very vertically integrated operation that allows us to design, manufacture, develop and test our product,” says Wilson. That can sometimes lead to tricky issues.
“The occupancy in this facility is very complex, because we have office people working next to shop space working next to manufacturing and engine testing,” he explains. “From a regulatory and permitting perspective, it requires a fair amount of oversight. One of our biggest oversights comes from the air quality management district, because we’re burning gasoline through the course of our engine testing. For several years we rode on a rider that qualified our operations as a test facility, and we weren’t required to have a permit. But that changed a few years ago when the volume of our work changed and production went up considerably. We had to go through the permitting process. We’ve done a good job, and our corporate culture is one where we really want to be good citizens. On the whole we’ve had very good experience with the agencies we face off with.”
Given a Choice
TRD landed in North Carolina when it entered the NASCAR world a decade ago, ultimately opening a full facility in September 2008. About 50 team members work there in such disciplines as chassis development and aerodynamics, with racing teams coming and going every day.
“We recognized the industry is all based in and around the Charlotte area,” Wilson says. “It’s important to have a footprint there. There’s a practical component, and there is also a social and political aspect — it was important to demonstrate to the community we were committed.” The state and community was solicitous in part because it represented the first Toyota facility in the state: “One of the reasons the state took notice and the community has embraced us is they’d like to be on the short list for the next manufacturing plant for Toyota, or some future manufacturing opportunity.”
Given the fact that TRD by far has its biggest investment in NASCAR, Wilson says, “You could argue, ‘Why don’t you just pick this up and move it to North Carolina?’ There are probably some advantages there to be realized. We studied that — you have to at least do the math.”
In fact, the footprint in Salisbury is set up for it, with the current operation occupying only a small fraction of TRD’s 40-acre (16-hectare) portion of the 90-acre (36-hectare) overall parcel it owns. “There is room to literally punch the walls out and pick up everything we’re doing here in California and move it to North Carolina.,” he says. “But from a business and human resource perspective, the math doesn’t work.
“Our biggest investment and most important asset is the people,” he explains. “It sounds cliché, but it really is true. If we decided to do that, there would be a cost associated with it well beyond the capital investment. So that’s a real, tangible consideration, and a real value for doing business here in California.”
Toyota’s Calty Design team, like its neighbors at Toyota Racing Development down the street, has steadily built capability as well as national and global influence over the years. Shown here are Calty’s 2014 Toyota FT-1 Team and 1978 Toyota Celica Team.
Photos courtesy of Toyota
As for keeping that talent around in a souped-up marketplace, Wilson says TRD is not bashful about using the California lifestyle as a recruiting tool for its multinational workforce. “We have under roof just about every nationality you can imagine,” he says, noting associates of German, French, South African and New Zealand nationalities, among others. “We bring them out to Southern California, and it’s very easy to fall in love.”
At the same time, the high degree of capability TRD and its neighbors at Calty have developed is attributable to area schools. “We really do prefer to develop young engineers, because this world has some very exacting demands,” he says of the racing environment. “It’s a tremendous opportunity for a young engineer to see their work realized on a real-time basis, as opposed to being a part of a much larger company and having a narrower opportunity where sometimes it’s more difficult to see the payoff.”
Down the street, Toyota’s Calty Design Research hub last fall celebrated its 40th anniversary. “Ideally situated in California to best absorb the influence of the state’s burgeoning car culture, the first Calty studio was viewed as a unique exploratory branch of Toyota’s global vehicle design organization,” said the company early this year as it recognized the facility’s heritage. “At the time, no one in the Toyota organization could imagine that 40 years later, the Calty facility would play a key role in some of Toyota’s most significant designs and be pivotal in the company’s movement toward regional autonomy for North American product development.”
Wilson says TRD contributed some powertrain concepts to the company’s new FT-1 vehicle. It’s a far cry from another garage-type beginning.
“El Segundo wasn’t a campus,” said Doris Kusumoto, Calty financial manager, of the hub’s original location before it moved to Orange County’s Newport Beach in 1978, when one of the first Calty-influenced vehicles, the Celica liftback, reached production. “It was one portion of a modest building in an industrial area. There were about six designers and 25 people total in support. Meanwhile, we would hear that domestic studios had 300 modelers and 100 designers. The manpower available meant Calty designers had to know more about the package and the architecture of the cars since we only had a couple of studio engineers.”
In Newport Beach, the Calty facility grew in 1990, tripling in size, and adding two new buildings. Today, it employs 65 people working in an 85,000-sq.-ft. (7,897-sq.-m.) design space. An estimated 75 percent of the concepts emerging from Calty influence or become production vehicles down the road. In 2012, Calty added the Toyota Innovation Hub in San Francisco. Strategically located near Silicon Valley, the establishment of this facility was a key step in Toyota’s global initiative to partner with innovative companies in technology, social media and design. “We want to transplant the innovative culture of the Bay Area to Toyota’s in-house innovation team,” said, Kevin Hunter, president of Calty Design Research. A Toyota Design employee since 1982, he is Toyota’s first North American design president.
Got a Garage?
In the racing world, most other OEM competitors lean more on racing team partners do to the lion’s share of engineering. Wilson says Toyota’s model is different, in part because “we like to participate, and like to get our hands dirty. We like to learn something by doing it.” It’s an approach very much in sync with the current “maker” revolution, where everyone from tool and die specialists to software designers wants to get their hands at least metaphorically dirty, preferably in their own garage-like workspaces.
That approach is present throughout the Golden State, including in the professional services-level design community. The NEA Report notes that the 2011 payrolls of industrial design firms exceeded $239 million, compared to a total payroll in the design nexus of New York of just $94 million. Small wonder then, says the NEA report, that “California ranks first and foremost in grants of U.S. design patents. Between 2008 and 2012, 12,520 design patents were awarded in California. This tally represents 20 percent of all state-level design patents. Ranking a distant second was New York, which garnered roughly 4,600 design patents, or 7.3 percent of the state total.”
The range of design runs wide in California, and includes several of the largest firms nationally in the sector, such as IDEO and Lunar Design in Palo Alto, and Frog Designs in San Francisco. It also includes firms such as MVE & Partners in Irvine, where Vice President Rick Castillo oversees the technical production of the firm’s key residential, mixed-use and commercial assignments both nationally and overseas. Through MVE’s substantial work in the multifamily housing sector, he’s seen design innovation in the form of increased density and transit-oriented development.
“In the early ’90s we were doing three-story walkups with 25 units per acre, and now we’re pushing those to double and triple that,” he says. “So density has really driven our practices to a much higher level of design — we have to be much more creative to make those buildings work.”
Castillo says his firm’s payroll ranges between 95 and 100 employees, and he’s recently looked at expanding workspace for his professional staff. “We’re almost at capacity,” he says of MVE’s digs on the entire first floor of the California Bank & Trust Building. He says a number of clients are bullish on California, and developing major projects. As for talent, he touts the state’s “phenomenal” university system, as well as its strong schools of architecture. At the same time, he’s growing accustomed to appealing to that talent among his client base.
“It’s very easy to fall in love.”
— Toyota Racing Development President and GM David Wilson
on the power of the California lifestyle as a recruiting tool
“With companies like SpaceX, Tesla, Apple … it’s a very leading-edge industrial design community,” he observes. So MVE and others have to be on their game in designing living space that level of talent finds amenable. “It’s interesting in terms of the demographic, and the ability to be mobile and flexible. We had a project in San Jose, for instance, where Google came in and rented out a large number of apartments and put their interns there.”
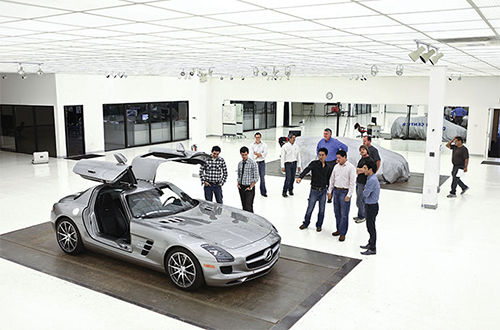
A 2010 portrait of the designer team of the Mercedes-Benz Advanced Design Studio in Carlsbad, Calif. Daimler’s first design studio outside Germany, it moved to Carlsbad in 2008 after first being established in Irvine in 1990.
Photo courtesy of Daimler
Google’s design genius lately has been required to focus on how it moves those people around. Its aircraft arrangements at NASA’s nearby Ames Research Center have drawn scrutiny. And street protests broke out over the charter buses it uses to move its people. The company still plans a major green office complex despite a recent postponement related to a bridge designed to ease those very traffic concerns. In the meantime, according to the San Jose Mercury News, it’s commissioned its own ferry, a WiFi-equipped catamaran dubbed “Triumphant,” to take employees back and forth between San Francisco and the Port of Redwood City, a quick private bus ride to Google’s campus in Mountain View. According to the report, Google, Apple, Facebook, Yahoo and Genentech have agreed “to pay up to $1.5 million in user fees” after the bus complaints.
Take Off or Stay Put?
In fall 2012, one of the companies Castillo mentioned — Elon Musk’s SpaceX — chose to remain in its 1-million-sq.-ft. (92,900-sq.-m.) headquarters in the L.A. community of Hawthorne, contingent on the establishment of a cap on annual business license fees (usually calculated based on gross receipts) and a 75-percent reduction in planning and building fees should it choose to expand.
In 2012 the company won a $440-million NASA contract to design and develop the next stage of human space flight, including 12 cargo missions to the International Space Stations.
Since SpaceX’s founding in 2002, the company has grown from three employees to over 3,500, with roughly 3,000 working at the company’s headquarters in Hawthorne. Los Angeles Economic Development Corp., Los Angeles County and the local South Bay community have all contributed to the process that has allowed SpaceX to successfully continue to expand operations. SpaceX is committed to hiring locally, with 275 trainees currently being taught advanced manufacturing skills.
Barbara Voss, senior regional manager for LAEDC, says the agency was initially contacted by SpaceX in December 2011. By January 2012, the agency was convening what they term a “red team” meeting of all relevant city, utility (Southern California Edison), workforce investment board and state officials to do everything they could to marshal resources that would keep SpaceX from decamping to such locations as Florida or Texas.
The final decision came in August of that year. Voss says the approval of an incentive agreement with the City of Hawthorne by the city council was a key turning point. So was consideration of talent.
“They had always expressed a strong commitment to their workforce in Hawthorne,” says Voss. ”Access to highly skilled and qualified employees was always a factor as they considered locating outside the state. So was existing infrastructure and the supplier network — because we have a high concentration of aerospace here, they have access to a whole range of suppliers and service providers.”
California Manufacturers & Technology Association (CMTA) spokesperson Gino DiCaro says despite looming concerns about the state’s cap-and-trade measure regarding emissions and workers’ comp costs that still amount to the nation’s third most expensive, the eight-year, 4.19-cent machinery and equipment sales tax exemption signed by Gov. Brown last year “puts California in the mix for some long-term investment coming up.” CMTA fought for 10 years to get the exemption passed.
Time for a Redesign?
Some wish California’s penchant for design could be brought to bear on its own government. In some ways it already has, as Gov. Jerry Brown has taken a number of steps winning plaudits from the business community. But some envision an even more altered reality. The most outlandish proposed redesign is a total restructuring of the state itself.
Tim Draper, founding partner of Silicon Valley venture capital firm Draper Fisher Jurvetson, in February took another official step forward in his effort to put a measure on the ballot calling for the state to be officially divided into six new states (see map). He can now collect petition signatures to qualify the “Six Californias” measure, and must collect approximately 806,000 of them by mid-summer to make it.
In a Q&A document furnished by Draper’s publicist, he says the lines “were drawn with population, geographic and regional considerations. Counties can vote to join another state if they choose.” As for water rights — important in a state suffering through a severe drought — he says, “Water has always been an issue that is negotiated among states. This will be no different. Except that it is possible that new states can work together to come up with new concepts in water distribution like load balancing and time division [rather than just geographical division] of water. I expect the same to be true of highways and distribution of electricity.
“Sacramento has an untenable job trying to match the needs of 38 million people with their policies,” he says. “It just doesn’t seem to work … Why not move government closer to the people and raise our voice in the Senate? Why not let voters choose if they are content with the way they are currently represented? I expect that new platforms will be laid for future prosperity and that more local government and better efficiency in government will benefit all Californians. And hopefully, each of the governments will learn from the improvements of the others.”
If so, they’d be emulating the practices of innovative companies who already call California home, and would like to keep doing so.