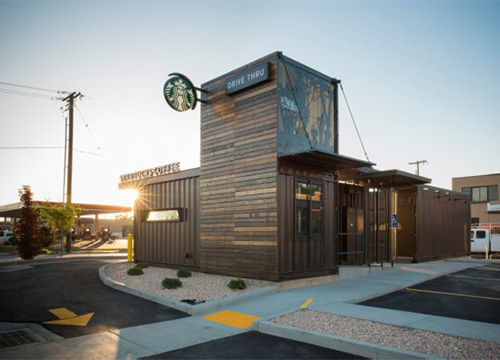
Could the cargo shipping containers that so efficiently transport our goods around the world also deliver the goods as an effective building solution?
New York-based SG Blocks thinks so. So do a growing number of clients and partners, including the US Navy, which in August signed an agreement with the designer of container-based structures for two modularized units that will provide supplemental office space pier-side or ship-side.
Not only are the units self-contained and non-combustible. They’ll also be ready by about … now, less than one month since the agreement was signed.
That’s because so much is already fabricated: Container-based structures – whether based on 20-ft. or 40-ft. containers – exceed many standard building code requirements, and also support developers, architects, builders and owners in achieving greener construction, faster execution, and stronger buildings of higher value.
“All containers are eight feet wide, so they can stack,” explains SG Blocks Chairman and CEO Paul Galvin in a phone interview from his New York office. “We work with that inherent strength. Corner castings are the common element. We try to help design structures to create a grid that reduces the number of cuts and reinforcements of the containers.”
The four SG Blocks product lines of retail, commercial, military and residential don’t include industrial per se. But they might soon, as corporate facilities and construction minds are opened to possibilities stacked right under their noses.
“A consistent part of our work is to educate and motivate long-term, traditional corporate builders, and encourage them to consider solutions that are greener and sustainable, and more prefabricated,” says Galvin. “Inertia prevents many companies from making changes. It’s not unusual for us to have people who have been building for 30 or 40 years to not be so familiar with the whole concepts of sustainability, recycling and repurposing of existing materials.”
But they’re getting familiar fast, influenced by corporate sustainability mandates from above, and by the priorities of their new millennial colleagues, who Galvin describes as “the first generation to have been raised on sustainability” and who see the large resources and energy impact of building construction choices on the ecosystem.
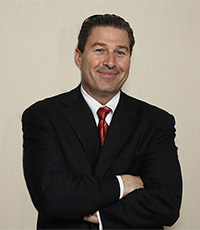
And if the older crowd doesn’t see things through a green lens just yet, they see costs very clearly.
“We save about 50 percent in time to market using our prefab containers” vs. traditional construction, says Galvin, noting that SG Blocks has also never encountered permitting difficulty due to specs that often exceed building standards. “It saves a lot of money on hard costs, but in particularly time to market.”
Ready to Roll
Galvin says his company’s range of permanent, temporary and mobile structures has appealed to a number of large Fortune 100 companies and several branches of the military over the past five to seven years. Bathroom and kitchen units, command centers and clinics have popped up in 46 states for military and multinational clients, and one container was transformed in South Carolina into a house destined for Shostka, Russia. The client list includes Starbucks, Puma, Lacoste and Schneider Electric, whose end user is Walmart.
The structures in that case, says Galvin, make for “a very efficient container-based electrical room, put on a slab when foundation work is finishing. They build the stores around the electrical room, and it becomes a permanent part of the infrastructure.”
In addition to architectural, engineering and design services, SG also offers predevelopment services including zoning, site plans, engineering specs, budgeting and pricing, builder selection and construction permits; project management; oversight of the building erection, cladding and finishes; and complete turn-key projects inclusive of delivering a finished building.
Crucial to SG Blocks’ business model is its just-renewed 10-year collaboration and supply contract with ConGlobal Industries Inc., one of the largest shipping container depot operators in the United States, with 30 locations in the US, Costa Rica and Mexico (see map). North America’s largest full-service supplier to the intermodal industry, ConGlobal, based in the Bay Area, early this year became a wholly owned subsidiary of In-Terminal Services LLC (ITS), a leading provider of rail intermodal terminal services, which is majority owned by Carlyle Group. Based in Tinley Park, Ill., ITS handles more than 6 million lifts annually and has approximately 2,000 employees. ITS customers are among North America’s largest railroad and intermodal service providers. ConGlobal, meanwhile, has control of about half of all the cargo containers in the US.
“SG Blocks is the clear first mover and innovator in green, modular construction and the clear partner of choice for ConGlobal,” said Mike Baldwin, president of ConGlobal, when the two companies renewed their agreement in June. The renewal includes the opening of an SG Blocks West Coast office at ConGlobal’s headquarters in San Ramon, Calif.
“The professionalism, expertise and geographic reach of ConGlobal cannot be matched by anyone in the industry and ensures that SG Blocks construction projects can be created and installed anywhere in the world,” said Galvin. “The ConGlobal team and reach propels SG Blocks growth and the adoption of container-based structures into the mainstream of construction.”
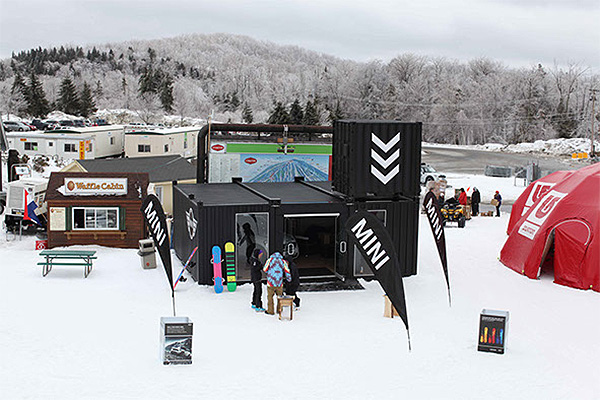
As a leading retailer of new and used containers, ConGlobal is able to supply SG Blocks from any of its locations. It’s a classic win-win, says Galvin, and he means it.
“We acquire the containers from their various sites, and we work with their team of welders and cutters and construction personnel, so we modify the containers in place,” he says, thus providing another green benefit by not requiring transport. “We do a lot of work in Jacksonville, Charleston and Houston. We’re not only buying surplus containers, but also surplus labor, by experienced professionals. And we don’t have to ship it to an intermediate facility to modify it.”
In an interview from San Ramon, Baldwin says the two firms are natural partners, noting one recent national project that was fairly complicated and on a short timeline.
“The beauty of ConGlobal is I took five of my locations and divvied up the project, and they’ll deliver from five different locations all on site and on the same day,” says Baldwin. “Nobody else can do that.”
ConGlobal’s primary business is inspecting, storing, repairing and sending back out intermodal containers and other related equipment for all the major global shipping lines and equipment operators. The company handles about 20,000 containers a week.
“We had 127,508 TEUs as of this morning in our possession for our customers,” Baldin says. (“TEU” refers to 20-ft. equivalent units.) The byproduct of that tremendous volume of containers that are slightly damaged or simply at the end of their useful lives. Asked by customers to get rid of them, ConGlobal would sometimes do minor modifications and sell them for tool sheds at job sites. Then SG Blocks came along about 10 years ago.
“They’ve turned it into more of a mainstream building structure, and done all the engineering,” says Baldwin. “That’s not what we do. I have 800 people in the company who are very good skilled technicians as it relates to containers. We pick out the container, do the hot work, and deliver that to SG Blocks’ job site. Our core competencies really complement each other.”
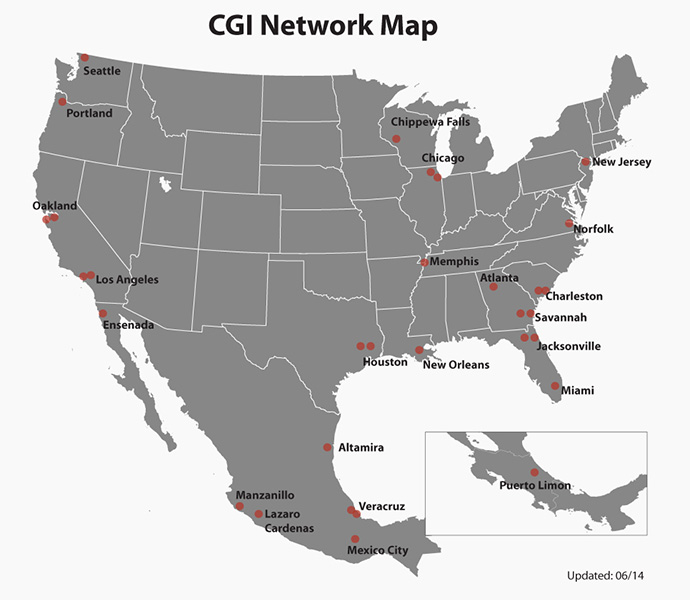
Recovery, Remediation, Reuse
Galvin calls SG Blocks structures “a very opportunistic product.” And opportunities sometimes come from hardship, such as Superstorm Sandy. He says SG Blocks was engaged by construction manager Hunter Roberts on behalf of developer Howard Hughes in helping South Street Seaport in New York inch its way back from the storm by creating a retail and food and beverage environment as the long-term rebuilding process unfolds.
Before SG Blocks, Galvin was a social entrepreneur, and he is looking for a corporate or charitable partner to work with his firm to pre-position assets before a major event such as a hurricane, as FEMA is not statutorily authorized to do so.
“With Hurricane Katrina,” he explains, “the biggest problem was the distance first responders had to travel. We could do things on tiles or foundations, get structures delivered within hours of an event and provide a base of operations for everybody who plays a role,” from emergency, utility and medical personnel to media to something as mundane but necessary as a place to charge mobile phones. “If you’ve ever been in a container structure, you feel this overwhelming sense of physical security,” he says. “In the aftermath of an event, one of the first things people need is a sense of physical security, and we provide that.”
Galvin says this model could apply to any site where planning or environmental remediation has a three-to-five-year timetable.
“When the future use arrives, we can disassemble and relocate,” he says. “We call that an activation service. Some properties have an inherent value, by generating revenue during a pre-construction or hold period.” The model also serves retailers and food and beverage companies looking to test market a concept without committing to major real estate.
“There is so much stress on the corporate office and CFOs to deliver turns,” observes Galvin. “Balance sheets are littered with properties and structures they’ve inherited – markets change, demographics change, and highest and best use changes. With our product you could potentially lease a piece of property in a new market or lease in a secondary or tertiary market, and we can create a smaller-footprint store or restaurant for you to test the market. It’s easily expandable. If the decision didn’t work out, you could have an exit clause in your lease and relocate.”
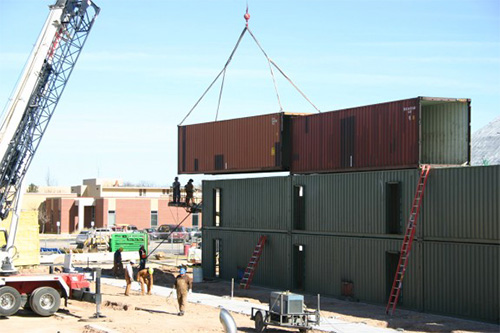
Asked if SG Blocks structures are serving the needs of crew camps in energy boom territories such as North Dakota, Galvin says, “They’re in our pipeline. Remote work locations offer an opportunity to scale a community as they expand.” And that means not having to carry the real estate and facility cost of a huge site footprint while you wait for it to fill up with people.
Galvin says SG Blocks is working with a couple large companies to design products for server farms and data centers. And biopharma, already used to modularization of labs, could be another promising market.
“Server farms occupy an enormous footprint,” he says. “Our product can house any kind of equipment, and densify vertically, so that if we can stack these servers one on top of another, we reduce the overall cost of the project. If the land is owned, you can get that land back and do something with it.”
For now, the two companies are happy to be doing something with literal boatloads of containers.
“To this day, we still send out a lot of empty containers,” says ConGlobal’s Mike Baldwin. “Frequently we see a ship leaving for China with half of its containers empty. That was part of the whole desire to find other uses for these containers.”
Government regulations may help the business case too. Baldwin notes new building regulations that just went into effect in Marin County, Calif., that are geared specifically for sustainability.
“Things like container construction will fit so beautifully,” he says.
And it just so happens those containers fit beautifully together.
“Containers,” he says, “are just like LEGOs. Big, giant, structurally sound LEGOs.”