Would you rather reshore operations to the US because of the business case, or because the President-elect told you to?
“Obviously because of the business case,” says Harry Moser, founder of the Reshoring Initiative, in response to an inquiry from Site Selection following President-elect Donald Trump’s assertion that he’d personally convinced corporate leaders at Carrier (part of United Technologies) to keep 1,000 jobs in Indiana instead of offshoring them.
“One problem is that about 60 percent of companies do not calculate the business case correctly. They look only at the wage rates or the ex-works prices and ignore the other costs, risks and strategic factors that go into total cost of ownership, missing 15 percent or more of the offshoring cost. So when the president calls, they probably sharpen the pencil, do the business case accurately and conclude they can stay.”
Moser’s organization has designed a TCO Estimator (found at www.reshorenow.org) for companies to quantify all of those costs, risks and strategic impacts of offshoring.
“You may find that you will actually be more profitable staying in the US,” he says. “It may be better to do the math today, than to get a call from President-elect Trump tomorrow. The real challenge is for President Trump and Congress to implement policies that make the US the most profitable location to produce for the US market, eliminating the need for interventions.”
Retrenching and Robots
According to Moser, policy actions should include: massive skilled workforce training, lower corporate tax rate, a value-added tax (VAT) as in Europe, reduced regulations, reduced healthcare costs and fairer trade agreements. By balancing the $800-billion-per-year manufactured goods trade deficit, the US will add 5 million manufacturing jobs, an increase of 40 percent, Moser asserted in a press briefing in fall 2016.
Some of those jobs might be going to robots. But a new report from the Frankfurt, Germany-based International Federation of Robotics says automation actually helps create US jobs.
“In the last six years, (2010–2015), the US industry has installed around 135,000 new industrial robots,” said the IFR’s World Robotics Report, released in November. “The principal driver in this race to automate is the car industry. During this same period, (2010–2015), the number of employees in the automotive sector increased by 230,000.
“The industrial renaissance in North America continues unabated,” the report continued, projecting growth in robot shipments to NAFTA of between 5 percent and 10 percent annually. “The main driver of this growth is the ongoing trend to automate production in order to strengthen the competitiveness of American industry globally, to keep manufacturing at home, and, in some cases, to bring back manufacturing that had previously been outsourced to other countries.”
Jeff Burnstein, president of the Robotic Industries Association, noted the penetration of robotics into life sciences, warehousing, and semiconductor and electronics manufacturing, as well as among medium-sized companies “who see robotics as a key factor in improving productivity and product quality in order to stay globally competitive.”
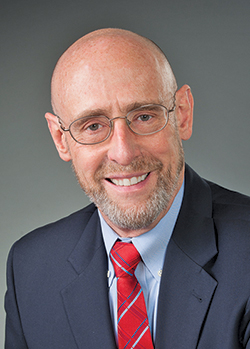
Harry Moser agrees with the IFR’s observations. But he has some ideas of his own.
“The world is automating, e.g. China is installing more robots/year than we are,” he says. “So we either do not automate and thus lose jobs to the countries that are automating and have lower wage rates, or we automate and save most or all of the jobs. Thus automation either keeps or adds manufacturing jobs here. Either case is better than losing them.”
As for investment, “actually, we have been underinvesting in automation, partially due to offshoring,” Moser says. “An increased rate of capital investment in the newest manufacturing technology is essential to increasing productivity. Capital investment will occur when capacity utilization is high. Capacity utilization will be higher when manufacturing output rises beyond the current trend line. The most direct way to achieve such output increase is to eliminate the trade deficit, increasing US manufacturing by about 25 percent, requiring an approximately 25-percent increase in annual capital investment for 20 years. The most direct way to reduce the trade deficit is to substitute domestic production for imports, i.e. via reshoring and FDI.”
Moser says the trend toward automation and advanced manufacturing favors the US vs. low-wage countries in several ways, including fewer labor hours per unit of output; a shift of the labor force to a higher percentage of high-skilled workers; cost structure shifts (“equipment costs are often higher in China because of the VAT tax on imports and generally higher tariff rates”); and quicker production and delivery.
Counter-Intuitive Case Study?
A team from National Center for Defense Manufacturing and Machining (NCDMM), The Boeing Company, and Southwest Research Institute (SwRI) in San Antonio, Texas, in December was awarded a $6.7-million contract to help the U.S. Air Force develop software and technology to make advanced robotics reusable for a variety of aerospace manufacturing and maintenance processes. Boeing’s technology center in South Carolina will provide equipment. But are there jobs?
“ROS-Industrial is an open-source robotics platform that is making advanced manufacturing and automation more accessible around the world,” says SwRI spokesman Robert Crowe, noting that SwRI leads the ROS-Industrial Consortium. “There is quite a large community involved in the development of robotics software using ROS-I in the US, Europe and now the Asia-Pacific region. There are actually a lot of tech job opportunities created in the ROS-Industrial space for coders and software engineers who are designing robotics automation. There’s also a lot of training that goes into implementation at the factory level.
“That’s a good counter-intuitive job creation story,” he says.