Logistics facilities seem to be growing as fast as children: Every time you see them they’re bigger and taller.
New research from Cushman & Wakefield says you’re not imagining things.
“Innovations in materials handling technology have created a demand for higher clear height in warehouses and distribution centers — specifically from e-commerce occupiers who want the latest generation of logistics space,” says Ben Conwell, senior managing director & e-commerce practice leader, Americas, for Cushman & Wakefield. His colleague Jason Tolliver, head of Logistics & Industrial Research, Americas, agrees.
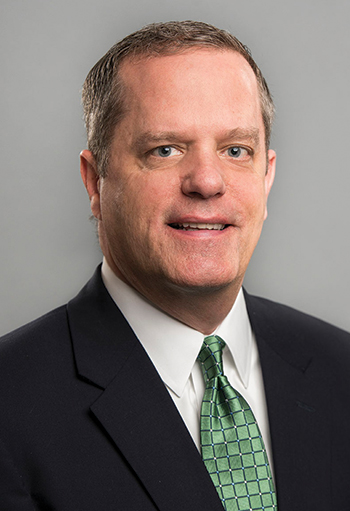
“The growth of e-commerce will continue to drive distribution center design, including ceiling height,” says Tolliver. “It remains the case that for many traditional warehouse occupiers, higher clear height and modern functionality are not as critical to success. But for occupiers competing in an omni-channel world, building functionality can be the difference between success and failure, bankruptcy or profit. As a result, commercial real estate and its attributes will increasingly be viewed as strategic assets driving revenue growth, not a cost center detracting from it.”
“While Amazon was an early demander and adapter in enlarging the cubic space of industrial assets, they aren’t the only company taking advantage of the additional space,” Conwell says. “Companies from Wayfair to Walmart are all specifying larger, taller buildings to increase cube and throughput.”
We shouldn’t expect that trend to just continue, however.
“Right now, fire and life safety regulations and associated costs have defined a general upper limit in building heights,” Conwell says. “It is possible to create additional cubic space, but the cost step-up is more than linear. For speculative development, we see 40 feet generally staying the upper limit, at least for the time being. If history is any indication, as the technology continues to advance, that number will certainly rise.”
Cushman & Wakefield Report Highlights
Over the past 20 years, the average rentable building area (RBA) for newly delivered warehouse product has increased by 60 percent nationally to an average of 268,000 sq. ft. (24,897 sq. m) today. The desire to optimize cubage has also resulted in buildings growing taller, with subtleties existing by size segment.
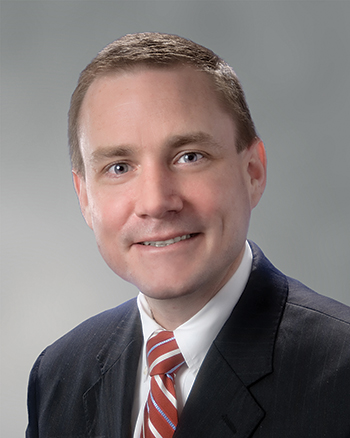
Twenty years ago, the average clear height for a new warehouse was 25 ft. (7.6 m.). Today, in newly constructed product larger than 300,000 sq. ft. (27,870 sq. m.), 32 ft. (9.7 m.) is typical. In mega-sized buildings, 36 ft. (11 m.) is common, with clear heights rising past 40 ft. (12.2 m.) in some cases.
Many traditional industrial tenants do not require higher clear height for pallet positioning, but the clear design trend is to raise the roof to 32 ft. or higher to garner the interest of a larger pool of occupiers. Since 1997, the largest concentration of taller building construction has occurred in distribution-intense markets like the Inland Empire, the Pennsylvania I-81/I-78 Distribution Corridor, Chicago, Atlanta, New Jersey, Dallas/Ft. Worth, Cincinnati, Columbus, Baltimore, and Kansas City, among others.
For developers, there is a tradeoff between the need for optimal clear height inside and the desire to minimize a building’s overall height-associated costs. Three of the primary cost drivers are slab, structure and fire protection.
As clear height exceeds 32 ft., the flatness of the slab surface itself may require tighter specification to ensure the stability of the rack. Column spacing often must be increased to accommodate the larger forklifts needed to reach the taller pallet positions, and if exterior walls are load bearing, they will likely get thicker. Fire protection systems may need to be upgraded. And if storage height exceeds 40 ft., in-rack sprinklers might be required which can increase costs during tenant rollover if they must be removed for the next occupant.