When exactly did a robot or a software application start gunning for your job?
Was it when Apple and Samsung supplier Foxconn announced in May that it had replaced 60,000 factory workers in China with robots?
Was it when fast-food giant Wendy’s announced that same month that it would replace cashiers with automated kiosks for taking customers’ orders at its restaurants?
Or was it when global shoemaker and sports apparel firm Adidas said in late 2015 that it would pilot a new automated manufacturing process in a facility called a Speedfactory?
None of the above, you say? You don’t work in a fast-food restaurant or a low-wage factory, you say?
Think again. The same forces that are at work to displace the jobs of low-wage workers are also at work, long-term, to displace many advanced manufacturing and white-collar jobs.
As robots and automation disrupt everything from mobile device manufacturing to financial services, the inevitable pink slip is coming for almost any job that is routine, easily replicable or low-skilled. And the color of your collar won’t matter.
If failing to prepare is preparing to fail, then hundreds of millions of workers who are doing little to nothing to upgrade their job skills around the world are racing toward a rude awakening.
Just because you’re not handed a pink slip tomorrow or sometime later this year doesn’t mean you should feel safe, says Martin Ford, author of New York Times bestseller Rise of the Robots: Technology and the Threat of a Jobless Future and founder of a Silicon Valley-based software development firm.
“Some of the first jobs to fall to white-collar automation are sure to be the entry-level positions taken by new college graduates,” Ford writes in his breakthrough 2015 book. “There is already evidence to suggest that this process is well underway.”
‘Forces Moving Faster than Anticipated’
In an interview with Site Selection, approximately one year after he released his book, Ford said that, if anything, he underestimated the speed and impact of the impending tsunami of job displacement due to robots and automation.
“These forces are moving faster than what I had anticipated,” Ford says. “In my book, I said that self-driving cars would be here in about 15 years. But there are companies out there right now who say that they will have them on the road next year. Foxconn has already automated an entire factory in China and eliminated 60,000 jobs. There is not really a discernible endpoint to this. It will just keep going. Technology will just keep getting better and better.”
News from the International Federation of Robotics (IFR) on June 22 confirmed this trend. Worldwide sales of industrial robots achieved a new record number of 248,000 units in 2015, representing a 12-percent increase from 2014, according to the 2016 World Robotics Statistics report issued by IFR.
“This sees the continuation of the global automation boom, which commenced in the wake of the financial crisis in 2009,” the report states. “The sales figures for industrial robots have increased almost four-fold since that time. There is no end in sight for this growth trajectory. By 2018, 2.3 million units will be deployed on factory floors, more than twice as many as in 2009.”
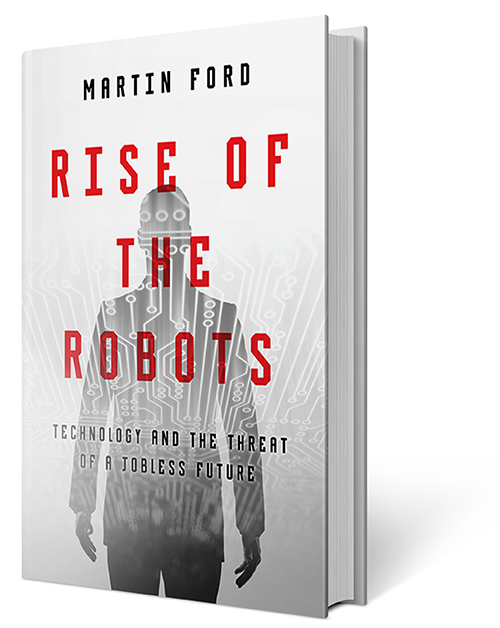
At the same time, the robotics avalanche is colliding with the Internet of Things — a phenomenon that will see 6.4 billion smart, connected things in use globally by the end of 2016. According to Gartner Inc., that represents a 30-percent jump from 2015.
The tidal wave swamping over our world won’t be confined to shoe factories, mobile device makers or even advanced automotive assembly plants like the one seen in the 2002 Steven Spielberg sci-fi classic Minority Report, contend the people who study job trends for a living.
Rather, it will reach the ranks of highly paid professionals who once thought they were immune, says John Boyd, founder and principal of The Boyd Company Inc., a Princeton, New Jersey–based site consulting firm.
“The adoption of robotics in the white-collar workplace is definitely something that is impacting our clients as well as how we will be approaching certain site selection engagements,” Boyd says. “The epicenter of this growing, white-collar job-shedding phenomenon is a sector that our firm has been very active in over the years, namely the banking and financial services industry, with clients like JP Morgan Chase, BNP Paribas, PNC Bank, TD Bank, Sun Life Financial, Visa International, Progressive Insurance and others. Looking ahead, our firm is projecting that a full third of all banking jobs will be eliminated over the next decade due to advances in technology and robotics applications. Most of these will be white-collar support jobs in back-office settings and at the retail branch level.”
What This Means for Site Selection
Traditional banking is not the only industry under siege, but in many ways it’s the “canary in the coal mine,” says Boyd.
“The financial services sector is going to be impacted the most by automation and robotics, and the white-collar job losses will be the most severe,” Boyd says. “Looking ahead, overall corporate back-office relocations are going to be smaller and less labor-intensive and will be putting more of a premium on intellectual capital rather than some of the more mundane clerical-related aspects of running a back-office facility.”
He adds that “infrastructure requirements will be putting more of a premium on high-speed fiber and sophisticated telecommunications techniques, continuity of operations and insulation from natural and man-made disasters — factors more commonly linked to our data center site selection projects than traditional back offices. Energy costs and the reliability of the grid will also play into the equation more than ever before for back-office relocations due to the growing use of automation and robotic applications.”
The potential cost savings for banks are enormous. “We have seen figures that point to robotic process automation costing 50 percent less than a worker in the Philippines and 34 percent less than one in India,” Boyd says. “In the more developed world, for a full-time back-office worker in the US, the cost savings could be as high as 90 percent — based on an assumed back-office salary of $45,000 per year.”
In short, here’s what the coming wave of robotics means for site selection: Locations will no longer be able to compete largely on the basis of low wages and low overall costs. As robots and other forms of automation become cheaper, companies will have little incentive to choose low-cost countries or cities.
The most competitive locations will be those that offer the largest amount of highly education, technical, STEM-proficient workers who can easily adapt to rapid advances in technology and automation.
Locations must act quickly to determine whether their “target industry sectors” will be viable entities in the future. If you’re a location banking on the job-growth prospects of low-to-middle-skilled manufacturing operations, your economic development plan is going to have a very brief shelf life.
There is an opportunity right now for locations to seize upon emerging industry sectors that are ripe for growth, particularly in certain software-driven fields that tend to command the most creative talent.
Why Some Locations Will Prosper
The FinTech sector is one such field, notes Boyd. “Just as the financial services sector is jettisoning white-collar jobs due to automation and robotic technologies, its protagonist industry — financial technology — is booming with investments this year alone of some $20 billion,” says Boyd. “It is one of the leading growth sectors these days in the site selection field, with hot spots like San Francisco, Silicon Valley, Atlanta and Omaha.”
In fact, the same factors that drive FinTech operations to these high-tech locations — large concentrations of knowledge workers; access to venture capital; presence of software development workers and code writers; and all the amenities demanded by highly educated millennials — are turning places like Pittsburgh into 21st-century industry magnets.
Red Whittaker, a world-renowned roboticist who serves as chief professor of robotics at Carnegie Mellon University and founder and CEO of Astrobotic in Pittsburgh, says that Pittsburgh has the right combination of technical talent, capital, ingenuity and advanced manufacturing prowess to become one of the leading centers of robotics on the planet.
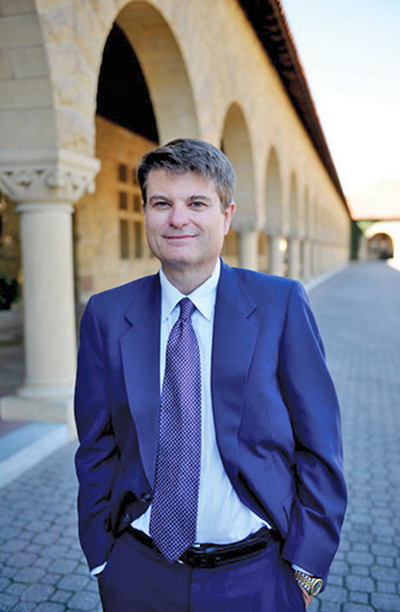
“I chose Pittsburgh for the development of robotics very consciously,” says Whittaker, who’s leading a team of scientists engaged in a competition to win the $20-million Google Lunar X Prize for landing a robot on the moon and sending video of its landing back to earth. “I looked at a lot of other cities. Pittsburgh has a great technical base. It was very affordable, and people could come here from anywhere. I considered Seattle. I looked at the Bay Area. I looked at Austin and Atlanta and Detroit. In the final analysis, all of the computing and software expertise needed for a robotics cluster were here. You absolutely need a first-tier community for that, and that is exactly what I found in Pittsburgh.”
Whittaker says the advances in robotics will impact every aspect of the traditional manufacturing and distribution supply chains. The real estate implications are immense. “There was a day when square footage mattered,” he says. “Not anymore — 3D printing is revolutionizing the way that very-small-batch productions are made. You can print so many materials now. You can actually get production finishes by printing now.”
Embrace Robots or Be Obsolete
Roger Quinn, the Arthur P. Armington Professor of Engineering at Case Western Reserve University in Cleveland, says there are a handful of places in the US that have already staked out a competitive edge by establishing industry-leading robotics clusters. These include San Jose, Pittsburgh, Boston, Atlanta and Cleveland — all places that have world-class research universities centered around science and engineering.
“The San Jose area has a lot of robotics startups,” he notes. “Several of my students have received jobs there. San Jose has an insatiable appetite for Ph.D.s in robotics right now. Major universities around the country are growing their robotics clusters. Companies want these workers. Uber stole a lot of the CMU staff in robotics.”
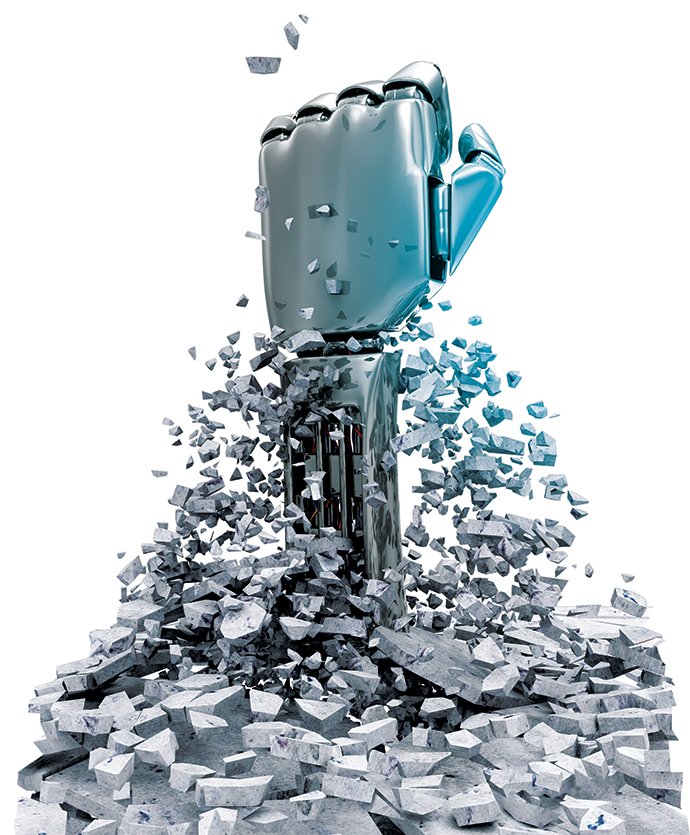
Martin Ford says that proximity to markets will trump costs as a prime location factor. “The cost of labor will be less important,” he says. “You will no longer place your plant reflexively in a low-wage country. It will make more sense to place your factory close to the marketplace.”
He even adds that “it might revitalize manufacturing in Detroit because the cost of labor will be less important. Established factories will be retooled. The real question is, what happens to all of the countries that have relied on low-wage workers for so many years? We are entering an age when that will not be viable anymore. How will those countries gain wealth in the future?”
Ford says that CEOs and others who ignore the ramifications of the robotics wave are doomed to fail. “There is no choice,” he says. “You need to embrace this technology or you will be at an extraordinarily competitive disadvantage. This has implications for all of society.”
Ford encourages companies to invest more into education. “The economy needs workers,” he says. “We have skill mismatch issues. Nearly half of the people who graduate from college today end up in jobs that are not even relevant to their degree. We must encourage young people and older adults alike to pursue occupations that rely on creativity. To be competitive in this new job market, you must have the ability to keep on learning and be flexible.”
The bottom line, he says, is that “the rise of artificial intelligence is going to be the biggest thing that is going to happen over the next decade. This will be the biggest force to impact your business, and it will become obvious very soon.”