Since its inception 27 years ago, the national Hollings Manufacturing Extension Partnership (MEP) network, part of the US Dept. of Commerce’s National Institute of Standards and Technology (NIST), has worked with nearly 80,000 manufacturers. That work has led to $88 billion in sales and $14 billion in cost savings, and the creation of more than 729,000 jobs. More than a few thousand of those jobs have sprung up in the Southeast.
MEP national advisory board member Thomas M. (Tommy) Lee, president and CEO of aluminum manufacturing firm Vulcan, Inc., is a former Alabama Power engineer whose Baldwin County company has benefited a number of times over the years from Alabama’s MEP program, the Alabama Technology Network. Part of the Alabama Community College System, ATN has 12 Centers, satellite offices throughout the state and three contract centers at 4-year universities.
“We have used ATN many, many times for manufacturing training, wall-to-wall safety inspection work, lots of different functions,” says Lee, whose company is in the midst of doubling its aluminum mill capacity. “It’s eye-opening work they do at NIST. We have to do a better job, however, of getting the technology and opportunity that are there for small and medium-sized manufacturers pushed down to them.”
The MEP advisory board has created a subcommittee on technology acceleration to improve that process — in much the same way MEPs improve manufacturing processes nationwide every day. That work is unfolding as all 50 state MEP centers are re-competing for that status, thus drawing awareness to the program as a whole. The evaluation process will be done by year’s end.
ATN is a great model, in part because it’s one of only eight MEPs nationwide to operate across a statewide network of locations. Its team, says Lee, “has done a terrific job of leveraging state and federal dollars,” and works hand in glove with the state’s Alabama Industrial Development Training (AIDT) agency. ATN often provides services in the areas of industrial maintenance; quality engineering and systems; lean manufacturing; environmental, safety, and health programs; IT and employee development to new companies coming to Alabama through AIDT.
Site Selection asked the leaders of state MEP centers across the Southeast to respond to three questions.
Chester Vrocher
Director
Alabama Technology Network
www.atn.org
In rural Alabama (a town with less than 6,000 people), the local economic developer (ED) is currently recruiting a company from China. The company has made several visits to the location and has given it favorable reviews. As with any company moving from China to the US, the dramatic disparity in wage rates is often a roadblock and inhibits further discussion. The local ED reached out to ATN to assist in creating the economic viability study for the potential new plant. ATN staff met with the company, site selector and ED to discuss further options.
The decision was to investigate potential production improvements that could be made should the company relocate a plant to Alabama. To complete the assessment, ATN recommended that one of its staff, a nationally certified Lean Engineer, visit China and recommend solutions to solve the economic situation. The local ED accepted the concept and volunteered to contract and pay ATN directly for the travel and expert costs (an enormous fiscal commitment for a rural county). The Lean Engineer traveled to China, visited multiple sites, and made recommendations for the company to implement within the new Alabama facility. Negotiations are still ongoing with the potential client and the local EDA.
The ATN Staffer was local to the proposed site, less than 40 minutes away. Should the company locate in Alabama, ATN and this staff member would already have an existing relationship with the company and could assist in many ways. ATN has multiple sites throughout the state, staffed by employees residing near each location. This is a major advantage for ATN and Alabama.
As the economy has returned, many employees who postponed retirement due to the recession are now retiring in vast numbers. One industry sector in a rural section of the state expects a need for 5,000 to 8,000 employees over the next 10 years. Compounding the issue is that most manufacturers have modernized their facilities to improve profitability. New entry-level employees are not equipped with the skills to operate the production processes.
Recently, a chemical company requested assistance from the State of Alabama to address this issue. The company expects to lose over 75 percent of its workforce (300-plus employees) in the next 5 years. Since Alabama does not offer incentives for attrition, ATN was asked to provide a solution. The company requested a training program that would cover subjects including math concepts, production parameters, chemistry, operating procedures, safety, quality and machinery. In total, each new employee will receive over 120 hours of classroom and hands-on training onsite prior to beginning work. The company has accepted the concept of new-hire training and has contracted with ATN to begin the process in the fall of 2015.
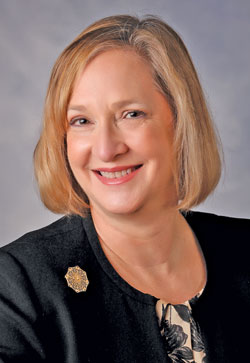
Karen J. Fite
GaMEP Director
Enterprise Innovation Institute Georgia Tech
www.gamep.org
www.innovate.gatech.edu
Crider Foods, a canning and frozen/fully cooked poultry manufacturer in Stillmore, Ga., is a 60-year-old family business. In anticipation of the company’s aggressive growth plan, Billy Crider Jr. knew he had to make a few key changes in warehouse space and in the packaging and canning lines. Crider was operating three warehouses, one attached to the plant, one that was on the grounds of the plant but disconnected from the facility, and one 25 miles away in Vidalia, Ga., that required transportation of product several times a day, and the employment of a person to load and unload trucks. In addition, Crider was operating two packaging lines, utilizing older equipment that was operating seven days a week and 22 hours each day, four more hours a day than the canning line, creating a bottleneck.
Crider had seen opportunities within new markets, but could not reach them because of capacity issues. He asked his team to call on Alan Barfoot, the Central Georgia region manager for the Georgia Manufacturing Extension Partnership (GaMEP) at Georgia Tech. The region is one of nine in the GaMEP network. Barfoot determined that having three warehouses, including two off-site, was inefficient and costing the company time, resources, and money for space rental and travel costs. Knowing that the company needed to build a single warehouse that could house everything, Barfoot began determining how much space Crider would need. He met with the company’s sales and marketing team to review and log every SKU and forecast the amount of inventory needed to be stored. By working through these numbers, Barfoot was able to help determine the need for warehouse capacity, utilization of racks in the new warehouse space, types of storage methods, and the forklift truck and picking equipment that would be needed. Crider built its new warehouse and was not only able to save time and money, but was also able to reassign the one Vidalia employee to the Stillmore plant.
Next Barfoot and Steve Jarrard, one of Crider’s operations managers, led a team to conduct a value stream map of the packaging process. Crider decided to not only replace the machines on the two lines, but also to add a third line to allow for business growth. By making these improvements, Crider Foods:
Saved time, resources and money by eliminating traveling 50 miles round-trip multiple times a day to the off-site warehouse.
Combined three separate warehouses into one efficient warehouse space.
Doubled throughput from 260 cans a minute to 520 cans a minute.
Increased plant capacity to allow for expansion into new markets and new opportunities for existing customers.
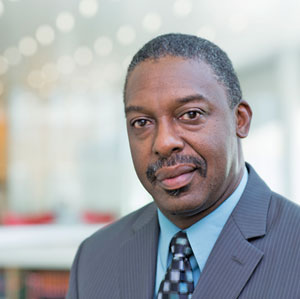
Phil Mintz
Director
North Carolina Manufacturing Extension Partnership
www.ies.ncsu.edu
NCMEP was recently involved in a manufacturer recruitment effort of a specialty furniture assembler. The target county for this new plant has struggled for several years through the effects of continued weakness in traditional manufacturing industries, including textiles and furniture. The center now routinely collaborates with the state’s economic development unit to provide a wider range of incentives and assistance for companies considering expansion.
As the discussions progressed, it was discovered that NCMEP had led a successful project with an established sister plant in another part of the state. As a result, we were able to assist in the negotiation of a NCMEP continuous improvement project as part of the recruiting proposal. The company representative referred to this particular project as a deciding factor in the new plant expansion, which is expected to bring over 150 need jobs to the area.
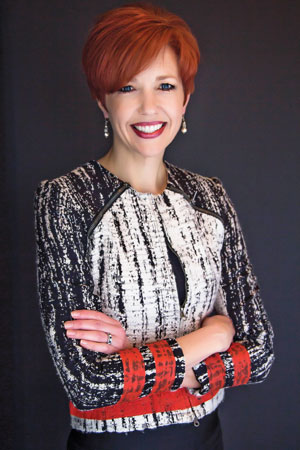
Jennifer Hagan-Dier
Director
University of Tennessee Center for Industrial Services
Tennessee MEP
www.cis.tennessee.edu
In November 2014, the regional UTCIS solutions consultant, Dwaine Raper, was contacted by John Campbell, director of AccelNow (the Northeast TN Entrepreneur Accelerator) to inquire about university assistance for Per Vivo Labs (PVL), a US Department of Veterans Affairs-certified Service-Disabled Veteran-Owned Small Business. The company had been successful in establishing trial sales with the U.S. Army. However, the Procurement Agent needed PVL to provide some product performance validation testing results, before they could recommend the Polar Skin Product as the primary thermoregulation solution for the U.S. Army.
The UTCIS Solutions Consultant arranged for Gajanan Bhat, Ph. D. Director of the UT Knoxville Nonwoven Materials Research Laboratory (UTNRL) and Professor in the UTK Department of Materials Science & Engineering, to help PVL with the effort of developing and conducting an applicable product performance validation testing protocol. The objectives of the testing were to evaluate the permeability, wetting, and drying characteristics of the Polar Skin product, along with the capillary wicking and cooling performance. The testing results validated the superior performance of the Polar Skin product in comparison to the existing solution (a wet cotton bed sheet). Additionally, UTCIS and its PTAC Program are assisting PVL in its pursuit to be the selected heat related illness solution for all of the DOD.
As a result of the collaboration, sales increased by 980 percent in 2015 over 2014 sales, to an estimated $598,000, and six jobs have been retained.
“From initial contact to finished product the collaboration process was smooth and efficient,” said Per Vivo President Russ Hubbard. “Our expectations were far exceeded and the level of communication was spectacular. We intend to continue to work with this team to continue to grow our business.”
Walker Die Casting is a major employer and corporate citizen in the city of Lewisburg. Many Tennessee manufacturers are finding that ISO 9001 and ISO 14001 certifications are key to servicing a greater number of automotive companies as the industry grows in the Southeast. Recognizing this, Walker Die Casting contacted the local Tennessee Manufacturing Extension Program (TMEP) for assistance in updating and fully implementing an ISO 14001 environmental management system. The final deliverable of the project was to complete Walker Die Casting’s ISO 14001 registration, which would satisfy new requirements from one of its major customers. Results attained due in part to this project included increasing sales from $18 million to $25 million, retaining 15 jobs and adding 15 new jobs.
“When as an industry you have a need to address a problem, it is nice to have a place to go where you can find the skill sets you need to address those problems,” said Tom McCormack, director of quality for Walker Die Casting.
Chester Vrocher, ATN: ATN has partnered with the Alabama Automotive Manufacturing Association (AAMA) to provide training to its members since its inception in 2001. This year, ATN has created a yearlong training program for AAMA members, with much of the training targeted to automotive-specific concepts, particularly the core quality tools required by OEMs. Such programs as FMEA, SPC, TS 16949, and APQP are being offered at different locations throughout the state in an open enrollment format.
Karen Fite, GaMEP: GaMEP, in partnership with the Georgia Center of Innovation for Aerospace, the Georgia Small Business Development Center and the Georgia Department of Economic Development held a Supplier Development Conference for the Aerospace Industry in Macon in 2014. The 2014 conference drew more than 120 attendees from 89 manufacturing companies from 33 counties across the state. The success of pairing these suppliers with the OEMs drove the GaMEP and our partners to launch a similar conference in 2015 in Savannah. In September 2015, Lockheed, Gulfstream, Boeing, and more OEMs will be on hand to meet with new suppliers to continue to increase the supply chain in Georgia.
Phil Mintz, NCMEP: We have developed programs such as Executive Peer Councils, Lean Improvement Councils and Manufactured in North Carolina (MNC), a program that provides opportunities for companies to more fully develop their supply chains and identify potential buyers for their products. The MNC program provides multiple tools and resources that includes: a free Web presence; a searchable database with Internet exposure to state, national and global markets; expert content creation and editing that uses search engine optimization best practices; and one‐on‐one instruction so manufacturers can revise and maintain their own content.
Jennifer Hagan-Dier, Director, University of Tennessee Center for Industrial Services, Tennessee MEP: The Nissan Supply Chain Quality Development Program is a partnership between UT CIS and Nissan North America to address quality issues in their supply chain. This is a great program that is a “grassroots” developed program between UT CIS and the OEM, and I am not sure there are any other programs like this in the country.
Developed, coordinated and managed by UT CIS, and delivered by resources from UT CIS and other NIST MEP Centers — including the Center for Advanced Vehicular Systems (CAVS) in Mississippi and Michigan Manufacturing Technology Center (MMTC) in Michigan — the program specifically addresses issues identified by Nissan as important to supply chain quality, growth and development through a combination of open enrollment classes, in-plant training sessions and individual supplier projects.
Development of The Nissan Supply Chain Initiative began in early 2013 as a result of Nissan’s desire to differentiate itself from its competition with high-quality cars and extremely low defect rates. UT CIS and Nissan worked together to identify and prioritize quality issues and challenges across the supply
chain in light of Nissan’s increasingly aggressive quality goals. Nissan’s quality goals for the 2015 fiscal year include a 16-percent reduction targeted across warranties, defects and recalls.
The program was officially launched in Tennessee in June 2013 with the first of six modules — Potential Process Failure Mode and Effects Analysis (PFMEA)/Control Plans — and has since expanded to Mississippi and Michigan.
Pursuant to an agreement with Nissan, UT CIS has exclusive rights to coordinate the delivery of the materials jointly developed by UT CIS and Nissan to Nissan suppliers in the United States for two years from the launch of each module of the program.
Chester Vrocher, ATN: ATN is a workforce development program in itself. ATN is also involved in multiple programs at all levels. Here are a few examples.
- MBUSI has the Mercedes-Benz Mechatronics and Automotive Technician Program with Shelton State Community College in nearby Tuscaloosa. ATN is involved by providing instructors for some of the more advanced technical classes. Multiple ATN engineers have been assisting Shelton State for over three years.
- ATN has also been involved in BEST Robotics (Boosting Engineering Science and Technology) in Alabama for five years. BEST Robotics is a nation wide program to promote STEM education in middle and high schools. This effort has increased the number of Robotics teams in Alabama from 100 to over 250, with many in rural areas.
Karen Fite, GaMEP: In 2015 the GaMEP launched Faces of Manufacturing, a program to honor hard-working, dedicated people throughout the state who work within or are affected by manufacturing companies. By telling stories of these people, the GaMEP has been able to showcase manufacturing’s impact to Georgia communities and continue to promote manufacturing as a thriving industry within the state.
Phil Mintz, NCMEP: NCMEP has a formal relationship with the North Carolina Community College System. As part of that relationship, the center routinely plans and delivers individual worker skill training through the state supported Customized Industry Training program. Additionally, NCMEP has provided technical support to a regional workforce development board helping them with layout planning of an Industry Training Center supported by local manufacturers who will use the new center in order to better prepare students for in-plant work.
Jennifer Hagan-Dier, Director, University of Tennessee Center for Industrial Services, Tennessee MEP: LIFT (Lightweighting Innovation for Tomorrow NNMI) Workforce and Education Working Group. I, as the TMEP Director, sit on the LIFT Workforce and Education Working Group, and we are developing workforce projects for each state in the NNMI area, including Tennessee.