Stephen Moret, president and CEO of the Virginia Economic Development Partnership, knows how crucial Hampton Roads is to the Commonwealth’s economy. And even though “Roads” refers to roadsteads — the region’s historic and valuable network of sheltered waterways — the landside roads matter too.
“The region is currently investing $11 billion in land transportation infrastructure, including over $5.8 billion in interstate system expansion and improvements,” he says, backed in part by a special gas tax the region passed a decade ago. With 11 localities serving as the beating heart of the mid-Atlantic economy, it pays to keep the arteries up to date.
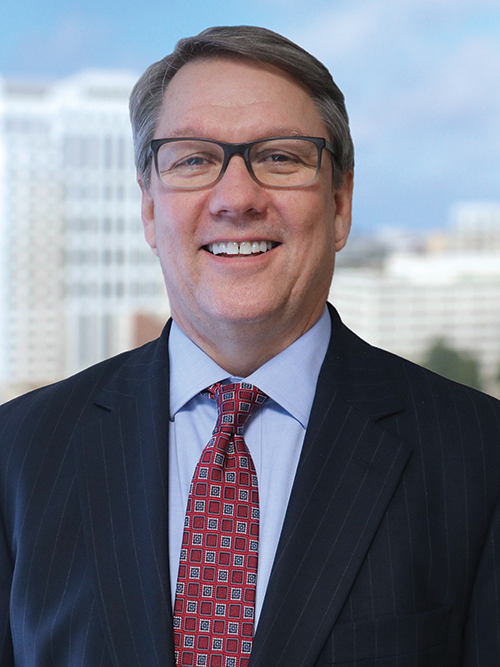
“The I-64 Hampton Roads Bridge-Tunnel, a major thoroughfare in the region, has long been one of the region’s most congested corridors,” Moret says. “The existing 3.5-mile facility consists of two two-lane immersed-tube tunnels on artificial islands, with trestle bridges to shore.” The $3.5-billion Hampton Roads Bridge-Tunnel Expansion Project will ease this congestion with the addition of twin two-lane bored tunnels just west of the existing eastbound tunnel. In addition, the four-lane segments of the I-64 corridor in the cities of Hampton and Norfolk will be widened.
It’s a good thing. If you think 100,000 vehicles per day during peak summer traffic is due to all the families heading to the shore, you’re only partly right. Such assets as the Port of Virginia, two Class I rail services and two international airports make this region a logistics magnet, attracting projects in recent months from such firms as Preferred Freezer Services (now Lineage Logistics) in Portsmouth, Total Fiber Recovery (Chesapeake) and Amazon, which this year announced on the same day a multi-story robotics fulfillment center at Northgate Commerce Park in Suffolk, creating 1,000 new jobs, as well as a 500-job processing center in Chesapeake.
“This announcement is a big win for the 757 and further solidifies the Hampton Roads region as a premier location for distribution-related business investment,” said Doug Smith, president and CEO of the Hampton Roads Alliance, the region’s lead economic development organization. (The 757 is the region’s trademark area code.)
Smith says the area’s distribution capabilities go well beyond its strengths in food & beverage and consumer goods. As Virginia’s offshore wind energy projects launch, “Hampton Roads is really well positioned to be home for supply chain for turbines and towers and blades, transporting, installing and then maintaining them,” he says.
Enlarge the picture even wider, and you can see the role of Hampton Roads getting bigger too, as part of the first ever comprehensive international trade strategic plan for Virginia announced by Governor Ralph Northam in November 2019. The plan calls for expanding the Commonwealth’s international trade output by 50% over the next 15 years.
A Port Like No Other
Recent international investors include Spanish olive oil producer Acesur, which is investing $11 million in a processing facility in Suffolk that will handle imports from Spain, Argentina and Australia. Joseph Fairchild, vice president of operations and director of purchasing for Acesur USA LLC, said Virginia was chosen over North Carolina “due to its market proximity, progressive infrastructure investment, as well as the Port of Virginia’s proximity to the plant.” Suffolk is where Ace Hardware first located its own redistribution center for the same reason, in 2011, and expanded in 2017.
Between FY2013 and FY2018 more than 250 businesses located or expanded their Virginia operations due to the Port of Virginia, which in 2019 helped generate more than 3,500 new jobs and the development of nearly 5 million sq. ft. of space that had a total investment value of $2 billion.
So it’s no surprise that the Port — already the third largest on the East Coast — is receiving investment. A $700-million project will expand overall container capacity by 40%. Dredging work started in 2019 will create the deepest commercial harbor and shipping channels on the U.S. East Coast by 2024.
“We’re not just going deeper, but wider,” says Russ Held, vice president of economic development, Port of Virginia. “For 14,000-TEU vessels now, it’s usually a one-way trip. This will give us the ability to run two-way traffic.”
The area’s shipbuilding heritage means Hampton Roads boasts a location quotient three times the national average in engineering, logistics and sheet metalworking — a strong factor in S23 Holdings’ decision this year to choose Newport News over Florida and Puerto Rico to invest $64.4 million and create 332 new jobs at a new corporate and industrial campus.
Only 2.5 hours to open sea, the Port is the only port on the East Coast authorized for 55-foot channel depths to handle the larger cargo ships of the future. The Port processed 2.8 million TEUs in 2019 — 13% of the coast’s market share. Expansions underway at the Norfolk International Terminal and Virginia International Gateway will add 43 container stacks and hundreds of thousands of TEUs to the Port’s capacity by the end of 2020.
Technology Pioneers
Among the Port’s incentives are tax credits tied to port volume increase; barge and rail usage; and international trade facilities expanding due to cargo transit increase. It also offers an economic and infrastructure development zone grant program (used by Amazon, among others). The expanding Port also is home to Foreign Trade Zone 20, where over $1.6 billion of total merchandise is received annually, and where companies produce more than $430 million in exports annually.
Among the lesser known aspects of the Port are its two inland terminals, and the possibility of container-on-barge service three times a week to and from the Richmond marine terminal. What’s more, 37% of cargo arrives and departs the port by rail — the largest such percentage on the East Coast. The Port is also an automation pioneer.
“Thirteen years ago was the first time they’d introduced automated marine operations in the western hemisphere,” says Joanne Jenkins, terminal services manager for the Virginia International Gateway (VIG) container terminal in Portsmouth, where between 10,000 and 15,000 containers a day are optimized and sorted. The Port was also the first in the U.S. to negotiate an agreement with the International Longshoremen’s Association for working in an automated environment.
In 2019, The Port of Virginia completed a three-year, $312 million investment that doubled VIG’s container and rail capacity. VIG also incorporated the Port’s trucker reservation system called PRO-PASS® that is increasing productivity. Many drivers are making the dropoff and turnaround in under 40 minutes, enabling multiple turns in a day for some, with one driver recently making 10 turns in a day.
Having your warehouse within two minutes’ drive is one way to get that many turns. That was a big factor in Preferred Freezer/Lineage Logistics choosing Portsmouth over Savannah for its $60 million investment.
“These infrastructure improvements will only strengthen Hampton Roads’ position as a prime location for international connectivity and global business,” Stephen Moret says.
From what I learned during recent visits with company leaders in the area, the region already is a prime logistics hub with an appetite for growth.
SRP Companies, Virginia Beach
SRP is the granddaddy of them all when it comes to impulse purchases. From 5-Hour Energy, keychains and plush animals to neckties at the Smithsonian or sunglasses at the theme park because you left yours in the car, SRP is there for you. “The car charger at 7-11? That’s us,” says Dodd Duquette, senior warehouse manager for SRP. “I have 60,000 square feet of neck pillows in my facility right now.”
The Virginia Beach site consolidates six former sites into one, and is part of a national network of distribution centers serving 55,000 stores across the U.S. and Canada. Ninety percent of its inventory comes from China. Duquette says Virginia Beach won out over two other locations. The site will soon flip the previous company protocol which sorted goods in Salt Lake City for distribution to “spoke” facilities. “Soon I’ll be the hub and they’ll be the spokes,” Duquette says.
SRP’s analysis showed that the region from South Carolina up to Virginia Beach was a sweet spot for customer service. His hiring of the first 75 people proved out that projection. “Out of any place I’ve worked in 36 years, this has been the most successful ramp-up I’ve seen,” he says. “We’re building a different culture of empowerment and rewards. Then we’ll cut, copy and paste it across the country. When it’s all set, I get to bring in all the other DC managers and say, ‘Look what you can do.’ ”
Interchange, Portsmouth
The 200,000-sq.-ft. Portsmouth Logistics Center 20 minutes from the Port’s terminals is one of two terminals serving Interchange, a third-party logistics provider whose bread and butter is the food business — from orange peel for Blue Moon beer to heated caramel for Hershey. T. Keith Robinson, Interchange sales manager, says it was the company’s first building in the area, after years of experience in container drayage to inland facilities including the company’s home location in Harrisonburg. Of the company’s 23 facilities in the state, “this is our furthest location from our home offices,” Robinson says. “We’re considering another one down here.”
As for the Port’s truck system, “We have not had a single truck held up,” he says. “The check-in and check-out system is fantastic. They are money. They’ve expanded their hours with appointments, so guys aren’t wasting hours sitting in detention. Keeping those wheels turning is important, and they’ve done a great job keeping those wheels turning for us.”
Swisslog Logistics, Newport News
There’s so much goods movement in Hampton Roads, it’s a de facto hub for logistics-oriented technology too.
Bill Leber is director of business development in consumer goods and logistics automation for the Americas for warehouse automation company Swisslog, part of the $4 billion Kuka Group. “We put the business here because we made the cranes here,” he says of the operation’s origins as Munck Automation in the 1960s, “and Newport News Shipbuilding was one of the few certified welders in the region.”
Today the expertise is software and systems. Among the company’s national customers are Target, Walmart, Michelin, Medline and John Deere. “In our industry, we’re the only ones who have all the people who built and designed the system, as well as the spare parts, right behind this wall,” Leber says.
Haulotte North America, Virginia Beach
This French manufacturer of people and material lifting equipment opened its North American and Americas headquarters, distribution, parts fulfillment, warehousing, inspections and repairs complex in Virginia Beach in March 2016. Shawn Bone, U.S. general manager, says the company has invested tens of millions of dollars, “and we’re looking at some expansion opportunities in the Virginia Beach area.” Most overseas-made product is brought into Virginia Beach and distributed from there, with parts going anywhere from Canada to Chile. after past locations in Atlanta and Maryland, Haulotte has landed where it needed to be all along. “Proximity to the Port is why we picked the location,” Bone says.
Dollar Tree, Chesapeake
Since opening the first Dollar Tree store in the Hampton Roads area in 1993, it’s safe to say this company has grown exponentially across the nation. That includes 25 distribution centers, at a pace that is seeing a new one open every year. Harry Thetford, general manager, is a 29-year U.S. Navy veteran just two years in with Dollar Tree, so for him, it’s still “really fun to go into a Dollar Tree store and have a customer hold something up and ask, ‘How much is this?’ It’s a dollar.
“One of my passions has been to recruit veterans,” he says. “I run the DCs, so I’m looking for young sailors or Marines who did their three or four years, got out, and want to start their careers. Dollar Tree has a great reputation around here, so a lot of people call me.”
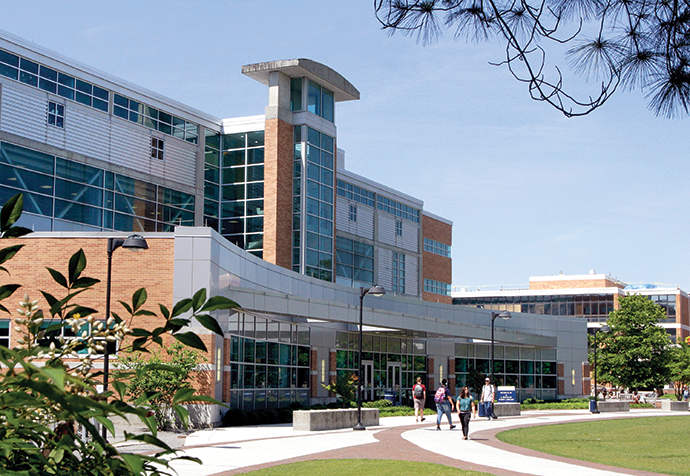
More than 14,000 ex-military transition into the civilian workforce in Hampton Roads every year.
The company is constructing a new headquarters campus at the Summit Pointe mixed-use development, chosen over Charlotte, North Carolina, after the company merged with Family Dollar. Employment at the HQ is projected to reach 2,600 in the next few years. Attached to the site are “DC1,” a 400,000-sq.-ft. facility that employs approximately 320, and a speculative office facility attracting strong interest.
Givens Trucking, Chesapeake
Founded by an international motorcycle racer with a penchant for winning nearly every race he entered, Givens owns and operate over 1.6 million sq. ft. of warehouse space at its six distribution centers, where 350 employees serve the needs of clients such as a major flooring company, a consumer electronics giant, a forklift manufacturer and an Austrian maker of motorcycle and ATVs — 68 customers in all. One of them is an engine manufacturer in North Carolina that receives up to 25 loads a day for its just-in-time system.
Among other sources of talent is the maritime and supply chain program at Old Dominion University in Norfolk. The site was granted U.S Foreign Trade Zone status in 1994.
“We’re a major beneficiary,” says Givens Director of Operations Trevor Dunlap, “of the port being successful.”
That’s a common refrain across the 11 localities served by the Hampton Roads Alliance, where the shipping channels run deep, and the connections run deeper.
This Investment Profile was prepared under the auspices of the Hampton Roads Alliance, the regional economic development organization representing 11 localities in a remarkable region centrally located on the U.S. East Coast. For more information, visit hamptonroadsalliance.com.