The locations where companies and workers can stretch their dollars the furthest.
Inflation has become household dinner table talk over the last few years, but its impact is both cumulative and real. A shrinking dollar makes everything more expensive. Whether you are the CEO or the frontline worker, you feel the pinch in your wallet every day. But do you have to?
Enter the data. Number crunching is what we do, and for this exercise, we turned to the experts. Drawing upon the numerical analysis skills of the people who conduct major site selection projects for a living, Site Selection presents a detailed report on the most cost-effective locations in the U.S. for manufacturing projects, for corporate headquarters projects and for working families.
Lowest-Cost Manufacturing Locations
If you want to know how much it costs to build and operate a manufacturing plant, it pays to seek out the expertise of those who conduct large-scale industrial site selection. One such firm is Global Location Strategies in Greenville, South Carolina. Locating billion-dollar-plus factories is what they do.
“Every project is unique, even those within the same industry sector, and it is important to base location decisions on project-specific cost considerations,” they write in exclusive analysis for Site Selection. “The location-dependent cost criteria considered for this evaluation are grouped into the following primary categories: labor costs, utilities and industrial lease costs.”
For the purposes of this exercise, GLS assigned the following percentages of overall costs to each category: labor — 55%; utilities — 26%; and lease costs — 19%. Their spring 2025 ranking of metro areas in the U.S. also reflects project-specific analysis inputs.
“The operation is assumed to run seven days a week with two eight-hour shifts per day,” GLS states. “In addition to the total number of employees, a labor profile has been developed that includes a mix of industry-specific white- and blue-collar occupations to measure labor quality, availability and cost. This analysis is designed to allow for a customization of inputs, which would result in a modified ranking according to the unique needs of a specific project.”
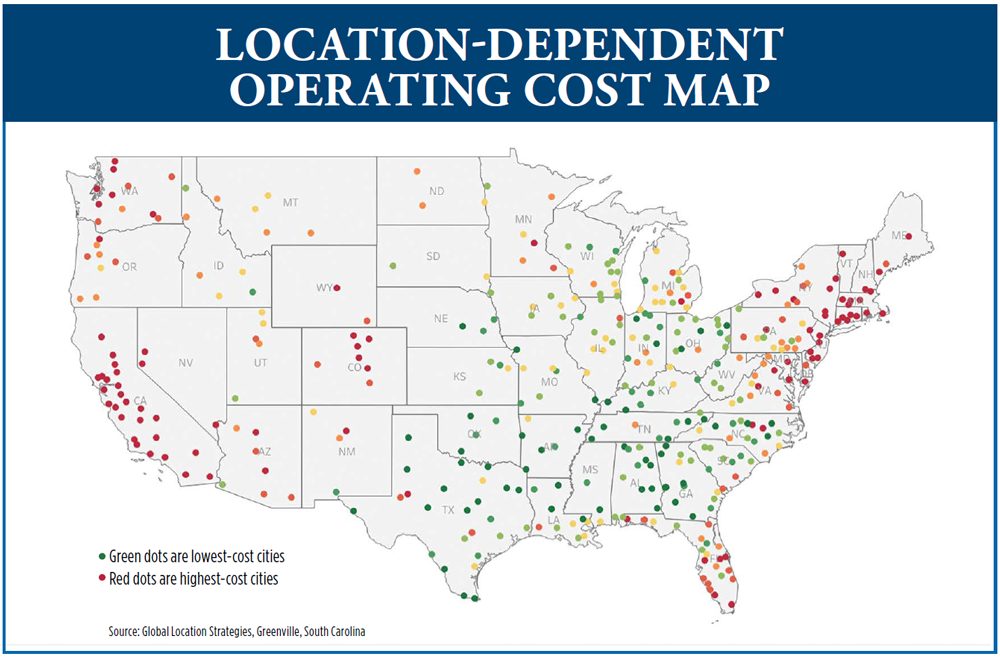
Assumptions are a 250,000-sq.-ft. facility; 75 full-time employees; 5 MW electric load factor of 0.80; 15 MCFPH natural gas; 200K GPD water; and 50K GPD wastewater. Based upon those criteria, GLS ranked the following metros as having the lowest annual operating costs: Florence-Muscle Shoals, Alabama, came in at No. 1 with annual operating costs of $9.14 million, followed by Brownsville-Harlingen, Texas, at $9.18 million and Gadsden, Alabama, at $9.24 million. See the chart on this page for the entire top 25.
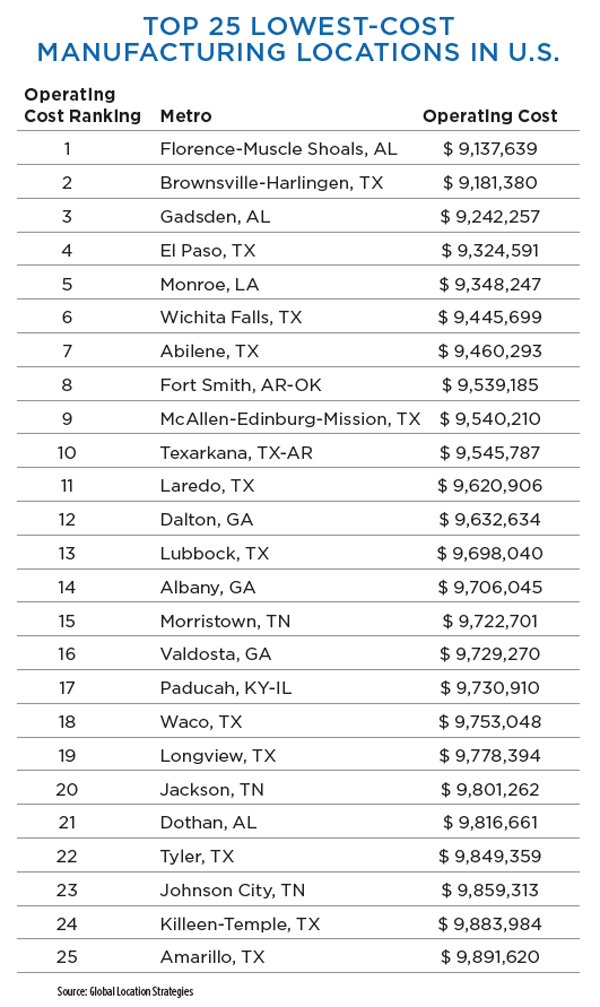
Thirteen of the 25 lowest-cost metros are in Texas. The remainder are in the Southeast or South Central region. This is not an anomaly, says Tess Fay, principal and vice president of location intelligence at GLS.
“The biggest drivers of expenses are the labor costs,” says Fay. “That favors the Southeast and the Midwest. Utilities on average make up 26% of the overall operating costs of a manufacturing plant, and people are trying to navigate rising electric costs.”
GLS knows location cost profiles better than anyone. That’s a big reason why they have recently located massive aluminum plants in Alabama and Oklahoma. On May 16, Emirates Global Aluminium, the world’s largest producer of premium aluminum, selected a 350-acre site at the Port of Inola in Rogers County in northeast Oklahoma for a $4 billion aluminum factory that will create 1,000 new jobs in the area. GLS found and recommended that site for the company.
Located 30 minutes east of Tulsa, Inola is indicative of the types of smaller, rural communities that are winning the biggest-budget factories of the future. Analysis of the ranking data shows that the 42 lowest-cost locations in the country are all small to mid-sized metros. The first large MSA does not show up until No. 43: Memphis.
“Our projects are usually on the periphery of these medium-sized metros,” says Fay. “We are often prioritizing infrastructure as well as the utilities and the costs. The workforce is a challenge for smaller communities. So are water and wastewater capacity.”
One smaller community that is excelling at overcoming its size is Gadsden in northeast Alabama — ranked No. 3 for lowest costs in the nation on the GLS index. David Hooks, executive director of the Gadsden-Etowah County Industrial Development Authority, says Gadsden has 35,000 people. The county has 103,000.
“While all companies look at overall costs of production, from our side, the quality of our workforce and the availability of our utility services are paramount,” says Hooks. “Gadsden has been an industrial town since the late 1980s. It was developed as a railroad town, and it has continued to be known as a manufacturing community for metals.”
Located on Interstate 59 two hours northwest of Atlanta, 60 miles north of Birmingham and 80 miles south of Chattanooga, Gadsden sits in the sweet spot of the Mid-South automotive manufacturing corridor.
Recently, Fehrer Automotive grew its Gadsden plant by investing more than $6 million into a 200,000-sq.-ft. expansion, giving Fehrer a total of 500,000 sq. ft. of space — quadruple the company’s footprint when it first opened 10 years ago.
“Fehrer employs about 500 people, making it the second-largest foam plant in the Fehrer Group worldwide and one of the largest employers in Etowah County,” says Hooks.
National Headquarters Locations
BizCosts is the proprietary data bank of corporate site consultancy The Boyd Company Inc. For this report, BizCosts calculated the annual operating costs of a 60,000-sq.-ft. corporate headquarters office employing 300 workers in the 20 major head office markets in the country.
BizCosts found that Midtown New York City is the most expensive market today at a total annual operating cost of $33.42 million for 2025, followed by the San Francisco CBD at $33.4 million and Sunnyvale, California, in Silicon Valley at $33.2 million.
The least expensive head office market is Boca Raton Northwest, Florida, at $25.89 million. The second cheapest is Midtown Atlanta at $27.36 million; and third lowest is Miami CBD at $28.65 million. Austin CBD and Chicago Central Loop round out the five lowest-cost markets. See the ranking of all 20 markets on this page.
“There is a dominant common thread among the lower-cost headquarters locations,” says John Boyd Jr., principal of The Boyd Company Inc. “This dominant theme is the presence of relative bargains today for leasing high-end, Class-A office space consistent with the needs of a corporate head office.”
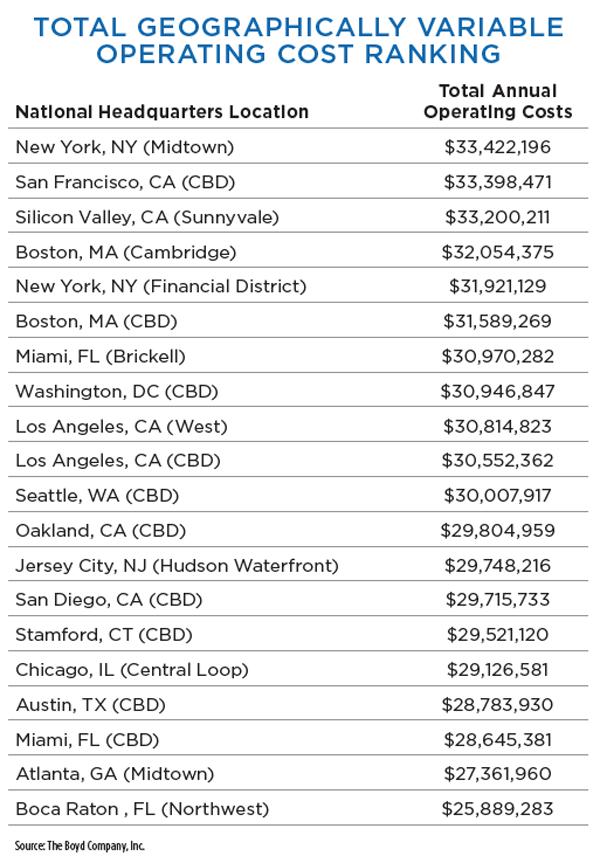
Asked why Boca Raton stacks up as such a bargain compared to the most expensive markets, Boyd says, “Like the Philly suburban markets, it [Boca Raton] houses an affordable office market at $44.42 per square foot, which is in stark contrast to the hyper-hot Miami market where Class-A office lease rates in the popular Brickell submarket at $107.86 per square foot rival those of New York City. Rates in Miami’s CBD submarket are also pricey at $81.38 per square foot. I suspect that Boca Raton cost structures are often mistakenly assumed to mirror the sky-high rates now associated with Miami, but that is not the case. Also, like in most of Florida, real estate property tax rates and electric power rates are low in Boca Raton by national standards – not to mention the lack of a personal income tax, which is a major driver in corporate headquarters relocation decisions.”
Best States for Saving Money
No analysis of inflation-busting locations is complete without considering the impact of costs on workers and their families. For this data, we turned to Bankrate and its April 14 report on the easiest and hardest states in which to save money in 2025. Data categories used to compile this index included bank deposit rates; household debt-to-income ratio; state and local taxes; economic performance; job growth; inflation-adjusted changes in household income; and cost of living.
Based upon these criteria, Tennessee ranks as the No. 1 Best U.S. State for Saving Money in 2025, per Bankrate, followed by No. 2 Missouri and No. 3 Texas. Rounding out the top 10, in order, are Oklahoma, Florida, Kentucky, South Dakota, Louisiana, Indiana and Michigan.
According to Bankrate, these are the study’s key takeaways:
- Driven by low tax rates and a favorable cost of living, Tennessee ranks as the easiest state in which to save money.
- Due to its high cost of living and a declining employment rate, Hawaii ranks as the hardest state in which to save money.
- Southern and Midwestern states are generally easier for saving money, while Northeastern and Western states are harder.
The common denominators for the best states for saving money are lower-than-average tax burdens, affordable living costs and stable employment growth.