Looking for a Mid-Atlantic location for your next manufacturing operation? Site Selection has done some of the legwork for you by reaching out to manufacturing partnerships in Virginia, Delaware and Maryland for their views on the manufacturing landscape in their states.
We sent four questions to manufacturing associations in all three states, and we appreciate their participation in this exercise. Let’s meet the participants:
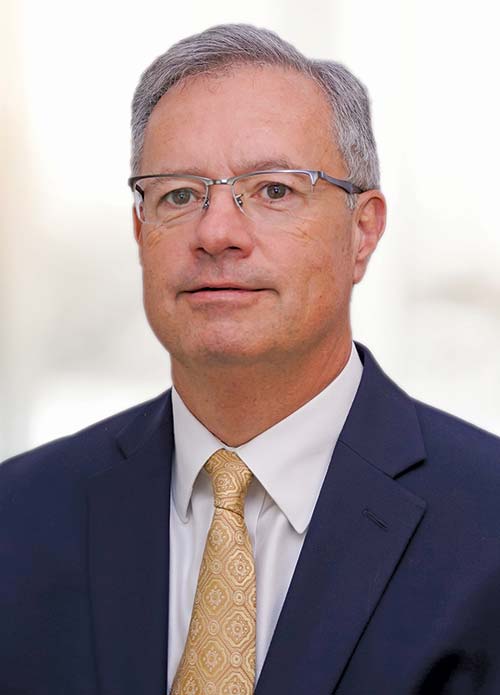
Virginia
Bill Donohue
President and Executive Director
GENEDGE
bdonohue@genedge.com
276-732-5755
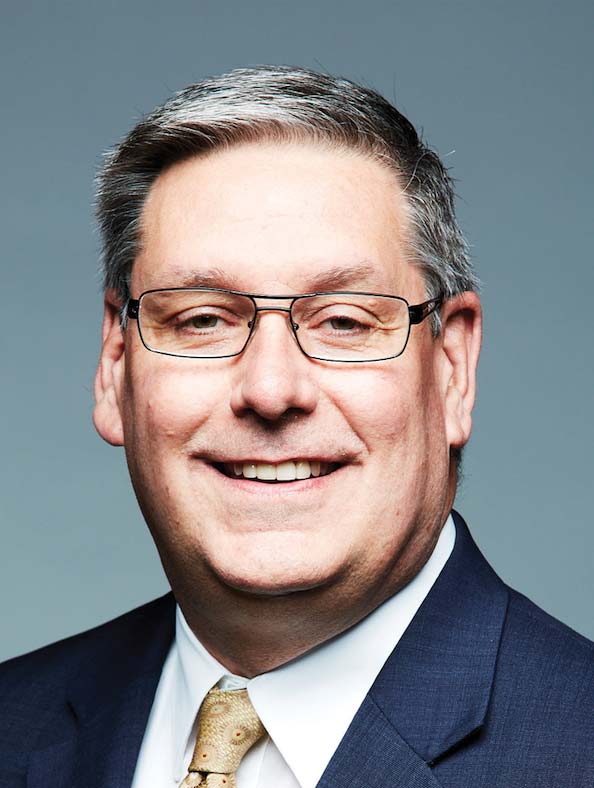
Delaware
Kurt Foreman
President and CEO
Delaware Prosperity Partnership (DPP)
kforeman@choosedelaware.com
302-576-6586
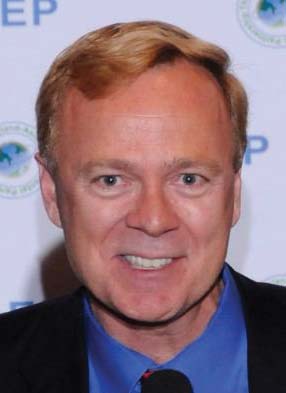
Maryland
Peter Gourlay
Vice President
Regional Manufacturing Institute
Peter.gourlay@rmiofmaryland.com
443-276-2489
What is the “manufacturing mood” in your state as we enter the close of 2019? Are manufacturers optimistic, pessimistic or neutral?
Bill Donohue, Virginia: I would say overall optimistic but guarded at the same time. Virginia is fortunate that our economy has continued to strengthen. We have seen the addition of 88 establishments and 3,680 jobs across the state in GENEDGE ALLIANCE’s target market, which includes manufacturing, engineering and technology businesses. However, our 2018 CEO study identified that a lack of engineering, sales, marketing, IT and production management staff is creating a significant drag on company growth. Recent steps taken by the General Assembly are intended to close those gaps through increased production of graduates.
Governor Northam announced recently that his administration has secured $20 billion in investment since taking office in January 2018 — more than any previous administration has announced in a full four-year term. This economic development has created over 51,000 new jobs across the Commonwealth, many of which are in manufacturing.
As we look ahead, two new DoD-funded programs focused on Supplier Cyber Security & Rural Supply Chain Capability Expansion will position GENEDGE well to leverage a key industry to spur cluster growth by taking advantage of the upturn in defense spending to support the economic development goals of the Commonwealth.
“MEP plays a critical role in addressing cybersecurity as a national priority, strengthening the defense industrial supply base and addressing the manufacturing skills gap.”
Kurt Foreman, Delaware: In Delaware, the mood is definitely optimistic. That’s the feedback we are hearing from our partners that serve or represent the manufacturing and advanced manufacturing sector. Delaware’s manufacturing base is a diverse one and ranges from traditional manufacturing to advanced materials manufacturing with products that are competitive on a national and global scale. DPP’s project pipeline consistently includes manufacturing opportunities — in fact, it’s nearly half the projects. Delaware’s enviable East Coast location, competitive costs and diverse talent pool have positioned the state to nurture and grow a diverse manufacturing base.
Peter Gourlay, Maryland: Maryland’s business environment has greatly improved. When we ask small-to-medium-sized manufacturers about their business, the great majority have given a positive response.
What are the most common issues manufacturers reach out to your office about?
Kurt Foreman, Delaware: Like many places, access to a skilled workforce remains a primary issue for manufacturers in Delaware. The good news is that Delaware is well positioned to respond to the demands for a skilled workforce with an array of innovative skilled labor training programs throughout the state. Our ability to create uniquely designed educational opportunities based on the current, rapidly evolving needs of manufacturers is a distinctive advantage for companies looking to grow or locate on the East Coast.
Peter Gourlay, Maryland: By far, the No. 1 issue is workforce and finding talent.
Bill Donohue, Virginia: Small manufacturers in Virginia and nationwide face new challenges and opportunities related to top-line growth, skill gaps, product development, cost reductions, cybersecurity, 3-D printing, Industry 4.0, improved operational efficiencies, supply chain resiliency and succession planning. The challenges that Virginia’s manufacturers face also vary from region to region, with a significant divide between the rural areas of the state and the more populated urban centers. We organize our outreach regionally to better understand and serve these areas based on their needs and current situation and to help connect companies to resources to drive improvement in the regional and state economies and make these areas more attractive for manufacturers.
Are MEP Centers promoting any particular strategy (process improvements, green manufacturing, etc.)?
Peter Gourlay, Maryland: The Regional Manufacturing Institute of Maryland focuses on the transformation of Maryland manufacturing as companies grapple with the transition from analog to digital. We do this by connecting STEM students with manufacturers and by educating manufacturers about the Industry 4.0 movement and guiding them to relevant resources. We also help inform our educational institutions and policymakers about the importance of the Industry 4.0 impact, so that training and resources will increasingly become more aligned with the future needs of industry.
We also help our manufacturers become more green. RMI has played a leadership role in helping various groups of Maryland manufacturers become more sustainable by helping them to cut their energy costs, saving them over $7.5 million. We have helped them to publicly state their sustainability commitments via the Maryland Green Registry
“RMI has played a leadership role in helping various groups of Maryland manufacturers become more sustainable by helping them to cut their energy costs, saving them over $7.5 million.”
Bill Donohue, Virginia: MEP plays a critical role in addressing cybersecurity as a national priority, strengthening the defense industrial supply base and addressing the manufacturing skills gap. For example, the DoD recently released its report, “Assessing and Strengthening the Manufacturing and Defense Industrial Base and Supply Chain Resiliency of the United States,” which highlights sessions held by MEP with more than 1,000 US manufacturers to familiarize them with DFARs requirements to ensure adequate cybersecurity protections.
Kurt Foreman, Delaware: At DPP, we like to say that Delaware is bigger because of its size; one of my colleagues calls it our “personable size.” Put another way, access is easier in Delaware. Delaware’s MEP can easily connect with the entire local ecosystem and tailor the support its client companies need. Companies are regularly asking for resources to grow their facilities, develop new international markets or better leverage their current assets. What DEMEP calls “ultra-small companies” are a key new focus for their staff.
What is the most effective way to help manufacturers locate and acquire the talent they need?
Bill Donohue, Virginia: The nation is at nearly full employment, and the number of people in the workforce is also peaking. Therefore, manufacturers face new challenges in identifying, selecting and retaining talent. The types of challenges can be quite different based on the area of the state, particularly in the rural parts of the Commonwealth. To compete, companies need to engage better in their communities, as well as transform to “employers of choice.” MEP centers across the country are delivering services to help companies do so.
While a postsecondary degree is not essential, most manufacturing jobs require specific training beyond a high school degree. Interested students will benefit from hands-on experience, either in the form of project-oriented learning, internships, apprenticeships, or training through their employers. Manufacturing Day (MFG Day) is another avenue for manufacturers to open their doors and showcase what modern manufacturing is — and what it isn’t. The demographic shifts and increased demand for skills has necessitated a new understanding of manufacturing as a desirable career and we are working across the MEP National Network to facilitate that understanding. (Manufacturing Day 2019 occurs on Friday, October 4. For more information, visit www.mfgday.com. — Ed.)
“DPP’s project pipeline consistently includes manufacturing opportunities — in fact, it’s nearly half the projects.”
Peter Gourlay, Maryland: The Regional Manufacturing Partnership has surveyed a cohort of Maryland manufacturers, and by far the most effective way they find talent is through word of mouth.
Kurt Foreman, Delaware: First, there is no wrong door in Delaware. The various partners including DEMEP, the Division of Small Business or the Delaware Prosperity Partnership can all be a good entry point for existing manufacturers or those considering Delaware for the first time. One key initiative in Delaware, widely supported by the public and private sectors, is the Career Pathways program. It’s garnered national attention and support from the Bloomberg Foundation, and is designed to help students be part of the talent pipeline for companies, including manufacturers. The Career Pathways program is so effective it is expanding from 12,000 students to 24,000. Our community and technical college, DelTech, is another key asset for both customized support and overall pipeline access.