While many places around the U.S. struggled to find adequate supplies of PPE during the COVID-19 pandemic, one community that was ahead of the curve was Pflugerville, Texas.
Known as “The 3D City,” this Austin suburb punches well above its weight class when it comes to additive manufacturing — a feature that enabled this city of 65,000 people to respond quickly to the crisis and fill supply chain gaps in PPE and other essential supplies.
“Three companies in town pivoted to make new products to supply essential gear and medical equipment to the health-care providers during the pandemic,” says Amy Madison, executive director of the Pflugerville Community Development Corp. “Our response group grew to as many as 25 participants over time with regular Zoom calls. A lot of supply chain issues were addressed. The collaborative effort that our small community made to respond to COVID-19 quickly was due to the technology we have at our 3D-printing manufacturers.”
Cumberland Additive, EOS and Essentium are the Pflugerville-based additive manufacturers that took the lead in this response, notes Madison. Each played a crucial role in getting needed protective gear and other medical devices to front-line workers and COVID patients.
“We do both metal and plastic 3D printing at this site for aerospace, defense, oil and gas, and the transportation sectors,” says Michael Celardo, vice president of business development and engineering for Cumberland Additive. “Our products are designed by our customers and 3D printed by us. It does not take a lot of time to develop new products. The benefit is being able to make a part from a 3D model without a lot of iterations. We made three different things: ventilator components, respirator face masks, and face shields.”
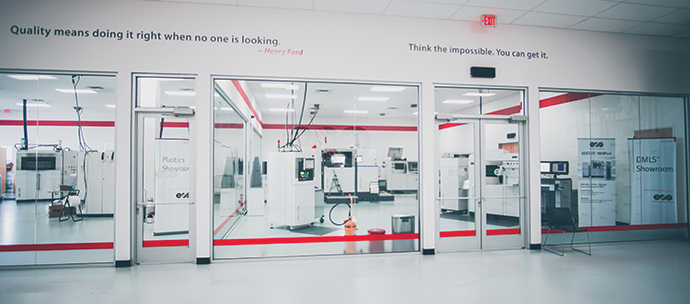
This quick action enabled Pflugerville’s first responders to be ahead of the game in receipt of essential protective gear. “We printed and delivered parts within a week,” says Celardo. “We are printing parts three-dimensionally using powder. We produced over 500 ventilator components, over 200 face shields, and around 30 prototype face masks.”
Cumberland’s work enabled masks to be delivered to the Pflugerville Police Department and the Dell Medical Center. “The two key lessons learned were the value of collaboration and the knowledge that if something like this happened again, we know the protocol for how to respond,” says Celardo.
Donnie Vanelli, senior vice president of EOS, says that his company’s response had four elements. “First was bridging the gap,” he says. “We asked, where can we use additive manufacturing to fill short-term interruptions in the supply chain? Secondly, we had to adapt our current designs to be more useful in additive. We used design engineering to enable a critical part to be made with additive. Third, we accelerated our activity to scale up ventilator production. Fourth was sustaining. How do we use additive and 3D printing as a means of changing the way the supply chain operates so that when we have the next pandemic, we don’t have to wait 60 to 90 days for critical supplies?”
Vanelli says EOS elected to make metal parts going into ventilators and other devices. “These first articles have to go to the FDA or other authorities for approval,” he says. “We had to accelerate the process. We printed adaptors that allowed 20 ventilators to be put into service. We’re now printing holders for face shields. In designing the face shield adaptors, we created the whole 3D printing assembly. We’ve also done some face mask projects.”
“The two key lessons learned were the value of collaboration and the knowledge that if something like this happened again, we know the protocol for how to respond.”
Through it all, EOS has been able to retain all 170 employees without having a single worker diagnosed with COVID-19. “That is a real success,” Vanelli says. “We’ve had people traveling to install machines in other states, and we were able to keep everyone safe.”
Blake Teipei, CEO of Essentium, uses an extrusion system in its additive technology. “We relocated from College Station because it was a mid-sized city that did not have the ability to serve clients globally,” he notes. “By moving to Pflugerville, we found all the benefits of Austin without all the challenges of Austin like taxes and traffic. We had access to the same talent pool. We’re just eight miles down the road from Apple. We make the materials right here in Texas, and then we ship those to the customers.”
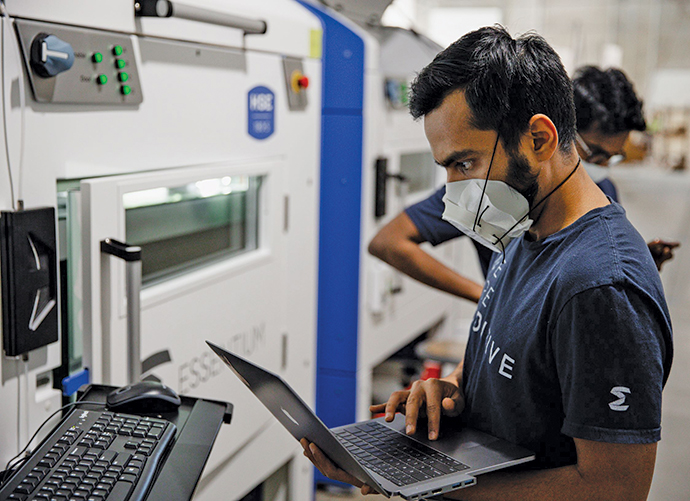
Family ties prompted a key connection. “My wife is our chief development officer,” says Teipei. “She was presiding over our work with the Texas Air National Guard. The head of the Guard called us on March 22 and said the governor had pulled together a task force to coordinate pandemic response. He asked us who could be pulled together to be agile and make a pivot to meet a need.”
Essentium stepped up. “3D printing has an inherent degree of agility,” says Teipei. “Our printers are very, very fast. The state made an investment in the supply chain and procured a small fleet of high-speed extrusion printers. We produced over 3 million face masks in that time. We outfitted the entire Texas Air National Guard with masks.”
Madison says what all three companies did is indicative of the spirit of businesses in Pflugerville. “It’ s about responding to community needs,” she says. “Being able to pivot and retool in a small community is a real asset.”
This Investment Profile was prepared under the auspices of the Pflugerville Community Development Corp. For more information, contact Amy Madison at 512-990-3725 or amym@pfdevelopment.com. On the web, go to www.pfdevelopment.com.