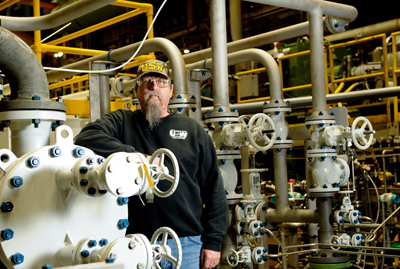
The plethora of reports coming out only confirm what the public seems to already know and what policy makers in Washington are now grasping: Manufacturing matters.
The latest in-depth analysis comes from the McKinsey Global Institute and was published Nov. 19. It was followed the next day by the release of the “9th Edition of the Facts About Modern Manufacturing,” a collaboration between the Manufacturing Institute, the Manufacturers Alliance for Productivity and Innovation (MAPI) and the National Association of Manufacturers (NAM).
These two reports come on the heels of multiple studies released this year by Deloitte Touche, Boston Consulting Group, the Brookings Institution, the Information Technology and Innovation Foundation and the New America Foundation, to name a few, all focusing on manufacturing.
“In some ways this has become a cottage industry for jumping on the manufacturing bandwagon,” says Stephen Gold, president and CEO at MAPI. “They [the reports] all seem to talk about the global marketplace and the growing intensity of the competition.”
But the McKinsey report, “Manufacturing the Future,” is getting especially good reviews for its analysis and conclusions. The good news, according to McKinsey, is that manufacturing worldwide has a “promising future” in which another 1.8 billion people will enter the global marketplace over the next 15 years and worldwide consumption will nearly double to US$64 trillion.
Developing countries, such as China, India, and Indonesia, will continue to increase their share of global production, particularly for basic goods, whereas richer and more developed countries, like the United States, Germany and Japan, will concentrate more on value-added products that are more costly, innovative and high-tech.
But there are ominous warnings within the McKinsey report, which states that “the future of manufacturing is unfolding in an environment of far greater risk and uncertainty than before the Great Recession.”
According to McKinsey, “To win in this environment, companies and governments need new analytical rigor and foresight, new capabilities, and the conviction to act.”
While there is recognition from policy makers in Washington as to the importance of manufacturing, there is no assurance that they will take needed action to help put U.S. manufacturing in a more competitive stance in relation to the rest of the world, according to knowledgeable observers.
The structural costs — corporate tax liability, employee benefits, tort litigation, and regulatory compliance — of U.S. manufacturing have been rising. Taken together, these structural costs were 20 percent higher in 2011 than for the major competitors of the U.S., up from 17.6 percent in 2008.
“There are so many different challenges that we face that you have to be careful not to be too optimistic,” Gold says. “Things are not going to be a piece of cake.”
Declining But Efficient
Indeed, the McKinsey report confirms that, as a manufacturing nation, the U.S. cannot go home again. Opportunities will remain limited as certain types of jobs, particularly those requiring lower skills, are almost certain to never return to a U.S. manufacturing environment which continues to shift toward more automation and robotics.
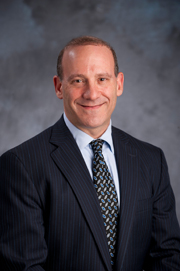
And while manufacturing will continue to play a paramount role in wealth creation, it will play a more limited role in job creation, particularly in the more advanced economies.
“Manufacturing makes outsized contributions to GDP. It makes outsized contributions to overall productivity growth. It drives prosperity,” said James Manyika, one of the authors of the report, in comments to the Washington Post. “But purely on employment, it has been declining over time.”
Between 2000 and 2011, the U.S. economy lost 5.4 million jobs in manufacturing, an average of 1,276 jobs and 17 manufacturing plants lost per day. Despite job growth in the last two years, the long-term prospect for manufacturing job growth in the U.S. is not good.
The evidence, according to McKinsey, shows that as countries become wealthier and develop a strong middle class, consumption shifts toward services. With that comes a resulting decline of manufacturing’s share of the GDP. Employment follows a similar pattern: Manufacturing’s share of U.S. employment declined from 25 percent in 1950 to 9 percent in 2008. In Germany, manufacturing jobs fell from 35 percent of employment in 1970 to 18 percent in 2008.
At the same time, while manufacturing continues to be an engine of growth worldwide, the distinction between manufacturing and services has blurred.
“Over time, service-like activities — such as R&D, marketing and sales, and customer support — have become a larger share of what manufacturing companies do,” the McKinsey report said. More than 34 percent of U.S. manufacturing employment is in such service-like occupations today. While manufacturers in advanced countries will continue to seek out and hire skilled workers, manufacturing’s share of employment will continue to come under pressure.
“This is due to ongoing productivity improvements, the continued growth of services as a share of the economy, and the force of global competition, which pushes advanced economies to specialize in more high-skill activities. Manufacturing cannot be expected to create mass employment in advanced economies on the scale that it did decades ago,” according to the report.
“The only way you are ever going to see manufacturing employment rise dramatically — and I don’t think it is going to happen — is if we saw an overwhelming growth in new industries in this country,” Gold says. “For instance, if you have a revolution in some new technology — the energy revolution in this country may be an example. Then all of a sudden a lot of new industries pop up, and you need supply chain and you don’t want to put it on the other side of the world.”
Just that sort of convergence may be happening in Pittsburgh, in the heart of the Marcellus Shale activity, where earlier this week Gov. Tom Corbett announced $1 million in awards to small companies Acutronics, Paramount Industries and Ex One from the state’s Research for Advanced Manufacturing in Pennsylvania (RAMP) program, part of Pennsylvania’s new Discovered and Developed in Pennsylvania (D2PA) program. All three companies are involved in additive manufacturing, otherwise known as 3-D modeling.
Carnegie Mellon University, Lehigh University and the University of Pittsburgh, led by policies Corbett’s administration had already put into place focusing on making things, were successful earlier this year in garnering federal support for a National Additive Manufacturing Innovation Institute (NAMII), a first-of-its-kind national public-private partnership that has $30 million in federal support from the Dept. of Defense and $40 million in regional cost share commitments. The consortium supporting NAMII comprises 40 companies (including the three RAMP award winners), 13 higher education institutions and 11 trade associations.
“I think they’re finally getting it,” said Ralph Resnick, acting director of NAMII and a longtime presence in the regional manufacturing scene. “The national economic leadership is finally getting that manufacturing is crucial to our economy, and you need to make where you create.”
Resnick said additive manufacturing’s applications range from oil and gas equipment to aircraft, medical devices and structural materials. And he characterized 3-D printing as the 21st century’s laser printer: “In essence, the way we democratized publishing, we can also democratize manufacturing,” he said. Along the way, he added, there’s the potential for turning the region of eastern Ohio, western Pennsylvania and northern West Virginia known as the “Tech Belt” into “the Silicon Valley of additive manufacturing.”
‘Embrace the Link’
In a speech at the Atlanta Regional Commission’s “State of the Region” event earlier this fall, Bruce Katz of the Brookings Institution’s Metropolitan Policy Program said Northeast Ohio was also electing to build on its manufacturing prowess, and that Atlanta could too. The secret, he said of the southern logistics hub, was to move from a place that moves goods other people make to a place that capitalizes on its metropolitan asset and knowledge base and evolves “from port to production, tourism to technology, airport to aerospace.”
“Get back into the export game,” he said, noting that Americans “don’t get out very much” and that only 26 percent of them even have passports. “We still make things here that the rest of the world wants. For all the talk of a post-industrial economy, we still export $955 billion of manufactured goods. We’re the third largest industrial powerhouse in the world behind China and Germany. We lead the world in advanced services, and this is the reason why our trade deficit is not as large as it could be.”
Things are even better than Katz thought. U.S. exports of manufactured goods reached a record $1.27 trillion in 2011, up 15.1 percent from 2010, said the U.S. Commerce Department’s International Trade Administration last February.
“We have to be a hothouse of invention and a platform for advanced production,” Katz told this Atlanta audience. “Embrace the link between innovation and manufacturing. Only about 9 percent of jobs are in manufacturing, but about 35 percent of engineers work in manufacturing, and manufacturers account for a 68-percent share of R&D. We will innovate less if we do not produce more. We must make things again.”
Katz said the supply chain fragility revealed by the tsunami in Japan last year was one reason companies are coming home, noting that 38 percent of economic growth coming out of the recession is coming from the manufacturing sector. But not all is bright on the horizon.
Rob Atkinson, founder and president of the Information Technology and Innovation Foundation, says the pattern of U.S. manufacturing “is essentially a downward ratchet.” Absent another recession, he foresees stability but not a major rebound, not a renaissance, not real growth for the long term.
“The latest MAPI report shows that the U.S. manufacturing trade deficit has gone up and that the Chinese trade surplus has skyrocketed, so there is still severe competition from offshore,” Atkinson says.
Echoing Gold’s concerns, Atkinson says it is the United States’ competitive position in the world that should be of primary concern.
“Yes, manufacturing is declining because it is getting more productive, but that’s not the right question. The right question is, ‘How competitive are you globally with your manufacturing, and are you able to be sustainable?’ ” he says.
Among the nine largest U.S. trading partners, only France has high structural costs, according to MAPI. Two of the chief culprits that are ensuring a competitive disadvantage for U.S. manufacturers, according to both Gold and Atkinson, are corporate taxes that rank among the highest in the industrialized world and an ever-expanding and obstructive regulatory climate.
On the tax front, Atkinson sees little prospect for relief for U.S. manufacturers.
“That is one of the easiest red flags that people can point to. It’s kind of a no brainer and yet it’s almost impossible for us to do anything about it because of the current political dynamics in Washington,” he says.
The regulatory burden on U.S. manufacturers is equivalent to an 11-percent tax on the businesses, according to the 2012 “Facts” report from NAM and MAPI. Healthcare costs, typically not faced by foreign competition, remain a huge concern and cost burden.
But the U.S. also has some distinct advantages, which are drawing substantial foreign direct investment. Besides generally having a skilled work force, America’ trump card is energy.
Natural gas prices in the U.S. plunged to a decade low this year after companies ramped up output from shale deposits to make the nation the world’s largest producer. Demand for liquefied natural gas is high in Europe and Asia, where the fuel costs $10 to $16 per million British thermal units — far more than the $3.70 it fetches in the US.
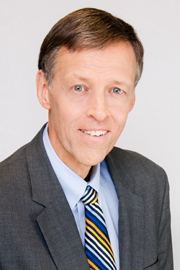
For those industries that use much energy in the production process — pulp and paper, steel, and petrochemicals — the allure of cheap natural gas could prompt considerable foreign direct investment into the U.S. Exhibit A: Sasol’s planned $15-billion investment in southwest Louisiana, announced earlier this week, for a combined ethane cracker and gas-to-liquids complex.
Meanwhile, talks and continue for Shell’s planned $4-billion cracker complex at the former Horsehead Corp. zinc manufacturing site near Monaca in western Pennsylvania. Site Selection asked Gov. Corbett this week at the Pittsburgh event how the project was progressing as the option period on the site nears its expiration. He said things are still moving forward.
“I still feel very good” about the project, he said, citing meetings that “went very well” between his administration and officials from a higher level than previously at Shell, and various ongoing permitting processes. “I think they’re still on track.”
Speaking of the small companies his administration’s new program is supporting, his comments ranged farther afield, offering a glimpse of a possible future that could place Pittsburgh and the Commonwealth in the same pioneering position it was in for coal, oil, electricity and steel.
“What we invent here, we should build here,” said Corbett. “If we take the lead in additive manufacturing, Pittsburgh could well be the place to which manufacturers around the world turn for their equipment.”
That’s already the case at such southwest Pennsylvania companies as Aggressive Grinding Services in Latrobe, Elliott Group in Jeannette and Dura-Bond Coating in Duquesne, which have recently finished expansions — driven by energy activity near home and around the world — for carbide and ceramic grinding services, turbomachinery and coated pipe, respectively.
“A huge percentage of anything we do anymore is for a shale gas deposit somewhere,” says Mike Reeder, 66, the plant manager for Dura-Bond’s new plant along the banks of the Monongahela River that just opened Nov. 19. The company’s still running its former plant in nearby McKeesport too, and can barely acquire land fast enough to keep up with the need for pipe laydown area.
Elliott, headquartered in Jeannette for 102 years, just celebrated the grand opening of its new $17-million headquarters in August. It was the culmination of a company comeback from the brink of being closed down just four years ago.
COO Art Titus says all parts of Elliott’s business are benefiting from shale gas production, beginning with the reactivation of a lot of old refineries and gas processing plants that some companies previously had in “run it into the ground mode,” i.e. not bothering to replace parts and equipment because of no longer being able to compete globally. Now, cheap natural gas feedstock is causing some of those businesses to suddenly want to improve the reliability of their equipment.
“Our parts organization was in decline for years,” he says. Today, “Our North American parts business has been growing dramatically, driven by a re-emphasis on North America-based equipment.”
“Archaeologically, when you dig up something, you look for what tools they were able to make,” says Lester Sutton, CEO of Aggressive Grinding, whose customers include Kennametal, among others, who in turn serve the energy patches in Pennsylvania and beyond. “Everything in this room was made by a machinist, or a tool and die maker had some sort of effect on it.”
Sutton’s company just finished its own $4-million expansion.
“The only way we pulled out of a Depression was through manufacturing,” Sutton says. “The only way an economy can survive is through manufacturing. It’s how you judge the intelligence of a society.”