The abundance of shale gas in Pennsylvania is reducing energy costs across the state and lending a hand to the already robust manufacturing sector. As the country’s second-largest producer of natural gas, the state is utilizing the resource in the best way it knows — advancing the foundation of its economy.
Over the past seven years of the Marcellus development, direct employment in the natural gas industry increased by 23,478. Pennsylvania is the 10th-largest chemical producing state and in 2014, the state’s Marcellus Shale yielded a record-breaking 4 trillion cubic feet — 16 percent of annual US consumption.
“Geologists have known for decades that the gas was down there, but no one knew how to economically extract it,” says William Hall, director of the Shale Gas Innovation and Commercialization Center at Ben Franklin Technology Partners. “But innovators and researchers kept developing the science and engineering of both exploration and extraction techniques.”
Eventually, scientists and researchers improved both the hydraulic fracturing technique and horizontal drilling technique that allowed the drill to slowly turn from drilling vertically to drilling horizontally along the shale seam. The result was access to a greater surface area within the natural gas liquids (NGLs) bearing zone and now an abundance of shale gas.
every citizen of the Commonwealth through
lower energy rates, not to mention the
lower cost to manufacturers through
lower energy costs.”
— William Hall, director,
Shale Gas Innovation and Commercialization Center
at Ben Franklin Technology Partners
“The industry keeps improving every aspect of their operations through innovation, from identification of the ‘sweet spots’ to the speed of drilling operation and improvements to the drilling rigs, to all the environmental and safety improvements that have been implemented,” says Hall. “The benefits are being felt by every citizen of the Commonwealth through lower energy rates, not to mention the lower cost to manufacturers through lower energy costs.”
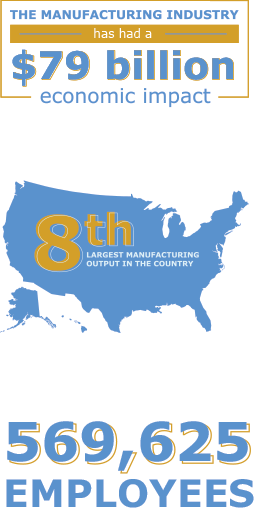
This decrease in energy costs has benefited every business in the Commonwealth, according to Hall. But any manufacturing operation that uses high levels of energy is benefiting from lower electricity costs and if they use natural gas or even propane as their fuel source, they have seen a major reduction in their cost of energy.
“The shale energy revolution, as I like to refer to it, is directly responsible for this drop in energy prices,” says Hall. “Many manufacturers from the glass industry to grain dryers to paper mills and steel manufacturers who are high-energy users are seeing huge benefits.”
Each and Every Drop
Manufacturing in the state has expanded to include the use of innovative technology to enhance products and processes. Once such manufacturing company, KCF Technologies is making moves and changing the way shale gas is extracted.
“Before KCF Technologies introduced SmartDiagnostics to the oil and gas industry, it was impossible for this industry to accurately monitor the health of most of its equipment,” says Ben Lawrence, vice president of sales for KCF Technologies. The metric that Lawrence and his company is proud of the most would be that the company has reduced the amount of time that shale gas workers are likely to be injured by 50 percent.
The surge of shale gas has also led to other manufacturing companies that are specifically geared toward shale gas production. ProChemTech, a company that manufactures water and wastewater treatment chemicals and equipment, started research and development work in 2008. The company examined how to handle the production wastewaters generated through shale extraction in an environmentally acceptable way.
“Our first generation technology, removed suspended solids, barium, calcium, and magnesium from the wastewater so that it could be reused as hydrofracture makeup water,” says Tim Keister, chief chemist and president of ProChemTech International, Inc. “With the decrease in hydrofracture activity and existing substantial gas production, there is far more production wastewater than can be reused as hydrofracture makeup water.”
But ProChemTech has even come up with a solution for the excess wastewater. “Our second generation technology, which disposes of flow back and production wastewater by converting it into chemical products; barite, sodium chloride, calcium chloride solution, and distilled water, totally eliminates disposal by deep-well injection,” says Keister. “All the wastewater is converted into products that are in high demand.”
Another emerging manufacturing company piggybacking of the shale surge is PixController, Inc. The company was one of four to win the Ben Franklin Shale Innovation Award and the reason is sound. Originally, Pixcontroller, developed a connected device technology that was designed for remote security and surveillance markets. “Later, we saw a growing need in the shale gas industry for remote industrial device and environmental sensor monitoring, where we could apply our technology,” says Bill Powers, president and CEO of PixController.
An Ideal Situation
KCF Technologies, ProChemTech and PixController have each recently expanded in Pennsylvania due in large part to the state’s strong manufacturing sector and the heavy production of shale gas. ProChemTech just finished construction of a 4,000-sq.-ft. office and laboratory space in Brockway, Pennsylvania. And PixController is in the process of expanding its operations to a recently renovated 70,000-sq.-ft. manufacturing facility in Export.
It was a perfect mix of location, innovation and collaboration that led to the recent shale surge. “Our state agencies reacted positively to the opportunity while also acting aggressively to implement safeguards to ensure that the development of the resource is being done in an environmentally sound manner,” says Hall. “The Commonwealth is well-positioned to be a dominant force in the industry.”