Two South Korean battery makers are slugging it out on U.S. soil, and the ultimate loser could wind up being the state of Georgia, which has a massive stake in the rival companies’ battle over trade secrets.
SK Innovation broke ground in March 2019 on the first of two EV battery plants at a sprawling site fronting I-85 northeast of Atlanta. Encouraged by $300 million in public grants, free land and other incentives, the $2.6 billion project, spread across 283 acres (115 hectares) in Jackson County, has been hailed as one of the largest economic projects in Georgia history. The company has pledged to hire 2,600 workers by 2024. County officials expect tax revenues to pour tens of millions of dollars into the public-school system.
But merely a month after the official ground-breaking, rival battery supplier LG Chem filed trade complaints against SK Innovation, accusing it of stealing battery technology secrets by hiring scores of former LG employees. The complaint seeks to block SK from producing battery cells in the United States and importing necessary components.
“In a worst-case scenario,” reported the Atlanta Journal-Constitution in late October, “some officials have said that SK may be forced to abandon the project.”
SK isn’t acting like a company that’s running scared. In June, the company announced an additional $940 million investment for a third building at the complex. That same month, it donated $400,000 toward Augusta University’s coronavirus response. Construction at the site continues apace for an initial 2021 launch that officials say remains on target.
“They’re still going full steam,” says John Scott, director of economic development or the Jackson Area Chamber of Commerce. “That wouldn’t be the case if they thought they were going to cancel. This being such a high-profile project,” he tells Site Selection, “is the kind of thing that’s really easy to blow out of proportion.”
The U.S. International Trade Commission, on Oct. 26, postponed for a second time a decision on LG Chem’s complaint. Some suggest that the delays underscore the Commission’s delicate position in a case that involves thousands of jobs and billions of dollars. The postponement, until Dec. 10, could give the two companies additional time to reach a settlement. The commission’s ruling will be subject to appeal.
Separately, LG Chem said in mid-October that it is considering expanding in the U.S. and Europe in an effort to triple production of its cylindrical EV batteries to meet surging worldwide demand. LG’s biggest customer, Tesla, is launching massive, new EV factories being constructed in Berlin and Austin, Texas.
“Sales are continuously expected to grow thanks to greater shipments of automotive batteries and cylindrical batteries for EVs,” said the company, which also supplies General Motors, Volkswagen and Hyundai. LG Chem did not release details of potential locations or a timeframe to scale up production.
LG Chem and General Motors are in partnership to build an EV battery factory in Lordstown, Ohio. The joint venture, named Ultium Cells LLC, began excavation at the Lordstown site in May. GM Chief Executive Mary Barra says the 50-50 joint venture is aimed at “dramatically enhancing electric vehicle affordability and profitability,” and will accelerate the automaker’s initiative to introduce 20 new electric vehicles globally by 2023.
The Ultium facility, to be built near GM’s closed assembly plant in Lordstown, is to employ more than 1,100 workers. In late September, Ohio ordered GM to pay back $28 million in tax credits it received as part of a 2008 agreement under which the company had agreed to keep 3,700 workers at the plant through 2028. GM shuttered the plant in March 2018, with a loss of some 1,400 jobs.
Here Come the Electric Trucks
In October, the new Lordstown Motors, which purchased the GM complex last fall, was listed on Nasdaq’s Global Select market after merging with DiamondPeak, an acquisitions company. The financial moves are expected to enable Lordstown to launch production next year of its electric truck, named Endurance. CEO Steve Burns told the Detroit News Oct. 26 that he wants to be first to market among the intensely awaited, initial wave of electric pickups expected to hit the road next year.
“Since we’re in a race to be first,” Burns said, “it was really important for us to get that funding, so that we could be assured of production by September.”
At least half a dozen electric pickups have been promised for delivery in 2021. In addition to Endurance, they include Atlas XT, Bollinger B2, GMC Hummer EV, Nikola Badger, Rivian’s R1T and Tesla Cybertruck.
In September, Ford confirmed groundbreaking at the site of its newly announced $700 million Rouge Electric Vehicle Center in Michigan, where it’s to build an all-electric line of the iconic F-150. The investment follows the automaker’s pledge to spend $11.5 billion to produce more than a dozen electrified models by 2022.
Ford says the lifetime cost of ownership of the all-electric F-150 will be half that of the current standard model, excluding initial purchase price. The company says it will have more power, produce more torque and accelerate faster than any current F-150. Chief operating officer and CEO Jim Farley describes it as “a seriously capable, purpose-built tool for serious truck customers.”
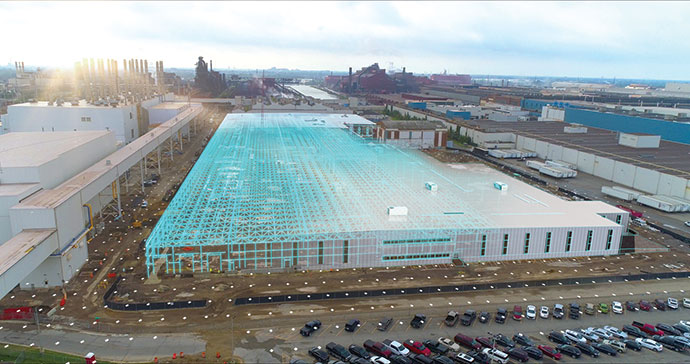
The new manufacturing center at the Dearborn-based Rouge Center, once complete, will add 300 jobs and is part of a $700 million investment in building the all-new F-150 lineup, which also includes an F-150 PowerBoost hybrid. The new jobs, the company says, will support battery assembly and production of the F-150 PowerBoost hybrid and fully electric F-150.
Including investments for Bronco and Ranger at the Michigan Assembly Plant in Wayne, Michigan, announced last year, Ford plans to invest more than $1.45 billion and create approximately 3,000 jobs over the next three years in Michigan alone.
“We are proud to once again build and innovate for the future here at the Rouge with the debut of our all-new F-150 and the construction of a modern new manufacturing center to build the first-ever all-electric F-150,” said Bill Ford, executive chairman, Ford Motor Company. “This year’s COVID-19 crisis made it clear why it is so important for companies like Ford to help keep our U.S. manufacturing base strong and help our country get back to work.”
Europe Steps Up Its Game
Groupe PSA/Opel and Total/Saft, in September finalized a joint venture to develop and produce EV batteries at gigafactories planned for Douvrin, France, and Kaiserslautern, Germany. The JV, called Automotive Cells Company (ACC), represents an investment of close to $6 billion. The project is being subsidized by the German government.
Germany’s Economics Minister Peter Altmaier said in late October that Europe will need to produce nearly one-third of the world’s supply of EV battery cells by 2030 to remain competitive.
“More than 20,000 jobs could thus be created in the 2020s,” Altmaier said in remarks at an online event hosted by the European industry group ACEA. “We want Germany and Europe to account for 30% of the global production of battery cells.”
Spanish automaker SEAT, a Volkswagen subsidiary, has initiated investments totaling some $6 billion in new production facilities in Barcelona and at its main production plant in nearby Martorell. The company plans to launch production of electric vehicles in Martorell in 2025.
In October, SEAT began construction of an $8 million electric laboratory at the Martorell facility to develop and test battery systems for electric and hybrid vehicles.
“SEAT has been committed to the electrification of the company for years, and the construction of this unique new Test Center Energy in Spain is a firm step in this direction,” says SEAT’s head of development Werner Tietz. “This new battery lab will enable us to develop the energy systems of future hybrid and electric vehicles, thus contributing to the creation of sustainable electromobility.”
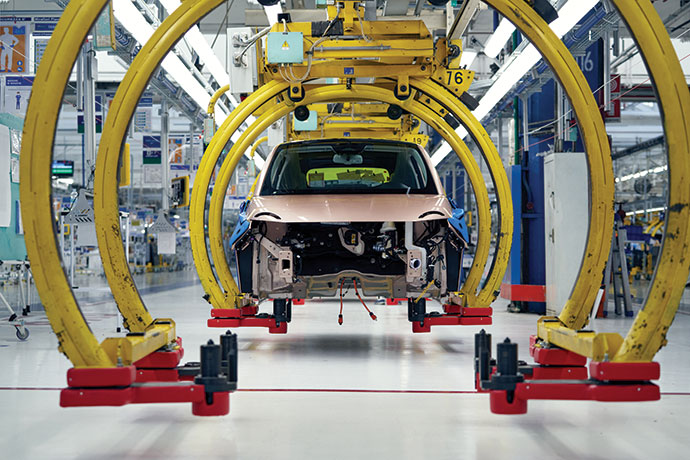
FCA in October unveiled the third and final model of its revived Fiat 500 series. The Fiat 500 3+1, like its two earlier partners in the all-electric class, is being manufactured at FCA’s 81-year-old Mirafiori plant in Turin. Italy. With some 20,000 workers in production, engineering, sales and financial services, it is the largest manufacturing facility in the FCA universe.
FCA has committed to investing some $6 billion in the plant, its single largest investment in electric vehicles to date. The investments include a new assembly line expected to produce up to 80,000 units of the electric 500 and a new electric battery complex.
“The automotive industry is undergoing a period of profound change and one of the major trends is closely linked to electrification,” said Pietro Gorlier, COO for FCA’s EMEA Region. “With its new car battery assembly center at Mirafiori, FCA accelerates its drive to electrify, adding now another element to the ‘ecosystem’ that starts from supply chain and ends with customer support.”