Additive manufacturing, known better as 3D printing, is under way in lots of locations. But when a cluster for this embryonic industry sector is born, it will be in northeast Ohio. And the due date is fast approaching. Youngstown is the home of America Makes — the National Additive Manufacturing Innovation Institute, a consortium of 100 companies, non-profit organizations, academic institutions and government agencies from around the US that was founded in August 2012 to make the US additive manufacturing industry more competitive. The Institute is organized by the National Center for Defense Manufacturing and Machining, which was awarded a $30-million public-private partnership for development of the network.
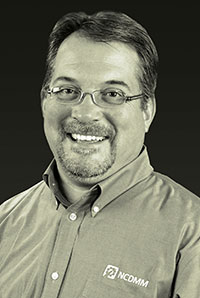
Scott Deutsch, communications and special programs manager, America Makes
“We are a research institute whose primary function is to move an already exciting set of companies, resources and technologies forward,” says Scott Deutsch, manager of communications and special programs at America Makes. “There are hurdles that these organizations face, whether it’s materials characterization, process validation, inspection, design — these are key problems the industry faces at large. With some public money and some private money, we can do the necessary research to advance the entire industry forward.” The institute is currently working on 22 projects, says Deutsch.
“As these projects realize their results, those results become available to any institute members. We’re not looking to commercialize anything, but for industry to commercialize, to get it to the factory floor.”
Members include large aerospace manufacturing corporations, such as GE Aviation, Boeing and Lockheed Martin, seeking to better understand material properties so they can trust the componentry they are making with additives for use in critical applications; makers of 3D printing systems, like Stratasys, Inc., ExOne and 3D Systems Corp.; materials suppliers; several federal departments; more than a dozen major universities and research institutions, including the Oak Ridge National Laboratory; and other enterprises.
“The R&D required to get materials to work together to produce something can be expensive and risky and beyond the reach of some companies in terms of capital to invest in that R&D,” says Deutsch. “By pooling our resources together in a public-private, one-to-one cost share, we can all move forward together.”
Three other advanced manufacturing institutes now exist — the Digital Manufacturing and Design Innovation — or DMDI — Institute team headquartered in Chicago and led by UI Labs; one at N. C. State University in Raleigh, focused on wide bandgap semiconductors; and the Lightweight and Modern Metals Manufacturing Innovation — or LM3I — Institute team, headquartered in the Detroit area and led by EWI.
“Additive manufacturing and other advanced manufacturing technologies are key to keeping manufacturing here in the US and keeping us globally competitive.”
— Scott Deutsch, America Makes
“There is a proposed network of up to 45 of these institutes that would focus on key areas,” notes Deutsch. Part of the reason additive manufacturing research is focused in northeast Ohio is that Youngstown and Cleveland are located within relative proximity to much of the manufacturing in the US.
Made in the USA
“This is where things are made,” says Deutsch. “Additive manufacturing will allow us to make the things that could not have been made by traditional means, particularly applications that are low volume and require a high degree of customization, such as dental, orthopedic and prosthetic devices requiring patient-specific, digital data converted into a specific device manufactured for a specific patient. And the bio-medical area is very hot in this part of the country.”
Deutsch says additive manufacturing is putting manufacturing back in a region that was once synonymous with it.
“Manufacturing went away from here because we allowed global forces to take over, we let other things get in the way,” he points out. “If we manufacture in this country, our economy is strong. Our middle class is strong. We are a strong nation when we make things. If we allow them to be made elsewhere, we lose that. Additive manufacturing and other advanced manufacturing technologies are key to keeping manufacturing here in the US and keeping us globally competitive. It’s one thing to say we design it here, but it’s made overseas. Well, eventually, design will happen overseas, too. We need to have design here and manufacturing here. The more we realize the benefits of what additive can do, we won’t necessarily make cars additively, but we can make tooling and parts that help fixture the cars additively and help reduce the costs of the end product. Manufacturing is pivotal, and we’re proud that this type of manufacturing is here. It’s about time we did these things to keep manufacturing alive and moving forward.”
Industry Advocate
The Manufacturing Advocacy & Growth Network (MAGNET) is a Cleveland-based incubator that supports, educates and champions manufacturing in the region. It’s part of the Ohio Manufacturing Extension Partnership (MEP) program funded by the state and federal MEP funds from the National Institute of Science and Technology, which is part of the US Department of Commerce.
“We work with manufacturing companies in the region to help them grow through new market development, adoption of new technologies and innovation strategies in general,” says MAGNET President Dan Berry. “Part of our mission is to move our region toward a center of advanced manufacturing.”
MAGNET worked with the National Additive Manufacturing Innovation Institute in Youngstown and with western Pennsylvania — including Carnegie Mellon University and other groups in the Pittsburgh area — to put together the proposal that led to the creation of America Makes. He says that securing the consortium for the region has helped accelerate its becoming a center of advanced manufacturing.
“Prior to that victory, we had a lot of potential but we needed a catalyst to help unleash it. We had some good academic capabilities at Case Western Reserve University and the University of Akron, and we have a number of companies that were dabbling in additive. But by ourselves, I don’t think we had the critical mass. Pairing up with western Pennsylvania and the National Center for Defense Manufacturing and Machining in Latrobe, Pennsylvania, and adding up the assets in northeast Ohio and western Pennsylvania, it gave us the ability to craft a proposal that was very competitive.”
Today, says Berry, the region has three attributes that make it ripe for additional growth in the additive manufacturing sector. The first is the presence of hundreds of manufacturing companies that will be directly and significantly affected by developments in the 3D printing field — metal fabricators and machining companies in particular. “We have a lot of people who stand to benefit from understanding the potentials of that technology and how to use it productively rather than being run over by it,” he says.
Second is industry sectors in the region that already use the technology in a significant way, including aerospace suppliers and bio-medical companies. “Their manufactured parts lend themselves to additive technology, because they involve high-value, small-batch production,” Berry relates. “Cost is not the major issue — it’s the quality and the ability to machine the parts correctly.
The third attribute is the region’s expertise in formulating the materials required for additive manufacturing. “That’s a real strength of this area both within our companies that do coatings and metal treatments and also our polymer base of companies. They will be key contributors to making additive manufacturing more usable.” Areas outside the immediate region also contribute to its success, such as Wright-Patterson Air Force Base in Dayton and GE Aviation in Cincinnati, which Berry says are heavily involved with America Makes. “There are a lot of pieces and parts around the state that make this a good location for this technology expertise. There is only one national additive manufacturing center in the US, and it’s in northeast Ohio. It is a real asset for the region.”