M |
ONTGOMERY COUNTY, Md. — Can the building blocks of life become the foundation of a new economy? They can if the companies mapping the human genome happen to be in your own backyard.
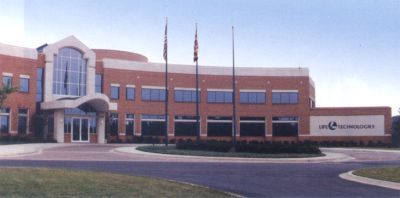
which is also home to the federal Food and Drug Administration and the National Institutes of Health.
Stretching along 15 miles (24 kilometers) of Interstate 270 from Bethesda to Gaithersburg, Md., the so-called “DNA Alley” in Montgomery County has become the anchor of the nation’s third largest biotech community. Home to 200 of Maryland’s 300 life sciences organizations, the county’s map now reads like a Who’s Who of the human genome project: Celera, Human Genome Sciences, Gene Logic, Origene, the Institute for Genomic Research and others.
For prospective corporate real estate deal-makers, that’s a “gene pool” of talent that cannot be found anywhere else in the United States.
“We have a high level of intellectual employees and employers clustered in this county,” says Stephen L. Christian, business development specialist for the county’s Department of Economic Development. “Our focus is on growing from within as well as growing from the outside, with the right type of employers who need what we have to offer. That’s why we call Montgomery County ‘the Idea Location.'”
That’s also why the editors of Site Selection magazine have identified Montgomery County, Md., as one of five hot high-tech markets to watch. Like Central Florida; Huntsville, Ala.; Kansas City, Mo.; and Albuquerque, N.M., Montgomery County is an emerging market that offers a base of high-tech talent and industry to rival most cities of much larger size.
The latest numbers show that more than 63,000 people work in private-sector high-tech jobs in Montgomery (pop. 860,000), representing 15 percent of the 420,000 jobs in the county. The largest group of high-tech jobs is in information technology (25,400), followed by aerospace (16,000), biotechnology (11,700) and telecommunications (10,500). Another 40,000 people in Montgomery work at one of the 19 federal agencies in the county, including the National Institutes of Health (15,500 jobs) and the Food and Drug Administration (4,600).
Possessing one of the largest concentrations of scientists and engineers in the nation, Montgomery boasts one of the highest educated and most affluent work forces in the United States. The average household income is US$120,700. An estimated 60 percent of adults in the county hold a bachelor’s degree and more than 30 percent hold a graduate or professional degree. Many of these grads come from the nearby campuses of Johns Hopkins University and the University of Maryland.
More than 3 million sq. ft. (279,000 sq. m.) of new commercial space came on line last year in Montgomery, where the rental rate for new office space ranges from $29 to $42 per sq. ft. But the county’s leaders say they are determined to manage growth in an orderly fashion.
“We don’t recruit heavy manufacturers,” says Christian. “We recruit corporate headquarters, high-tech and biotech. Our real estate market has remained stable and strong because we have a really excellent mix of the right kind of companies. We don’t have the boom-and-bust problem that other areas have experienced with the dot-com failures.”
Several leading commercial real estate service providers have recognized this market’s potential and moved in to take advantage of it. The Staubach Co., for example, opened an office in Bethesda to meet the needs of its growing client list in the area.
“We recently represented Manugistics Inc. in the relocation and consolidation of its corporate headquarters,” says James Cahill, president of Staubach’s Maryland office. “This 210,000-sq.-ft. (19,530-sq.-m.) build-to-suit will deliver in the spring of 2002.”
Land of Magic Home to Florida’s High-Tech Corridor
Think that Tampa and Orlando, Fla., are only the land of sun, fun and Mickey Mouse? Think again. According to a report released recently by the American Electronics Association and the NASDAQ Stock Market, Central Florida is home to one of the fastest-growing technology markets in the country.
Tampa, Orlando and Melbourne, Fla., all boast extremely strong technology bases and are adding new high-tech jobs faster than the national average. Tampa’s 42,809 high-tech employees earn an average annual salary of $46,900; Orlando’s 31,200 tech workers earn an average of $48,100; and Melbourne has 19,500 tech workers earning an average of $44,500.
“There are more than 5,300 high-tech companies employing more than 160,000 high-tech workers along the Florida High-Tech Corridor,” says Randy Berridge, president of the Florida High-Tech Corridor Council. “Many of these companies are engaged in manufacturing. However, there are a number of initiatives under way to make the state even more attractive to high-tech manufacturers, not the least of which is Gov. Jeb Bush’s focus on work-force development. Workforce Florida is a statewide effort to put all the necessary resources to work to assure Florida will be able to meet the needs of high-tech employers.”
added 100 high-wage, high-skill jobs to the Central Florida market.
The Corridor Council — a public/private initiative that is anchored by the University of South Florida in Tampa and the University of Central Florida in Orlando — has played a pivotal role in several major corporate real estate deals along Interstate 4. Just two years ago, Cirent Semiconductor committed $700 million to upgrade and expand its Agere microelectronics fabrication facility in Orlando. Today, Cirent produces more semiconductors in its two local cleanrooms than all other Agere locations combined.
The council also secured Lucent Technologies’ $300 million investment into a new Bell Labs Advanced Development and Research Facility in Orlando on the campus of Cirent Semiconductor. The deal made the Cirent location Lucent’s flagship research facility.
Other high-profile corporate announcements include Uniroyal Optoelectronics’ expansion in the Tampa Bay Area. After studying five different states and weighing factors such as fast permitting and access to academia, Uniroyal established a 77,000-sq.-ft. (7,161-sq.-m.) facility in Tampa. The $35 million investment resulted in 100 high-wage, high-skill jobs for the local economy.
“In Hillsborough and Pinellas counties, we have a blend of technology-driven companies,” says Robin Ronne, head of the Tampa Committee of 100. “It all goes back to the University of South Florida College of Engineering, a statewide-designated center of excellence for microelectronics engineering. Also, our USF College of Business’s Department of Information Sciences and Decision Systems is one of the top-five rated programs in the country.”
Without this higher-education infrastructure, Ronne says, Tampa would not have secured the $113 million, 1,500-employee, 450,000-sq.-ft. (41,850-sq.-m.) global headquarters of J.P. Morgan Treasury Technologies/Chase Manhattan Securities. This one business unit, he says, provides all of the software development for the movement of some $1.6 trillion in global transactions every day.
Albuquerque: Federal Labs Spur Private Industry
Approximately 90 percent of today’s kindergartners will work at jobs that don’t yet exist, according to the U.S. Department of Labor. In New Mexico, scientists and engineers at two federal research labs are busy developing the technology that will create many of those jobs.
Sixty years ago, these scientists helped build the atomic bomb. Today, they are building companies like EMCORE Photovoltaic in Sandia Technology Park in Albuquerque. A manufacturer of solar cells, optical components and networking products, EMCORE expanded by 36,000 sq. ft. (3,348 sq. m.) in December 2000.
Howard Pollard, director of space programs and solar cells for EMCORE, says that without the support of the Sandia National Laboratories, his company would not exist today. “EMCORE is a direct technology spinoff of Sandia Labs,” Pollard says.
“Legislation that was passed at the federal level in 1989 opened the door for technology transfer out of the national labs. Sandia and the Technology Ventures Corp. (TVC) made it possible for two entrepreneurs to leave the federal labs and develop EMCORE.”
Today, the company manufactures the solar cells that are used in communications and military satellites. EMCORE’s sales have grown from $9 million in 1994 to $93 million in 2000. Its work force of 115 includes about a dozen staff scientists.
“We are effectively doubling our solar cell production capacity with three new reactors,” Pollard says of his firm’s recent expansion.
More than 6,800 people work at Albuquerque’s Sandia National Labs, the anchor of the area’s high-tech economy. Some 4,500 of these employees have master’s degrees, and 1,500 hold Ph.D.’s. Within the entire corridor of Albuquerque and Los Alamos, there are nearly 4,000 Ph.D.’s and more than 8,000 master’s degrees. More than $4 billion is spent on research and development in the region each year.
Thirteen area colleges and universities have a combined enrollment of 50,000 students. The largest school, the University of New Mexico, has 30,970 students, with 5,200 enrolled in graduate and professional programs. The university also produces 80 percent of New Mexico’s Ph.D. candidates. UNM’s research facilities include the Center for High Technology Materials, Clinical and Magnetic Resonance Research Center, High Performance Computing Education and Research Center, Microelectronics Research Center and four other specialized high-tech programs.
But the real reason corporate employers are flocking to Albuquerque, however, is this fact: The Albuquerque work force generates 31 percent more productivity than the U.S. average for the same payroll dollars, according to a Grant Thornton research study. In fact, three separate labor studies have ranked New Mexico’s work force as the most productive in the nation.
“Albuquerque is the No. 1 market in the U.S. for electronics and the seventh-fastest growing high-tech market in the country,” says Michael Skaggs, president of venture capital firm Next Generation Economy in Albuquerque. “People are coming back to New Mexico because of the energy and opportunity here.”
Huntsville: Technology Transfer in the Space Age
Space may be the “final frontier” in the Star Trek universe, but it’s just the beginning of technology transfer in Huntsville, Ala. A community of 158,000 people in North Alabama, Huntsville ranks fifth in the nation in software employment, according to the Software & Information Industry Association.
Many of these jobs are direct descendants of the establishment of the Marshall Space Flight Center in northern Alabama in 1960. Today, workers at the space center assemble payloads for the International Space Station Freedom, while clustered around it thousands of workers apply their skills in electronics, aerospace, software development and data transmission.
An estimated 1,000 high-tech firms in Huntsville employ more than 25,000 people. Last year, venture capital firms invested $66 million into businesses in this area — up from $2 million in 1999.
Why the sudden surge in high-tech growth? “One thing Alabama has done well recently is step up to the plate to make sure that the deal is done,” says Alex Hardy of the Huntsville-Madison County Chamber of Commerce, one of the organizations leading the effort to attract a semiconductor fabrication plant to the Huntsville area.
Working with the newly formed Alabama Semiconductor Alliance, the Huntsville region has hired the Lockwood Greene Microelectronics Engineering Group to “pre-certify” sites for chip plants. Two sites in Huntsville each have more than 200 acres (80 hectares) of available land, are serviced by more than 10 million gallons of water per day, carry 16-kilovolt transmission lines and 400-megawatt power capacity, and have access to more than 280,000 cubic meters (73.5 million gallons) of natural gas per day.
Much of the high-tech growth in Huntsville has occurred at the Cummings Research Park (CRP). With 220 companies occupying 8.5 million sq. ft. (790,500 sq. m.) and employing more than 22,000 people in 33 different high-tech fields, CRP is the second-largest research park in the country (Research Triangle Park in Raleigh, N.C., is No. 1).
Major companies in CRP include Boeing, Hewlett-Packard, Scientific Atlanta, Red Hat Inc., Adtran Inc., Motorola, Lockheed Martin, Northrop Grumman, Raytheon and Xerox. The park is also home to the Alabama Supercomputer. BellSouth has spent more than $112 million to transform CRP into a nationally recognized test center for telecommunications technology.
Kansas City: Thriving Center of Life Sciences Research
Kansas City bills itself as the “Heart of America” at the crossroads of the country’s geographic center. But Kansas City plans to put itself on the map for another reason. The city hopes to become the US’s center for life science research. The KCCatalyst, a combined effort by many KC area institutions to promote hometown high-tech growth, and the Kansas City Life Sciences Institute, a combination of six local medical and research facilities, are two new projects which hope to spotlight the city.
“There’s an economic downturn,” said Joe Kessinger, president of Kessinger Consulting Associates of Kansas City. “And the city is forced to develop a strategy to revitalize.”
Enter the KCCatalyst, a strategic plan for promoting the KC area technology community. The effort will combine emerging technology companies, academic and research institutes, and financial and professional services.
Two wealthy Kansas City cancer survivors, Jim and Virginia Stowers, were the impetus behind the Kansas City Life Sciences Institute. The couple wanted to spend their fortune on a biomedical institute in their hometown. Their initial donation of $515 million founded the Kansas City Area Life Sciences Institute.
The combination of hospitals and research facilities will seek to bring in $500 million per year for financed research. The institute has identified five areas for advanced studies: cancer, human development and aging, cardiovascular, and infectious and neurological diseases.
The Stowers Institute of Medical Research opened in late 2000 and is the centerpiece for the Kansas Life Sciences Institute. The Stowers Institute has a $360 million grant and is considered one of the best-funded medical research centers in the world. With help from the National Institute of Health and other organizations, the Kansas Life Institute estimates that the city’s annual biomedical effort could expand from $100 million to $500 million. That’s a large welcome mat for world-class researchers as well as high-tech biomedical businesses.
In early 2000, Bayer announced a $200 million plant expansion in northeast Kansas City. The company will produce ingredients for two new drugs: Avelox, an antibiotic used to treat respiratory disease, and Baycol, a new cholesterol-reducing drug. This expansion is part of the company’s five-year $5 billion plan that includes the construction of two additional plants in the Kansas City area. Company officials said they value Kansas City’s work force and location.