Chinese-made fireworks, considered the world’s best by a long shot, will light up US skies from coast to coast this weekend, in part because they offer such a vivid array of colors. The lighting products made there, however, are frequently called inferior for the same reason.
Five years ago, Charlie Szoradi, the chairman and CEO of Independence LED, based in the Greater Philadelphia suburb of Wayne, Pa., was fed up with quality issues emanating from outsourced manufacturing in China, led by an inconsistent color palette range. So he put NASA to work as a site selection tool, calling up nighttime images taken by space shuttle crew members as they orbited past the United States. When considering brightness as a site selection factor, a good flow of talent from high-caliber schools usually fits the bill. But Szoradi took it more literally.
“From Washington, DC, to New York is the brightest spot on the planet,” says Szoradi, so it made sense to pick a place somewhere in that Northeast corridor. It was also time for the company to transition from being a value-added reseller (VAR) to an out-and-out manufacturer.
“It was a combination of patriotism — to make something happen in America and create the jobs — and some fundamental math,” says Szoradi. “The product is shipped closer to the end user, we maintain quality, and we reduce the operating expense. There were lots of good reasons to bring it on shore.”
The place Independence picked, two and a half hours from DC and the Big Apple, was Boyertown, Pa., where Advanced Electronic Assembly employees make the heart of the final linear tube product, placing about 15,000 diodes an hour onto circuit boards. Independence also now has a second facility in the Philly suburb of Norristown, Pa. Module housings come from Lamar Lighting on Long Island, and aluminum for the company’s patent-pending beam angle adjustable deep-fin heat sinks comes from New Jersey. About 50 employees cover the bases on production.
Szoradi says that particular patent-pending innovation was another site selection factor, since incorporating the deep-fin heat sink into the product would make manufacturing and shipping from China costlier than sourcing locally in the US. The heat sink is also an advantage to end users of his firm’s products:
“Independence LED’s deep fin aluminum heat sinks are more reliable and last longer than other LED high-bay fixtures that require active fans to keep the diodes cool versus our passive cooling,” he explains. “This is ideal for unconditioned warehouses in southern states and also helps reduce air conditioning loads across commercial properties.”
Genetically Predisposed
Toss in the company’s sales network of 150 at nearly 80 resellers, and you have the ingredients for an American success story. But that’s nothing new for Szoradi’s family, which has been patenting innovations and making products for four generations, with an awareness of energy usage and buildings that goes back just as far.
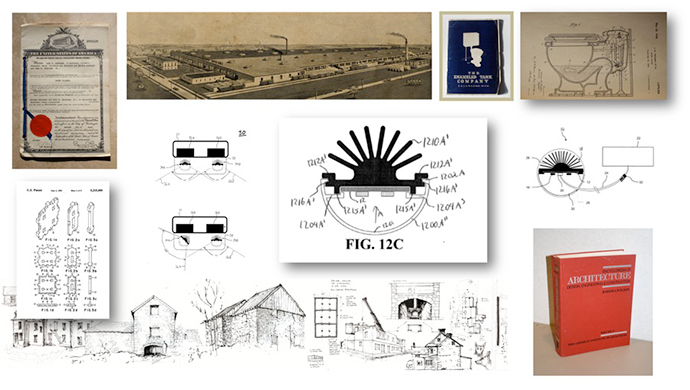
His great grandfather Carl Zwermann invented several components of the modern toilet, establishing major production plants in Michigan and Illinois in the first few decades of the 20th century that used innovative thermal management to increase efficiency in the porcelain kiln and drying processes. Szoradi’s wife Cynthia’s great grandfather, meanwhile, in 1904 launched Colorado-based real estate firm L.C. Fulenwider, which today still holds Colorado Real Estate License #1 as its focus has evolved toward sustainability. “It’s more important to us to do it right, than to do it right now,” says the company’s president L.C. “Cal” Fulenwider III.
Zwermann’s company made special plumbing fixtures for the US Army and Navy during World War II (a relationship Szoradi continued in 2011 with his first installation of LED solutions for the armed services). Through a series of transactions the toilet manufacturer eventually became part of Ogden Corp., a conglomerate that today has 39,000 employees and a market value of more than $1.3 billion.
Szoradi’s grandfather Clyde Hill left the family firm to eventually found Lancaster Equipment Engineers, specializing in sprinkler systems and fire safety for commercial and industrial facilities. Szoradi’s father Charles, an architect, developed passive solar and sustainable design practices as early as the 1960s. His studies in urban architecture and technology were carried on by his son Charlie, who wrote his 1993 Master’s thesis on environmentally sustainable architecture and “eco-humanism.”
The family tendency toward philosophical illumination gradually grew more literal, as Szoradi’s energy auditing business evolved toward a focus on lighting.
“Twenty to 30 percent of a building’s energy use is illumination,” explains Szoradi. When the company started looking to that niche as an energy use optimization target, lighting manufacturers Sylvania, Philips and GE “had fundamentally not changed the fluorescent tube for a few decades,” he says. Linear tube technology was proved to be better than incandescents in the 1950s, showing a 20-percent wattage improvement by lowering it to 32 watts. “With the LED, we could bring it down into the 18- to 16-watt range,” he says.
Today Independence LED installations grace the ceilings of companies such as MetLife and Morgan Stanley, as well as developments such as New York–based Muss Development’s 1.2-million-sq.-ft. Brooklyn Renaissance Plaza and New York Marriott at the Brooklyn Bridge complex, where Muss leaders expected to see payback on a parking garage retrofit in a mere 18 months.
The retrofits are also taking place among industrial users such as Waters International and Mercedes, which is phasing in Independence LED tubes at its complex in Alabama. Szoradi says the fact that a business case can be made down South, where electricity might be nearly a third the cost of what it is in New England, shows LEDs are here to stay.
The ROI
LEDs have the potential to help building owners and operators write their own success stories, measured in such terms as reduced costs and energy usage, even with the higher price tag LEDs command.
A 2013 US Dept. of Energy report that examined nine major lighting applications where light-emitting diodes (LEDs) are already competing with traditional lighting technologies found that in 2012 LED lighting was responsible for saving 71 trillion British thermal units (tBtu) of source energy, equating to roughly $675 million in energy cost savings. (See graph below.)
It’s only the beginning: “If the U.S. were to make an immediate switch to all LED lighting, the savings that would result is about 3.9 quadrillion Btu (quads),” said the report. “In addition, this estimate is based on current efficacies of LED products. As LED efficacies continue to advance, as is projected by DOE’s SSL [solid-state lighting] program, the energy savings potential will grow.”
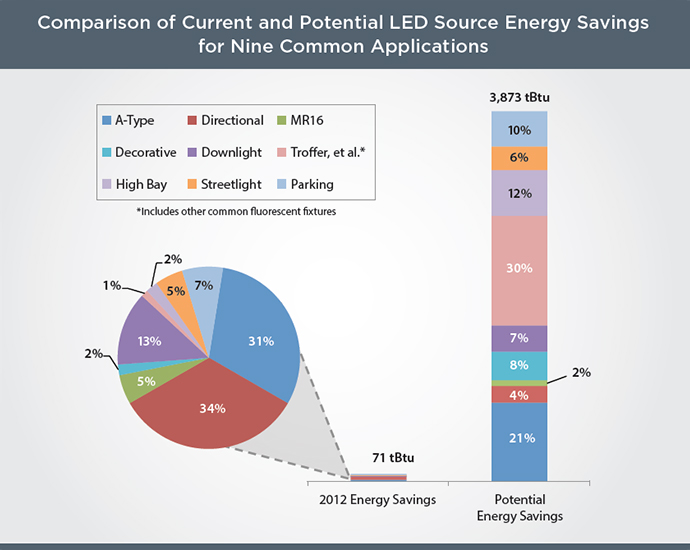
As documented in these pages a few years ago, LED manufacturing is on a roll, with more than one company reshoring manufacturing to the US after encountering quality and logistics issues in Asia. But that doesn’t mean it’s all come back. According to Site Selection’s New Plant Database, over the past five years at least 20 major facility investments have been made in the LED lighting sub-sector, in locations such as North Carolina, Texas, Pennsylvania, New Hampshire and Michigan, but also abroad in Taiwan, Vietnam and the Slovak Republic.
“One of the challenges that will come up is not whether it’s made in the US, but whether the ROI is there,” says Szoradi. “We’re not the size of GE, but we’re able to outperform them in lumens per watt.” His firm also offers a 10-year or 60,000-hour warranty.
In 2012 Independence LED completed the largest LED tube retrofit in US history to date, with over 2 miles (38 football fields) of installed high-efficiency LED tubes at luxury kitchen and bath fixture purveyor Davis & Warshow’s 209,000-sq.-ft. distribution center on 49th St. in the New York City borough of Queens. It was the country’s first facility to achieve net-zero lighting costs with LED tubes thanks to a rooftop solar array installed in 2010 that exceeds the 200,000 annual kWh to power the lighting.
Prior to the conversion — part of the company’s Practically Green program launched in 2008 — lighting equaled nearly 65 percent of the structure’s total power usage, costing almost $50,000 per year. That cost was slated to decrease to less than 50 percent of the building’s total energy use and would cost less than $20,000 per year to run – reducing the company’s lighting tab by 60 percent or nearly $40,000 a year. Davis & Warshow President David Finkel said the company’s investment to convert to the LED tubes was more than $250,000. But part of that was covered almost immediately by incentives from Con Edison totaling $63,704. The utility’s energy efficiency programs helped it earn Newsweek’s ranking this month as the greenest utility in the nation and 16th greenest company overall among the 500 largest global companies and 500 largest US companies examined as part of the publication’s Green Rankings 2014.
Reached by phone this week, Finkel says the projected savings were a bit greater than what’s been realized, in part because his firm was better than it thought at turning off the lights, thanks to auto-motion sensors. “But when comparing fluorescent to LED, every second it’s on there’s a savings,” he says. “We still believe in the ROI on it.”
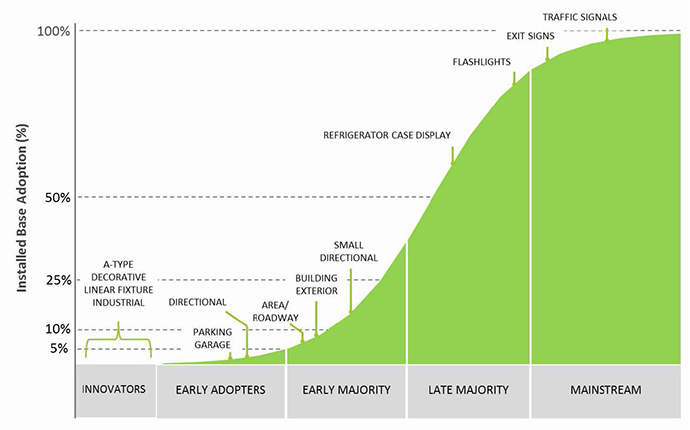
Beyond the direct financial benefit, he adds, is the fact that when you have a warehouse lighted by hundreds of fluorescent tubes, “a good portion of your warehouse is dimmer than it should be. You don’t replace them until they’re out, and then you don’t replace them immediately.” So both safety and productivity are enhanced with the brighter, longer-lasting LED tubes. The effect on workers was immediate, with many asking how many new lights had been added. “The answer was ‘zero,’ ” says Finkel. Workers ferreting out SKUs and barcodes “are loving the fact that it’s bright. It really does make a significant difference.”
Independence offers state-by-state and country-by-country lists of kWh costs, as well as a sample of utility rebates in various parts of the US for a luminaire such as an LED parking garage fixture. Szoradi says top property types for LED installation include those with 24/7 emergency lighting or 24/7 operations, as well as parking garages. “Attendant garages are an ideal sub-set,” he says, “specifically in high rebate areas like NYC and Baltimore, where the rebate covers 100 percent of the cost of the fixture.”
Other candidates include properties with hazardous location fixtures, such as refineries, mines and labs; properties with solar PV panels (so as not to waste hard-earned PV power on inefficient lights); and indoor agriculture operations where grow lights can be customized by plant type.
Full Circle
A different sort of plant type is on Szoradi’s mind.
“We’re now being courted by Pontiac, Michigan,” he says. “We have an opportunity in Sacramento, California, and then one outside Toronto too, all looking for what I would call ‘micro-manufacturing’ — this idea of local, smaller hubs of production.” Other interest is coming from Brazil and from the Slovak Republic, where Romanian aluminum could help supply tens of thousands of tubes for the nation’s healthcare system.
The idea is attractive to Szoradi, not just because of his business philosophy background, but because of the opportunity to customize from what basically amounts to some 1,200 product choices once you consider different varieties of modules, color temperatures, wattage, end caps and lenses his company offers.
“Think of the old adage ‘Think global, but act local,’ ” he says. “It’s the whole trend toward localized production and economic development, supporting the jobs in the region where the product is purchased, and the energy auditing that happens in advance of a sale. Installation can be local, and the jobs in between, including the cardboard boxes, can create jobs in the region, where the environmental benefit also is realized, with an average of 1.34 pounds of CO2 reduced for every kilowatt-hour saved.”
Describing the housing and packaging necessary to ship a parking lot fixture, he says, “it’s crazy to ship that across the country, because you’re shipping a lot of air. We could ship components, or we could have them made in California.”
Either way, the engineering and ingenuity keeps coming, and the future keeps looking brighter. Szoradi could just as easily be talking about his family’s penchant for American innovation when he says this about his company’s market position and continuously improving line of products:
“It’s an interesting dance,” he says. “We’re into our sixth generation of improvements.”