If you had the chance to go from eight bags of fresh caramel popcorn per minute to 30, wouldn’t you?
Fisher’s Popcorn of Delaware thought so too.
That’s how much production capacity will grow for the company thanks to a new $4.85 million facility it’s locating on a 17-acre site in Frankford, Delaware that will more than quadruple space for its manufacturing and wholesale operations and add 20 jobs to its staff of 22. All operations are in Sussex County, a coastal jurisdiction within 100 miles of Philadelphia, Baltimore and Washington, D.C.
In addition to assistance from the Delaware Prosperity Partnership and Sussex County Economic Development, Delaware’s Council on Development Finance approved the company’s request for up to $205,500 in grant funding through the Delaware Strategic Fund’s Jobs Performance Grant and Capital Expenditure Grant programs.
“We’re very grateful for the opportunity to expand our operations while still being part of our local community here in Delaware,” said Fisher’s Popcorn of Delaware Vice President Russell Hall in a release. “This expansion will enable us to bring the classic flavors of the Delaware beach resorts to more people around the country while adding quality jobs in Sussex County. The grant assistance from the state is a key component to making this happen.”
Reached by email, Hall — the great grandson of company founder Everett Fisher — expounded on his company’s site selection process and evolution from shops to e-commerce.
“We are based in southern Delaware, so we wanted a location close to our existing facilities, but far enough away from the beach area to bring the land costs down,” he explains. “There is very little real estate in this area zoned for commercial development, so we purchased a raw parcel of land and rezoned it for our purposes. We just broke ground a few weeks ago on the new building and hope to have it up and running mid-next year.”
“We” in this case includes six family owners of the business, including Hall’s parents and siblings. “We are a fourth-generation business,” he says. “We have slowly added stores over the years at the different Delmarva beach towns. Once we ran out of beach towns, rather than expand into other states — which would have its own set of issues — we decided to channel our efforts into starting a wholesale division. We did that for about 10 years, manufacturing our product in our existing stores for distribution to grocery stores. We’ve now outgrown that and are building this stand-alone facility to serve that purpose.
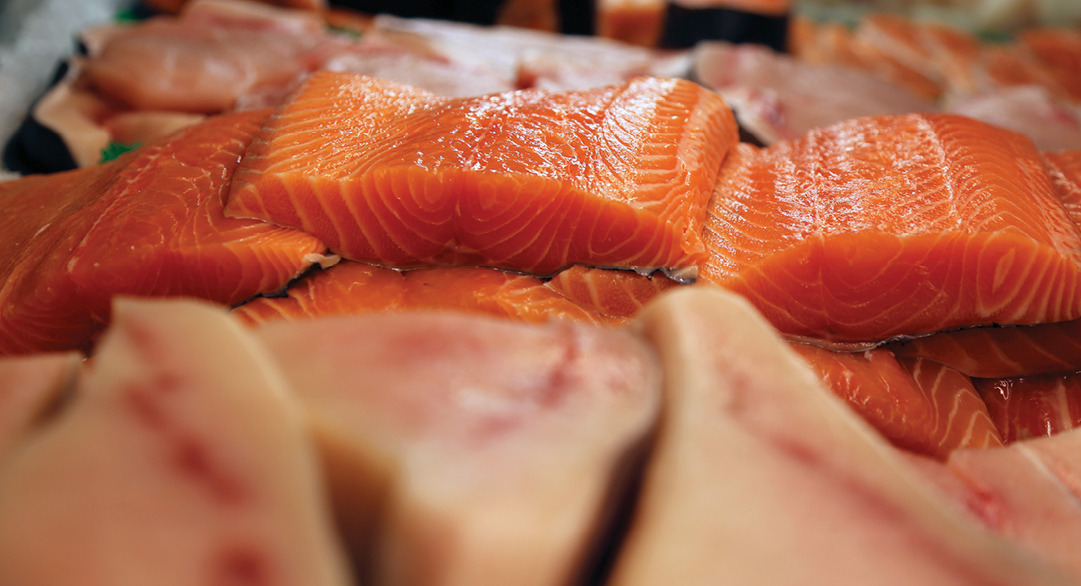
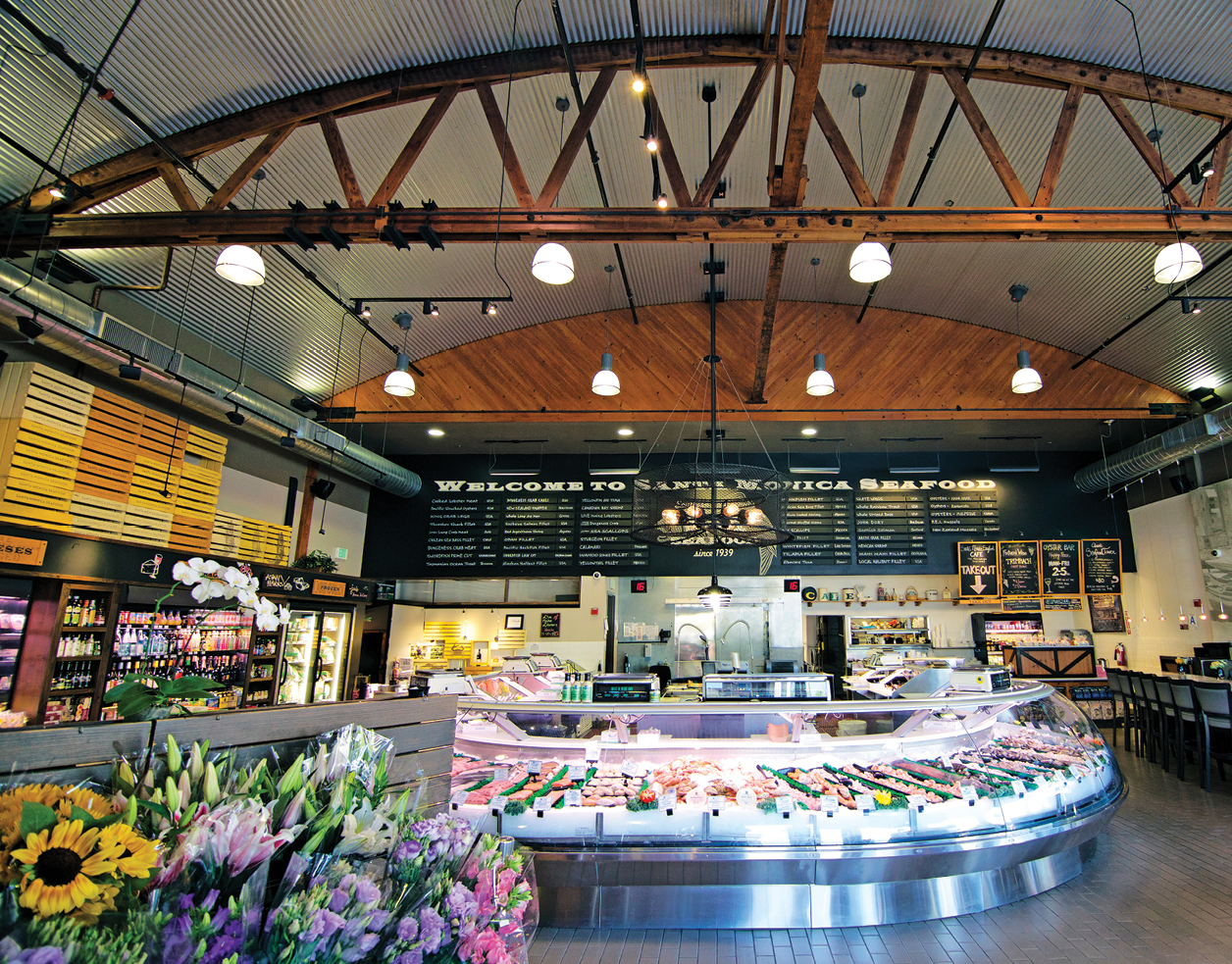
Photos courtesy of Santa Monica Seafood
“The e-com business has been around as long as e-commerce has been a thing,” he says. “Prior to the internet we had a robust mail order via phone/fax business. When I was a kid, we used to hand-write the shipping labels. That has steadily grown over time.”
Meats Company Moves to New HQ in Maryland
There is no shortage of Mid-Atlantic food traditions that go back generations. One even older than Fisher’s is meat processor and purveyor Hahn Bros., also known as Hahn’s of Westminster, which after 127 years is moving to a new, larger headquarters and manufacturing complex about 10 miles up the road in Hampstead, still located in Carroll County in north-central Maryland not far from the Pennsylvania state line.
“Hahn’s site search included out-of-state options, and its decision to remain in Carroll County is a testament to our pro-business environment and the quality of our workforce,” said Carroll County Director of Economic Development Jack Lyburn.
The company, which specializes in smoking domestic pork and beef with hickory wood, stated in a release that it had “experienced significant growth and success over the past few years, necessitating the need for a larger and more modern facility” to serve its customers in Maryland, Virginia and Delaware. The new 54,000-sq.-ft. HQ on a 10-acre parcel will mean increased production capacity as well as more advanced processing technology and equipment. The new facility, said the company, also enables Hahn’s to streamline its operations, resulting in improved supply chain management and faster order fulfillment. A state release said it will lead to a doubling of the company’s workforce. The company currently employs 85 people in the county.
“We are excited about this new chapter in our company’s history,” said Ed Ladzinski, president of Hahn’s of Westminster. “The relocation and expansion of our headquarters enables us to better serve our customers and continue our mission of delivering exceptional products. We are confident that this move brings us closer to achieving our long-term growth objectives.”
“As a company rooted in family values, we are thrilled to announce our ongoing growth and flourishing partnership with Carroll County,” said Hahn’s Assistant General Manager Amanda Ladzinski. “At Hahn’s, we take great pride in our commitment to serving our community and delivering exceptional meat products. Through our expansion, we are excited to continue this journey of growth, working hand in hand with our Carroll County family to meet the evolving needs of our customers.”
The Maryland Department of Commerce is working to approve a $400,000 conditional loan through Advantage Maryland, and is providing a $25,000 workforce training grant through its Partnership for Workforce Quality program. “Carroll County Economic Development has also been working with Hahn’s on its expansion plans over the last few years,” said the state.
Coast to Coast
Follow the food trail to Baltimore and you’ll find a new 26,000-sq.-ft. site taking shape for Santa Monica Seafood that will be the 84-year-old California company’s third location for skin-pack operations. Operations are expected to begin in Q2 2023.
“Since launching our skin-packed seafood program in 2016 in Los Angeles and again in 2018 in Chicago, we have seen explosive growth and tremendous support from our retail partners for chilled, case-ready seafood,” Roger O’Brien, president and CEO of Santa Monica Seafood, said in a January release. “Opening this third location and expanding our services and capabilities to the Mid-Atlantic and New England regions will give us delivery coverage to approximately 40 states, all within a maximum 48 hours of the pack date.
“Our Baltimore site will initially have 8 million pounds capacity for both plain and value-added case-ready seafood, and we have provided for further expansion of packaging lines and additional facility space to expand capacity as our growth continues,” O’Brien explained. “Our Phase 1 program will require an investment of $8 million in leasehold improvements and equipment. As a company, we will have 100,000 square feet of space devoted exclusively to case-ready, chilled skin-packed seafood,” part of 300,000 sq. ft. and 15 facilities overall nationwide.
Project Roundup
The seafood company, as it turns out, isn’t the only expanding Maryland operation with roots in Santa Monica. Here are summaries of that project and others across the region:
Maryland
The same month as Santa Monica Seafood’s announcement, Kite, a Gilead Company based in Santa Monica, announced that it is expanding its global cell therapy supply chain operations in Frederick, Maryland, with a new, centralized 100-job raw materials warehouse that will serve Kite’s global manufacturing network. “As the global leader in cell therapy, it is important to continue to streamline our manufacturing processes to meet the needs of people living with difficult-to-treat blood cancers. Centralizing our raw materials storage and testing will enable us to bring control of materials in-house to increase the speed and efficiency of our global manufacturing operations so we can continue to grow to meet patient demand,” said Chris McDonald, senior vice president and global head of technical operations for Kite, in a January release. “Additionally, by locating these global operations in Maryland, we can serve both our European and California manufacturing operations in the same day. With three major airports in the area, we have increased flexibility in receiving and shipping materials, which is critical for patients who are waiting for our therapies.”
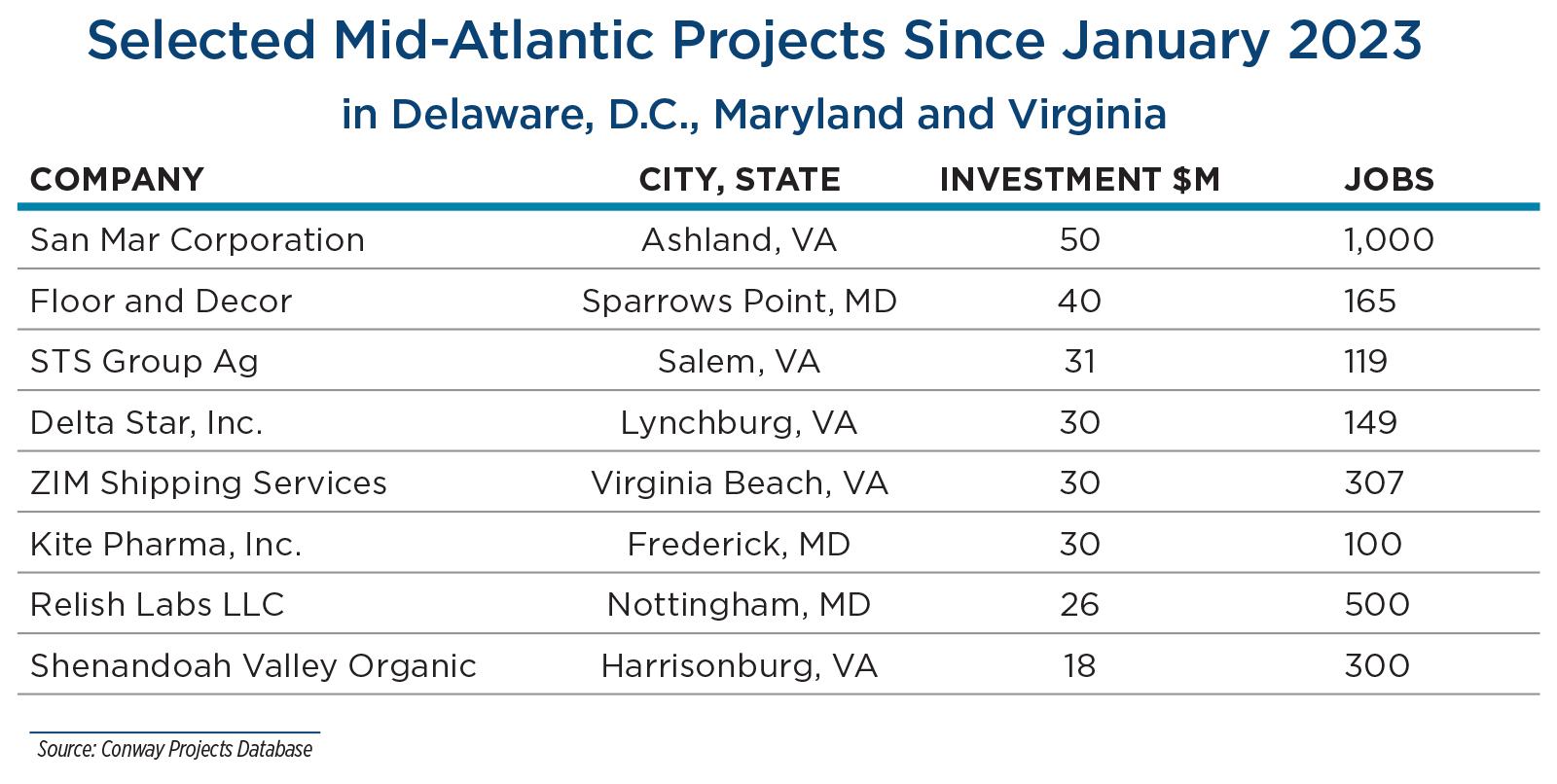
The site will be adjacent to Kite’s manufacturing facility at the Urbana Corporate Center in Frederick. The company expects to employ more than 500 full-time staff in Maryland across both sites by the end of 2026.
Delaware
Agilent Technologies Inc., the analytical instrumentation development and manufacturing company based in Wilmington that employs more than 950 people in the state, announced in June it will invest nearly $22 million modernize and expand its Newport, Delaware, manufacturing facility to meet growing global demand for its biopharma consumables. The move will add 10 jobs to a Newport payroll of 110, and follows an expansion in 2022 at the company’s Little Falls R&D labs in the Wilmington area.
The Newport facility, one of several Agilent manufacturing sites across the United States, produces liquid chromatography columns used for chemical and biochemical analysis, drug discovery, environmental control and analytical chemistry. “Growing worldwide demand for these analytical consumables led the company to review its U.S. facilities to determine the best opportunity to grow production capacity,” said a release from the state, noting engagement with the Delaware Prosperity Partnership. “Agilent’s decision to invest in its Newport site in New Castle County reflects confidence in Delaware’s dynamic business environment and the large pool of regional talent.”
Virginia
Germany’s STS Group AG, a global supplier of interior and exterior parts for commercial and personal vehicles, announced in March it will invest $32 million to establish its North American headquarters in the former General Electric building in Salem, Virginia. The facility bring 119 jobs to the Roanoke region in southwestern Virginia and will supply commercial truck assembly operations and automotive facilities throughout the Midwest and Southeast markets. STS Group AG said it is working with Phoenix Group, the owner of the former GE building, to upfit roughly 200,000 sq. ft. of the existing space and to construct a 32,000-sq.-ft. addition.
The project took a circuitous route to Salem: The company originally had decided on a greenfield project in Wythe County. “Faced with escalating costs of construction, company officials reevaluated the project and identified an existing building to serve the project’s needs,” VEDP explained. “Communication was established with Wythe County officials to ensure state and local interests were maintained during the transition.”
“Salem is a perfect base for STS Group to start its footprint in the USA, following existing customers locally and extending the customer portfolio,” said Alberto Buniato, CEO of STS Group. “On top of a perfect existing location in a suitable industrial cluster, we were delighted to find a very attentive and helpful support with the City of Salem, with Roanoke Regional Partnership, and with Virginia Economic Development Partnership.”
STS has 14 manufacturing facilities in four countries and three continents. It’s the seventh foreign-owned company and fifth nation represented in the Salem manufacturing community.
Another fast-growing company is making use of a redeveloped facility too. RapidFlight, a Virginia-based unmanned aircraft manufacturing company, celebrated its grand opening in July at its headquarters in Manassas, Virginia. The company has grown to more than 50 employees in two years and has sped up production timelines with the addition of additive manufacturing (3-D printing). It aims to create 119 new jobs over the next several years and has invested more than $5.5 million in upfitting the former Georator building to house its growing team.
Manassas is home to operations from Micron, BAE Systems, Lockheed Martin, and Virginia’s busiest general aviation airport at Manassas Regional Airport.