The following appears by permission of the American Short Line and Regional Railroad Association
(ASLRRA, at www.aslrra.org).
In September the American Short Line and Regional Railroad Association (ASLRRA), representing the nation’s 600 Class II and III freight railroads, and five of its member railroads presented at the Surface Transportation Board (STB) hearing, “Growth in the Freight Rail Industry, Docket No. EP 775.”
Over two days, the hearing brought together Class I railroads, short lines, industry analysts, rail customers, rail suppliers, labor organizations and other interested parties to provide an understanding of how the industry has grown and intends to grow in the future to reverse the trend of declining carload volume.
“Growth in the freight rail business is essential to short line railroads,” said ASLRRA Senior Vice President, Law, and General Counsel Sarah Yurasko. “Carload volume is the lifeblood of the short line industry. Short lines keenly focus on retaining and growing carload volume — and will partner with anyone to better serve a customer or build out a rail option for a new customer. Whether it is one carload of scrap a year that is hauled for a one-man scrap sorter, or several hundred carloads a week — there is no customer that our industry will not work to serve and grow business with. ASLRRA firmly believes that the way short lines do business is the reason short lines grow business so successfully.
ASLRRA member railroads commonly highlight four components as critical to short line freight rail growth and success:
1) A deep understanding of their customers — their pain points, their growth strategies — and the ability to provide efficient rail service that is responsive to their specific needs.
2) Investment in infrastructure — always with private funds, but also often supported by state or federal funding. Short lines are willing to invest with the long term in mind and are eager and willing to work with public partners when the opportunity arises.
3) Working closely with local business development groups such as Chambers of Commerce and government groups such as Economic Development Agencies to develop rail-served commercial properties such as business and industrial parks.
4) Strong partnerships with the community and Class Is to develop and efficiently deliver the white-glove excellent customer service our customers depend upon.
Short lines operate 50,000 route miles of track in 48 states, or approximately 30% of the national railroad network, touching in origination or termination one out of every five cars moving on the national railroad system, serving customers who otherwise would be cut off from the national railroad network.
“ASLRRA was pleased to participate in the hearing, and the examples shared are replicated across the nation, day in and day out on more than 600 short line railroads,” said ASLRRA President Chuck Baker. “Short lines are a critical piece of the freight rail network and are unrelenting in their pursuit of growth — one carload, one customer, one market at a time.”
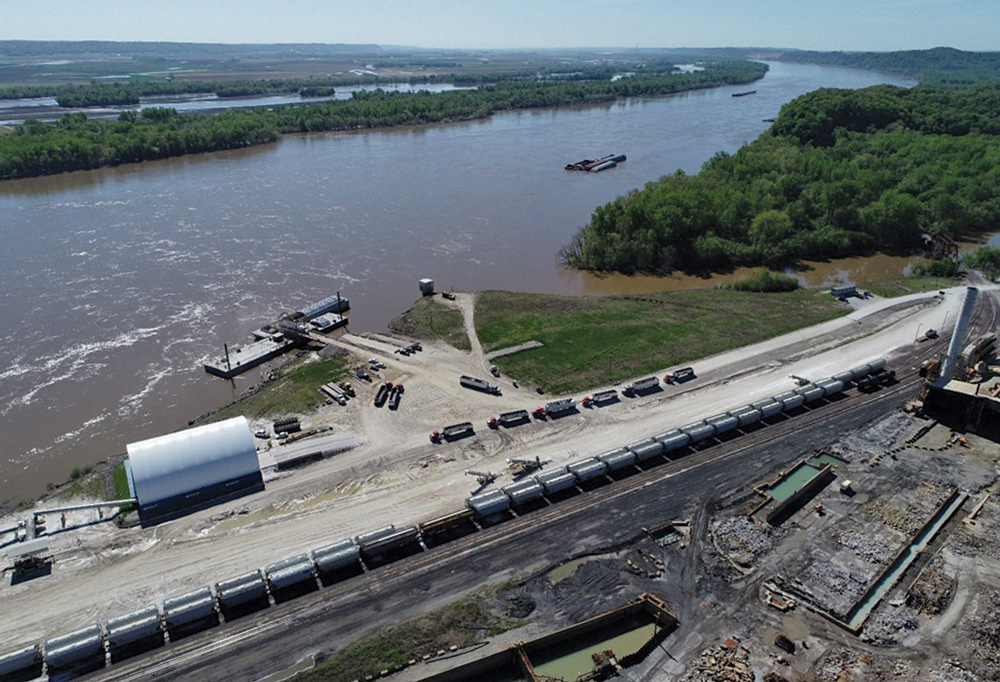
Jefferson County Port Authority (JCPA) in September purchased around 18 acres with 3,000 feet of rail spur connected to Union Pacific Railroad along the Mississippi River in Herculaneum, Missouri, that will serve as the first publicly owned terminal facility in Jefferson County. The facility will continue to be operated by Riverview Commerce Park, LLC, in partnership with JCPA. Approximately 1 million tons of freight moved through the port in 2023, said a release, noting the site’s location less than 2 miles from I-55.
Photo courtesy of St. Louis Regional Freightway
North Carolina Railroad Company
This year, the North Carolina Railroad Company (NCRR) is celebrating its 175th anniversary.

Chartered on Jan. 27, 1849, NCRR maintains a 317-mile rail corridor from Charlotte to Morehead City that serves as the state’s essential conduit.
To keep our state moving at the speed of business, NCRR makes strategic investments and is introducing several new economic development programs in addition to its ‘legacy’ programs.
NCRR Invests:
Since its inception in 2016, the NCRR Invests program has been instrumental in securing new or expanded locations for multiple manufacturing facilities across North Carolina. Overall, NCRR committed more than $18 million of its private revenue, resulting in new or expanded locations for 21 manufacturing facilities and supporting the creation of more than 13,500 new jobs.
As capital investment from these companies exceeds $8.3 billion, addressing freight rail infrastructure needs and prioritizing collaborative partnerships through NCRR Invests are critical components in advancing North Carolina’s economic prosperity.
Build Ready Sites:
Site availability is another key piece of keeping our state competitive. Frequently, companies do not have the time or budget to wait for municipalities to create infrastructure improvements. NCRR’s Build Ready Sites initiative provides essential funding and support to rail-served sites, transforming them into “build-ready” spaces primed for attracting new businesses.
The program eliminates common roadblocks to advancement by ensuring the availability of sites that are ready for immediate development, significantly reducing the time and resources required for new business setups. By addressing these foundational needs, NCRR empowers communities to proactively attract new businesses, create jobs, and bolster local economies. To date, NCRR committed more than $7.8 million to 16 sites in 14 counties across North Carolina.
In 2024, NCRR enhanced its economic development program portfolio, including:
The Brownfields Program:
As a supplement to Build Ready Sites, this program will invest in environmentally challenged industrial sites to create more build-ready, rail-served sites that can attract new businesses to the state, create jobs, and increase freight rail usage.
The Microgrants Program:
Provides funding applicable towards due diligence studies, intended to eliminate barriers to entry for site development. These due diligence needs include Phase I and II Environmental Site Assessments, wetland and stream delineations, boundary and/or ALTA surveys, geotechnical reports, title opinions, and more.
The Wetland Mitigation Program:
Connects economic and industrial developers with wetland mitigation credits, encouraging regulatory compliance, streamlining the permitting process, and maximizing land use and cost savings for new projects. The program aims to preserve and restore North Carolina’s wetlands while balancing the needs of our state’s growing economy and future industrial development projects.
NCRR Services:
In additional to NCRR’s economic development programs, NCRR provides a suite of services designed to help current rail-served industries and those with truck-to-rail conversion potential do just that.
Consulting Services:
NCRR offers options for commodity & logistic analysis, site selection, and marketing assistances to Economic Development Organizations (EDOs) and industries, to drive data-driven decision making and drive economic development.
Engineering and Construction Services:
Working closely with rail-served industries, the North Carolina Department of Transportation, and other rail construction organizations, NCRR leverages in-house expertise for engineering review, design of on-site rail construction, and rail track inspection to achieve the highest standards of safety and efficiency
Track Protection and Safety Services:
After identifying the insufficient number of qualified railroad flagging services as an obstacle to expediting rail and roadway projects throughout the state, NCRR launched its Track Protection Program. The company now supplies flaggers for safety and coordination during construction, repair, and maintenance projects on the NCRR corridor and Norfolk Southern-owned corridors.
NCRR is dedicated to advancing the state’s rail network and promoting long-term economic sustainability in our state. The NCRR team is proud to offer these new services and economic development programs to ensure the continued success and vitality of local economies.
The North Carolina Railroad Company is excited for its next 175 years as it continues to keep North Carolina forever in motion.
Game On: Rail + Real Estate Changing
Supply Chain Strategies
Following the explosion of post-pandemic domestic industrial projects, industrial demand remains strong. NAIOP forecasts industrial absorption to increase by 17.8% in 2025. From manufacturing to fulfillment, companies across industry are changing to meet the moment. Global competition, evolving consumer needs, and just-in-time fulfillment are shaping change. At the center of the revolution is rail-served real estate.
Faced with supply chain disruptions, rising operational costs, and reduced margins, industry innovators are employing a powerful tool to increase financial efficiency: bundling rail and real estate development.
Rail has long held a transportational edge for its safety and cost efficiency per ton, but companies across industry are realizing the transformative financial impact on operational efficiency when rail and real estate development are combined. Rail efficiencies compound when sites are dual rail served, reducing captivity and increasing optionality. Given the exhaustive efforts companies invest to identify strategic locations, equal consideration should be given to logistics solutions that maximize operational efficiency. These decisions span the life of the project. A 2024 analysis from RSI Logistics found that direct rail solutions deliver a 51% savings compared to long-haul shipments.
New Rules of the Game
Traditionally, companies invest considerable time and resources to identify the optimal location for manufacturing and distribution centers; however, transportation solutions for these new hubs are developed at a later stage. That misplaced timing often boxes out the most efficient transportation solutions and inhibits optimized flow of the newly constructed site.
Across the country, site selectors, developers, and companies are including railroads into early conversations that preserve transportation options and uncover a site’s full logistical efficiency. By baking optimized transportation plans into the site’s design phase, all options from footprint to floorplan are preserved. These conversations influence loading and unloading design, storage needs, and impact shipping and receiving options on planned inventory management solutions. The result is optimized flow and savings, enabling a much more efficient use of capital.
Leading the Way
OmniTRAX, the transportation affiliate of infrastructure developer The Broe Group, is demonstrating the impact of rail and real estate bundles to industry leaders and innovators across the country. As North America’s largest privately held infrastructure development company, OmniTRAX provides the reach, readiness, and resources that bring transformative rail and real estate solutions to life. Serving more than 400 customers, OmniTRAX is large enough to tackle complex supply chain challenges while maintaining its hyperlocal focus of building success stories one community at a time.
The OmniTRAX reach includes 28 rail operations spanning coast-to-coast and from Canada to Mexico. In addition to connecting customers to the North American rail network, OmniTRAX provides access to industrial parks and ports in strategic markets across the country.
Within this vast network, OmniTRAX offers immediate readiness for customers seeking rail and non-rail served sites that combine strategic location with logistics efficiency. Industry leaders such as The Home Depot, P&G, and Commercial Metals Company and innovators such as Gotham Greens and Quantix have taken notice. Many Fortune 500 companies are OmniTRAX rail customers, affiliated industrial park tenants, or both.
OmniTRAX’s unique ability to provide integrated supply chain solutions is attracting site selectors across the country. “OmniTRAX moves at the speed of business,” said Strategic Development Group President Mark Williams. “When our customers are seeking complete logistics solutions, OmniTRAX consistently provides the invaluable counsel they need to make informed decisions.”
Its unique pairing of rail expertise and a fully integrated real estate development affiliate company (Broe Real Estate) provides OmniTRAX customers a comprehensive view to optimize operational efficiency. Conventional developers just focus on “building the box” for customers. OmniTRAX helps clients avoid being boxed out of optimized shipping solutions, by injecting dual expertise into the design phase.
Equally important to its reach and readiness is its resources. As a privately held company, OmniTRAX excels at bespoke solutions. When a customer seeks land or rail service beyond its portfolio, OmniTRAX acquires the assets needed to create the desired solution. “When The Home Depot identified the greater Denver area as the ideal location for its latest flatbed distribution center, I knew we could count on OmniTRAX to make it happen,” said Upstate Colorado Economic Development CEO Rich Werner. “OmniTRAX quickly acquired 300 acres and delivered an award-winning facility in record time. Their entrepreneurial approach to providing solutions is what makes OmniTRAX so different.”
Market Outlook
Supply chain efficiency is more important than ever, and bundling is proving its value with each new project. Bundling rail service and real estate development provides immediate operational efficiencies, positions projects to scale with company growth, and positions businesses for long-term success in an increasingly competitive global marketplace.
Location and logistics are equally important pieces of the supply chain puzzle. Planning both pieces from the beginning of project design, is the key to solving it. OmniTRAX provides the collective rail and real estate expertise to help companies create customized solutions that drive their business forward. As domestic supply chains continue to evolve, the rail and real estate development bundle is proving to be the blueprint for optimized logistics solutions and operational efficiency.
Dual-rail service and distinct power capabilities bring 2MSF of
world-class logistics space to Southeast Wisconsin
Dermody Properties — a diversified private equity investment management company focused exclusively on the national logistics real estate sector — is developing LogistiCenter® at Pleasant Prairie.
LogistiCenter® at Pleasant Prairie is strategically located in Southeast Wisconsin, broadly known as a suburb of the greater Chicago industrial market. The site, redeveloped from a decommissioned We Energies power plant, offers the ability to deliver heavy power to meet the increasing demand of advanced manufacturing. The three-building park is planned to accommodate more than 2 million square feet of Class A industrial and logistics space and has substantial power capacity, fresh water access from Lake Michigan and the extremely rare opportunity to receive or transload due to the dual rail service from the Union Pacific Railroad and Canadian Pacific Kansas City Southern Railroad.
Smurfit Westrock signs 583,000 SF build-to-suit for advanced manufacturing facility
Believing in the value proposition, Smurfit Westrock, a global leader in sustainability packaging with 320 manufacturing facilities, design centers, research labs and sales offices worldwide, ended its multi-state search in January 2024, signing a build-to-suit lease at LogistiCenter® at Pleasant Prairie.
The logistics park sits at the confluence of east/west and north/south railroads, connecting the park from East to West in the United States, and North to South from Mexico to Canada. This rail connection to the Union Pacific allows Smurfit Westrock to transport raw materials with increased efficiency and reduce environmental impact. Utilizing the rail to deliver raw materials cuts weekly inbound truck traffic by approximately 150 trips. The rail versus truck transportation model also significantly cuts transportation cost by several million dollars per year and benefits the local community by reducing truck traffic and maintenance on roadway infrastructure.
The asset-rich former power plant has been given new purpose for the Pleasant Prairie community and incoming businesses alike, contributing to the area’s well-established and respected manufacturing and technological business community. Situated between Milwaukee and Chicago, Pleasant Prairie has seen rapid economic development due to its business-friendly environment and access to a high-quality labor force.
LogistiCenter® at Pleasant Prairie’s distinct combination of powerful capabilities shows Dermody Properties’ continuous commitment to providing customers with value that will support growth in an evolving economy. To learn more about LogistiCenter® at Pleasant Prairie, visit dermody.com.
Arizona’s Manufacturing Mega Site – Inland Port Arizona
The rise of reshoring and e-commerce has dramatically increased the demand for efficient, cost-effective industrial sites. As businesses look for strategic locations to establish manufacturing facilities or distribution centers, Inland Port Arizona (IPAZ) is taking the lead. Located in Pinal County, midway between the major metropolitan areas of Phoenix and Tucson, this 2,700-acre rail served industrial mega park offers numerous advantages for businesses seeking a competitive edge in supply chain management and operational efficiency. Companies like Procter & Gamble and Nikola Motor Company haven taken notice and selected IPAZ for their advanced manufacturing Facilities. IPAZ was developed by Saint Holdings, the same developer as the nearby Central Arizona Commerce Park, which is home to Tractor Supply Company, Lucid Motors and several suppliers to the semiconductor industry.
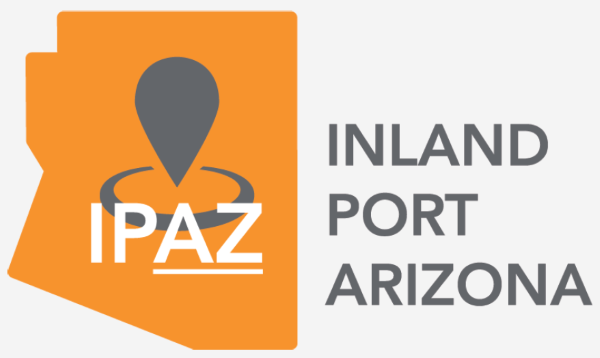
Strategic Location and Connectivity
Inland Port Arizona’s location is one of its most attractive features. It is situated near major highways, including Interstates 8 and 10, which connect the region to both the East and West Coasts. This strategic location allows companies to easily distribute products to key markets such as California, Texas, and even Mexico. Additionally, Inland Port Arizona is just a short distance from the country’s busiest ports of Los Angeles and Long Beach.
Another significant advantage is the proximity to Union Pacific rail lines, including the onsite lead track and nearby Sunset Route, which allow businesses to tap into cost-effective, large-scale transportation solutions. This multi-modal connectivity creates a seamless logistics network that enhances delivery speed and reduces transportation costs. Businesses operating out of Inland Port Arizona can also capitalize on its proximity to Phoenix Sky Harbor, Tucson International & Mesa Gateway airports, which provide critical air freight services for time-sensitive goods.
Infrastructure and Cost-Effective Operations
One of the key advantages of IPAZ is its robust utilities infrastructure, designed to support the needs of large-scale industrial operations. The region boasts reliable access to essential utilities such as electricity, plentiful water, and natural gas, ensuring that businesses can operate efficiently without disruptions. Arizona Public Service (APS), one of the state’s largest energy providers, supplies electricity to the region with competitive rates and immediate plans for additional capacity.
Water availability is another critical factor for manufacturing and distribution facilities, and IPAZ is well-equipped to meet this demand. The area benefits from an integrated water, wastewater and recycled water provider, Global Water Resources (NASDAQ: GWRS). Global’s programs ensure that businesses can maintain steady operations even in a desert environment, with long-term plans in place to ensure water sustainability.
In addition to electricity and water, the region has a well-established natural gas network, providing businesses with a reliable energy source for industrial processes. Telecommunications infrastructure, including high-speed internet and fiber optic networks, is also readily available, enabling companies to leverage the latest technologies for real-time data management, logistics tracking, and communication.
Another compelling reason to choose IPAZ is its cost-effective environment. Compared to major metropolitan areas, real estate, labor and utility costs in Pinal County are significantly lower, which translates into substantial savings for businesses looking to establish large-scale operations.
Moreover, the existing skilled workforce and tailored training programs available in the area ensure that companies can hire qualified employees for both manufacturing and distribution roles. Local educational institutions and workforce development programs such as Central Arizona College and Pinal County @ Work are also geared towards meeting the needs of growing industries.
Kiamichi Railroad Provides Maximum Logistics Flexibility for
New Tyson Foods Mega Poultry Feed Mill
On May 10, 2022, the first Kiamichi Railroad (KRR) train arrived at Tyson Foods’ new $65 million “mega” feed mill in McNab, Arkansas — marking the culmination of a multi-year project for both companies.
In 2018, Tyson solidified plans to locate a new mill in southwest Arkansas that could produce feed for its existing farms and replace the aging feed mills at Hope and Nashville, Arkansas. With a need to receive inbound unit trains of corn and manifest soybean meal cars at start-up and connectivity to the North American rail-freight network, Tyson worked with Genesee & Wyoming’s Industrial Development group to find a site and develop a track plan.
Building on its solid relationship with Tyson in Hope, Arkansas, Kiamichi Railroad offered Tyson the logistic flexibility it required at a 145-acre greenfield site situated along the railroad’s line and with ample space for further development in McNab, Arkansas. Among the site’s most significant benefits is its access to three Class I carriers, giving Tyson maximum flexibility to source materials as well as rate competitiveness.
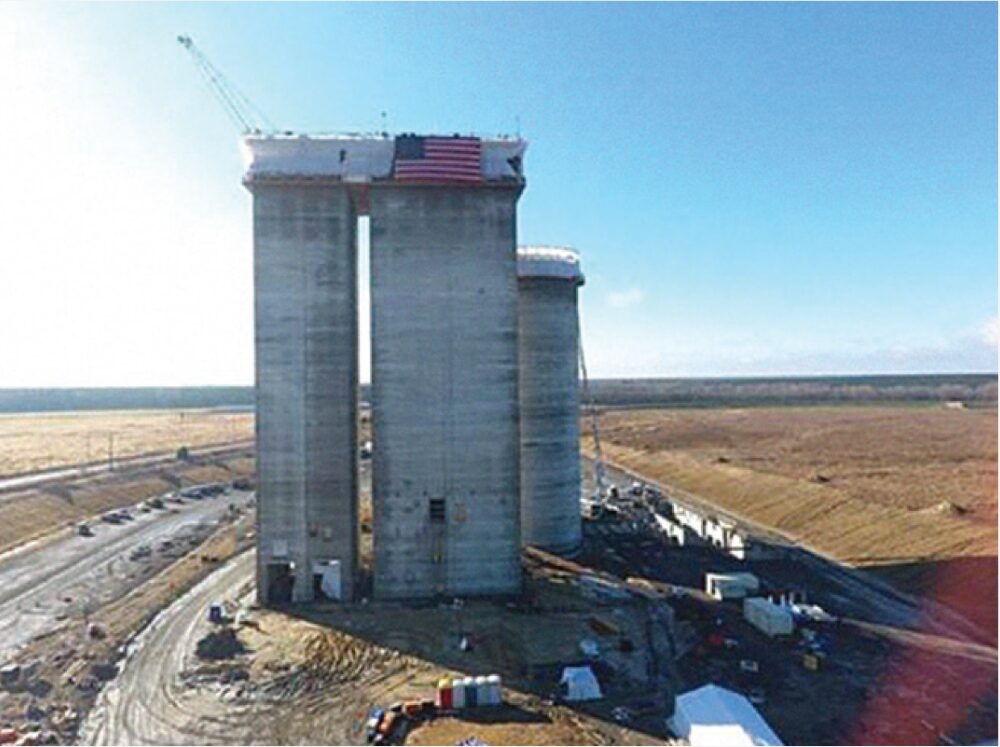
Tyson Foods’ new “mega” feed mill during its construction.
Tyson began construction on the new mill in June 2020. To support the project operationally, Kiamichi Railroad invested nearly $9 million in building two main line switches and a side track at the McNab site as well as bringing the entire Tyson route — over 180 track miles from Madill, Oklahoma, to Hope, Arkansas — up to 286k capacity. This track improvement included not only rail replacement but the repair and strengthening of more than 80 bridges.
Just under two years later, unit train service to the completed mega mill was underway weekly. This is just one example of how Genesee & Wyoming Rail Services’ Industrial Development team worked to find a site, meet the needs of our customer and invest in a growth-oriented project. Find out more about how G&W’s Industrial Development team has the know-how and toolset to assist on growth projects in any location our railroads serve by going to www.gwrr.com/id.