It wasn’t too long ago when logistical marvels such as Amazon transformed the B-to-C product delivery world. Now, many B-to-B companies are realizing that these same shortened delivery expectations are filtering into their world, with warehouse site selection critical to a successful fulfillment program.
There was a time when B-to-B companies worked on order fulfilment expectations of one week. Then that moved to 72 hours, and now next-day delivery is increasingly becoming the norm. One such company listening to its clients’ needs for quicker order fulfillment is Lawson Products.
Since 1952, Chicago-based Lawson Products has supplied high-performance maintenance and repair products to customers across North America. With approximately 300,000 products, the company serves customers through distribution centers in McCook, Ill. (southwest Chicago); Suwanee, Ga. (northeast Atlanta); Fairfield, N.J.; Reno, Nev.; and Mississauga, Ont., near Toronto Pearson International Airport.
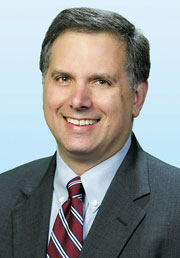
I have worked with Lawson for five years. Most recently they contacted me to assist them in finding a location that would allow for a later UPS pickup — from the regular 7 p.m. cut-off time to 11:30 p.m. This extended pickup window would be critical in getting orders out the same day, and reducing the need for next-day-air deliveries. Air shipments are not a cost-effective option for Lawson or its customers, as their products tend to be heavy and relatively low cost per sku. Thus building an efficient ground delivery network is critical to maintaining profitability.
We spent 12 months thoroughly researching opportunities, looking at both existing locations and possible new-build spaces. We concentrated our efforts around the I-55 corridor, an area that runs about 10 to 35 miles southwest of the Chicago loop.
We visited 16 prospective sites, and Lawson decided to rent a build-to-suit facility in McCook, just four miles from the UPS Cach (Chicago Area Consolidation Hub) facility in Hodgkins, allowing them to improve their customer service.
The McCook location gave Lawson four-and-a-half more hours of order picking and preparation every day. In addition to an expansive one- and two-day delivery area, this has allowed Lawson to minimize the need for overnight freight shipments while still meeting the customer’s needs of quick delivery.
Existing Location or New Build?
A situation that inevitably arises is the question of whether to build your warehouse to spec, or locate in an existing building. There are pros and cons to each, and each situation requires a different weighting of criteria.
According to June 2015 analysis by Dodge Analytics for NAIOP, “Warehouse construction registered a fourth strong year of increased expenditures in 2014, gaining 19.7 percent. In 2011, expenditures for warehouse construction increased 17.8 percent; in 2012, they increased another 28.4 percent; and in 2013, they increased 38.1 percent.” Warehouse construction totaled 157.4 million sq. ft. (14.6 million sq. m.) of space in 2014, accompanied by total capital investment of more than $10.7 billion.
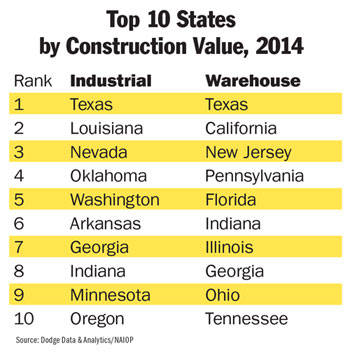
Building to suit (BTS) allows a company to have the new facility tailored specifically to its needs. E-commerce companies such as Amazon often need 2,500 parking spaces for a 1-million-sq.-ft. (92,900-sq.-m.) distribution center (DC). A normal DC will need about 350 parking spaces. E-commerce companies also often want 40-ft.-clear ceilings to accommodate multiple levels of mezzanines for multi-level order picking. If a company has very specific needs, a build-to-suit is often the best option.
BTS projects can also yield impressive results in their economics. With enough lead time, a corporate distribution user can create a virtual auction among qualified developers that want to win the assignment. This competition can result in a lower rental rate than existing buildings.
This economic benefit has been especially valuable during the recent years of near zero interest rates and the cap rate compression that has driven investor prices for leased assets to record high per-sq.-ft. prices.
The downside of a BTS project is that it will take around 18 months to design the building, negotiate the rent and the lease and construct the building. So the BTS process is not available for those distribution users that cannot wait for space.
The economic slowdown that started in 2008 and lasted through 2011 stopped the real estate development industry dead in its tracks. Industrial developers were not able to secure loans nor financial partners to build new speculative (spec) industrial buildings. When the debt and equity for spec buildings returned, lenders and equity partners approved smaller buildings that could be divided for several tenants, thus mitigating the risk of being limited to looking for a single tenant.
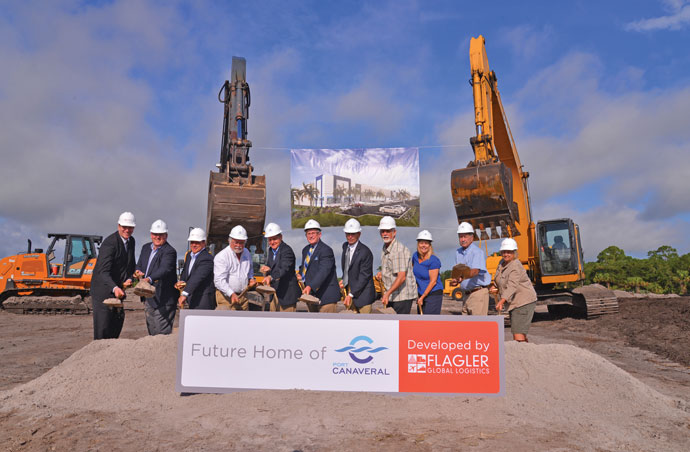
However, the industrial real estate market fundamentals continued to improve from 2012 through 2014. All over the US, absorption grew and vacancies declined. As of August 2015, the industrial real estate market is the strongest landlord’s market in this author’s 30-plus year career.
Rents are rising, demand is strong, vacancy is low and those spec buildings underway have undergone significant pre-leasing.
2015 has already been a very strong year for new spec construction, including single-tenant buildings from 600,000 to 1.2 million sq. ft. (55,740 to 111,480 sq. m.). 2016 will be a record year for industrial real estate construction.
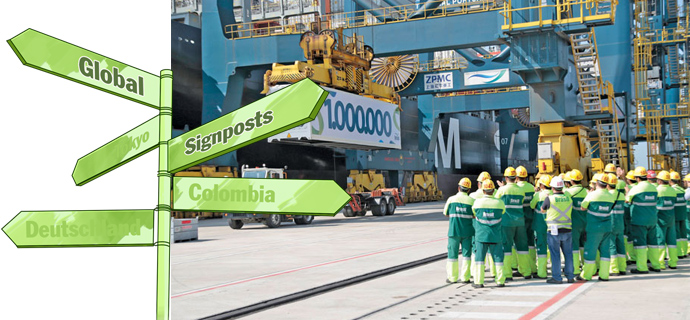
Follow a few blue chip companies and you’ll find some blue chip clues to the logistics locations and best practices of tomorrow. The acronyms APM and DHL are good places to begin.
This summer, Netherlands-based APM and Compañia de Puertos Asociados S.A. (Compas S.A.) committed to jointly investing more than US$200 million in upgrading and expanding Compas S.A.’s multipurpose Cartagena Terminal in Colombia, which has an annual throughput capacity of 250,000 TEUs and 1.5 million tons of general cargo.
The upgrade will triple annual throughput capacity for the terminal to handle the larger vessels transiting the widened Panama Canal.
“Colombia represents one of the most promising investment opportunities in the region, and we are pleased to participate in the country’s ongoing economic growth and development,” said APM Terminals CEO Kim Fejfer. The facility becomes the sixth operational Latin American facility within the APM Terminals Global Terminal Network, which includes interests in operating port facilities in Callao, Peru; Buenos Aires, Argentina; and Santos, Pecém, and Itajaí, Brazil. Compas S.A. is a major terminal operator in Colombia, but also has terminal interests in Houston and Panama. APM Terminals also has two new deep-water terminals under construction in Latin America at Moin, Costa Rica, and Lazaro Cardenas, Mexico.
A major stop for more than 30 shipping lines, Cartagena was the second-busiest container port in South America in 2014, and the fifth-busiest in the Latin American/Caribbean Region, with a throughput of 2.23 million TEUs, trailing only Balboa and Colón, Panama; Santos, Brazil and Manzanillo, Mexico, in container volume, and shipping more than 40 million tons annually. The Port of Cartagena’s annual container volume growth rate was 13 percent from 2013 to 2014.
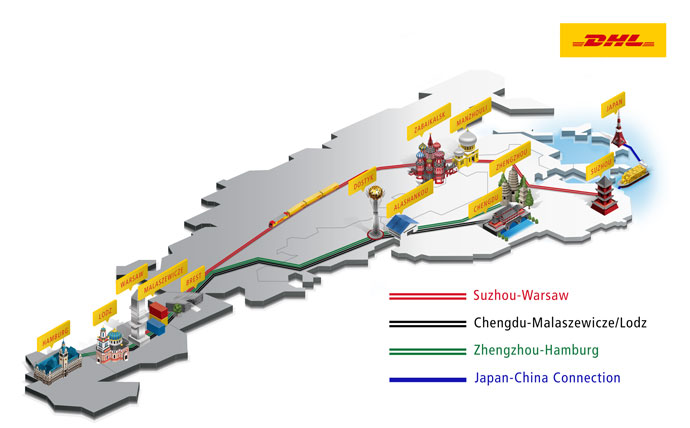
It’s been a long road from 20 years ago, says Aníbal Ochoa, commercial coordinator for the Port of Cartagena, when the site was “a very torn-up terminal” that prospects rejected as soon as they saw it. After some global benchmarking, the port grew to just under 700,000 TEUs annually by 2005, and has taken off since then. Among $16 billion in projects now underway in the city’s industrial zone (including expansion of the Tenaris petrochemical complex), the $660-million Contecar container terminal is being developed to take the port complex’s overall capacity up to 5.2 million TEUs, and the new El Cayao LNG terminal will open nearby in 2016, as Cartagena reiterates its role as a transshipment hub for all of the Americas and aims to be among the 30 largest-volume ports in the world once all investments are complete.
“Two big reasons for more cargo in the Caribbean are that north-south trade is becoming more important, and there is more near-sourcing,” says Ochoa. “Customers are shifting production from Asia to Mexico, Brazil and the Latin American countries, and the labor in China is no longer as cheap as it used to be.”
As for the potential for future logistics facility supply in the area, “We are thinking of a third location for a port, “ says Ochoa. “We are okay now. But look at Singapore — that’s what we want. That’s where we’re going.”
Even as it consolidates its US port terminals to locations in Elizabeth, N.J.; Miami, Fla.; Mobile, Ala.; Los Angeles, Calif.; and Tacoma, Wash., APM is growing in Santos, Brazil, too. The company’s Brasil Terminal Portuário (BTP) handled its millionth container in July, just 20 months after operations began. Elsewhere, in partnership with Bolloré Africa Logistics and the Ghana Ports and Harbour Authority, APM will invest $1.5 billion in a massive upgrade of Tema, Ghana’s most important port. The project will add 3.5 million TEUs in annual throughput capacity and help create more than 5,000 jobs. And in May, APM reiterated its commitment to keep growing operations at the Poti Seaport in the Republic of Georgia, where an expansion envisioned for completion in 2018 would bring annual throughput capacity to 1 million TEUs and position the port as a gateway for Black Sea, Mediterranean and Central Asian trade.
Innovation Inroads
DHL this year opened a redesigned Innovation Center in Troisdorf, Germany, near Bonn, and will open its new Asia Pacific Innovation Center later this year in Singapore.
“At Deutsche Post DHL Group, customer-centric innovation is key to two of our major ambitions,” said Frank Appel, CEO Deutsche Post DHL Group, said at the opening ceremony in Troisdorf. “One is to play a pioneering role in spearheading the global evolution of logistics, which is at the core for the sustainability of our planet. Second, to remain the logistics leader by innovating products and services that our customers need most — whether that is to make an e-commerce delivery, design a global supply chain or ship temperature sensitive pharmaceuticals.”
The Singapore facility will be located within the new $100-million DHL Supply Chain Advanced Regional Center currently under construction.
In March, DHL Express unveiled the blueprint of DHL Express South Asia Hub, a 24-hour express hub facility located within Changi Airfreight Center at Singapore Changi Airport. It’s part of a recent series of plans to bolster DHL Express’ network infrastructure in the region, including DHL Express’ Central Asia Hub in Hong Kong (which boasts the region’s largest throughput), the North Asia Hub in Shanghai Pudong International Airport and a new gateway in Tokyo slated for completion in 2016.
In July, DHL Global Forwarding signed an MOU with Kazakhstan Temir Zholy Express which will aim to provide greater rail connectivity and trade among China, Kazakhstan, the Commonwealth of Independent States (CIS) countries and Europe. In June DHL committed to further expansion of its multimodal services in China with a new twice-weekly service between Zhengzhou and Hamburg via Poland (see infographic).
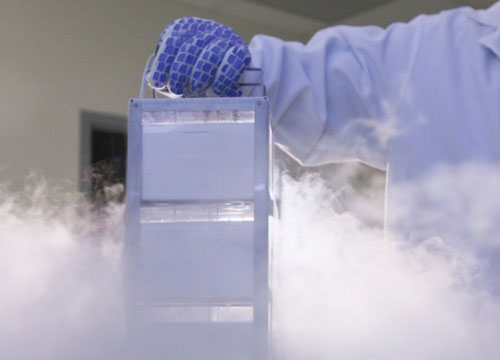
Cold storage plays a key role in the food and pharmaceutical sectors, both of which continue to grow in importance to regional economies. As such, the role of the cold storage supply chain — the cold chain, in industry parlance — is increasing in value to the players in those economies.
Exhibit A: APM Terminals and GF Group recently announced the acquisition of 100 percent of the Vado Ligure Reefer Terminal S.p.A. by APM in Vado, Italy. Reefer Terminal, the largest refrigerated terminal in the Mediterranean for more than 30 years (handling 600,000 pallets per year of fresh produce), is part of the port master plan to create new supply chains to markets in Northern Italy, Southern France, Switzerland and Bavaria. The Reefer Terminal is located adjacent to the construction site of the APM Terminals Vado port project, which will open in January 2018 with 800,000 TEU annual capacity.
“The integration of the Vado Reefer Terminal with our new, future semi-automated container terminal enhances the logistics options for businesses and the shipping lines calling [on] the Ligurian coast, serving all of Northern Italy and beyond,” said APM Terminals Vado CEO Carlo Merli. “We are building Italy’s port of the future with ideal access to Turin and Northern Italy manufacturing zones as well as consumer markets. Equally important, we will have the best port system and product in the market capable of serving container vessels, reefer vessels, RoRo and breakbulk vessels. The APM Terminals Vado facility will be the only port in Italy able to handle Ultra-Large Container Ships (ULCS) of over 18,000 TEU capacity when it opens in January 2018.”
A June research note from Cushman & Wakefield reported that cold storage buildings, particularly those constructed since 2000, sell at approximately double the price per square foot of standard warehouse/ distribution facilities. Emerging technologies in newer buildings have pushed values even higher. There are currently 1,497 cold storage facilities in the U.S., totaling 4.06 billion sq. ft. (377 million sq. m.), and controlled by just a handful of operators.
“Industry growth largely depends on household income and consumer spending,” said the report. “With both on the upswing post-recession, growth in US cold storage capacity has increased by an annual average of 9.3 percent since 2008.”
Chill Capacity
In June, DHL Freight integrated three certified Life Sciences & Healthcare Competency Centers into its LTL (less than truckload) ColdChain network, adding new stations in Lyon, Milan and Madrid, with another in Budapest scheduled to be added soon. Targeting the life sciences and healthcare industry, an integrated “Solution Suite” from DHL offers services specifically tailored for these customers’ needs, as well as an IT platform, CoolTrack, that allows continuous monitoring and real-time tracking of cargo temperature via GPS.
Running twice a week, DHL’s ColdChain service in Europe includes central routing via a cross-docking center in Mechelen, Belgium, from which shipments can be further transported under predefined temperature conditions (2-8° Celsius or 15-25° Celsius) to 30 countries in Europe.
“Our customers in the life sciences and healthcare sector are looking for better ways to manage the risk of product damage and loss from temperature deviations in increasingly long and diverse supply chains. With DHL’s pan-European LTL ColdChain network we are embedding the new standard for cold-chain road freight transport further into Europe,” said Amadou Diallo, CEO, DHL Freight.
Those same nettlesome issues of port and customs delays affecting temperature-sensitive shipments are present in South America.
Aníbal Ochoa, commercial coordinator for the Port of Cartagena in Colombia, says his team has responded by dedicating special personnel to tracking perishables, as transshipment of reefer containers has grown by 500 percent at the port over the past five years. He’s also looking for an international partner to develop a cold-chain cross-dock facility on the port.
As the port grows, he says, “This business unit will become very important.”
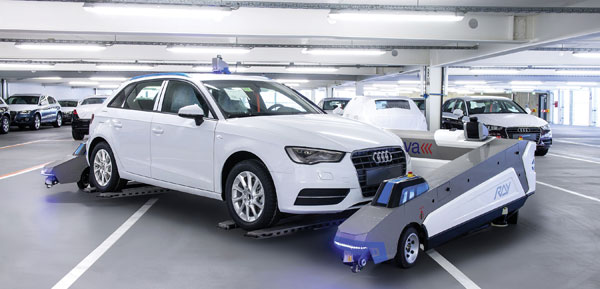
Logistics plays a key role for our company’s success.”
With those words, Markus Schäfer, member of the Divisional Board of Mercedes-Benz Cars, Production and Supply Chain Management, welcomed the opening of the division’s new consolidation center in Speyer, located in the Southwest German state of Rhineland-Palatinate, in July.
Anyone wishing to study global logistics decision-making can benefit from studying the recent actions of German automotive giants. In Mercedes-Benz’s case, the focus will be on securing the supply of materials in its global production networks, reducing inventories, ensuring on-time deliveries of new vehicles to customers around the world, and incorporating the logistics organization into the continuous advancement of the global production network at an early stage.
Supply Chain Management at Mercedes-Benz Cars employs nearly 7,500 people, and numerous service providers. “Our investment of several hundred million euros in our Supply Chain Management organization will optimize logistics throughout our global production networks,” said Alexander Koesling, head of Supply Chain Management, Mercedes-Benz Cars. “By reducing our logistics costs per vehicle we will improve our competitiveness, since logistics have a major impact on our overall cost position.”
Noting that increased versions and customization options are straining logistics operations, the company plans to have highly specialized logistics service providers consolidate supplier shipments in an optimal manner to ensure deliveries from Speyer to the three major Mercedes-Benz Cars plants abroad — in China, the US and South Africa.
“The setup of similar consolidation centers in the upcoming years is being considered, especially in growth regions like China and NAFTA,” said the company.
A total of approximately €90 million was invested in the Speyer facility. When it becomes fully operational in 2016, the center will ship several hundred sea containers per week via inland waterways or rail to Antwerp and Bremerhaven, where they will be loaded onto freighters and transported to assembly plants in Beijing; Tuscaloosa, Ala.; and East London, Eastern Cape, South Africa. “After intense examination, Daimler chose Speyer for the new center because of the available space and the geographic location,” said the company.
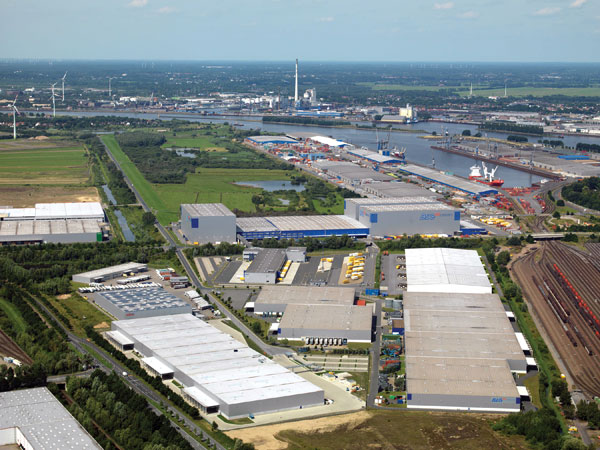
Until now, logistics service providers in Bremen were solely responsible for managing shipments of materials from German and European suppliers to the major Mercedes-Benz plants abroad. Thanks to the new consolidation center in southwestern Germany, deliveries from European suppliers south of the Main River will no longer have to be shipped over long distances, which will significantly reduce the logistics costs.
Activities in the area of outbound logistics revolve around the realignment of the global transport network in order to prepare it for the significant increase in unit volumes at plants around the world, said the company. “A key strategic project in this area was recently given the green light. It involves the construction of a new network hub at a port in the Adriatic Sea that will be used to ship vehicles to Asia.”
Deals for Dealers
Getting parts to automotive dealers in their worldwide networks is another challenge automakers are meeting head on. Last November, Mercedes-Benz pledged to invest $2.8 million to expand its parts distribution operation in Jacksonville, Fla., which opened in 2010. Porsche invested $90 million in a new parts distribution center in Sachsenheim, Baden-Wurttemberg, while also collaborating with Volkswagen in a $41-million shared parts distribution investment in Siezenheim, Salzburg, Germany.
This summer, Volkswagen Group of America announced plans to invest $6.8 million to opens a new Pacific Northwest Parts Distribution Center in Sacramento, Calif., which will be VW’s second parts distribution warehouse in California, along with a facility in Los Angeles.
Daimler, meanwhile, recently started benefiting from a new parts distribution facility in Kunshan, Jiangsu Province, China, operated by Kerry Logistics. And it’s taking advantage of the parts distribution prowess located in Bremen, where BLG Logistics operates 300,000 sq. m. (3.2 million sq. ft.) of indoor storage exclusively for auto parts logistics, largely at the Güterverkehrszentrum (Freight Village – GVZ). BLG recently occupied “LC GVZ 2” after its development by Panattoni Europe.
Each year more than 40,000 containers with vehicle parts are packed and delivered just-in-time to assembly plants in Asia, the Americas and Africa from Bremen. “The parts and components arrive from the Daimler plants in Germany and from several hundred suppliers,” said a BLG release in August. “Due to a new production strategy implemented by the customer, transport volume has been increased considerably. The volume of containers shipped to China alone, thanks to the expansion of the Daimler plant in Beijing, will rise to 20,000 units.”