Batson-Cook Construction, founded in 1915, provides commercial general contracting, preconstruction, construction management, and design-build services to a wide range of clients throughout the southeastern United States. With offices in West Point and Atlanta, Ga., and in Tampa and Jacksonville, Fla., Batson-Cook brings quality construction practices to such varied sectors as industrial, manufacturing, office, multi-family housing, retail, institutional, healthcare, hospitality, education, and resort facilities. “We have the heart of a family-owned general contractor with the reach of a global construction firm,” says the company, a reach that extended further in 2008 with its acquisition by Japan’s Kajima Group. Batson-Cook President and CEO Randy Hall recently talked with Site Selection Managing Editor Adam Bruns about the company’s past, present and future.
Site Selection: Describe your team’s experience of the return of manufacturing to the United States.
Randy Hall: A few years back, Kajima suggested to us that manufacturing and industrial work was on the move back to the US, and really challenged us to play a role in the construction of those projects. We decided to dedicate a group of professionals to pursue this work. Batson-Cook’s West Point Office serves as the hub for manufacturing and industrial pursuits across the Southeast. Clients include Mitsubishi Power Systems, Mead-Westvaco, Pratt-Whitney & Cessna. We are also building manufacturing-related work for the Tampa Port Authority and Nexlube Oil. Our project for Mitsubishi Power Systems in Savannah involved an assembly plant and balancing bunker for large gas turbine equipment. Our expertise in complicated foundations helped us be successful on this project.
SS: A century ago, the company got its start building textile plants and “mill villages.” Today people seem to want that village concept all over again.
RH: The Skyhouse program is thriving based upon the public interest in returning to urban environments and walkable communities. We have watched this trend grow over the past few years — pre-2008 we were building urban condominiums for the same reasons. The Skyhouse concept — conceived by Jim Borders, president of the development firm The Novare Group, and designed by Smallwood Reynolds Stewart & Stewart Architects — has been wildly successful in Atlanta, Orlando, Tampa, Austin, Houston, Dallas, Raleigh and Charlotte.
Batson-Cook Construction approaches these projects using a program of lean construction premised on the elimination of waste. We engage the field foremen to help us make decisions on how to build in the most efficient and effective manner. Lean asks for incremental improvements every day. This construction process has been a huge success at Batson-Cook.
SS: How has sustainability risen as a priority among your client base and within your company?
RH: We are seeing more design professionals move to sustainable design as a matter of general design. Conservation of materials, water, air and energy are all being incorporated in the initial design. One of our projects, Duke Energy Center in Charlotte, N.C., was the first high-rise office building to receive the LEED Platinum Certification. Batson-Cook also is credited with the first Business Conference Center to be awarded LEED Certification — the Callaway Gardens Conference Center in Pine Mountain, Ga. And we’re constructing what will be the district’s first LEED-Certified elementary school in Hillsborough County, Fla. We have over 20 LEED Accredited Professionals working for Batson-Cook, and we have completed over $350 million in LEED-Certified projects.
SS: Challenges in the engineering and construction field today include talent cultivation, and more modularization and prefab. How is Batson-Cook positioned to address these challenges?
RH: There is a talent war we are all going to fight, no question about that. We support and encourage our industry to embrace technology and the benefits that come from it. We believe there is a direct relationship to attracting the next generation of builders. We have a Director of Field Technology and a training department dedicated to field innovation.
The lean construction process also encourages prefab and modularization as a means to eliminate waste. We are seeing more and more modularization of mechanical and electrical systems, bathroom pods, pre-casting concrete and many other trades. I believe virtual construction and modularization are the future of our industry.
SS: Industry analysts see manufacturing, coastal port expansion and healthcare as looming opportunities. Do you share that view?
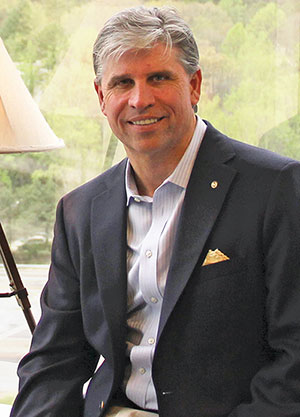
Randy Hall, President and CEO, Batson-Cook Construction
RH: Batson-Cook has dedicated sales and operations staffs to all three of these market sectors. Our men and women are specialists in these areas and we believe we can be good partners in the development and construction process.
SS: Describe how being part of Kajima USA Group is helping Batson-Cook serve its corporate clients’ needs.
RH: We became a part of Kajima USA in 2008. As you know, 2008 was the year when the economy started to tank. Through the tough years of 2008-2011, Kajima supported Batson-Cook with integrity and responsibility. Batson-Cook has existed for almost 100 years and Kajima more than 150 years — we work very well together. Today, we are technically a very large company that has the ability to do business like a medium-sized family-owned business. We have access to many in-house development, design and construction professionals. We are simply a better company today because of the Kajima organization.
SS: In addition to serving growing companies, Batson-Cook is a growing company itself, with 350 employees and $500 million worth of work put in place in 2013. What’s in store as the company’s next century gets under way?
RH: That’s simple. We want to be the only choice for construction services in the markets we serve. This is my vision for our company. Growth is not our priority — our mission is to passionately provide high quality construction services to our clients.
This Investment Profile was prepared under the auspices of Batson-Cook Construction (www.batson-cook.com).
For more information, contact:
Manufacturing Market: Becca Hardin, Vice-President, Business Development, (706) 575-9671, bhardin@batson-cook.com
Florida Commercial Market: Frank Rygiel, Vice-President, Business Development, (813) 610-5889, frygiel@batson-cook.com
Florida Healthcare Market: Scott Dunkle, Vice-President, Business Development, (407) 620-1496, sdunkle@batson-cook.com
Georgia Commercial Market: Scott Thompson, Vice-President, Business Development, (770) 906-4283, sthompson@batson-cook.com
Georgia Healthcare Market: Rhett Partin, FACHE, Vice-President, Business Development, (229) 237-3334, rpartin@batson-cook.com